EP #064: Nano Concrete
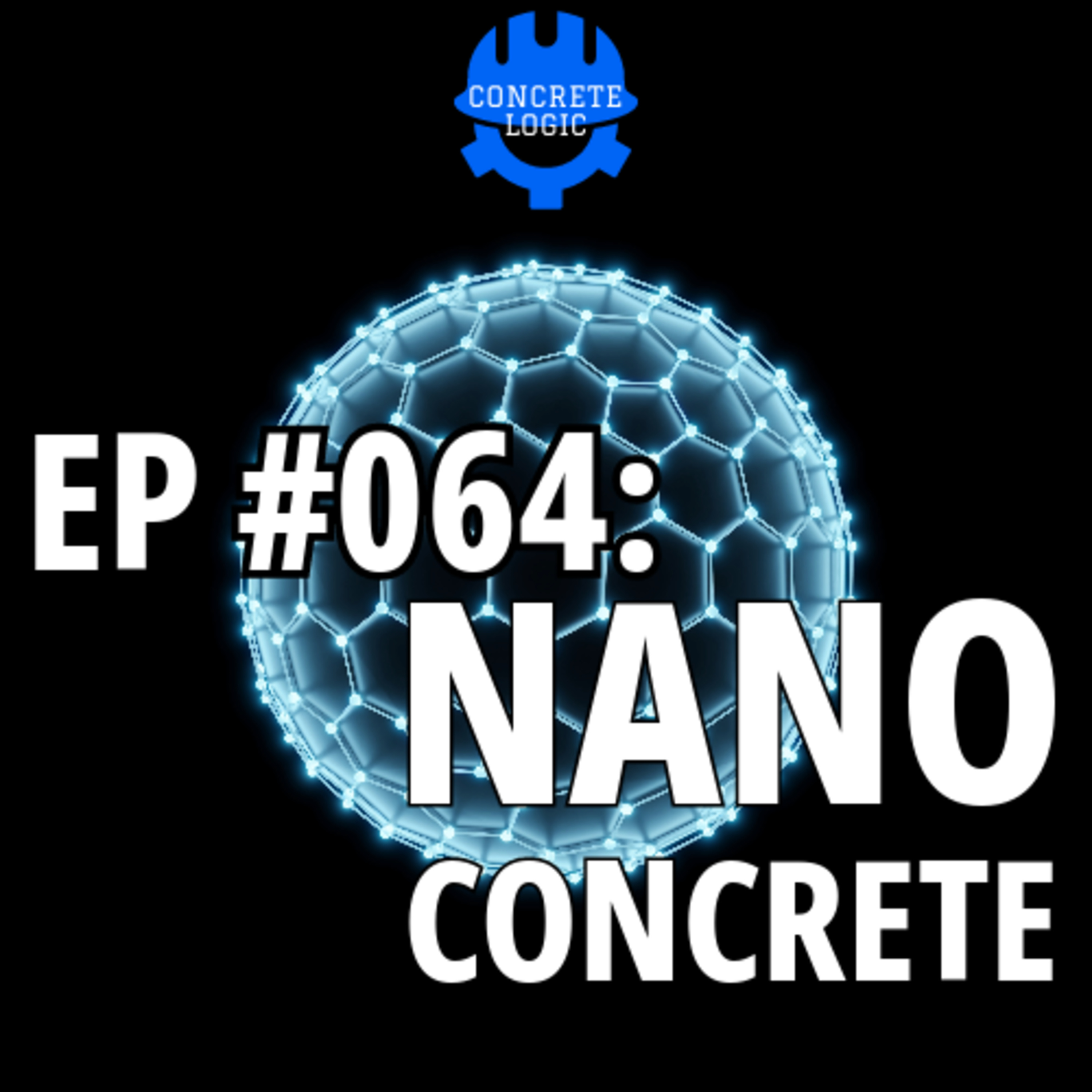
Usually in concrete construction, we think about the big things we can see - formwork, rebar, ready-mix concrete, tower cranes, trucks, excavation equipment, and laser screeds.
In this episode, we will explore the benefits of thinking about concrete at a one-billionth nanoscale.
Dan McCoy joins the podcast and shares his experience introducing nano-silica technology to his contracting business. Dan designs, pumps, and builds bridges with concrete.
If you want to hear from a contractor that has a ton of experience of nano-silica, this is the episode for you!
Did you learn something from this episode? If so, please consider donating to the show to help us continue to provide high-quality content for the concrete industry.
Donate here: https://www.concretelogicpodcast.com/support/
***
Episode References
Guest: Dan McCoy | R. L. McCoy, Inc. | danmccoy@rlmccoy.net Guest Website: http://rlmccoy.net
Producers: Jodi Tandett, Olivia Stocker
Donate & Become a Producer: https://www.concretelogicpodcast.com/support/
Music: Mike Dunton | https://www.mikeduntonmusic.com | mikeduntonmusic@gmail.com | Instagram @Mike_Dunton
Host: Seth Tandett, seth@concretelogicpodcast.com
Host LinkedIn: https://www.linkedin.com/in/seth-tandett/
Website: https://www.concretelogicpodcast.com/
LinkedIn: https://www.linkedin.com/company/concrete-logic-podcast
Seth: And welcome to another episode of the concrete logic podcast today. I have Dan McCoy with me. Dan's a third generation bridge builder, second generation concrete pumper and first generation engineer. So he's got a lot to say. He does a lot of work with the Indiana DOT and does, it sounds like you do some research work as well, Dan, is that correct?
Dan McCoy: for the DOT and for my own benefit.
Seth: And I see you've done some work with nano silica, which we've talked about a lot on the podcast. And one thing you and I have similar is you got three boys and I got three boys too. Oh plus I got it. I got the daughter in addition to those three boys.
Dan McCoy: Oh boy. Well, that may even things out a little bit because I'm telling you what, my three boys, it's like going to war every day.
Seth: Yeah. Well, I would say the girl is winning in our house, she's 11 and she's a handful. But anyways yeah, I, know what you're going through with the three, boys but it's fun.
I wouldn't trade it for the world. So Dan, we're going to talk a little bit, I think about what's going on over at the Indiana DOT. I want to pick your brain about that and things that you're working on over there. But before we get started, I just want to mention to everybody.
And I've tried to explain this in the past about how this podcast works. But if you're listening to the podcast and you find something of value that we share with you and say, Hey Dan had this great idea. Dan saves me 20 minutes or 30 minutes today or whatever based on our conversation today, what we're asking you is if you get any kind of value from this podcast is to visit our website.
And there's a link on there. It says, donate, you click on donate and you can give any amount It could be a dollar. It can be five, it could be 10, it could be a hundred. But we have two ladies that help us out every month.
They donate 10 bucks Jodi Tandett, my wife and then Olivia Stocker and she's been, supporting us as well. So I thank them very much. And so when you do this donation, you actually get your name listed on the podcast. So you're attached to the next podcast that comes out.
So check it out and see what you guys think. If we're providing any kind of value to you, all I ask is you visit the website, maybe throw, a penny or two our way.
Anyways now that's over Dan. We were talking a little bit before we hit the record button and I'm always amazed at some of these conversations about new things in concrete.
It seems like the Indiana Department of Transportation is on the forefront of some of these things. And I was curious why that is.
Dan McCoy: Well, Seth, thanks for having me on. It's, I always, this is, it's a passion to talk about anything infrastructure related, any and I, that goes over all variants of infrastructure, not just roads highways, bridges but learning about the grid, power, infrastructure, sanitation, sewer, everything.
The difference between a first world country and a third world country is civil engineering. Right. And, that's a 100 percent fact but there to go on to your point about in dot being leading the answer is why shouldn't we be? We have the largest in the United States, we have the largest producer of civil engineering undergraduates out of Purdue.
That's just one school by itself. I'm a graduate of tri state university, which is now trying, which my other engineering colleagues love to make fun of me for my, my school changing its name, but it's a great engineering school and there are other engineering schools Valparaiso, Notre Dame Rose Hulman legendary, there are a lot of really high quality undergraduate civil engineering programs that are located in Indiana.
So we, essentially can take the overflow in dot can of and the respective consultants around have a plethora of options of graduates every year to pull from. So we have a very enriched environment to produce the kind of talent that would enjoy and take passion in advancing infrastructure.
So we're very lucky just geographically. We're very lucky. We have a lot of access to the Purdue research facilities with Bowen Laboratories and a lot of the professors there, also a very big research school in, terms of their graduate program. So having a curriculum that's that close to the infrastructure in Indiana really helps.
Dr. Luna Liu has been. Very instrumental with her work in the D. O. T. And that could be everything from the wave logic sensor to analyzing and doing her work with liquid fly ash and the nano silica is self-healing concrete. And then that just garners a lot of attention. And over the last, I think it was five years ago it was Mike Nelson, who is the he, gets on me every time he does have superiors above him and materials, but he is the, Concrete God, as you would say for INDOT and he is a very forward thinker.
He's very as an engineer, I would say we, we tend to be optimistic. People think we take chances, but don't think that we've had a really good thought experiment about how we think it's going to turn out. We don't blindly throw things at the wall to see if they'll stick. We have an intent and a reason for the things we try.
And then we analyze afterwards how, they work. And one of the things that Mike came up with was he listened to contractors from around the state. And then he looked at the data from his own bridge decks, mainly the bridge decks. And it was increased plastic shrinkage cracking in overlays and concrete decks themselves.
And he began to think, well, is that because we're not getting wet cure on it soon enough? So we're, contractors, too concerned about the finish and eliminating the risk to the concrete being exposed to the atmosphere. So what he came up with was he just out of the blue called specification products and said I've heard some things in the commercial world about.
The E5 internal cure and where we went from there was, we had a job. We were just right place, right time. We had a job in Northern Indiana. And I am the kind of contractor slash engineer that really likes to see the positive in everything until I find a reason for a negative. And Mike asked us to participate in this and said, hey, would you participate in this trial?
For E5 and I'm thinking about eliminating wet cure. And I said, sign me up internal cure. Yeah, I mean, this is the Jason Weiss from Purdue has been working on this forever with his internal cure. Which is a lightweight or a more porous aggregate that's super saturated. And then as hydration happens it's, it yields water from that aggregate to continue the curing process from the inside out.
So, instead of wet blanketing or curing one side or just the exterior of the concrete, now we're curing throughout. Now, what nano silica does is essentially the same thing, only you coat the outside of the particle with water molecules rather than the inside. And then it also yields to hydration.
So, we went into it with that understanding. We saw it work and then the benefits of how easy it was to work with. As compared to trying to work with a lightweight aggregate, and I know Seth, you said you did a lot of PT parking garages, hospitals, things like that you for, fire ratings and lightning of, the superstructure for cost savings and economics, you use lightweight concrete and when Jason was determining this, he wasn't really thinking about lightweight concrete, but it's pretty much.
Yeah. A similar concept and into the fact that use lightweight aggregate. It's very porous. And one of the things you run into is it's very hard with lightweight concrete. internally cured concrete using a porous aggregate for a massive amount of this concrete to be produced consistently. You've got to presoak the aggregate.
It's, it shows up presoaked. You still have to continue soaking it at the ready mix plant or find a way to do so. And then check your aggregate moisture constantly throughout the pour analyze what's going on. And with internal cure, that just, doesn’t happen. You, it is way more forgiving to the ready mix supplier and to the contractor and to The concrete pumper which it was the second reason I was really interested in it.
So on this particular pour, we had the very first one, we, I had our pump guru come up. And for those of you that are listening to this, you may have heard the name Gary Brown the, legend that works for us. Who's been very involved with the American Concrete Pumping Association. And he's a legend in the concrete pumping world with well over 40 years of concrete pumping experience.
And it just so happened that we were lucky enough that with our fleet of concrete pumps the day before there was a bridge deck south for another bridge contractor and I asked him Gary, go out there, take a look at it, look at everything. I know you've done it a thousand times but give it a look and then come up to our deck pour and see if you notice any differences.
So we did that, and he would look at it from the pumping perspective and I was looking at it from the contractor finishing perspective. And we couldn't believe it. I mean, you had over a hundred bar decrease in pump pressure. Because that, internal cure was acting like a viscosity modifier.
They don't say it's a viscosity modifier, but that's it definitely has those attributes when used. And, We did that and then we started pouring and I noticed if there's one thing you notice and you may notice it in PT decks or slab tops When you're doing like a thin top topping is you can tell the progression of the load in eight or ten yard loads of You can tell as a finisher.
That's a dry load. That's a wet load. That's a dry load. That's an okay load That's a dry and you can look at the concrete as it's going, one thing a bridge deck is good for is it's a skinny, long piece of concrete and we're all pouring the same way, so you can tell those low differences. And the one biggest thing that I noticed was when we started pouring with nano silicas, specifically E5.
I couldn't tell you where the difference in the concrete was. So I knew that somehow, even though we were working with a great ready mix supplier, I knew that they couldn't get loads that consistent. So something had to be different.
Seth: Dry, all dry batch, right?
Dan McCoy: Yes, this was, yes this was all dry batch out of this particular plant.
And I, just knew something was different because there's so much that goes. And I don't think a lot of people understand that from our side on the contracting side, how much goes into making a consistent concrete load when you're dealing with the values that we're dealing with and the quantities that we're dealing with in, in, in.
in terms of slump retention, what the slump is air entrainment percentage and yield and just trying to get all that right load after load with materials that were brought in maybe the day before trucked in from somewhere else. Maybe you've got cement material differences because you're going through silos once a day or every other day.
So you're getting different batches from different silos or different, cement batches. Okay. From the same manufacturer. Sometimes they, get mixed together. It's not supposed to happen, but if it's an approved source, it's an approved source. So technically a type one should be the same all over.
We all know it's not, but it meets the qualification for a Portland cement. So it was amazing to see those differences. Disappear with it and then the added benefit of not having to cover it up and do a seven day wet cure was just phenomenal Yeah, and from there we've only progressed with the things we've tried So since then that was a standard mix with just adding e5 From there we reduced the cement content by about 100 and we replaced it with liquid fly ash and E5 in combination to create a longer lasting and more resilient structure.
I'm an engineer. Do I love compressive strength? I do. Do I think it's everything? Absolutely not. When you're looking for long life, durability and serviceability for a structure. I would forego compressive strength any day of the week. Over something that I know is going to be resilient and, at least extend the service life the life cycle analysis.
So that's why I really became involved in it because I was afraid that what we were going to have, and I think Mike felt this too, Mike Nelson with INDOT is, it was our view that if, the green movement was going to continue to happen, as engineers, we were worried that there were going to be products or methods shoved on our throats that by bureaucrats that may not be the best for civil engineering, civil for the people in our minds, it may not be the best. So why not let the engineers figure it out and let us figure out a way to hopefully make things better in terms of long term life cycle analysis rather than some of the other methods about.
Dealing with co2. So we reduce co2 by really just decreasing the amount of cement in the mix. And even when you went with a higher water cement ratio, which brought up workability, but we didn't worry about too much water cement and in terms of the ratio because we knew that water in terms of bleed water wasn't going anywhere because we witnessed this, and it was all staying in.
So we could increase the water cement ratio without increasing the chances of plastic shrinkage occurring. So, all of those, and if we can avoid those cracks, then or at least minimize those cracks, then what we've done is we've extended the life of the structure because we've taken those giant canyons and when you're talking on a nano or a pico scale, those even micro cracks are canyons.
And, when water gets in there and expands contracts it propagates that crack along with chlorides and bridges are totally exposed and open to the elements and they're treated rough all the time. So we were looking for something more durable. And longer lasting for the effects of the concrete rather than creating some super mix.
So that was the start of it. And then from there, we've just gone every everywhere else using really just common sense engineering practices with contractors into another, example might be that the states around us use. Epoxy reinforcing we used epoxy reinforcing but they would use, we were using normal tie wire.
Every state around us was using then epoxy tie wire or a poly tie wire to prevent corrosion. That's another thing that helped only when we looked at it instead of tying it 100 percent bottom. And 100 percent top mats for bridge decks. Ooh I did some unofficial research we've got line dragons.
that go out, stop, start for, holding that, cage together. If you've got 1500 pounds moving back and forth, that has the tendency to move rebar or so we thought. So we came up with that. We're really tying about 30 percent on a normal slab deck. So what if we went 50%? So we're saving half of that.
We went to 50 percent ties instead of 100 percent ties and have noticed no difference. So it's just little incremental things like that, that We try to advance, so we're not so much, we're not so much on the envelope of total concrete advancement. We're just trying things one way at a time, and eventually we're changing the industry to make concrete easier, to make working with concrete.
easier. And in the, in you're getting a benefit for all for one because you're increasing the longevity serviceability workability of the concrete for the, for that life cycle. And if that's what we're going to do, that's what we're going to do. And then we took that another step and issued some construction memorandums that allow almost everybody's doing it.
And then we took another step, added fibers and got ourselves a really, nice overlay mix for bridge deck overlays. Again, working backwards to say, what do we want out of the final product? Not so much. What does this product yield to us? What do we want? And then designing backwards from there.
Seth: As far as the fibers, what are you guys using?
Dan McCoy: Macro fibers. And it's, it really, so this is, the funny thing. In my terms now I'm sure Mr. Nelson would say something different, but in my terms, the whole reason I put them in. The first time we ever used them was if one of the things we're worrying about with overlays is that they're very thin inch and three quarter to two inches.
They're anywhere from 25 to 40 feet wide and then they're long. So you have this massive amount of surface area for a very small amount of concrete in proportion. So you're, just asking, you're just asking for bad things to happen in terms of plastic shrinkage. So the addition of the fiber was to do nothing more than to take up that initial stress in in the initial set where plastic shrinkage may occur.
And if we can stop those cracks from occurring at early onset, we've got a better chance for the overall lifetime of, the overlay. So that was the main, and then as. Luna Lu got further in with self-healing concrete and working with nano silicas and how they branch out and they, form more nucleation sites, the other thought. Post that was these fibers regardless of what they were provided more locations and branches for the nano silica and the cement to get together to so called daisy chain each other and then increase hydration for nucleation sites so I really think that's a good thing for the long term.
It was an unintended consequence, but that's, a pretty darn good consequence. Yeah. So that even when you do have cracks that occur five to seven days after a pour, you go back later and some of them you can't find anymore. So they're still there. I'm sure they're still there. I think there's a lot of cracks in places that you can't see.
Just the just from autogenous shrinkage, but is it reduced with what we're doing? Well, I really think it is Very much so and I think over the last five years that we've been doing this implemented it We're seeing a lot healthier bridge decks and a lot healthier bridge deck overlays and with the intent of extending the life cycle of that structure.
Seth: Yeah, have you guys made a comparison? before you were changing with the colloidal silica when you're including in that mix, those bridges have you compared the maintenance costs to bridges that you guys built before that?
Dan McCoy: Well, we can only extrapolate because in civil engineering, everything takes forever to analyze, right?
Here's the unfortunate thing. If you do a really good job, you're not going to know for a really long time. If you do a really bad job, you're going to know right away. So... Right. We're seeing a lot as Mike says he sits in his office, and he waits for people to have problems with things.
And he gets phone calls about those problems throughout every district. When it has to do with if someone perceives a material defect. So, the good news is since we switched to that, His phone calls have gone down dramatically, and to him, that's a lot of good news because the old mix with the overlays was a 658 pound cementitious with an additional 50 pounds of micro silica.
And as I've told Dr. Belkowitz before, I am not a hater of micro silica. I just think there's a right way to use it. And it was being abused to the point where we were begging it to fail. The whole mix itself, begging it to fail. Mike and I had a conversation about the mix heating up in the drum, and maybe if we sprayed the drum with water, or if we maybe only allowed pours between midnight and 4 a.
- And I'm thinking, Mike, if we have to limit it that much... We're doing something wrong. We need a mix that we can work with whenever and however, and we need this out of it. And we went from there we went from There were a lot of problems with a silica fume mix was just way too hot.
And the concrete guys, I think that are listening to this will know what a hot mix is. And it's just temperamental. You're nervous all the time. When's it going to flash? When's it going to, when's it going to go and what am I going to have to deal with the problems? Am I going to be back tomorrow?
Or after several days, am I going to be back doing epoxy crack injection to try and save it? Or am I going to rip it out and redo it? And unfortunately, that's what a lot of us had to think going into it. So it is what it is when it comes down to. What you want and what you perceived you wanted.
So a lot of delicate few mixes with over 700 pounds of cementitious. They were getting great beam breaks and great compressive strength. But is that what we wanted? I don't think so. It's, a wear.
Seth: Well, that's what you can pound your chest about, right?
Dan McCoy: Yeah, it is what you can pound your chest about.
And the, new mix is no slouch. You just took over a hundred pounds of powder out of it. And increase the water cement ratio but by just by the basic math volumes by themselves, even increasing the water cement ratio with a lower amount of cement still means we're not putting as much water into the mix as we were before, which is.
Less shrinkage volume to compensate for. So it makes sense from that standpoint of everything that we were doing. So those are the advancements that we've made. And that was our intent is something that was easy and workable for the contractor to place without all the inherent risks. Things could go wrong.
Plants could break down. You had time to work with it. The consistency of the mix stayed the same. And nano silica did a lot of that for us. 95 percent of that for us. So that's why I'm a believer in it. And then on the pump side pump jobs just go easier with a nano silica in there. And like I tell people that are considering using an internal cure E five it was like, listen if you're going to want this to pump easy, you're probably with this mix some of them can be pretty harsh.
If you're going to want this to pump easy, you're going to want a viscosity modifier in there. And then I tell them, but if you want a viscosity modifier and then not have to wet cure it, why don't you just, why don't you just get the E5? I just tell people that flat out because we've now poured in Indiana, hundreds of bridge decks.
And if there was going to be a systemic problem, we would have noticed it by now.
Seth: when, was the first one you did?
Dan McCoy: First bridge deck might've been 2000, 2020 was when we did the first E5 bridge deck.
And then later in the year and in the spring of the next year I internally threw up and threw in dots concrete design out the window and came up with something we thought would work and took all the risk. And then it was big for us, right? Because you're taking a tried and true thing.
That's in a book that's already covered. In the specifications of this is how you do it. And this is what you use. And I just thought we could do better. So we did that, took the risk and it worked. One of the first structures we did with the V580 mix was it wasn't a wimp try.
It wasn't like you could rip a deck out and redo it. This was a slab top bridge, so the slab itself was the superstructure. So in retrospect, maybe I shouldn't have tried it on that kind of structure first, but I was confident in the strength gain. I, knew that we would meet our minimum compressive strength and, if we did that, even with a lower cement volume it wouldn't matter because we met our minimum compressive strength.
It's just all the other additional benefits we were going for. And then we thought if we can do it with less why not?
Seth: I don't have any bridge experience, bridge construction experience, but I assume that you need those things to be in service pretty quick, right? You don't have the luxury of waiting two weeks for this thing to cure up and to be used.
Dan McCoy: That's interesting. There are and I think that's why INDOT is perceived to be ahead of the game. We go from a seven day wet cure, which is what a lot of people in the Midwest were doing a lot of people were to basically a single sheet of plastic over it. Now for a year we went through putting a white pig down.
I continued to pour bridge decks. For counties and municipalities on an experimental basis where I did nothing. I did nothing to the post treatment of the deck. We poured it, we tined it, and we walked away. And that was my evidence that the belt and suspenders that are throughout the DOTs now, we're going to have success with.
Because they're protecting it even more than I was for placing bridge and letting it go. But yeah, you're right some other DOTs, I said that to get to the point that some other DOTs, for example, Pennsylvania, still have a 14 day wet cure, regardless of strength. And you can't get on it, no construction loads, no live loads, no nothing.
NDOT, we could have... In the old days, if you did a seven day wet cure and you had a beam break of 550 PSI flexure, you could at least construction live load, you could begin to remove false work. You could begin that, you could still wet cure while loading. In theory, you could run traffic across it, but you still had to do the wet cure.
So there's no, way, there's no way you're going to allow live traffic to go over wet cure. So, so yeah you had to wait until the wet cure was up. And then it was easier to do the other things like place the parapet walls. Place railing, guardrail, all that other stuff. But when we went to this new method, yes it was, possible for us to increase our downtime and waiting, which is a good thing.
Don't say it too loud. I don't want the guys in, in, in contracts and specs to think that we can speed up every bridge job now, but it's nice to have that extra, it's nice to have that extra. miracle or ace in your hole. If things get tight you can push it a little bit and it'll take it.
Seth: It's called schedule float, Dan.
Dan McCoy: Yeah, schedule float, yeah.
Right, right. Yeah, so I, but yeah, that it's, nice to have that in your pocket. Like I said I'm, an optimistic engineer, but I'm still realistic and I still think that once it's up to its compressive design load you're good to go. Yeah. And if you design the mix right, it should get there when you think it should get there, which should be around seven days, a little less than seven days.
And that, I think that's fine. I think that's fine. If you want to go high early, I think you're being detrimental to the life cycle of the structure. So what is that extra four days’ worth? Is it worth 15 years at the end of the life? I don't think so.
So the ideal mix what did that look like as far as aggregate sand?
Like what size aggregate did you guys change anything from what you were doing to standard mix before?
So the in the one, way that in dot is backwards, I think, is we have our own aggregate requirement. And they're called in dot eights the AP source material. I, think the.
that there are some other states, Ohio I may be a little bit jealous because their, aggregate selection is a little bit, it's a little bit wider. So it gives you a little more freedom in, in that gradation and you end up with a better aggregate gradation, sometimes more than a gap graded aggregate.
So but as far as that, when you obviously, when you reduce, that's one of the things I was concerned of as a concrete pumper is if, the big thing in the future is going to be to reduce CO two. And one of the things we've reduced CO2 is by reducing cement content. And by that, what I mean is less paste.
Which is scary to a pump guy, right? We like that paste. That's what coats our line. That's what makes everything pump easier. So, I was looking at more wear and tear on our concrete pumps. Then I would be so I, wanted to get involved and say, Hey, we, if we're going to reduce if the end result to reduce CO2 is to reduce the cement content by optimized mix design, let's make sure we've got a mix we can work with.
Let's get out ahead of the curve until we run into problems on the construction side, which on a job site is the last place you want to run into problems with a mix.
Seth: you say that you use number eight most of the time. Yep. Which is about size of pea gravel, right?
Dan McCoy: No. N. 8 is all different than what you're thinking.
So, but N. 8 is a, it's a three quarter inch aggregate.
Seth: Okay. Three quarter inch. Okay.
Dan McCoy: Yeah. Very, similar to, oh, what's Ohio, let's say C57. Well, down here,
Seth: yeah, we call, yeah, Virginia is 57.
Dan McCoy: 57. So it's very similar to that. And I like the 57s a little better because I think they're aggregate gradations better.
It works into the work that Tyler Lay's done with the optimized, the tarantula curve, the optimized mixed design. Okay. It probably fits a little better without adding an intermediate than our No. 8s do.
Seth: Okay. I gotcha. I was wondering what y'all are using. If, folks want to mirror what you're working on is like, Hey, up in Indiana, they got this weird aggregate that they use and that's why they're successful or something.
Dan McCoy: No, it's no, it's we're a limestone rich state and so it's all, limestone. And hence it's a little softer, limestone is pretty soft. So, excuse me, the most the most you're going to get out of a limestone is 11, 12, 000 PSI. And not that it's our intent to do, it's just a softer rock and those are the gradations we have.
This mix would work just as well with 57s, maybe even more so you could probably dial it down a little bit more because of the gradation is just a little bit better.
Seth: what other additives or admixtures have you seen? I guess been able to reduce or any changes there as well.
I've heard things like plasticizers, reduction of use of plasticizer and things like that. When you're using nano silica. It depends on what you want to do with the mix.
Dan McCoy: Yeah, you're absolutely right. So the, all of those are based on a hundred weight and most of those dosage rates are based on a hundred weight of the cement.
Seth: Oh, okay. Yeah. Good point.
Dan McCoy: So if you reduce the cement, then you inherently reduce the admixture dosage. One of the things I do like, and Dr. Belkowitz can get into it more and Tyler Ley's actually got a great video on it, that but it's how polycarboxylates work really well in concrete and how well they work with a nano silica.
So the addition of a polycarboxylate in there. So it. A high range water reducer even at a lower dosage really helps to, propagate that hydration and all the good stuff that happens in concrete. They just work really well together. Do you need it? No, I don't think you do.
And when I, wanted in, it's definitely not for a slump modification because I, the concrete pump is the ultimate lie detector. You can bring me an 8 inch slump that's all chemical and my pump will tell you there's no water in it. It may act like it, but it's not. It's the water slump that matters.
So find a water slump that you like. And if you want or, need to modify that mix in terms of strength or get the most performance out of it that you can, that's why I ask people to add a polycarboxylate or a high range water reducer. It's not for workability. I don't, I mean, it is in the industry but for me, I don't request it because I want more chemical slump.
I request it because in, in the end of the paste matrix, it just. Man really helps that nano silica find that cement and really bond well to the aggregate. Okay, it does a lot for the concrete strength in general, but the reason that's working for the concrete strength is because you're getting so, you're getting really good with your hydration and you're getting really good with your bonding.
Yeah, that’s one of the things we noticed with the overlays the overlays were getting twice as good as results from pull offs as the silica fume overlays were in with 100 and 120 or 130 pounds less cement or paste content. So that's pretty impressive. We're using less to get more with a higher water cement ratio.
Good to figure. So it really tells you that all that good stuff that you're going for in nano silica is love water anyway, so they will find that unhydrated cement in the sub base and they will latch onto it.
Seth: It's cool stuff. And it's great to hear your point of view being a contractor.
Cause we've had other folks on the podcast from. Dr. Belkowitz to Joe Shetterly has been on here. Joe's used his own stuff. He was a contractor at one time too. but it's still good to hear from somebody that's not selling the stuff, their experience with it.
What happened before they used it and what positives they've seen after using it.
Dan McCoy: I tell people all the time, listen I don't know if Joe, I don't know if Joe lucked out and just got it right and found something that worked. He could have, because there's literally an unlimited amount of combinations.
You could make nano silica at, and some of them will work and some of them, they won't work at all. When it comes down to solids content, it comes down to particle size, particle charge, Joe, just Joe and his team got it right. They just got it right with internal cure and liquid fly ash.
Each one does something different, but I'm I am pretty sure that's a very specific nano silica, and there are other people out there or, other combinations of, nano silica you can use, and you're going to get different performances out of each. It's just so happens that the right the right combination of whatever the team at Speck Pro did.
Works really well. Yeah, so Dr. Jon and I go back and forth about what is it because we're on the STM committee and John's writing it for what? Is a nano silica and we're not trying to define what a nano silica does for concrete We're just trying to define what a nano silica is Who can market it and prove that they have the ASTM qualification to call themselves a true nano silica and not a silicate or, other uses.
So it's hard to find. I'm just saying there's a million and one different combinations out there used for different reasons, but the guys at SpecPro just found it. It's just found it in everything I've done. I'm like, I'm an engineer constantly looking for problems. I know. I shouldn't be.
I should just let it go and be happy. But I'm always looking for Something to go wrong. And in the years that we've been using this and really looking at it not like any other concrete where we just look and see when something new comes up and you start using it, you really want to see the differences and for as much scrutiny as it's had, I've seen all benefits and no problems.
Seth: You're validating some of my concerns as far as well, not validating, but addressing my concerns. Like I said, I've heard from others, and they might have some benefit in telling me that stuff is great, and they might, have earn some percentage of sales or something like that was my fear.
And they were selling me on something that didn't actually work. So it's great to hear from a contractor so that I appreciate you coming on the show and sharing your experience.
Dan McCoy: Anytime and there's a million and one different things we just did a you, wanted to talk about overall infrastructure and some other things that we were doing within DOT.
We just completed our first accelerated bridge track.
Seth: Well, we'll save that if you're willing to come back on the show, we'll say, we'll save that for another episode. Cause I think we could do a whole new episode on that one.
Dan McCoy: We can, but yeah, if you want to talk about that, but we've been using ultra high performance concrete in the, last several months.
With some really stuff, really cool stuff even though it's called concrete, man, it's more like a composite bulletproof material.
Seth: I do want to talk to you about that. Cause I've had one creator of that on the show as well. I haven't circled back to that in a while.
So that'd be a good episode to talk to you about if you're willing to come back on.
Dan McCoy: Oh, absolutely. This is so much fun. Cause this is if you're listening right now, driving down the road, you're probably listening by yourself because nobody else likes to talk about concrete with you.
Seth: Your wife and kids don't like to listen to you?
Dan McCoy: They don't like to get into what we're doing but this is, this stuff is so much fun for us and that it's, just a lot of it's, a lot of passion for wanting to do better in, in your professional life, I mean it's to ask the things you're doing in it the things you want to get out of it. And I, love being able to tell people with some of the bridges that I built. My grandkids won't even have to replace it. That's awesome. That's cool to be able to design a structure with that kind of life cycle structurally.
Now, as Dr. Jon and I have talked about before. If Urban Sprawl continues to develop, it may render itself obsolete by traffic design. But by structure design, it'll be there. So it's cool to get to the point where now you're, we're back to building a hundred year structures.
Seth: All right. Well, we'll end this one today and then we'll get you back on here. Hopefully not too long. If folks want to reach out to you, Dan, and learn more about what you're doing what's the best way to get ahold of you.
Dan McCoy: Oh, email. Email is great. And that's DanMcCoy@rlmccoy.Net.
if anybody wants to get a hold of me and be tortured to hear me talk about engineering concrete infrastructure. We didn't even get to nuclear power.
We touched a nano of all the things in smart infrastructure and infrastructure development that's been going on in the last six, seven years. And it's really picked up, but it's really exciting.
It's an exciting time to be doing concrete.
Seth: Yeah, well, like I said we'll end this one today and we'll circle back. Thanks, Dan, for coming on the show.
Dan McCoy: Thanks, Seth. It was awesome. Anytime.
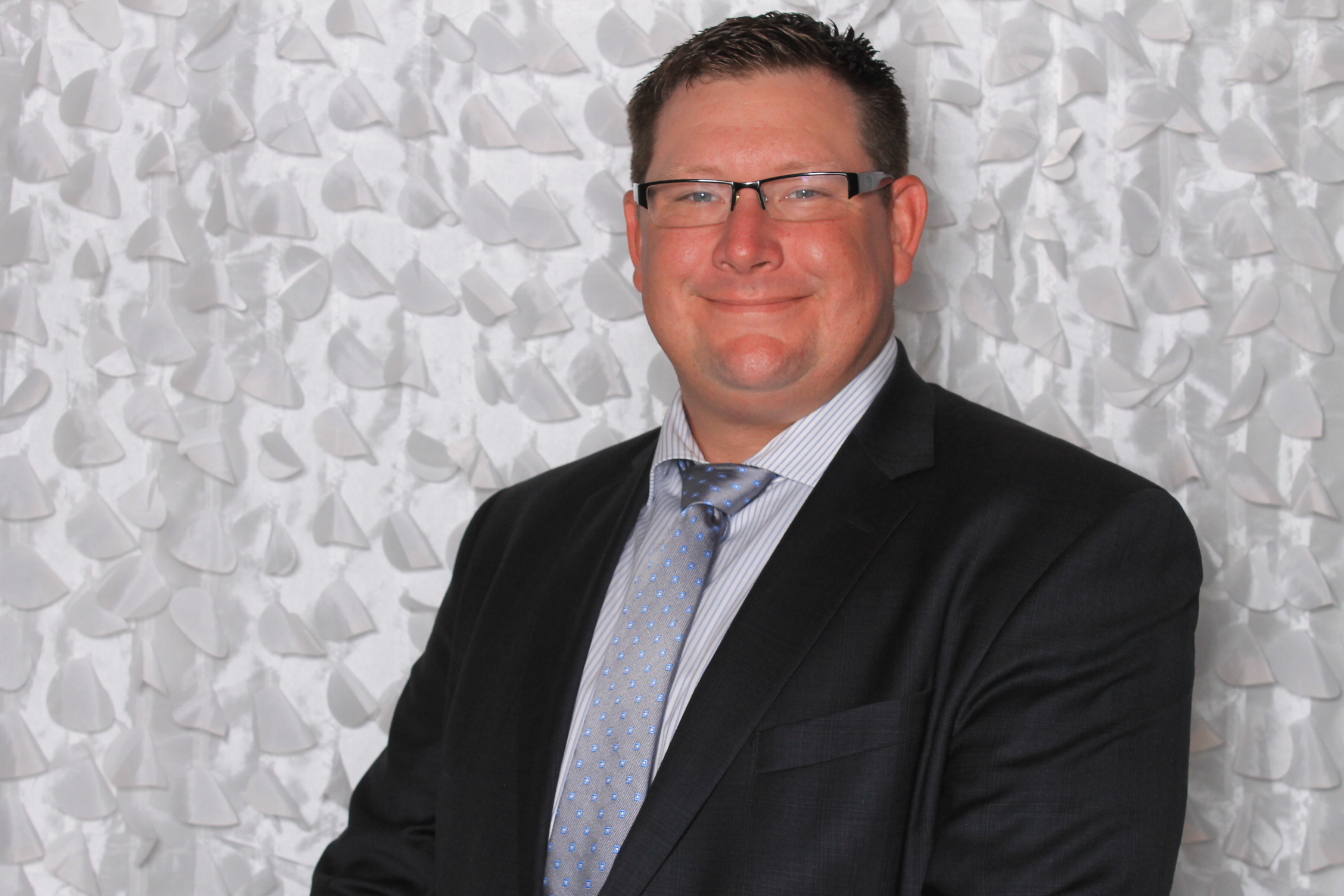
Dan McCoy
Engineer
Dan is a third-generation bridge builder, 2nd generation concrete pumper, and first-generation engineer. He has 27 years of construction and concrete experience with a passion for improving infrastructure and improving daily life (and commutes!). Dan has worked as a contractor in an experimental capacity with the Indiana Department of Transportation and Universities to seek out new and innovative means, methods and materials used in the construction industry. Most recently Dan has been a part of an initiative to improve concrete performance, workability, and lifecycle for concrete used in Indiana Heavy Highway Infrastructure by implementing changes to the design and specification of concrete as it relates to nano silica in concrete. More specifically, the uses of E5 and Liquid Fly Ash as well as other topical solutions involving nano silica. Dan is a lover of SMART infrastructure, and all things that go along with it! He is married to his wife of 18 years, Hillary, and has 3 boys that are actively trying to kill him 78% of the time.