EP #063: The Future of Concrete is Robotic
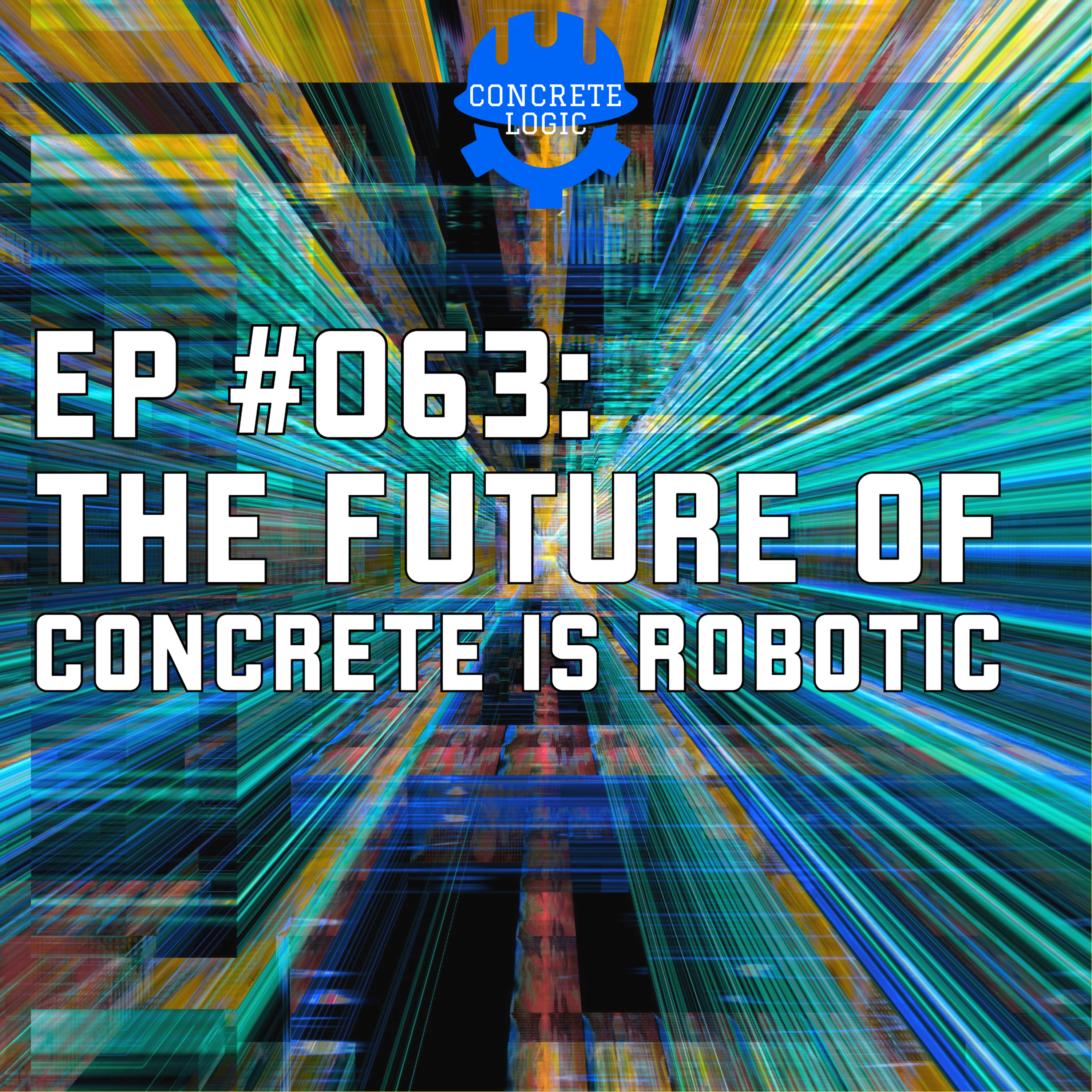
In this riveting episode of the Concrete Logic podcast, we’re thrilled to have Danielle Proctor, the CEO of Advanced Construction Robotics, as our special guest. Danielle, with her 25 years of experience in technology construction, new product development, and leadership, will be sharing her insights on the role of robotics in the construction industry. We’ll be diving deep into the workings of Tybot and Ironbot, two revolutionary robotic tools transforming how we approach concrete construction.
This is an episode you won’t want to miss, especially if you’re interested in the intersection of technology and construction. Danielle’s expertise and the innovative solutions her company is bringing to the table are truly game-changing. Join us as we explore how robotics is filling the labor gap, increasing efficiency, and redefining the future of the concrete industry.
***
Did you learn something from this episode? If so, please consider donating to the show to help us continue to provide high-quality content for the concrete industry.
Donate here: https://www.concretelogicpodcast.com/support/
***
Episode References
Guest: Danielle Proctor | Advanced Construction Robots | bnelson@constructionrobots.com
Guest Website: https://www.constructionrobots.com/
Producers: Jodi Tandett, Olivia Stocker
Donate & Become a Producer: https://www.concretelogicpodcast.com/support/
Music: Mike Dunton | https://www.mikeduntonmusic.com | mikeduntonmusic@gmail.com | Instagram @Mike_Dunton
Host: Seth Tandett, seth@concretelogicpodcast.com
Host LinkedIn: https://www.linkedin.com/in/seth-tandett/
Website: https://www.concretelogicpodcast.com/
LinkedIn: https://www.linkedin.com/company/concrete-logic-podcast
Seth: Welcome to another episode of the Concrete Logic podcast. And today I'm excited. I got Danielle Proctor from Advanced Construction Robotics. She's the CEO. She brings over 25 years of technology construction and new product development and leadership experience. Just a slew of experience. But what we're going to talk today is about robotics.
You, you all might've, I know I'm I've been following them for a while. First heard about Tybot I think about a year ago. And then I've been Trying to get the folks to come over here on the podcast and we finally lined up schedule. So it's awesome. Danielle, thank you for coming on the show.
Danielle Proctor: Thanks for having me. Appreciate it.
Seth: Yeah. Could you just give us a little bit of background on what Advanced Construction Robotics is? And then we'll talk about specifically about the Tybot and IronBot, and then we'll just roll with some questions that I have.
Danielle Proctor: Yeah, absolutely. Advanced Construction Robotics.
We are the leading developer of robotic equipment for the construction industry. This company actually was started out of a need by a contractor. So our founder and funder Stephen mock from Brayman Construction he, saw this labor gap and shortage occurring probably even pre COVID and started realizing, in order to make this workforce basically a little bit more modern and help with the gap of labor shortage and increasing demand automation and autonomy was going to be the help. So he builds bridges. He's ties a lot of rebar, lays a lot of bar, and he came up with this idea of Tybot.
And that was probably about. Five years ago since then we put out nine Tybots and we've just also released the new Ironbot, but Advanced Construction Robotics, essentially, we want to be able to help augment our construction crews and take away the dull, the dirty, the dangerous, repetitive tasks to make the skilled labor force more effective.
Seth: Yeah, and you picked one of the dirtiest jobs out there to start with.,
Danielle Proctor: Have you laid bar? It's not fun.
Seth: It's not fun. I I've touched rebar. I've, pretended I've, laid rebar, but no, I have utmost respect for the iron workers out there, the rod busters. They definitely have one of the hardest jobs out there.
So when I saw this robot that y'all have. I was like, oh, that makes, it makes a ton of sense. Especially what you what you guys started with as far as going after the rebar installation. But I think the Ironbot, that maybe the easiest thing to do is maybe share a video of the Tybot first.
Yeah. Usually we're an audio only podcast, but to get a kind of idea what this thing does, I think we'll, share a video here and you and I will do our best to describe what's going on.
Danielle Proctor: That sounds good. Yeah. I think that's the best way for anybody who hasn't ever touched Rebar.
I know Concrete and Rebar are twins and hand in hand, but I think, yeah, let's roll a video and we can walk them through it.
Seth: Yeah. Let's see here. So I found this video here from y'all's website. It looks like you worked with Shelby Erectors. So I'll just play it here.
What this reminds me of is it's a gantry, right? It's a gantry that goes over the top of and most of the stuff y'all are doing right now is bridges. Is that right?
Danielle Proctor: Yeah, we're primarily in bridge decks. The technology can be applied to any other larger horizontal rebar So we did a pilot with tilt up walls, ground slabs this would go anywhere that there are as rebar being placed and tied these, this application can be addressed.
So what you're seeing here is Tybot. It is a gantry. We don't really talk about them as robots. We talk about them as modern tools of the trade and we, want it to look as least scary as possible. So you are 100 percent correct. The gantry system. It's very similar to the bid.
Well, system. That comes out there to pour and finish the concrete. So the goal was to try and minimize disruption and any current. Construction processes, so we already knew that the screed wells would be there. So Tybots, they're sitting on the screed rail. It's expandable. So it can go from 9 foot to 117 foot wide and we just replace those.
You see those truss sections in the middle. Those just can keep on moving out. Or in the smarts of the product is right there where that time module head is. And that's called the tram. There's dual cameras and I'd love to say it's a little bit more exciting. There's, a lot of work putting in to make this thing as simple as possible.
That is our goal. We want to keep things simple. So once the Tybot is assembled and put on the bridge, it takes about maybe two to four hours to lift and get it up and running. You have a belly box, you give it a couple simple commands where its area of work's gonna start, whether you want it to tie at 50 percent or 100 percent coverage, and you hit go.
Those cameras now are actively watching the grid, and any time it sees an intersection, it's gonna tie it. So literally, Tybot is just looking for this. So if you put your fingers, it would tie it as well. It's not that's it's been given one dedicated task. And that's the fun thing with robotics is we train these to do one thing very well.
So as soon as Tybot gets up and running, it will self-locate, it will self-position, self-tie there's no mapping, there's no programming, there's no BIM input and it can do so pretty much 24, seven rain or shine night or day.
Seth: I noticed that there was no pre mapping requirement, so you don't have to tell it what's coming out.
So it actually looks for the intersection of two rebar lengths overlapping each other. So that 90 degree, it's looking for that 90-degree intersection and doing a tie. And I saw something or heard something that you do a lot of work in Florida and they, I guess they had a requirement of double wire versus single wire.
Did you guys figure that out or how did you guys deal with that challenge?
Danielle Proctor: I have to give a bit of a shout out to Florida DOT and the highway when Tybot first came in, Florida has probably been one of our more active areas just by the sheer amount of quantity of work that they're doing.
So when we got on site, we had a meeting with the highway. And we showed them the Tybot. We showed them the ties that we were making the consistency. And they actually added a specification into their standards to allow for Tybot to perform in Florida. So it went from a double snap every 3rd.
And they adjusted it and provided a provision where you also had the option to use the Tybot technology and you could do single snap every other.
Seth: Oh, okay. So just more ties. And it does, top and bottom mat. So you would do the bottom at first and then run and do the top mat.
Is that how y'all operate?
Danielle Proctor: So essentially, we still need a crew. This is truly augmenting the bulk time portion of the project. So there's still a crew out there. Once the bar is laid they have to frame tie it and get everything ready for to come through can cover approximately 85 percent of the deck.
So you still have about 15 percent that's being manually tied either located one and a half foot on either side of the rails where the tram can't get to and then if there are any missed ties. So we have a robot supervisor with the technology when we provide them, their only job is to look over and support the robot, but Shelby is an excellent example.
They've trained their own group of robot supervisors. So their rod busters are doing both jobs. So once that thing's running, you literally see this belly box go on their hip. So they're still working alongside of the Tybot while it handles the bulk ties. About 85 percent of the structure.
Seth: It looks like for us concrete guys; it looks like the same remote box that we have for concrete pumps except for he's not active.
It's not as active as a pump. He just, like you said, you're just telling it to start. And I guess you got to tell it how many ties are required to in that box?
Danielle Proctor: No. All you're doing is letting it know what type percentages you want. Again moving forward in the innovation side of this, we will be releasing Tybot probably Q1.
We'll start being able to do a 3rd so that we're working again with Florida to get that pushed through. We adapt. We want to hear from our customers. Shelby's what we call an integration partner. So whenever we have new technology, we're sending it out to the site. The interesting thing about robotics and technology these days is you have to have a problem to solve.
And once you identify that problem, we can hit it very hard. You want to stay away from creating cool technology. That's looking for a problem. So it's been great working with our concrete contractors just cause we get feedback, and we listen to it, and we can get that into the development plan for
them.
Seth: That's the unfortunate thing is some of the robotics out there, some of the technology out there, I think they're just fishing for the problem.
Danielle Proctor: It's so cool. We're not sure yet. And that's not knocking. There's some great construction technology out there. We're, just seeing this market boom.
We're really excited to be a part of it.
Seth: And then as far as the job site requirements, what, do you have to have there for, the machine to run as far as power, cranes that kind of stuff.
Danielle Proctor: You need crane support to get it lifted on the bridge max configuration.
You're maybe looking at about like 6,000 pounds. So it's not horrible. We did design this though that the load bearings we were less because the Bid-Wells are going to be going out with heavy concrete. So our load is significantly less. So you need lay down area. You need a crane. The screed rail should be installed in the event that it isn't.
We also did just release a new version of Tybot that can run on the edge forms, which is great. So from a two by four to two by eight, if the edge forms are up, we can still get the unit on there and. Rebar that's laid down and ready to tie. Yeah, you're good to go.
Seth: Gotcha. So it and black Bar epoxy bar doesn't matter, right?
Nope. No.
The machine itself, the head of it looks like there's the handheld version of the tie. I forgot what that thing's called. I've seen it a couple times. But for the guys that can't manually tie with a pair of pliers, there's the machine.
That's what kind of the head of this machine looks like.
Danielle Proctor: Yeah, it's similar. Again when we're designing this technology, we want it to be as accommodating and accepting with the crew, right? So we want it to look and feel similar. So you're exactly right. If the guys aren't out there with a hip reel, they're using tie guns and then this would be the next level, which is an automated time module each unit comes with three of them.
So it's feeding its wire. So the other interesting thing about Tybot is it can carry a 15-pound spool of wire, so you're only changing wire, maybe twice. On a really good day, 3 times, so it's just constantly feeding itself at almost a 5 X capacity of what's usually being out there with the hip or the guns.
And like I said, each unit comes with three of them. So in the event that is your wear component in the event that there's any issues, if it jams or you need to swap it out it's just a quick interchange, you unhook two hooks underneath, you flip it out, pull it in and you're back up and running maybe within 30 to 45 seconds.
Seth: And, did I read the tie rate right? It was like 1200 ties an hour. Is that right?
Danielle Proctor: Yeah. And it keeps on getting better. I wish I could have shown you a video of when Tybot did it very first time. It's learning that is the kind of the growth of these technologies.
Yeah, we're 12, 1300. We just hit a job up in Illinois. I think our max active rate was getting upwards of 1600.
Seth: Oh, wow.
Danielle Proctor: And things that will affect that is sometimes your environment chair placement. Definitely. It'll help early, but an ideally placed rebar, which as in the construction industry, every job is different.
Everyone has a personality. We're now seeing anywhere between 13 to 1500 ties per hour.
Seth: The ones, and we'll, get to Ironbot here in a minute, but for the projects that you've had just to Tybot at, so the guys are getting out there and they're actually laying the bar down and, but the robot is just looking for those intersections.
So if the guys are off. A little bit an inch or so. It doesn't matter. Is that what you're getting at?
Danielle Proctor: It's not a problem. It does not have to be a perfect. I think you'll see if there's some video footage out there who anybody's listening wants to check it out. We actually call it rebar vision so you can see how Tybots looking at it and it just understands if there's X percentage of a gap, it's going to go for it.
It'll try every if it misses an intersection, it's going to try 3 times. Usually, we just, the consistency rate on this is pretty, pretty good but it will try three times, and then in the event that it can't recognize the intersection, it'll just move along. And that's where that robot supervisor who is a rod buster, can then just click it real quick.
Seth: All right. Let's take a look at the IronBot.
Danielle Proctor: Yeah, the big one, the big boy.
Seth: This one if you can explain what it's doing here, but we'll pop this video on here.
So it looks like this actually, the, this is a separate robot, right?
Danielle Proctor: So different gantry system. Correct. It's bigger.
Seth: This actually lays out the bars.
Danielle Proctor: So IronBot will lift, carry and place up to 5, 000-pound bundles of rebar. So once the bundles are dropped off on the site, either they, get dropped on the deck Ironbot then will travel along that exact same screen rail system.
It'll go pick up the bundles. It uses just some it's just a hoist. And then it'll carry the bundle back to where it needs to start working. Same kind of belly box environment. We're now letting it know this is your area of work start. This is the spacing I want.
So do you want 6? Do you want 8? Do you want 12 inches? And then whether we are placing in a transverse or longitudinal direction, you hit start. Ironbot is a little bit, if you compare the two Tybot is the smarts and Ironbots like the muscle and heavy lifting. So it's a little bit less autonomous than Tybot in the fact that we need, I don't know if the video is going to come up, you need one of those rod busters, basically what we call singulating the bar.
So what they're doing is those big tires that are all running, that's helping us grab the rebar. So you have one person that'll feed that rebar. Into the roll index, and then it drops it into the cradles. Ironbots autonomy is it's like a dog with a bone. All it wants to do is as soon as it sees a bar, it wants to grab it with its grippers and place it down at the specified spacing.
So this one usually takes, we're seeing anywhere between 5 to 7 rod busters to run this operation. Again, we go back to how do we work with our crews. How do we augment and just provide them? A tool of the trade, right?
Seth: Yeah. I was going to ask you that the fella at the end there looks like he's just grabbing the end of the bar and flipping it over.
That's what you're talking about.
Danielle Proctor: Yeah. We call that singulating. So it's but those again, people out there who have dealt with bar the short of the bar it's not as a flimsy, but those are 60-foot bars. Yeah, you can see the spaghetti going on. So to be able to place we're seeing any anywhere up to depending on how the site is optimized.
You're looking at anywhere between 5 to 6,000 pounds per man hour. That's going down.
Seth: That's fantastic. I assume if you have an IronBot on the job, you probably have a TyBot too, is that it?
Danielle Proctor: Absolutely. Those two definitely like to stay together. Right. We've just completed our second project with IronBot, like as I mentioned, it's just come out this year.
So we're already seeing, it's been great. If both times keep the same crew, again, you keep the people, and we were able to cut both of those schedules in half. with IronBot and Tybot working together. So now your crew is more of the skilled functions of the job, right? You still have all the auxiliary still, you got the barrier bars, that crew's still placing, just like Iron Tybot's tying 85%, IronBot's handling about 90% of the bar.
All the other bars still need to be hand placed and double checked. So now you have the lift, the carry. It's starting to place, kick them into place, you make sure as it's going, you frame tie and then Tybot comes up behind and you continue the operations.
Seth: Ironbot and the Tybot, did they go on the same rail or do you gotta take one off and put one on or?
Danielle Proctor: Nope. They go on the same rail in the event that we need to hop 'em, you just grab the crane, and you can flip 'em, or we can put two Tybots out.
We're starting to see an acceleration where Tybot has to work a little bit longer to keep up with Ironbot which has been fun to see.
Seth: Oh, yeah, that makes sense.
Danielle Proctor: Yeah, so let's say IronBot's working an eight-hour shift. Tybot, you'll see, is probably out there ten.
Seth: Yeah, and I saw a video.
You ran that Tybot for 19 hours straight.
Danielle Proctor: Yeah, that was a good job. They needed to be out of there pretty much within a day. So it was fun to work with that contractor because they understood technology is only effective and good as the pre planning or the understanding of how to use it.
So you can plug and play this stuff on any site, but you have to understand we're going to be moving faster. So now, how do you plan for that runway? So if we can get maybe a day and a half, 2 days of work, all laid out, ready to go, that's what the contractor did. They actually Worked their entire crew and then left the crew and Tybot was able to work through the evening.
I don't know if you see that video. We're out of Pittsburgh. That's a Permani sandwich. We are known for a famous sandwich here in Pittsburgh. So that was a fun job. And the and the crew was able to go get a quick snack at their favorite restaurant.
Seth: I was going through your list of requirements and questions about your machines here.
There was a mention of a generator for power. Is that something you all provide?
Danielle Proctor: All of the units come with Cummins generator or diesel engine. So we have self-power on all of these units. We also do have a shore power option. So in the event that somebody would want to use a generator on site we have the leads that you can do that.
So it can be run both self or generator power.
it's better usually to use our generator.
Seth: Yeah, imagine a lot of the job sites you get to I, personally don't do a lot of bridge work, but I imagine There's not a local source of power or anything for you guys to hook up to.
Danielle Proctor: no, but if you start looking at as you start. The technology, the key components of the technology, Are the tying and the placing. So now we can start maybe looking at adapting these into other adjacent markets. let's say a precast or prefab facility indoors, that thing's on shore power.
Seth: Oh, you need to talk to some precasters then, huh?
Danielle Proctor: Yeah. I would love to talk to some precasters. We've already had discussions there's It's been great. The response the reason we're starting with bridges is because it's what we know. And again our chair and our founder, we have access to all of his bridge jobs.
So we can learn. We can test. We want to make sure that we are addressing the problem and then as we expand, it's adapting the technology for different modes of deployment or, Different modes of delivery. Some of them will be right out of the box and then some of them we would love to talk with people and more than happy to see how and if we could accommodate or change the technology to fit their specific application.
Seth: that's cool that y'all are testing it out on your own projects first. I think that's a key for a lot of the at least in the, technologies in concrete. Those seem to be the ones that succeed as you got the history to go back to and say, hey, I, I'm so confident in what I'm doing here with this new technology that I put it on my own job.
Danielle Proctor: Seth, a hundred percent. I can talk about this, but without proof or some sort of confidence level we are talking about putting these things on projects that are under schedule and under pressure and under critical path. So we absolutely want to make sure whatever we're putting out, it works, and it works well and addresses the problem that needs to be addressed.
Seth: I've walked precast plants before. I could see this going in there. Pretty easy. Yeah. Some double T's So, we know about Tybot and Ironbot. Is there anything else y'all are working on? Anything else you're excited about? Is there any applications beyond bridges that you're working on that you're willing to share with us?
Danielle Proctor: we're definitely staying along the bridge path again because it's what we know. We're excited to continue and identify areas on the bridge suite where we can increase that value chain of automation because then you start providing an end-to-end solution. We're definitely looking at more applications on the bridge path as well as what we were talking about before.
Where are our kind of easy tweaks where we can continue down the path on concrete? Industrial manufacturing, wind farms, there's a lot of bar out there and we're looking at them on both ways. And looking for partners to work with to explore how we could improve their efficiencies.
Seth: are you only looking at this as far as a horizontal application or are you looking at any vertical?
Danielle Proctor: Yeah, I know. I know. That is so like, that's so cool. We're a ways from that. Yeah. But we can go horizontal multi story, right? So absolutely we can start looking at how can we help alleviate some of the commercial or the high rise situations.
Vertical is definitely it's one that I'd love to see. That'll take a little bit of time, but we're absolutely attacking the horizontal rebar side of things.
Seth: When I saw that you figured out the putting these on the bulkhead. To roll them on the bulkhead instead of having the screed rails there, then I was like, now I see where you can move from the heavy civil bridge application to some more commercial applications.
Danielle Proctor: We started out with the Porter rail system. So we have like elevated ones that sit on if you're like for CRCP, right? So that's another market where there's literally miles of this stuff. I think there's about 8 or 9 states that are actively putting rebar CRCP. We're talking to some people about that and there is a bit of a funny story is in hindsight the edge forms are like.
Okay. Why don't we just run on the edge for them? So I'd love to say that we are brilliant all the time. We're not but it's definitely fun to say, hey, how can we make this more simple for deployment? You don't want to over-tech stuff. Those edge forms coming out has been a lot of fun in the idea of just throwing some 2x4's or 2x6's down, it definitely opens some doors for us.
Seth: Is there anything else that we hadn't discussed that I overlooked that do you wanted to share with the Concrete Logic audience today?
Danielle Proctor: I'm really happy that I was invited to come and talk about this. This is something of passion. I actually started out in the software world and then made the obvious decision to start a I was a contractor for 15 years.
So I had a structural steel rehab repair as well as foundation drilling company here in Pittsburgh. So it's just fun to be able to merge this idea of where are we going in the future with one of the oldest trades and something that hasn't seen this level of revolution or innovation yet.
it's just fun. If there's anybody out there who is interested in what we're doing give us a buzz and more than happy to show you a demo. We have a Tybot demo that travels around the country. So you can see it in person and just looking forward to seeing what comes next.
Seth: Yeah, I saw your trailer. I was thinking you guys should maybe start looking at a mobile unit that you can lease out to folks to like prefab columns or something that's what I thought when I saw that trailer is I think I could prefab some small mats there with that thing.
Danielle Proctor: Seth, we know what you just did is what's making this so much fun is one of my favorite questions I ask people is if you could do a robot that could do...? It's so funny just seeing a smidge of what we are doing. It just starts like, oh, what about this? Or what about this? When we talk to these engineers, we've got really great team downstairs.
Some people who have been at the precipice of autonomous vehicles, they always laugh because I say, well, that would be impossible. And they said, no, Danielle it's actually interesting. The impossible is usually easier than what you would think is easy is impossible. And that's because you need humans.
You still need humans. You still need the crews. So it's been a fun ride. We're looking forward to seeing what comes next.
Seth: it's exciting to see folks that were in the trades or in construction and then they're now in this automation technology space. they get where we're all coming from, the folks that are still in the trades I think there's some disconnect there with some folks That are in the technology space and then they try to fix our problems when they haven't spent any time in our space.
Danielle Proctor: you bring up a good point. We're still in an adoption curve and it's an early adoption at that point. We can talk in theory of how this is going to enhance your overall organizational culture in the sense of estimating it and being in efficiencies, but we still got to work with the crews on site.
And there's some that are like. Oh, my gosh, this is great! And there's some that are no way. So we're good. We're working with them again. It's this idea of a tool of a trade has been very important for us to work with everybody. It's not taking jobs. It's actually providing a level of career longevity. If you think about it bending over that back breaking work, could you imagine if somebody who's back isn't working or they've gone through their 4th or 5th surgery, this provides an ability for them to maybe work for another 5 to 10 years because it's less stressful but they're still providing all that knowledge?
Because it's an art. I give full credit to the rodbuster. This is an art. There's a way to do it, and a way to do it fast and safely. We haven't even really touched on the safety side of things just walking across open, loose bar is dangerous. So IronBot, Tybot, being able to carry 5,000 pounds with no fear that you're going to fall or trip. The safety of it is a huge thing for us as well.
Seth: it's an enhancement. It's not a replacement. Danielle, I appreciate you coming on the show today. I will share with everyone in the show notes, her contact information and their website. So you can check it out and reach out to them.
Danielle, thank you for coming on the show.
Danielle Proctor: I appreciate it. Seth, thank you so much.
Seth: You too.
And until next time, keep it concrete.
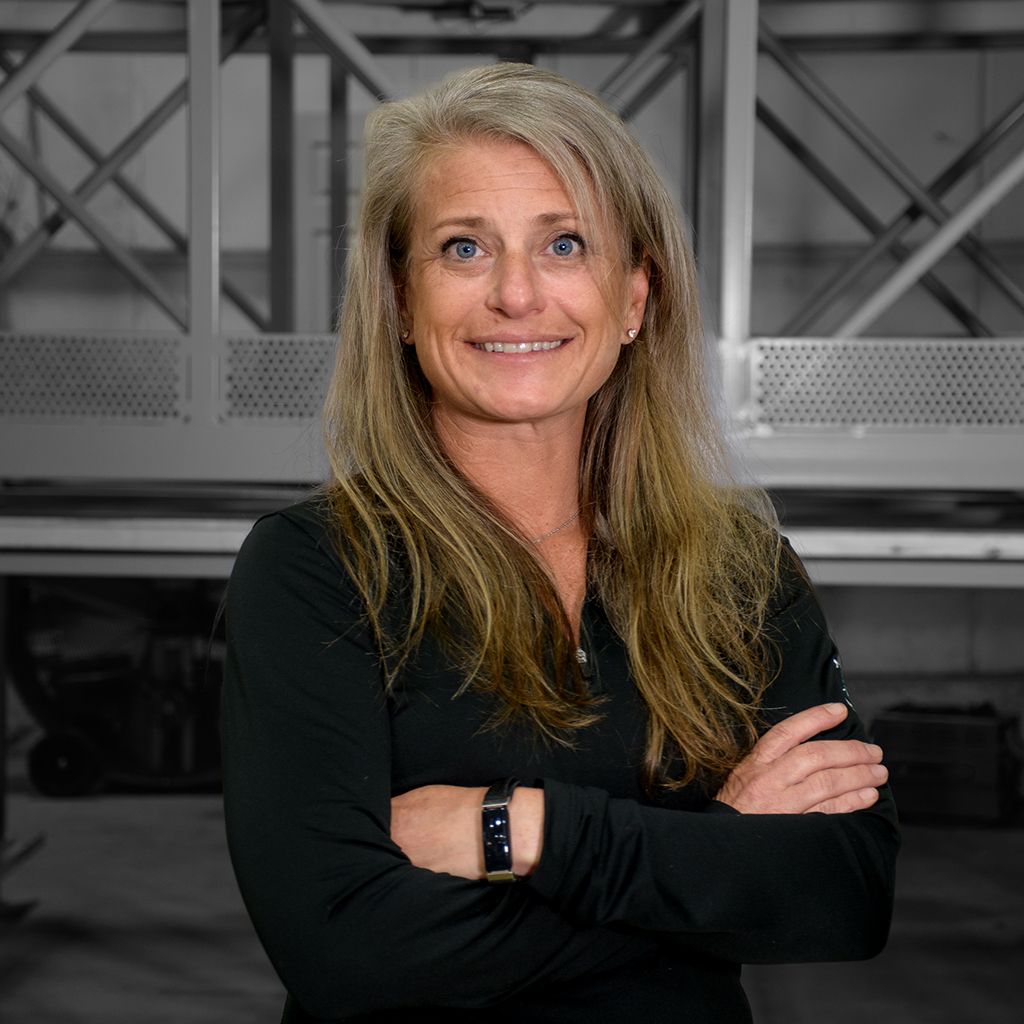
Danielle Proctor
CEO
Danielle A. Proctor joined the Advanced Construction Robotics, Inc. (ACR) team in 2020 as Director of Business Development and was named Chief Executive Officer in 2021, bringing over 25 years of technology, construction, new product development, and operational leadership experience. Danielle directs business strategy and operations, making ACR’s robots a commercial reality in the field.
Danielle got her start at the beginning of the software boom, working in product management and business development for business intelligence and analytical software firms, including Management Science Associates and FreeMarkets (later acquired by Ariba). Her entrepreneurial spirit quickly took over and, at the age of 28, she founded Amelie Construction & Supply, a certified Woman/Disadvantaged Business Enterprise (W/DBE) construction firm providing structural rehabilitation, erection, and foundation services where she served as President & CEO until selling her ownership in 2015. Danielle continued to pursue her passion of being involved with start-ups by forming several smaller ventures as well as providing consulting and private funding to companies during their critical formation stages until finding the perfect fit of launching new products into the construction industry with ACR.
Danielle obtained a B.S. in Industrial Management from Carnegie Mellon University