EP #066: UHPC, Not Your Grandma’s Concrete
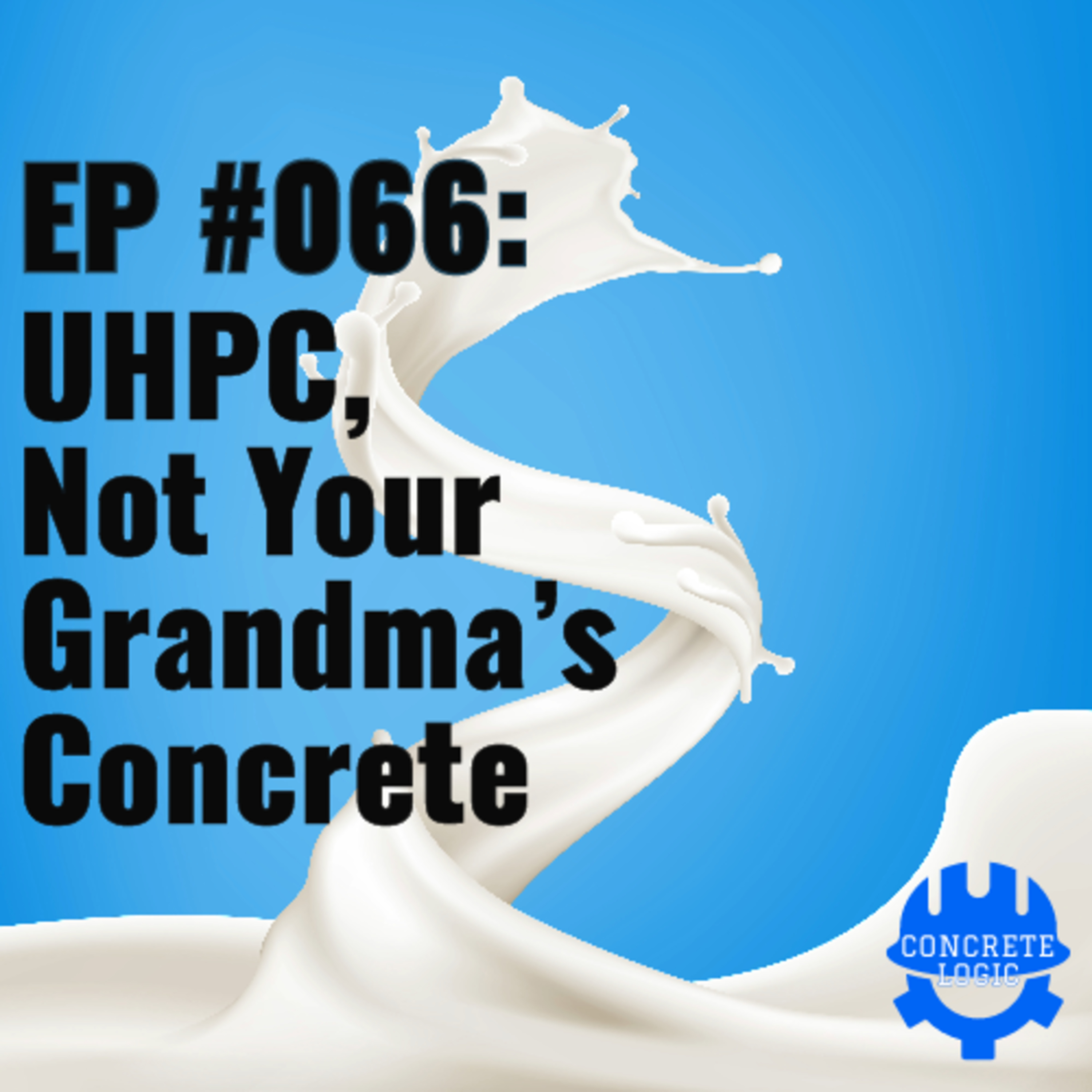
In this episode, Bill Kulish from Steelike discusses ultra-high-performance concrete (UHPC) and its applications in bridge construction.
UHPC is a composite material with a high binder content and a low water-cement ratio. It has superior compressive strength, tensile properties, and resistance to freeze-thaw cycles and chloride penetration. UHPC is commonly used for overlays, preservation, restoration, and repair of bridges.
Bill also explains the process of shotcreting UHPC and its potential for structural repairs and hardening.
Overall, UHPC offers a durable and sustainable solution for infrastructure projects.
Takeaways
- Ultra high-performance concrete (UHPC) is a composite material with a high binder content and a low water-cement ratio.
- UHPC has superior compressive strength, tensile properties, and resistance to freeze-thaw cycles and chloride penetration.
- UHPC is commonly used for overlays, preservation, restoration, and repair of bridges.
- Shotcreting UHPC offers a potential solution for structural repairs and hardening of various structures.
Chapters
00:00 Introduction and Value for Value
02:25 Introduction to Ultra High-Performance Concrete (UHPC)
08:19 Characteristics and Composition of UHPC
13:38 Applications of UHPC in Bridge Construction
19:50 UHPC Overlay without Profiling
25:48 Curing and Heat Generation in UHPC
32:38 Shotcrete Applications of UHPC
40:02 Conclusion and Future Topics
***
Did you learn something from this episode? If so, please consider donating to the show to help us continue to provide high-quality content for the concrete industry.
Donate here: https://www.concretelogicpodcast.com/support/
***
Episode References
Guest: Bill Kulish | Steelike, Inc. | Bill@steelike.com Guest Website: https://steelike.com/
Producers: Jodi Tandett, Olivia Stocker, Bill Kulish
Donate & Become a Producer: https://www.concretelogicpodcast.com/support/
Music: Mike Dunton | https://www.mikeduntonmusic.com | mikeduntonmusic@gmail.com | Instagram @Mike_Dunton
Host: Seth Tandett, seth@concretelogicpodcast.com
Host LinkedIn: https://www.linkedin.com/in/seth-tandett/
Website: https://www.concretelogicpodcast.com/
LinkedIn: https://www.linkedin.com/company/concrete-logic-podcast
Seth: [00:00:00] And welcome to another episode of the Concrete Logic podcast. And today I have another returning guest, Bill Kulish with Steelike. Bill, did I say your last name right? Should have checked with you before. Yes, you did. All right. Yes, you did. All right. He's gonna get us up to speed on ultra high-performance concrete.
And then remind me what that is, because we haven't talked about it for, I think he was on episode 34. And that was over 10 months ago, so I need a refresher Bill but before we get started, just a reminder, everybody the way this podcast works is it's a value for value. So if you get some value out of this podcast.
All I'm asking you is to return the value and you can do it in several different ways. One is share the podcast with a friend or a colleague or whoever you think would get something out of it. That's one way. The second way is if you go to our website, there is a microphone button on the bottom right [00:01:00] hand side.
If you click on that, you can actually record a voicemail to me. If you could go on there, if you've got a question, an idea for. Podcast hit that and record it and I'll send it to me. So that gives us an idea for podcasts and podcasts guests. So that is great. If you could do that. And then the third thing is again, back on the website, upper right-hand corner.
There's a donation button. You click on that. And like I said, if you get some value out of any of the podcast, if Bill says something to you today and you're like, Holy cow, I didn't know anything about ultra-high-performance concrete. Now I'm an ultra-high performance concrete guru. Or maybe not, who knows, but anyways, if you click on the donate button, you can donate any amount and any amount is appreciated.
It just helps us keep this thing going. With that Bill, Did I explain that...
Bill Kulish: very clear. Very clear.
I will be. I will be clicking one of those buttons. The last button when we're done.
Seth: Oh, Appreciate that.
Bill Kulish: Bill is with [00:02:00] Steelike, and Steelike is ultra-high-performance concrete.
Seth: What would we call your company?
Bill Kulish: A supplier of the material.
Seth: Okay. Yes. Inventor, right?
Bill Kulish: I'm the inventor. I have many letters, but basically, we're a small company. It's my wife and I, my wife's the CEO. She left a cushy job at DuPont, believes in the material enough. And that was back in 2018, 19.
And we've been charging full steam ahead ever since, but I invented it, designed it and I've been on, I used to say, every bridge project we've done, we've exceeded 50 and it's a good problem, but I had to let go of control. So now I have a good support team that is often on the project when I cannot get there.
Seth: Yeah, that way you can do more, right? Yes. Okay. Bill reminds us what ultra-high-performance concrete is and what separates it from normal concrete.
Bill Kulish: Absolutely. I'll start by just [00:03:00] changing one letter. So it's not the letter, but the what's ultra-high-performance concrete is actually ultra-high-performance composite.
It does, of course, have similarities with concrete, but. The largest aggregate. Is less than the diameter of a human hair. So where traditional 5K mix, 5,000 PSI mix, uh, might have a chunk of rock. For every chunk of rock, I'm replacing it with thousands of grains of different types of sands, different shapes, different mineral contents.
So that's one of the big differences. The other big difference is, it's a noncontiguous pore structure. So it, there's no channels left. When the material cures and hydrates, and because of that, there's no way for water to get in. There's no way for water to get out. And that also means that chlorides, salts, deicing agents, they can't get in.
Period. The other thing is [00:04:00] with a true UHPC, and I say that's that because you can Google it and you'll see companies offering unicorn dust to turn regular concrete into UHPC. It's frustrating with my colleagues and other suppliers, but a true UHPC, and there's really a handful of them globally, a true UHPC, the more you freeze and thaw it, the better it gets.
So you freeze and thaw steel, like 600 times, it goes from 100 percent to 104%. There is very little shrinkage. I'm not a mechanical engineer, but I surround myself with people smarter than I. And I said, here's my number. What does it mean? 427 micro strains. And they're like, blah, blah, blah. And then I said what does that mean?
Give me a football field. If I pour down, if I make something over a football field, how much is it going to shrink? It's going to shrink about eight inches. So there's the translation from science to just something we can all grab our head, wrap our head [00:05:00] our head around. Then we get into other benefits.
Quite often the big focus in our world, in your world, Seth, is compressive strength. Ah, I want compressive strength. Ah, it's really high compressive strength. Having really high compressive strength only. Is similar to going to your kitchen cabinet, pulling out a porcelain plate, which might be 50,000 psi and dropping it on the ground.
What does it do? It shatters. It's brittle. So UHPC is going to be brittle because it's extremely high compressive strengths. On average, it's all time related, temperature related, but we're always over 20-21,000 in 28 days at normal curing temperatures, 72 degrees. You can autoclave seal like, and it will be over 50,000 psi.
Yay! Who cares? You're not going to autoclave a bridge. So back to the real work. The material does have really good compressive [00:06:00] characteristics. More importantly, with that compression, with UHPC, there’s freeze thaw, abrasion resistance, chloride resistance, tensile is huge. The tensile properties of a true certified UHPC are remarkable.
To the extent that you'll actually get strain hardening. And I'll stop rambling in a second. I tend to get excited with your podcast, but you start to put a load on something. It cracks. You get your first visual crack. With normal concrete, you may get a couple seconds, and then you get catastrophic failure.
With UHPC, you get your first crack. It may be a visual crack, but there's millions of cracks occurring because of the metal fibers in most cases. Those metal fibers, redirect the beginning of the microscopic cracking the cracks are so small. They're watertight. We are talking invisible cracks within reason.
If you look at it under an electron [00:07:00] microscope, you would see things. But you would see things with any material you look at after that 1st crack occurs the fibers, the micro rebar, these half inch needle high tensile fibers. Start to carry the load of the stress, but then it goes back to the concrete.
And eventually a fiber slips, and then it goes back to the concrete. So in closure, you're doing a test, the strain goes up. And for those that can't see me, I'm just moving my finger upwards. Then you get your first crack, and it comes down. Then it goes back up. Sometimes it exceeds the force that cracked it.
Strain hardening, like steel. Then it comes down, it goes up, so you get a saw tooth. And then a very gradual, slow failure versus catastrophic.
Seth: Got it. It’s not truly concrete. What's in the composite?
Bill Kulish: The composite has a lot of [00:08:00] similarities with concrete. And everybody in the industry calls it concrete.
Nobody wants a composite driveway. So we like to push everything into big categories, which makes sense to me what we have in again, and I'll speak to steel which is a true certified vetted tested. What we have is a very high binder content, um, ironically. Because many of those binders are post industrial waste.
We actually have something that has a lower carbon footprint overall. When you factor in the life cycle costs you, you do, you encapsulate something, a bridge, the deck is worn out, the salt's got in, the steel's starting to get attacked. You clean it up and you put down a, let's just say a two-inch layer of UHPC, you're now fossilizing that bridge.
Because there's no big aggregates, there's extremely little air. Because there's... So [00:09:00] much binder, not all of which is cement. There's so much binder in there that it's sticking to everything. And you put all that together and the direct compare the answer to your question is, yes, there's some unicorn dust, which I'm not certainly going to go into the exact recipe, but for the most part, it's over 40 percent binder, 55 percent of the right aggregate. Very little water average water cement ratio is 18. I say average, because when you do an overlay, it might be 16 much less water. Which means. What is what you get. There is no creme. There's no cream. You do not trial UHPC. It's self-leveling, self-consolidating.
It's a composite, but for this podcast, we can certainly call it ultra-high-performance concrete. Okay.
Seth: Yeah. To explain what it looks like is I've seen your videos that you post on LinkedIn. It's I think before we, [00:10:00] we try to explain this, but I don't want to call like, it comes out almost if you were squeezing a toothpaste tube and watching it come out, something like that or, out of a caulk gun, the caulk coming out of that, it just, it has a whole different look to it than concrete.
And then when I, the one video you stuck your hand in it and moved it around and it just stayed together when you're moving around, didn't separate. So it was like almost like taffy was getting pulled is what it looked like to me.
Bill Kulish: That's a Great definition. And I enjoy speaking to people like you, because you have construction knowledge and background when I make you smile or take questions to what you're watching, I've achieved a big part of my goal from the beginning of the creation of this material.
There's some really cool words to use that are just. Thank you. Statements of science, non-Newtonian fluid, thixotropic properties. If you take enough starch and you put it into [00:11:00] water, we've all seen videos where you can run over it. if You stop, you sink. So this is a solid and a liquid at the same time.
It comes out to shoot as long as the material is moving. Whether it be from discharging, mixing slapping, flowing it's a liquid. Once it stops moving, it's the closest thing to a solid you can imagine. If you took your fist and punched it as hard as you could, you probably, you would hurt your hand.
But if you put your fist and you just slowly let it go, it would sink in like quicksand. That's a big part of the advantages of it. It will it's more dense than water, so it'll displace water. We were doing an all aboard Brightline project in Florida, and it had poured massively. All the joints that we were going to be connecting were full of water.
We started pouring on the low side. Nobody was allowed to touch it. And it just displaced all the water. And by, by the [00:12:00] time we got to the high side, clear water was coming out and we had UHPC throughout the joint.
Seth: Yeah, I've done that with regular concrete, but I won't tell you what job that was. It was a long time ago,
And we got caught in a downpour and it filled up a beam. And yeah. So we pushed the water out the concrete. Yeah. No, that's cool. So you hit on it, the type of projects this, your, this UHPC is on, it's normally, I see it, see the videos of bridge projects, and you're either repairing, it looks like you're repairing a section of it, or like you said, an overlay, is, is that normally where you apply your product?
Bill Kulish: As we speak today, yes, that's the majority of what it's used for when I hopefully come back and do another podcast in a couple of months, there'll be a whole bunch of other things that I can then describe. [00:13:00] I can tell you that all good UHPC is fantastic for preservation, restoration, repair, um, impact resistance weather proofing, and more.
You're not going to see, at least in the United States, you're not going to see too many bridges or highways made completely out of UHPC. There's an overengineering aspect to everything, Seth. And, as just because you can do something doesn't mean you do. It's got to be used at the right time.
It's a much more expensive material, but its life cycle costs are over 75 years. So if you're building a bridge today, and you're going to bury it under asphalt, it's sad to me. I'm not anti-asphalt, but asphalt has unintentional planned obsolescence. You're going to be back out there patching holes in a couple of years.
If you do a UHPC overlay, [00:14:00] and you don't put asphalt on it, the life cycle cost can go over 75 years. It's impervious. Salt, it doesn't recognize chlorides. If it's waterproof, and salt and water can't get in, there's nothing to freeze. And it's going to preserve and encapsulate or fossilize any existing chloride damage to the rebar.
So as long as that rebar is still mostly intact you're wrapping it with a material that just is going to put a membrane on it. That's going to stop it from ever being exposed to oxygen and water slash rust. Yeah,
Seth: yeah, it'd be nice if we didn't have to deal with those guys every summer repairing all those asphalt roads right on the highway and on the bridges.
Bill Kulish: Yeah, God, think of the, again, green. Reducing the carbon footprint. I get it. I'm with it 100%. Making Portland cement requires a lot of fossil fuels. I [00:15:00] was watching a documentary the other day on the water cost. The water footprint. And for the average bowl of curry, it was 2, 000 pounds of water.
And I'm like, what the, how's that possible? And they broke the thing down, I recorded it, I watched it over and over again. It had potatoes in it. It had different and all of those things require such an incredible amount of water. How we look at the actual real footprint. Also should be looking at the life cycle cost.
If it takes. I don't have this number calculated today, but if it takes 20 percent more, because I mentioned the binder ratio is higher, to make a UHPC, if it takes 20 percent more Portland cement but it lasts 50 times, 100 times longer, it's almost a net return on your investment. Yes, you put in a material that may have a higher carbon footprint, [00:16:00] but at year 30, you're not ripping it out and replacing it.
Asphalt, petroleum-based product, gets hot in the summer. It's wearing tires down faster; air conditioners have to be turned on more. There's just so many variables when you truly look at life cycle costs. And again, I'm not denying that UHPC has a bigger input or effect. But I will. Definitely respectfully stand toe to toe with anybody that says, Oh, my God, it's real bad.
You can use 40 to 50 percent less of it. So you got a material that has less carbon footprint, bringing trucks to deliver it, bringing trucks to remove stuff, getting rid of more earth than you need to. And you can remove 40 percent less earth, putting down 2 inches on a bridge that's going to most likely last over 75 years.
It really starts to make sense. And at year 30, 2530, higher carbon [00:17:00] footprint from day one has broken even with the recycling cost. Look at repairing a bridge. You have to factor in inflation. Rebuilding that bridge in 30 years is not going to be what it costs today. So just some overview stuff.
Seth: I totally agree. We get, we're getting too wrapped up on, I think the CO, CO2 thing and not missing. We're missing what you're talking about to me. The thing that pops in my head is it, you could either put all your money down, like a deposit up front and make that investment now, or you can go with something cheaper that you pay month to month.
And then eventually you're going to have to pay. A whole replacement, 5 years down the road. That's the type of material that we're using out there right now. Because I don't know, we just like to spend money.
Bill Kulish: And job security,
Seth: we got to make sure those asphalt guys stay [00:18:00] busy.
Yeah, we're I think you got us caught up and good refresher on What UHPC is and where it's being used. Did you want to talk a little bit about what you've done lately that you messaged me on LinkedIn about the so you can clue me in. Cause I was sharing with you before the podcast, some of your stuff it was over my head.
So you said you did the first UHPC overlay that did not require profiling. What is that?
Bill Kulish: Okay, so in Oregon we did the first UHPC overlay in Oregon. An ideal state, every state is, every part of the globe is, whether it's hot, cold. Freeze thaw, I mean we're talking about salts, chlorides, freeze thaw.
Really good place for UHPC to shine above the way it shines even in Florida. But that's salt, right? There's oceans around it. So there's very few places where it doesn't have advantages. In Oregon, it had more of an advantage. [00:19:00] So traditionally with overlays, you removed a decay. Think of the dentist.
You get a cavity, you go in, they don't say, rip it out, put in a new tooth. They get rid of the decay if the tooth has enough structure and then they put something over it or inside of it to keep it alive for another period of time. Overlays are exactly that. So if you come in, you remove the decay, generally they hydro demo.
They might shotblast, but they hydro demo to get rid of old stuff. Most often it doesn't go all the way down to the bar, but every now and then, and there was in Oregon, they got to a point where the decay was down and under some of the bar was still intact, but it was a pool that was holding salt and water.
In a couple of years, it would have required replacing the bar. In this case, it did not. And they take off about two inches, two and a half inches average. And then you come in and you place the material. And I mentioned the [00:20:00] word thixotropic. When you give Steelike or UHPC energy, it wakes up again.
Think of it as cold lava. It's liquid steel, but cold lava, right? Lava is flowing. If it was hot lava, it flows and then it freezes and it becomes hard. There's nothing you can do. If you could keep it hot, it would keep flowing. In this case, the material is cold, relatively speaking. You place the material, I told you it's self-leveling, self-consolidating, but there's no flat bridge that I'm aware of that I've ever worked on, because it has to have some kind of an arc, a curve, a dome, something to allow the water to drain.
So this particular print bridge had about a 2 percent crown. It went up and it came back down on this left- and right-hand side. We were able to come in. Lower water cement ratio, as I mentioned earlier, for an overlay. The thickness of that is closer to your toothpaste analogy. Almost like a yogurt, the material was placed down [00:21:00] and then all of us, meaning all the suppliers we put a vibrating truss screed or a vibrating screeding machine. Right over the freshly placed material it vibrates, but it only vibrates the amount of time the Mechanical device on the screen is touching the material what happens when you vibrate steel like it becomes liquid again but as soon as you go over it, it's no longer vibrating.
It becomes a solid again, or a semi plastic material. I. e., the whole bridge could be covered, even though it had a dome, a pitch, a crown, and the material didn't just flow off the sides. So it's a paradoxical thing. I'm telling you it's self-leveling, but I'm telling you that it'll self-level to a point, but then it'll stop self-leveling.
Normally... That whole process has to be done. Everything I mentioned, what we were able to do was, and it was because of this incredible [00:22:00] contracting company, the contractor was amazing. They embraced the differences of this material. Sometimes we get contractors saying, ah, I've been doing this 20 years.
You're not telling me anything. And the problem is it's a composite. So they're trying to treat it and project it as if it's concrete. And then they get right in the face, and they get pissed off and it's the materials defective. Doesn't happen often. And we've never failed a project. It's just, it can be really frustrating.
These guys embraced it, and we did a rehearsal. And we did a full-scale mockup, 20 feet long, 10 feet wide. After we'd spent two days doing that, we hit the actual live bridge. So it's four lanes with two shoulders. Trucks, traffic is going by on one side, and they close the other side. We come in with, in our case our modest, our method is a ready-mix truck because we can make seven yards of material, which won't impress you.
But seven yards is a lot to mix of UHPC in a ready mix [00:23:00] truck. You add the water after you add the powder. So if you try to put more than seven in, it would just start coming out the chute. That's the limitation of seven yards. We put, we serpentine the material down. They vibrated it with a vibrating truss screen.
Immediately sprayed it with wax to eliminate tarping. And to everybody's happiness, the state came back the next day and said, you don't have to profile this. The specification said it has to be within an eighth of an inch over every ten feet. So you couldn't have a half inch bump or anything over a ten-foot area.
And we kept within that eighth inch. So the only thing they really, and that's called profile, and I know most of you guys know. That's profile. That's where you're trying to shave off the high spots and get everything flat. They didn't have to grind the bridge. The environment was happy. Traffic was happy.
They were literally driving on this thing a day after it was placed, and it was cold. It wasn't like we had [00:24:00] chemicals and heat Seth. And all they did was put in ruffled potato chip grooves, eighth inch grooves running longitudinally, and that was just to avoid hydroplaning to give it a little more traction.
Okay.
Seth: Sounds awesome. One thing I heard you say, did you say they put wax over the top of it? Is that for a curing?
Bill Kulish: Yeah, curing compound wax is a beautiful thing. You don't want to be using solvent based blah, blah, blah. You just want to put a membrane over this material. There's very little water.
There's such a great surface area. That if you don't tarp it, normally the tradition is to tarp it. We simply have a design in our mix that allows it to avoid having a tarp. Now we may use it if it's 95 degrees sunny and windy. If it's no wind and within 40 to... 80 degrees. [00:25:00] We've been able to with contractors.
When I say we, the contractors, they're the guys doing the work. We're supplying the material. We're technically supporting them, guiding them and mixing the material once it comes out to shoot. It's on them. But again, we guide them based on what we've seen other contractors do. You put this stuff down.
Normally, you got to target the challenge with tarping. It is. You're hiding things. So you put the tarp down, if it's too soon, it can sink into the concrete. I have pictures of where they pull a tarp off the next day and it's just wrinkled and crinkled and there's, then they go, and they have the profile.
They profile, but it was so it dipped down so much, there's low spots that they cannot even put grooves in. So we simply with the right contractor using the method that we've reproduced a couple of times. We can eliminate all of that. You put the material down, you vibrate it, you spray it with a curing compound, and you're done.
[00:26:00] What is what you get.
Seth: Yeah, so that aspect of the curing or, do you need, is it the same as Since it was cold weather, do you need to blanket it at all or like regular concrete?
Bill Kulish: Yes, sir. At the everything with you might mind specifically heat. It loves cold when you're mixing and placing it.
It loves heat after you placed it. We did a girder for a federal organization. They steamed it at 130 degrees Fahrenheit, and in 7 hours, it was 14,000 PSI, which means if you're a precaster, you could put my material into a form, 7 hours later, demold it, do another one. You could do 3 a day if you wanted to.
That was because it had extra heat. If there's not heat... Obviously, the exothermic reaction when it's cooking, when it's creating crystallizing, if it loses [00:27:00] more heat than a generate set, you're you'll get there, but it just takes such a long time. We wanted to trap any heat we had because it was like 5560 degrees.
At the end of the day, it was a sunny day, so we let everything get as warm as it could with the sun. It was going to drop to 40 degrees. Then they put a blanket over it, not a powered blanket, but just an insulating blanket, and that trapped enough of its generated heat to allow it to accelerate to where they could be driving on it the next day.
Seth: Yeah, that's awesome. Yeah, because I read somewhere, I, again, I haven't done bridges in my career, but I read the one issue they have is when they need to repair a bridge or a road or whatever. like you said, you clean out the damage parts and you chip out the old concrete.
If you're not using UHPC, you're using regular concrete. [00:28:00] And my understanding is if there's a difference between the strength of the old concrete and the new concrete, that could be problematic. It can actually cause. I guess cracking and all kinds of stuff that you don't want to happen on the repair.
So it sounds like UHPC you're doing the same thing, but you're not having any concerns about the difference between the existing concrete and the UHPC. It's a, just a whole different type of material.
Bill Kulish: You nailed it. No, you're not only following, and I wish I could bring you to some pre-meetings with contractors.
You just nailed what it's about. Seth one is the thickness and mass. If you're using regular concrete, overlaying could be 5, inches. Number 1. Number 2, the bonding characteristics of are outrageous. The particles are so small. Some of them are sub-micron. Nano, and they're going into things that you and I don't even see little [00:29:00] scratches and nooks and crannies.
The other thing is the expansion contraction coefficient. And so we have bond expansion contraction capability. And then we have that tensile strength when I mentioned tensile as one of the biggies, it's much more than just being able to bend it that tensile. And I can't speak too much to it today.
Hopefully, I will the next time we speak, but tensile has so much. I'll just use the word impact resistance. It has so much. So many benefits to connecting to existing materials, whether it be steel, plastic would we've done. I've experimented with asphalt roofs, concrete, whether it's old, new. 5K, 3K, KSI, the stuff bonds amazingly because of its tensile capabilities and because of those fibers, that fiber matrix, it gives, one way to look at it is [00:30:00] almost like a hardwood floor in your house, that thing is living, it's moving, it's breathing, you put a new hardwood floor and you don't come in and butt it to the wall, you let it acclimate.
Now, that's for moisture offsetting, but concrete bridge is the same, but by putting on this material that has these tensile abilities to adapt and adjust, it doesn't shrink that much, relatively speaking. It shrinks, but not that much. Then it has the bond that it has. It's just it's a nice marriage.
Yeah. A really nice marriage to just about every material.
Seth: Yeah, I wonder if this is a good segue to the shotcrete. Do you want to talk about that? Sure. Oh so when you said that I was, and now that I'm looking at your message and connecting the two, so you could tell me what you're doing with shotcrete, but the first thing I thought of was you're shooting this stuff up against different material, right?
Or something like that.
Bill Kulish: Yes, sir. Yes, I will, [00:31:00] you may have saw on one of my posts, but that is correct. We did a shelter in Chattanooga, Tennessee. We've done a design beam by Cherie, a great professor who is semi leading along with a couple of other handful of professors and Ben Graybill at the FHWA and Zach Haber down in Florida.
Rafik, there's just so many people that are constantly proposing. academic ways to prove these things. We pick up, thanks to them, and we turn it into a physical representation. Case in point, we're in Chattanooga. They wanted a shelter. That was basically tornado hurricane weatherproof but could be erected quickly and would provide a quality of life for the people that would be in it.
So they, they basically took a rib, [00:32:00] uh, 3D printed, like a big 3D printed matrix, then they filled it full of polyfoam, then they shaved it off. So you basically have this four-inch wall with an incredible R rating. And they put it on a platform. Floor. Then we came in and shot about an inch of material over the whole thing.
And it's just, its a's so logical b it was bolted to the ground. It's just a beautiful piece. And that was done with shock treating. Why wouldn't you spackle it? Because it's a non-Newtonian fluid. Because it has isotropic properties. You could do it, but if you've ever played around with decorative concrete and you're trying to, or spackle and you're trying to trowel it up.
You try it up, 50 percent falls down, you try it up, 50 percent falls down, eventually it sticks, but it, every time it's falling and stuff, it's losing some of its water and characteristics. When you're spraying UHPC, nothing could be better. It's atomizing. [00:33:00] The water in the air. So it goes from a liquid to a gas back to a liquid over a 12 inch period.
So you're pumping the material in order to shock treat, you got to be able to pump and then it's at the nozzle and it's being pumped and pushed like a heart and then you have to inject air to atomize it so that it sprays. When you see spraying Very little it has to do with the pump. It all has to do with the air injection.
The pump has to keep up with supplying the material that then gets sprayed or turned atomized by the air. Then it hits the wall. What they're finding out is the characteristics only improve when you shock treat UHPC. The challenge of it, and why it took three and a half years and a lot of R& D funding the challenge was the metal fibers and the thickness and density of this material.
If you just go and you just rent a concrete pump, the ones that go 30 stories or the ones, cute little things that [00:34:00] make a wheelbarrows worth and they pump and you try to pump, you have a lot of internal parts, you have ledges, you have things touching the concrete internally, and I have these God awful, although they work hypodermic needles.
That are 300,000 PSI tensile strength. They don't bend is my point. Now you're trying to pump that thing through with a very low water cement ratio. First thing you're going to get is friction, which means you're going to get heat. I mentioned earlier that UHPC loves heat once it's placed. So you can get into a situation where it clogs, it just, it only works for a while.
And then when you're all done, it could take six, seven, eight hours to clean it. Because you don't want UHPC sitting in there for a half a day. It's over. You're going to throw away your thing. So we basically paid homage to an existing technology, a squeeze pump. But we had to modify the heck out of it to make it not fail.
The first one we bought off the shelf clogged up in about five minutes. 4 [00:35:00] years later, it works. We've run it all day long. We did an entire, we did bridge joints for pumping in Illinois, and we did the shock treating, the spraying at Iowa State University, and we did the shelter down in Chattanooga, Tennessee.
No problems. Everything went well. So we like spraying when it makes sense to do it, just because you can, I have guys now, contractors say we want to spray. I'm like, why? Because we want to spray and it's you got to have a reason to do it.
Seth: So are you thinking the spray is going to be for structural repairs, like vertical applications or what are you thinking with it?
Bill Kulish: I'm thinking hardening. Whether it be nuclear power plants, whether it be the spark plugs on electric plants, um, hardening, I'm thinking. Protecting, encapsulating, restoring. You got a bridge [00:36:00] and it's just rusting. The majority of that metal is still intact. 60, 70, 80 percent of it is still fine. You're not going to rip their girder out and redo it.
You could spray layers of this material, sandblast it, spray layers of this material, and just like laminates are with wood. Multiple layers are stronger than one thick coat, and you got yourself an encapsulated, fossilized, hardened, strengthened steel girder. You could spray buildings with it. You could spray...
Anything your imagination can think of as far as spraying, and let your mind, everybody on the podcast, just think of something that could realize an advantage by having a tensile, flexural, extremely high compressive strength material with all the characteristics Seth and I have been talking about.
It could be a balloon. We took some composite bar [00:37:00] as a proof of concept. We bent it, stuck it in the ground. Basically made what looked like a skeleton to an igloo. We went to Home Depot and stretched a bed sheet over it. We sprayed it. We sprayed three or four lifts about a quarter inch thick.
Two hours later, we could stand on it. The next day, you couldn't break it with a hammer. So let your imagination run wild with preservation, restoration, and hardening. And that's what you can do with it.
Seth: Yeah, that sounds pretty cool. Huh? I think this is a good spot to end today. Do you think we, we captured everything you want to talk about today and then you're going to come back here in a few months and share the other stuff you're working on.
Bill Kulish: Yes, to that, that question. I don't think we, you, Seth, you and I could go for hours, but sound bites are the best. Yeah, we covered everything you and I agreed to try to cover today, but I'd welcome the privilege to come back and expand on some of the things I wasn't able to disclose today.
Seth: Yeah, yeah, no, [00:38:00] that shotcrete part.
I think your timing is fantastic because I think we're going into a period of restoration and renovation and repair. If folks want to reach out to you, Bill, what's the best way to reach out to you?
Bill Kulish: Bill@steelike.com or just steelike.com. S T E E L, the word steel, I K E, one word, one L, and that's the easiest way to get me, or reach out to Seth.
Seth: Thank you, Bill. I appreciate that. Yeah, any, anybody that's on the podcast, if you're having a hard time getting a hold of them get a hold of me. I'll chase them down for you. All right, Bill, thanks for doing this again, and folks, until next time, keep it concrete.
Bill Kulish: Excellent.
Thank you, Seth.
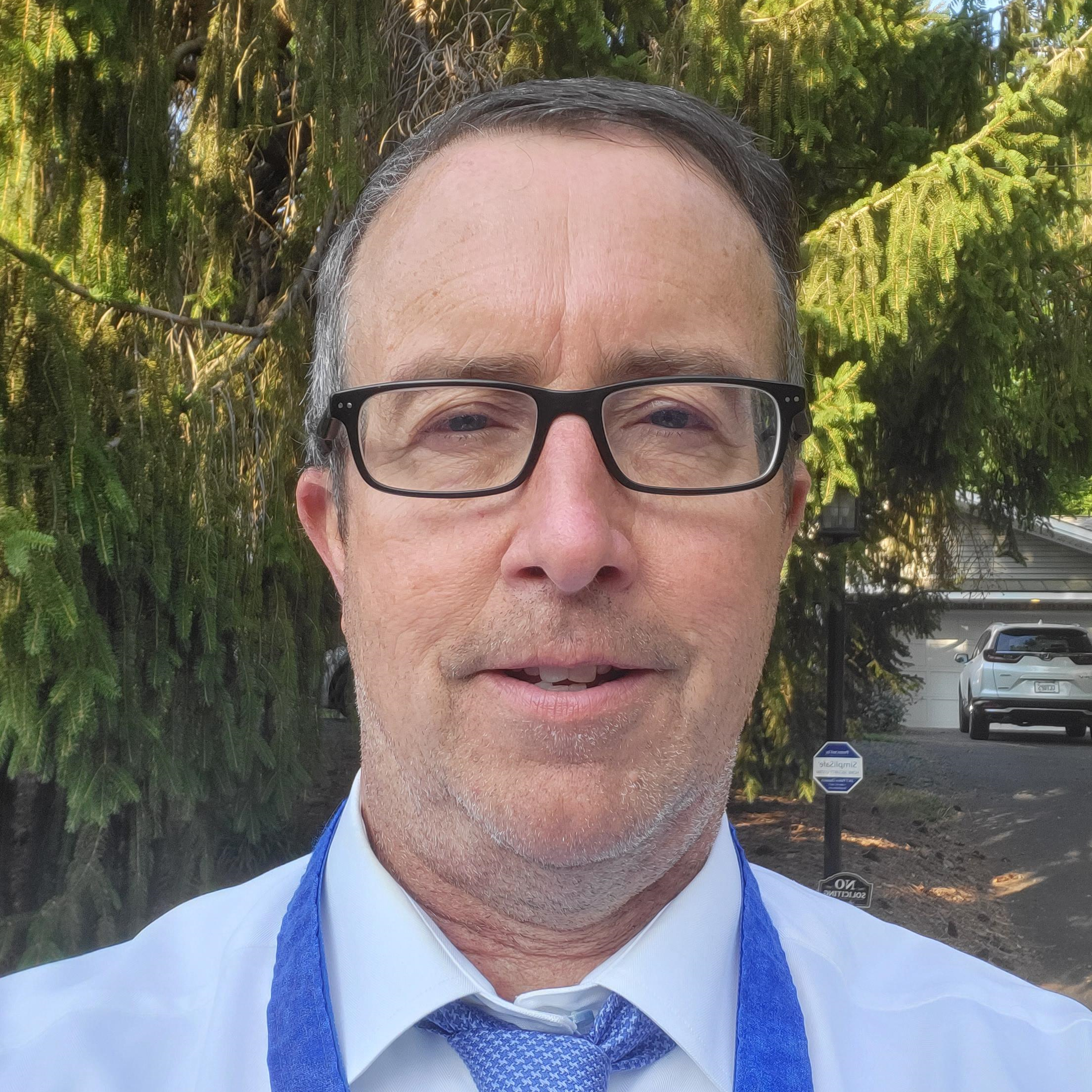
Bill Kulish
Founder/President and Chief Technology Officer
Bill Kulish is the Founder, President, and Chief Technology Officer of Steelike, Inc., a company at the forefront of advancing construction materials. His significant contributions lie in the creation of Steelike Ultra-High Performance Concrete (UHPC), a material that has garnered attention for its transformative potential in the construction sector.
Bill's expertise in UHPC has earned him recognition and invitations from prominent entities such as the United States Federal Highway Administration, Florida Department of Transportation, Pennsylvania Department of Transportation, Washington D.C. Department of Transportation, American Concrete Institute (ACI), and American Railway Engineering and Maintenance-of-Way Association (AREMA). He is a member of the Organizing Committee and Scientific Subcommittee of the International Interactive Symposium on UHPC, a member of AREMA Technical Committee 8 (Concrete Structures & Foundation), a member of the ACI Committees 134-00(Concrete Constructability), 230-SC (Steering Committee), 230-00 (UHPC), 230C (Structural Design on UHPC), 239-0D (Materials & Methods of Construction on UHPC), 239-0E (Education Outreach), 239-0F (UHPC Sustainability), and 329-00 (Performance Criteria for Ready Mixed Concrete)