EP #119: Is More Limestone the Key to Stronger, Cheaper Concrete?
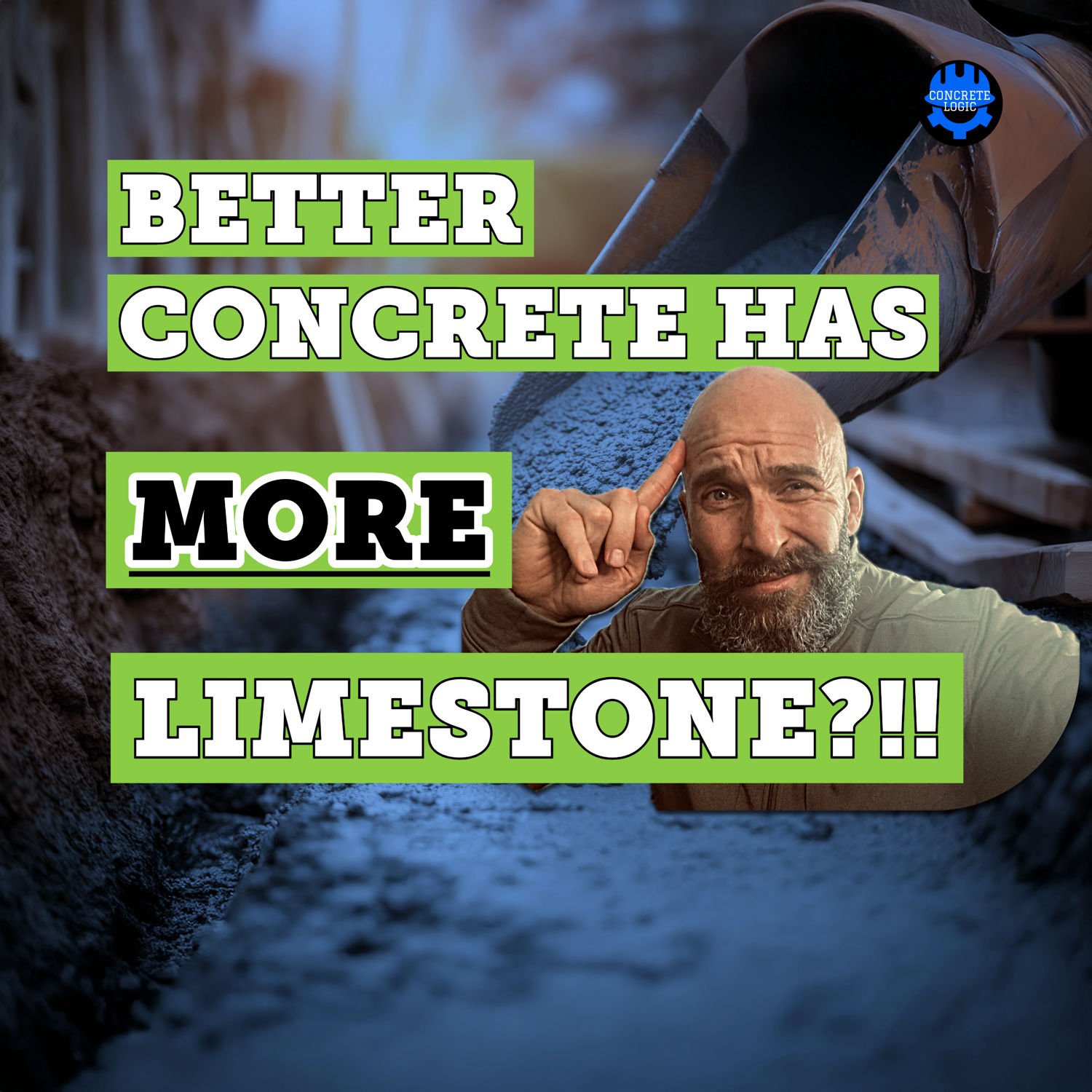
What if you were told there’s better concrete out there with more limestone than what’s used in Type IL cement mixes? Sounds crazy, right?
But that’s exactly what we’re exploring today with John Guynn and John Kline. In this episode, we explore ACI 211-7R and its potential to reduce cement content without sacrificing performance. Learn how adjusting particle size distribution, using admixtures, and understanding the water-cement ratio can improve workability and strength. Plus, get insights on the challenges and benefits of low carbon concrete, real-world applications, and the regulatory hurdles that must be overcome to make these innovations standard in construction. Don’t miss it!
What’s Inside:
- Limestone reduces cement content in concrete mixes.
- ACI 211-7R provides guidelines for using mineral fillers.
- Particle size distribution and admixtures optimize performance.
- Real-world applications demonstrate the benefits of reduced cement mixes.
- Low carbon concrete excels in strength, workability, and durability.
- Regulatory challenges exist around water-cement ratios and limestone classification.
- Smarter material use can reduce costs and improve sustainability.
- Ongoing research is key to advancing concrete technology.
CHAPTERS:
00:00 Introduction to Concrete Innovations
02:56 Understanding ACI 211-7R and Its Implications
06:06 The Role of Limestone in Concrete Performance
08:56 Balancing Performance and Cost in Concrete Mixes
11:58 Water Demand and Its Impact on Concrete Quality
15:00 Particle Size Distribution and Its Importance
17:59 Admixtures and Their Role in Modern Concrete
21:06 Real-World Applications and Case Studies
23:54 Feedback from Finishers and Practical Considerations
29:27 Performance of Low Carbon Concrete
32:13 Regulatory Challenges and Water-Cement Ratio
35:02 Innovations in Cement and SCMs
38:47 Field Testing and Real-World Applications
46:04 Durability Testing and Future Prospects
LISTEN NOW – Every concrete contractor & engineer needs to hear this one!
Guest: John Guynn
Company: Roman Cement
Email: john.guynn@roman-cement.com
Website: www.roman-cement.com
Guest: John Kline
Website: https://www.linkedin.com/in/john-kline-18003010/
=============================
Take Your Knowledge Further – Join Concrete Logic Academy!
Gain exclusive access to expert video courses, live Q&A, and cutting-edge industry insights. Earn Professional Development Hours (PDHs) and elevate your expertise!
Learn More: https://www.concretelogicacademy.com
Support the Podcast – Be Part of the Concrete Revolution!
Donate: https://www.concretelogicpodcast.com
Become a producer & get recognized on our next episode!
=============================
Recommended Resources:
ACI 211-7R.20: Guide for Proportioning Concrete Mixtures with Ground Calcium Carbonate and Other Mineral Fillers: https://www.concrete.org/Portals/0/Files/PDF/Previews/211.7R-20_preview.pdf
Producer: Jodi Tandett
Music by: Mike Dunton
Instagram: @Mike_Dunton
Stay Connected & Watch More!
Host: Seth Tandett
Email: seth@concretelogicpodcast.com
LinkedIn: https://www.linkedin.com/in/seth-tandett/
YouTube Channel: https://www.youtube.com/@concretelogicpodcast
Podcast Website: https://www.concretelogicpodcast.com
LIKE, SUBSCRIBE & SHARE for more expert concrete insights!
Seth Tandett (00:00)
Welcome to another episode of the Concrete Logic Podcast. And today I have two Johns with me. So I have John Gwynn with Roman Cement and John Klein with Klein Consulting. Some of you that have been following the podcast for some time, you'll remember John Klein. He came on and talked about carbon capture eons ago. I think it was 50 or 51.
was the episode number. if you go on the website, you can search up John Klein, but he is my go-to when I want to know anything and everything about what's going on with carbon capture. He gives talks all over the world. And you said, are you going to Vienna, John? Yep. So he's going to be in Vienna. So if you're listening and by the time this
John Kline (00:41)
Going to be in in May, yep.
Seth Tandett (00:47)
comes out, this will be before John does his talk in Vienna. Please look him up. And John Gwynne is with us today. He's from Roman Cement. He's also a patent lawyer. And he has a chemistry background. And I noticed you went to school at UVA. I'm in Richmond. So I'm very familiar with UVA. So I think my.
John Michael Guynn (01:06)
Okay.
Seth Tandett (01:09)
Hokie listeners probably wouldn't appreciate that you're on the podcast, but that's okay. We can't make everybody happy. But today what we wanted to do is John, both Johns, actually listened to our episode on ACI 323, where you had Dr. Belkowitz and Rich Sazy on the podcast, and those two folks had very strong opinions on ACI 323.
And we're all in the industry, we're you know, we're going through this transition with type 1L cement and blended cements. And we're all learning as we go. And what we are wanting to do today is John, the Johns are going to help me understand how we can reduce cement content without sacrificing concrete performance.
John, John's Gwen, John G has done some work with Roman cement utilizing this and we want to, I guess, John, you're going to help me understand ACI 217R better. I've shared with you, I've read it a few times and it's my understanding. I guess we should start there is my
I guess, simple man view of ACI 211-7 is it's sharing how to proportion concrete mixes utilizing mineral fillers. And mineral fillers includes limestone. Is that a correct, I guess, simple summary of it?
John Michael Guynn (02:38)
Yeah, mean,
limestone is the main one that they talk about and they also talk about leftovers from aggregate making or the fracture of aggregate minerals. And so they don't specify what those are, they could be other things other than limestone is one aggregate and you have other aggregates that are.
you know, more on Solicious based and so it permits those. Mind tailings is an interesting thing because you might consider or to be an aggregate and so mind tailings might satisfy 211 but I'm not really sure. So that's something that'll remains to be seen. I actually did recently join the committee, ACI 211 7R committee and I'm gonna make some recommendations or at have a discussion with them about how I think we can strengthen the...
this standard to help people better implement what it seeks to implement, is the use of mineral fines to replace cement, but it still has some practical things that need, I think that need to be improved.
Seth Tandett (03:29)
Okay, and if folks are reading through ACI 211, if I look at the ground calcium carbonate, is that the limestone filler, is that correct?
John Michael Guynn (03:41)
Well they call it, yeah, so I guess that's the definition of limestones. It has to have a certain minimum amount of calcium carbonate. So if it does, it's calcium carbonate or it's limestone. I mean it kind of goes back and forth, but it treats them kind of as if they're the same thing.
Seth Tandett (03:54)
but the aggregate Miller mineral fillers are not because.
John Michael Guynn (03:58)
They don't, yeah, they may or not be. I mean, guess if the aggregate is a limestone aggregate, then they would be, but if it's a salacious aggregate, they could be some other mineral.
Seth Tandett (04:05)
Okay, so I guess could we just start with, because you're the one that pointed ACI 211 to me. So how do we balance performance?
when using these fillers, I guess. What's your thoughts on that?
John Michael Guynn (04:22)
Okay, well the way that we've done it, first of all, there's been a lot of talk about using nano limestone, which is very finely ground limestone. That's not something that we use or recommend. Also in type 1L cement, when they grind it, the limestone being softer typically than the clinker will also end up in the very fine portion of the blended cement. So.
whether you're using nano limestone or limestone in type 1L cement, what we use is not that type of limestone. It has a different particle size distribution. Ours is a coarser limestone. I use the word coarse loosely. I don't really mean that it's sand. It's not that coarse. But it does occupy a size gap that's
exists between the largest cement particles, are around 40 to 45 microns, and the smallest sand particles, which are about 150 microns. So there's this huge gap in size that it fits nicely in and it provides a lot of benefits. And also, coarser limestone is a lot less expensive than nano-limestone. Typically it's around 1 fourth to 1 fifth the price of cement. And so it has cost benefits.
I think one of things that people say is, well, you have to use a lot more of coarse limestone to get the same effect as ultra fine limestone. But I say, we don't have to, we get to. And the reason why I think that that's a positive is because what we're really trying to do is utilize it.
for its volume, that it produces a lot of volume and it also creates a particle packing effect in the cement paste itself and to some extent with the aggregate fraction. So it acts as a microagriate, a term that John Klein likes to use. I agree with that term. It kind of bridges the size and the gaps between cement and sand. And so it's this sort of in-between material, but we have to use more of it, which means we get to use more of it. And because of it,
It basically acts as if it's in the cement paste and so it adds a lot of volume to the cement paste even though it's not cement per se.
but it allows you to maintain performance both in terms of workability and if you proportion it right with the right amount of cement and pozzolanic material and limestone and water, then you get really good strength and workability results. So we've tested this for about a decade and we've done some commercial projects and it's worked out very well. It's a question of implementation.
Seth Tandett (06:41)
Yeah, yeah, yeah.
No, that's great. I should have said the title of this ACI 211-7R is Guide for Proportioning Concrete Mixtures with Ground Calcium Carbonate and Other Mineral Fillers. And it seemed like it was you were hitting on the size of the ground up limestone. So it was saying it can't be too big, it can't be too small.
it's got to be a certain size and I don't know if I could pull out for me. There was a bunch of examples of proportioning calculations and things and that kind of lost me through there. But is there a size that you found that it points to that gives us a range or is this based on individual, I guess, individual mixes?
John Michael Guynn (07:15)
Yeah.
Seth Tandett (07:27)
It depends on, I guess the size depends on what you're doing for your individual mix.
John Michael Guynn (07:33)
Well, think that we started using limestone powder long before I even read ACI 211 7R.
And so we were using limestone that was actually practically available here in Utah. We still have coal mining, and there's two companies that create what's called mine rock dust. And they grind it to about 200 mesh, which is about 75 microns average particle size. So that actually is a great position because an average particle size of 75 microns is
is right in between the cement, which probably has an average particle size of 20 microns, and sand, which has a minimum particle size of 150, so it fits nicely. I think the ACI-211 might have some size restrictions. We might be slightly outside of those, at least part of it, but...
you know, there's a range of particles. They go down certainly below, down as low as 10 or five microns, they go up as large as say 100 to 110 microns. So they are, as any particles material, has a range of particles. I think that the issue that I see in 2.11.7r, even though it says guide to proportioning, guide for proportioning, it doesn't really say,
anything about what proportion of cement should be replaced with what proportion of calcium carbonate or limestone. And I think that's the blind spot in this thing. And I've given some presentations at a conference called the Anna Maria Workshop. what I tend to say is this. And this works with various limestones of various sizes. But depending on the mix design and depending on the actual particle size distribution of the limestone,
Seth Tandett (08:42)
Yeah.
John Michael Guynn (09:00)
when I design this, in my mind, think of part of it as being cement and part of it as being sort of an aggregate. And so the part that, counts as cement is going to replace the cement one-to-one. The part that's sort of the aggregate is in addition to the cement. And so we never replace cement one-to-one.
by weight of limestone powder because you need to have a greater amount of limestone powder than the cement you replace. So if we replace, if we reduce cement by say 100 pounds per cubic yard, we might add 150 to 180 pounds per cubic yard of limestone powder. And then we will.
typically adjust the water so we get the right flow and the right strength with the right amount of admixtures. And it's not a, if we reduce cement by 20%, we won't reduce the water by 20%, but it'll be something like five or 8%. None of that is really an ACI 211, but it's something that we have come across or noticed after years of testing that this is the way that you make it work.
Seth Tandett (10:00)
Yeah, John Klein, did you want to say something?
John Kline (10:02)
Yeah, I just wanted to back out a little bit because we're getting down into a lot of the details. Fundamentally,
Cement's got to flow. it flow, it's got to be fluid. For it to be fluid, you got to coat the surface of all the particles. The finer the particle, the more surface area it has, the higher the water demand. So it's a function of both the particle size and also the porosity of the particle. On the West Coast now, we're dealing with natural pozzolans, more porous, higher water demand. On the East Coast, we're starting to get into harvested fly ash, more surface area.
because of the way the the ashes as weathered I'd say so we have to add more water so
When the industry, I'm a powder guy, so I'm more on the cement side of things, when the industry went over to 1L, they had to grind the cement finer to get the same strength. And that's because, as John pointed out earlier, the limestone is softer material typically, it becomes a lot finer, the finer limestone becomes nucleation sites.
So this is not, we're not looking at a 1L type application where we're looking for nucleation sites. What we're doing is all of the Radimix guys know that if you have a very good particle packing distribution, a size distribution of your aggregate, you need less paste. We're just taking that, extending that down into a finer size range. That's why I like to say micro aggregate, because it is on the coarser side, the 75, 80, 100 micron.
that range, we can fill the gaps between the sand and the other aggregate. We don't need as much paste, still get the same strength, and because we don't have the surface area, we don't need as much water. Now, that's the simplified version. John, as he says, has been working 10 years on this and has worked out exactly how to adjust the water for this change in particle size. I won't say it's
slam dunk, but what we're doing is filling gaps with the filler material. We're not trying to replicate. In fact, we're trying to go the opposite way of the 1L. Let's get the limestone in without the overgrinding, without the additional need for water.
John Michael Guynn (12:10)
Okay, can I give a little background of how we got to where are, Seth?
Seth Tandett (12:15)
Yeah,
are you going to hit on the... So what I'm hearing is the water demand has changed. Is it increased? Is that what I'm hearing? Because when people hear, I'm having to add more water to these blended cements, the first thing they start thinking of is loss of strength, shrinkage, you know...
it's more prone to crack these type of things. I think, we, are you going to address that in what you want to show us or.
John Kline (12:43)
Let me just jump in. If we're looking at cementitious, because we're taking out cementitious and putting in the coarser limestone, if you're looking at cementitious, the water demand goes up. If you're looking at the total concrete, the water demand goes down.
John Michael Guynn (12:58)
Okay, I want to give you some background, Seth, as to how we got to where we are. Right now, I'm working with how to implement things at the batch plant. But early on, our technology looked mostly at the particle size distribution of the various components within the cement blend, if you're looking at a blended cement. Can I talk about that for just a brief moment? So.
Seth Tandett (12:59)
Okay.
Yes.
John Michael Guynn (13:18)
know, cement has a distribution of particles between sub-micron and say up to 45 microns. And the really fine cement particles will hydrate very quickly. The very coarse particles hydrate very slowly. And typically the largest cement particles will never fully hydrate. And you can imagine that if you have cement that never fully hydrates, then you're never going to...
extract the full strength potential of your cement. It's if you have gasoline in your car that you can't use. There's 20 or 30 percent of the gasoline that's in your tank that you can't use. Then it's just sort of added weight, which isn't doing anything. Cement's an expensive component and it has all the embodied CO2, most embodied CO2 and concrete. our original goal was to try to say what is the ideal particle sizes of various materials you would put into a blended cement if you
could select that. What we decided was early on, this was theoretical and we proved it out later and there's other articles that prove this, but if you were to reduce the maximum cement size down to something like say 25 microns, then you have a much greater chance of being able to fully hydrate the cement. And then we look at the ultra-fine end and you say, well, at some point the finer it gets, it's sort of counterproductive because, you know, maybe cement particles are as low
as three or five microns, produce all the cement, all the strength you're going to get from submicron particles, but the submicron particles just have increased water demand.
Our ideal cement early on would be a narrow particle size distribution cement, say between, you know, five and 25 or 30 microns. And then if you had to identify like a pozzolan or slag or something, how would you maximize its contribution to strength? Well, you'd want it to be as fine as possible. So in the ultra fine area, you would want to have a pozzolan, whether it's fly ash, natural pozzolan or slag or a blend thereof in the really ultra fine area.
Because that's where you get the most strength from your pozzolan the finer it is the more it's going to react and you might even get more strength out of The pozzolan than the cement you replace. We know that Solica fume for instance produces Tremendously more strength than cement pound for pound because of the way it reacts and it fills in the really Micro pores and creates a very tight matrix. So we thought about that, but then you're left with a very fine cement and a very ultra fine pozzolanic material which
that's still going to have a very, very high water demand. So then we said, then you need to backfill the coarse end with something that doesn't even have to react. It could be non-reactive. It could be a very coarse fly ash. It could be a coarse limestone or other mineral filler. And you could push that up. And in fact, 45 microns is not, that's just an artificial upper limit that's based on how they grind cement. But we thought we could go up to 100 microns, 150 microns. So we envisioned
distribution of particles where you had an ultra fine area with very highly reactive pozzolans but reactivity is very
subjective because it's not reactive like in the cement. They don't dissolve immediately and create this water demand issue in the same way. So they are there, but they don't negatively impact initial flow like the ultrafine cement particles. So you get a water demand decrease by having a very ultrafine fly ash. I did de-dusted fly ash.
excuse me, classified fly ash that was like five microns and smaller and it had really low water demand and produced incredibly high strength. So that's just an example.
So if you had a narrow particle size distribution cement, like I said, three to 30 microns, you had an ultra fine fly ash from say, sub micron to five microns or 10 microns, and a limestone powder from say 20 to 120 microns, we created tremendously strong cement and mortar with very low cement content. And that's the ideal. And we have patents that go way back that talk about that ideal, both in terms of particle size selection for maximizing performance of the various
components and also particle packing like John Klein said the more particle packing you have within your cement blend the less water needs to be available to you know fill the interstitial voids between the cement particles and so you get that also lowers water demand so you could you get all these benefits when you you select cement that size. John do you want to add anything there?
John Kline (17:31)
I would say it's not just less water, it's also less paste. So you need less cementitious material, less water. It's basically reversing the 1L situation. Take the limestone out of the fines, add it on the coarse side of the equation. Take advantage of the particle packing versus the nucleation and you'll get the same strength with less cement.
John Michael Guynn (17:52)
Yeah,
and as far as nucleation goes, the coarse particles still have a surface. They're not as small as the nano limestone, but they do have a surface, and it is a place where cement crystals will grow, and so they might not nucleate the same way as very fine.
Limestone in 1L cement, but they still I believe do it because we do notice that when we have limestone If you just replace cement with a lot of fly ash it retards setting and you get very slow strength development But you put in a lot of this coarse limestone and you get it It sets in the same period of time and it also develops very high early one or three day strength Sometimes even even higher so that limestone powder is doing something other than just acting as a passive filler so I believe that it is acting as a
nucleation site and because we have a lot in there there could be some you know release of calcium carbonates to form calcium carbo illuminates which they think occurs to some extent with the with the nanolimestone.
Seth Tandett (18:48)
Huh.
Is there, other than adjusting the water, is there anything else that you're adding into the mix to, I don't know, supplement the, I guess the use of water? is, is there something that we don't typically put in concrete? You're putting in the concrete to make it work with the additional filler that's replacing the cement?
John Michael Guynn (19:11)
Now we use the same traditional, the same admixtures, low, medium, higher range water reducers to get the right flow. There are products that are coming out that are specifically made for mineral fillers because the way in which...
you know, super plasticizers work is they deflocculate the cement particles because they tend to be charged and flocculate together. So you deflocculate, but when you have limestone particles, they're affecting water demand in a different way. And there's, and there are some products out there. don't want to list any names of, of manufacturers, but we have one that we've used and it creates a tremendously flowable material better than a super plasticizer because it doesn't create a sticky mix. It tends to reduce the
the
stickiness and create really good flow. So, and that is an admixture which is being introduced specifically for, I don't know if it's for 1L cement or for the proposed increased use of mineral fillers because of ACI 211 or maybe because of SEMs under ASTM 1697, but these have only been recently introduced and they seem to be a very powerful admixture that helps our material in particular.
John Kline (20:19)
And we need to keep in mind that from a cementitious basis, we're reducing cement, replacing it with the limestone filler or the whatever, the mineral filler. So from a cementitious standpoint, water demands going up. From a concrete standpoint, water demands going down. We're putting in less water. We're putting in less cement.
John Michael Guynn (20:35)
Correct.
John Kline (20:39)
So the amount of water is not reducing as much as the amount of cement. So when you look at those two in relationship, you see it going up a little bit. But if you look at the total concrete mix, we're putting in less cement, we're putting in the filler, on the total mix, it's less water.
John Michael Guynn (20:55)
Yeah.
And Seth, mean...
We typically do use a little bit more admixture than a mix that we are replacing because even though the water to cement ratio typically goes up in our mixes, the overall water to powder ratio goes down. And those are both mentioned in ACA 217R, the interplay between water to cementitious binder ratio and the water to powder ratio, limestone being powder but not cement, but it still does affect the rheology and the strength and it has to be taken into consideration.
delicate
balance, but because of the, we probably save eight to $10 a yard in cement reduction.
but then we use a little bit more admixture. So the net result is still about a five to seven dollar per cubic yard cost reduction, but we do use more admixture. some, some people might think, well, if you use more admixtures, it's going to make the concrete cost more, but it still costs less because of the cement reduction. So rather than, I don't view using more admixtures as a weakness. I view the strength, the cost reduction in the environmental benefits of
reducing cement as opening the door to more intelligent use of the admixtures that we already have. And so through the correct use of admixtures, we can get a mix that has really good properties of flow and strength and durability. We want to mention that as well.
Seth Tandett (22:13)
Yeah,
yeah. Now you're talking my language. We're reducing the cost of concrete and that's that was the whole origin of concrete use in the United States is because it was cheap and it was easy to use. Just wanted to touch on finishers will say that the more chemical you put in to the concrete the harder it is to finish. Have you with your work have you
had any kind of feedback from finishers? I mean, yeah.
John Michael Guynn (22:39)
Yes. Yes. Well, let
me see if I can share a slide here. I can do this again. OK, let's see.
Seth Tandett (22:46)
Okay, that'd be good.
John Kline (22:52)
I
would say at seven dollars a yard, do you think the finisher's opinion will matter? I'm not out there. I don't want to sound that way.
John Michael Guynn (22:58)
I it.
But I
want to show this. OK, so let's look at this. If you can see this, we did a project with the city of Salt Lake. It was 100 yard pour as part of an electric.
Seth Tandett (23:02)
depends. It depends who you ask.
John Michael Guynn (23:16)
bus station, electric charging station. And there are three slabs, ours is in the middle. So it takes the biggest brunt of where the buses sit. And then there's the outer ones, which are just the regular mixes. So the original mix, this is a Salt Lake City specified prescriptive mix. And you can see that it has 611 pounds of total cement and fly ash. That's a six and a half bag mix. It has a design strength of 4,000 PSI. is an errand train at 6.3%.
because you know we have a freeze-thaw issue here in Utah because it gets very cold and then if look at the Roman cement redesign mix, the cement and fly ash was
reduced to 495, the cement down to 391, that's a 20 % reduction in cement. The fly ash was reduced by a little bit and the water was also reduced by a bit from 32 gallons to 30.1, but that's not a 20 % reduction, that's about an 8 % reduction. And then we have 150 pounds per cubic yard of rock dust, which is just high calcium carbonate.
limestone powder. If you look at the admixtures, the standard mix only used an amount of low range water reducer. We used low range water reducer and a high range water reducer, so you would think that that would create a stickier mix. But it turns out that this is what
The general contractor who was overseeing this project said, and I highlighted these things in yellow, and it said, am delighted to report that the concrete has exceeded our expectations and is performing exceptionally well. As far as you talk about finishability, the second paragraph says, after conversing with the masons present that day, they confirmed that the low carbon concrete performed just as efficiency, just as efficiently as any 4,000 PSI mix while still being highly workable. And then the pump operator said,
that
there was a decrease in pressure required to move the mix. So it further highlighted its workability. That's actually kind of the exact opposite of what people are saying about low carbon concrete under ACI 323 that if you reduce cement, you're going to reduce the cement paste, you're going to have a very poorly workable mix, a very harsh mix. But it turns out that this particular mix was
less harsh or it was about the same as the standard mix even though we used a higher range water reducer it wasn't sticky stickier it finished well so that's not that's not been a problem and i think that with these new ags mixtures coming out that are specifically designed for for mineral fillers i think that we can get even better workability than what we got here because that was not available to us at the time but it is now
So workability is not something that we have had a problem with, but we do get tremendous strength. It does say in paragraph one that the average strength was 5450 PSI. One of the trucks came in at about 6400 PSI at 28 days, which was incredible. Another one came in lower and that was kind of...
the anomalies. We just took the average between the highest and lowest and came up to 5540 28 days and it was over 6000 at 56. So we got great strength, great workability and this saved about five to six dollars per cubic yard. We reduced the amount of cement by about 100 pounds per cubic yard.
Seth Tandett (26:39)
And when was this one?
John Michael Guynn (26:41)
This
was port in September of 2022. You know, we really expected this to launch us.
here in the Utah market, we've faced, we've talked to UDOT, they're very interested in using it. They have these standards, very strict, they follow a prescriptive mix, and so they're not sure what to make of the limestone powder. I point to ASTM 1797 that permits limestone in concrete. I point to ACA 211 7R, but they said, what about the water-cement ratio, and is the limestone aggregate, or is it cement, or neither? And so what do we do with it? So we're still trying to work
through those regulatory issues with them.
Seth Tandett (27:20)
So
the way we calculate water-cement ratio right now puts it out of the range of the U-dot spec.
John Michael Guynn (27:27)
Right,
so if I go back to this previous page here, let's see.
I don't really have a quick water-cement ratio calculation here,
It is higher. Let's say if the original mix had a water to cementitious binder ratio of .44, ours might be .50, which is quite a bit higher. And so, you know, nobody would really want to use a .50 mix because they would think it wouldn't have the strength. It'd be too watery. But it turns out that that's not the case with our mixes. you know, the water cement ratio is just a number. It doesn't mean anything really. It means something to people that like prescriptive mixes. But from a performance standpoint, it's
becoming irrelevant. So we want to try to see if we can, you know, satisfy the performance criteria and let them sort of loosen up the restrictions on water cement ratio. But I think there's other ways to get around that. We can meet the water cement ratio if we can get at least some of the limestone to be counted as part of the cement and I think there's some efforts to do that both in ACA 211 7R
which I'm on the committee. And also there's a new standard ASTM 1697, which is going to permit a blended SCM with pozzolan and limestone. And presumably the limestone in that case would be counted towards the cement, in which case we would not be penalized as we are now for the water cement ratio requirement.
Seth Tandett (28:50)
So in this example, are you more on the side of, or maybe I'm understanding this incorrectly, so just correct me if I'm wrong. Are you leaning towards the side of ACI 211 7R where that's a blend, it's a filler that's replacing cement? And then ASTM 1697 would be more of a blended SCM, which would be added at the
ready-mixed producer silo, right?
John Michael Guynn (29:22)
Yeah,
well, yeah, I mean, the limestone that we added was added at a silo at the ready mix plant. So it was definitely added just like the fly ash would be added at the batch plant. the fly ash, so the cement was in one silo, the fly ash was in the second silo, and the limestone was in the third silo. And that's been one of the impediments is installing new silos at a batch plant to utilize this third material, which we can purchase.
Seth Tandett (29:28)
Okay.
John Michael Guynn (29:49)
in large quantities and have it shipped to the plant. I see the proposed changes to ASTM 1697 that allow pozzolan and limestone to be blended to have a blended product which could then just be
Put into the typical fly ash or natural pozzol on silo so it wouldn't then require another silo But to answer your question all of these are always going to be added by the batch plant unless the cement company start to produce cement that has these This amount of coarse limestone, which I don't see them doing in the near future
Seth Tandett (30:24)
So was your the cement that used in this example, was it type 1L?
John Michael Guynn (30:28)
Yes, it was a type 1L. And in fact, when we met with the city engineers and even the concrete manufacturer, they expressed a lot of skepticism as to whether or not our limestone would actually work in the way we said it would. Because up until then, we had tested type 2-5 cement and they were just transitioning from type 2-5 to 1L in 2022. And they said, well, if they could add more limestone, I'm sure the cement companies would have already done it. And I said,
We're not using limestone in the same way and it's not the same particle size and we say that it behaves differently and it does something different and you'll see the results and the results confirmed what we said was this limestone is behaving differently even though it's limestone it is behaving quite differently because of the particle packing effect, the lower water demand effect because it has much lower surface area and the way that it's able to volumize.
the cement paste as a micro aggregate. So it still works. So if you think about it by using type 1L, they already reduced the clinker content of that cement by 10%. And then when we reduced the 1L by 20%, we reduced it by another 20%. Of course, it's not, if you do the math, it's not a 30 % reduction, it's a 28 % reduction in clinker factor, but nevertheless, basically triples what the 1L cement was able to accomplish.
And we got the same or better performance, I'd say better performance than the standard mix.
Seth Tandett (31:55)
Okay, so you're proposing just a whole different SEM is my understanding.
John Michael Guynn (32:02)
Yeah, I guess you could say it's an SCM microagrid. Here's just a photograph.
Seth Tandett (32:05)
Yeah. Have you tried
presenting it in that way? Is that how you presented the DOT?
John Michael Guynn (32:10)
Yeah, we presented the DOT as something that qualifies under ASTM and ACI standards, but it doesn't qualify as an SCM per se yet.
Like I said, it's defined in 211 as a mineral filler. It's not counted as an SCM or cement. So right now it's kind of in this no man's land of we're not sure what to call it. But right now it's not considered a cement. again, I think that performance is really where the rubber hits the road. Anyway, here's some photographs of when they were pumping it and finishing it and...
They loved it. You can see that there's a gentleman here finishing it and you can see that there's a slab, a pre-existing slab to the west of the slab that we poured. And then there's also another slab to the east of it. You can't see it in this picture, but when you go out to the bus station, you can see ours. It's slightly different tone of gray. And there's definitely some demarcations between
that are obvious to where our slab begins and theirs ends.
It's gone through three winters of freeze thaw. There's no damage whatsoever. There's no material. There's no missing material, no spalling, no surface cracks, no damage. It's performing very well. So that's a great field test. We've got quite a few other pores out there, not quite as big as this one. We've put concrete in trucks. So from the standpoint of performance, it's proven. It's just a question of getting it implemented. That's what we're working towards right now.
Seth Tandett (33:46)
No chalky dust on top.
John Michael Guynn (33:48)
No. Well actually because it's larger than the cement particles it doesn't really create that kind of chalkiness. No, we never had that issue.
Seth Tandett (33:55)
Yeah. Huh. It took me 38 minutes, but I finally figured out what you're doing.
John Michael Guynn (34:01)
Okay, well, that's better than
some people never understand what I'm doing. I met with a concrete company a few years ago. They gave me an opportunity to redesign their mixes. They're a national concrete company. I don't want to mention who they are. We were at their test facility.
and they ran some side-by-side tests and later on I was talking to their quality control person or R &D person and that person said, I have no idea what it is you're doing and I tried to explain it and they never really quite understood what I was doing and to me it seems really simple it's very straightforward but I guess if it was that simple then people would grasp it easier so I'm glad you got it in 38 minutes.
Seth Tandett (34:48)
Thank you. John, have you got a perspective from the cement folks? I mean, do they really care?
John Kline (35:00)
Well, we've had discussions with different cement companies and they basically say, we knew that or we understood that, but they're not using it. Now, anytime you reduce the amount of cement and concrete, you're kind of hurting their business. But this would be something John and I've talked about and we presented on it. This is something that would be.
Seth Tandett (35:16)
Uh-huh.
John Kline (35:22)
fairly easy for a cement company to do just to modify the particle size distribution in their cement particle by adding this stuff in at the cement plant. You know, it could be dust from the crusher operation. It could be something they're producing. just, it's all about particle size and water demand and balancing those two.
John Michael Guynn (35:33)
In fact.
Correct, yeah, John, this.
Yeah,
John talked about this and I think that there might be a company in South America doing something like that. What I would propose that a cement company could do would be, in my mind, they would create a one piece cement or the inner grind cement in Pozzolan and maybe they could grind it finer than usual because even though it's going to be finer, they can then backfill it, like John said, without intergrinding with the rock kiln feed, which is typically a lot coarser than the cement clinker's ground.
and it is around the 80 to 120 micron size as I did some research. And so it creates an ideal situation where they can do it, where they can blend it at the back end. The result would be a cement that, you know, again, it has more limestone powder than the cement it's replacing. So when used at a batch plant, they would have to use a little more of that blended cement than they would use currently and make some adjustments to the water and the admixtures. But that's the way in which a cement company could actually implement this technology.
Seth Tandett (36:40)
Yeah, I'd be more of a proponent of let's just stop messing with the cement. Let's all get used to type 1L and let the Ready Mix producer deal with the new SCM and let them experiment with the SCM. Because I think we keep fooling with the cement. We're just going to... I think we're confusing everyone. I think... Yeah.
John Michael Guynn (37:01)
Well, there's also some practical things, Seth, is that
depending on the strength in the mix design, you're not going to always want to have the same ratio of 1L cement with this blended Poslon or blended SEM, if you will. depending on the mix, might have different amounts of, different mixes right now have different amounts of fly ash or natural Poslon anyway, different ratios of cement and Poslon.
Seth Tandett (37:11)
Right.
John Michael Guynn (37:23)
we're going to want to be able to have the batch plants have maximum flexibility to be able to adjust the amounts of these materials. You get maximum adjustment if you put all three components in a different silo. But like I said, a compromise might be this blended SCM with pozzolan and limestone that would at least permit us to not have to use another silo. It would then fix the ratio of pozzolan and limestone, but
that's not as big of a deal as the ratio of this blended material compared to the cement. That's the ratio that we want to have maximum flexibility to change at the batch plant.
Seth Tandett (38:01)
Yeah.
John Kline (38:01)
I would agree with John. mean ideally mixing it at the batch plant gives you the most flexibility as a concrete producer. This job I can adjust this way, this job I can adjust that way. Unfortunately beyond the powder side of things if the cement guys can't get their CO2 down
the high cost of carbon capture could put some of these guys out of business, which isn't going to help anybody either. So there's kind of a trade-off there if they can get it down at the cement company. But from a flexibility and overall efficiency standpoint, I agree with John, it should be at the ready mix. The magic is understanding how the particle size impacts the water demand.
John Michael Guynn (38:46)
Well, one of the things...
John Kline (38:46)
and knowing
what you're going to get out of each portion. And that's what John brings to the table.
John Michael Guynn (38:52)
The cement companies could probably take advantage of this if they were to themselves make the blended SCM because, for example, I know that Geo Fortis here in Utah, their plant here in Utah was recently purchased by CRH. And so they are now under the same umbrella as Ashgrove Cement here in Utah. And also one of the Ready Mix producers is also owned by them.
So I can envision the natural pozzolan that's being produced in Utah being blended with a limestone powder without grinding so you can get the right particle size ranges. And then they could sell that as a blended product and maybe by selling the cement in tandem with this blended product,
then the cement companies might get credit for having produced a low carbon cement anyway. So that's just a that's just an idea.
Seth Tandett (39:50)
Yeah, or we can just reframe it somehow and get everyone to look at the concrete carbon footprint versus the cement, I guess. Because you're reducing the amount. I feel like we're chasing our tail. We could just reduce the amount of cement before we did all this. But anyways, but yeah, this was great.
John Michael Guynn (40:09)
Right.
John Kline (40:10)
Yep.
Seth Tandett (40:14)
This ties into a bunch of episodes that we recently had. was just looking through these on top of the ACI 323 episode we talked about. Folks might want to check out, had Tyler Lay on, we talked about the rise of blended cements. That's episode 103. John, what you're talking about too, John G., you're talking about...
a performance spec versus a prescriptive spec. We discussed that with Colin Lobo on episode 108. Let's see, what else was I going to point folks to? So if some of these things we're talking about, you might want to review these episodes. And the ACI 323 episode.
John Michael Guynn (40:57)
Thank
Seth Tandett (41:01)
is episode 109. if you're listening, you might want to review all those and then listen to this again, because I know I'm going to listen to this again. Was there, we mentioned ASTM 1697 and you said it was under review for maybe revision. Is that what you were saying?
John Michael Guynn (41:26)
Yeah, my understanding is I was talking to somebody that said that they're talking about, in fact, I saw some of revisions and some of the presentations were talking about allowing a blended SEM that contains limestone. I want to make a couple other points that first of all, that Orange Street project, we entered that into a contest or whatever with the National Ready Mix Concrete Association National.
Raymus concrete, NRMCA, and got one of the awards. think there were 48 contestants and we were one of the 12 who were given the award. So it was considered to be a very good low carbon concrete thing. I'm still, I wanted to share the screen. Maybe we don't need to share the screen, but we have durability tests now. Some people have been saying we've been talking to some of these engineering companies.
Bechtel, one of them, and they said, we want to see, this was last fall, want to see durability testing. So we now have durability test and we perform the same or better in all categories as the standard mix that we redesigned. First of all,
I can show the screen, but it's just a bunch of numbers. In terms of ASR reduction, we reduced ASR between 20 and 33 % compared to the standard mix, which contained a natural paucil unknown to be very good at reducing ASR, even better than fly ash.
And we further reduced ASR. Now why that is, is probably because we reduced the cement by 20 % and the cement contains all the alkalis that are gonna contribute to ASR. So by reducing the cement and putting in limestone, which does not contribute alkalis.
that we're reducing that. Plus I believe that because of particle packing, we have a denser cement paste. So it's going to be more difficult for ions to penetrate through. We still have air entrainment though, those microscopic bubbles are still there to prevent freeze thaw. And that's also borne out by some of the tests. we have fewer average coulombs of charge going through. resists salt incursion. Resistivity went way up.
in a different category. Freeze thaw damage, we were in about the same category. Scaling, we were off the charts better than the standard mix in terms of scaling when exposed to salt. Accelerated scaling. And then as far as shrinkage goes, showed that we had about the same shrinkage, although there are articles out there that say the use of limestone powder should...
because it's a microaggregate and doesn't react and doesn't...
doesn't shrink well it's during the hydration process it should act as a micro aggregate in the pace to to restrain shrinkage in that concrete company that I told about told you about before that did some side-by-side tests we always reduce shrinkage compared to their mixes every time so I believe that there are durability tests that show that not only is ours perform well in the other categories but in terms of durability it's very good and I did mention this when I went to the world of concrete was one of the
cement experts who was talking about admixtures to reduce ASR and I said we are reducing ASR more than your admixtures are by just doing this substitution of limestone with cement and not to say that your admixtures wouldn't work with ours but this is a again it's like an add-on that helps to reduce it a lot.
Seth Tandett (44:28)
Well, I would say that I know we had to do all those durability tests, but if you can go out there and point to something that's three to five years old from when it was placed and do those tests, I think it'd be interesting to take a core of that slab and see what the strength comes up with, because we all are so fascinated with 28 days, but we really don't study
anything beyond that and what concrete does beyond that. I think that would be interesting as well. Taking the last episode we released, we talked about petrographic analysis. If we took that and looked, it'd be interesting to see what your concrete looks like under a microscope versus what we typically use.
you know, there's pockets of cement that are activated in concrete that we use today. So if you look at yours under a microscope and there's not those pockets that could be interesting. Yeah, so, I mean, there's a lot to do there, but if you can convince a DOT, at least, you know, after doing this podcast for a few years and talking to people that are coming out with innovations, it seems like if you can get the DOT on board,
It opens the doors to many things out there.
John Michael Guynn (45:44)
Well, if anybody wants to see some of the durability test results and also think mention of the award we received from the National Ready Mix Concrete Association, you can go to our website, is www.roman-cement.com. We put the hyphen in there because it's easier to spell out and also early on Roman cement jam together spells, spells a romancement. And I think we've, we've been blocked.
Seth Tandett (46:08)
you
John Michael Guynn (46:10)
when I send emails because people might think that I'm sending some spam about some kind of dating site. So we put in there to eliminate that problem. But www.roman-cement.com websites is still a work in progress, but a lot of the basic information is there and it's going to, it's just going to get better.
Seth Tandett (46:15)
huh.
Yeah, that's
great. We'll stay in contact. John Klein, do you want to share how people can get ahold of you?
John Kline (46:33)
I would say just join me on LinkedIn and you can see my escapades there. I would close by saying you get all the environmental benefits of a 1L without some of the issues and your saving cost.
John Michael Guynn (46:45)
just one last thing. If people want to contact me directly, john.guinn.com. And I'd welcome any questions and I would answer anything that people would ask me.
Seth Tandett (47:01)
Yeah, I appreciate you both coming on the show today. I'm glad we finally got to do this. And it's interesting and I think people should look into it. It's a different way of producing concrete and we all have this challenge on our hands to reduce our carbon footprint. So I think this is a novel approach. So thank you, John Klein for connecting us. Thank you very much. Yes, sir.
John Michael Guynn (47:26)
Thank you, sir.
Seth Tandett (47:28)
And folks, until next time, let's keep it concrete.
John Michael Guynn (47:31)
Okay.
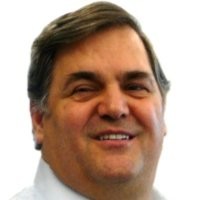
John Kline
Principal at Kline Consulting
John Kline is the Principal at Kline Consulting, LLC, a consulting firm assisting sustainable building material companies (start-ups to global producers), to improve their operational and environmental performance. John has over 45 Years in the mineral processing industry working in; Research, Sales, Plant Design, Engineering, Commissioning, and Operations. He retired from Lafarge in June of 2012 after 21 years, with the last 18 years in various international, executive positions. Kline Consulting is currently specializing in energy efficiency, operations optimization, green building products, and CO2 reduction technologies.
John has a BS degree in Chemical Engineering from Lafayette College, Pennsylvania. He has lived and worked in 6 countries on 4 continents and has authored over 20 peer reviewed technical papers, 40 magazine articles, and 100 technical presentations and webinars pertaining to the sustainable building materials industry.
IEEE – Life member
ASTM – C09 Committee
ACAA – American Coal Ash Association member
RILEM - Member
NIST- Low Carbon Cement and Concrete Consortium
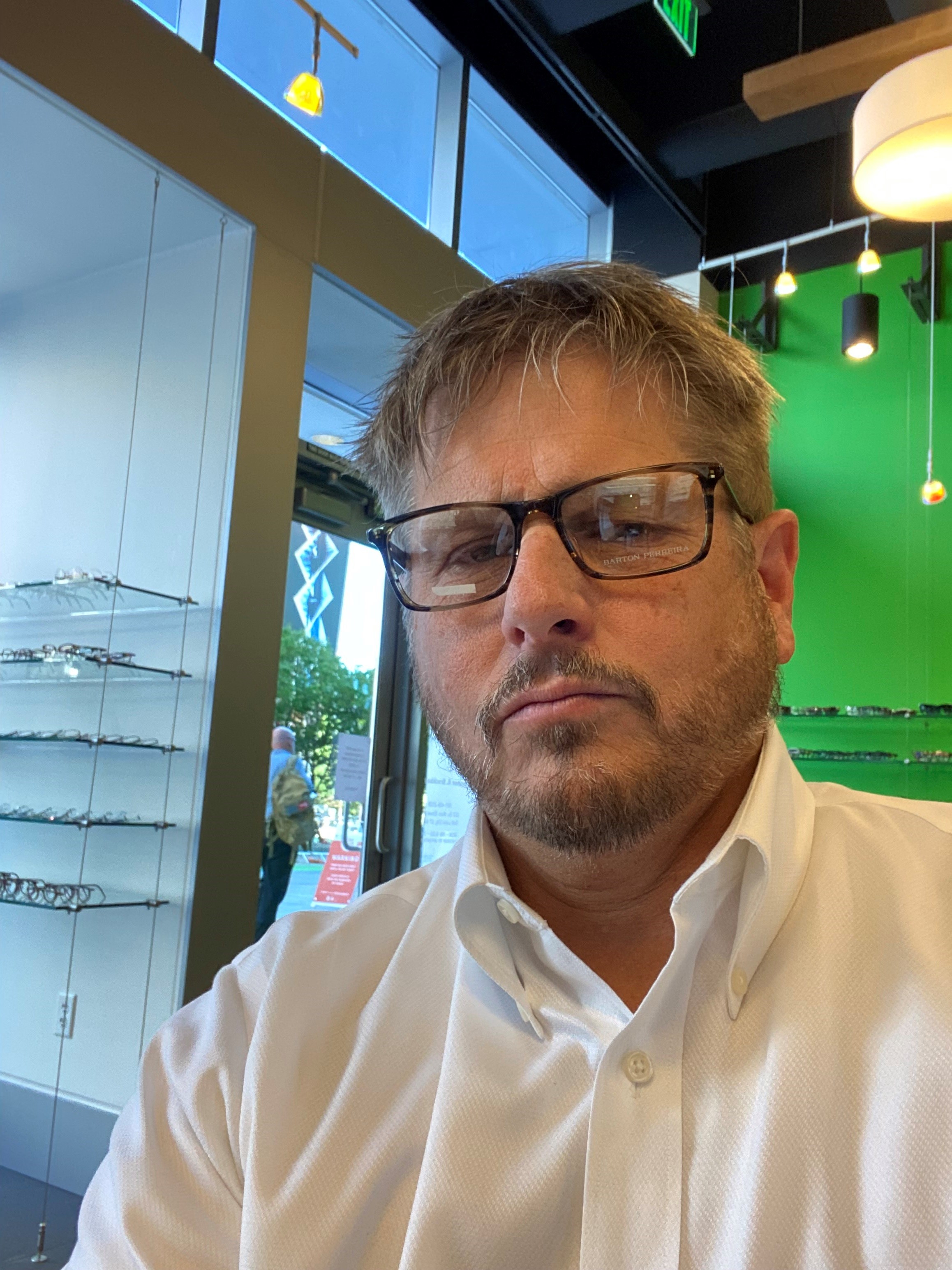
John Guynn
Inventor/patent attorney
I have bachelors and masters degrees in chemistry from BYU, a law degree from U. of Virginia, practice patent law as a vocation, and have worked for 15 years researching and developing a variety of ways to reduce cement content in concrete by particle size optimization of cement, SCMs and mineral fillers. Roman Cement, which I helped found, has done several field test pours for proof of concept.