EP #116: Why Concrete Fails โ The Hidden Truths About Moisture, Salt & Curing
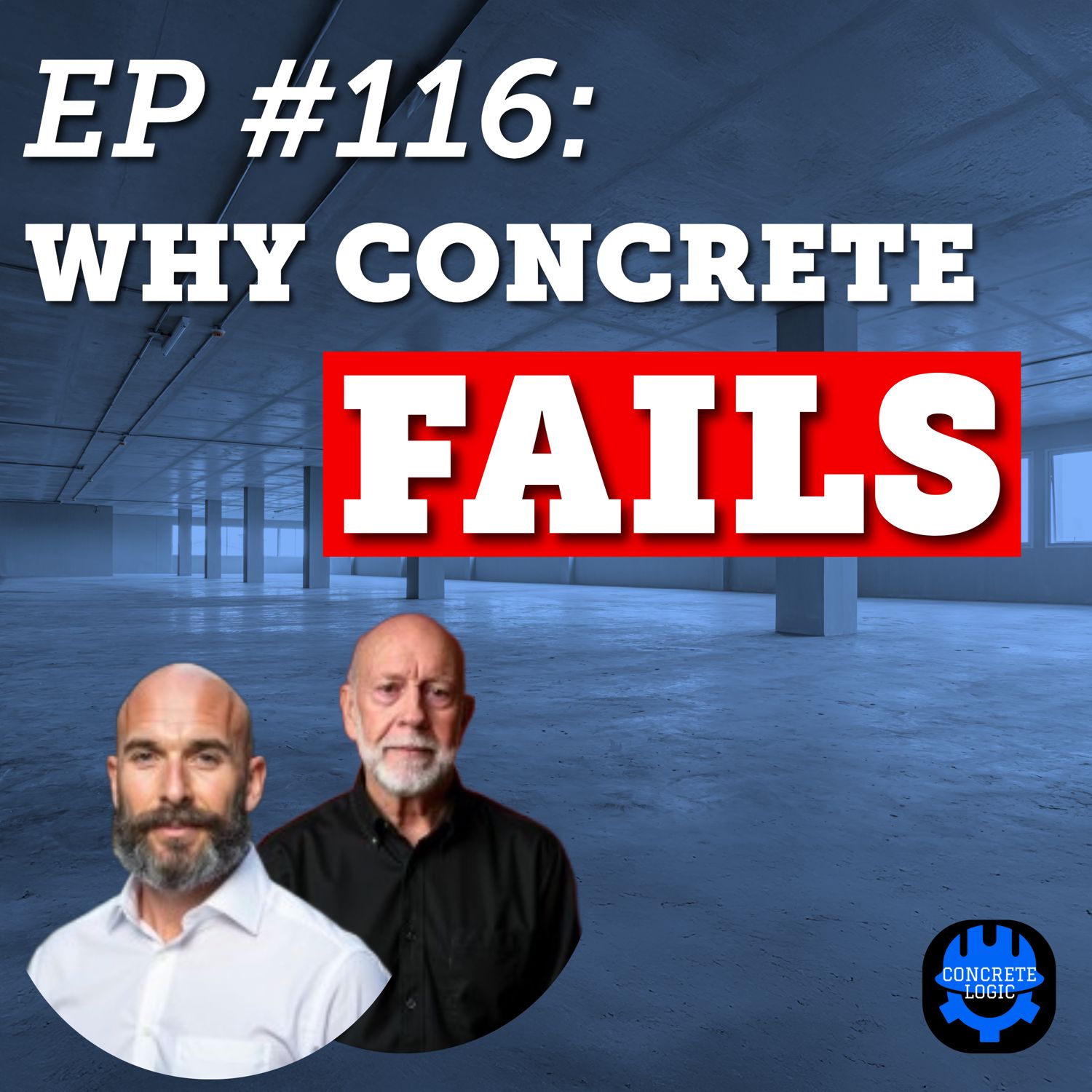
๐ฅ The Concrete Logic Podcast ๐ฅ
๐ ๏ธ Hosted by: Seth Tandett
๐ฅ EP #116: WHY CONCRETE FAILS – THE HIDDEN TRUTHS ABOUT MOISTURE, SALT & CURING ๐ฅ
=============================
This video is NOT sponsored. Some product links are affiliate links which means if you buy something we'll receive a small commission.
=============================
In this episode, Seth Tandett and "Concrete Bob" Higgins expose the biggest reasons why concrete fails. From moisture infiltration and salt damage to the surprising science of self-curing concrete, this episode is packed with critical insights that every builder, engineer, and contractor needs to know.
๐ What’s Inside:
โ๏ธ The real reasons older concrete is crumbling faster than expected
โ๏ธ How moisture and salts silently destroy structures from the inside out
โ๏ธ Self-curing concrete – the future or just another industry myth?
โ๏ธ Why the 28-day strength test might be misleading you
โ๏ธ The shocking truth about concrete chemistry (and why it matters!)
โ๏ธ How a lack of transparency in concrete production is hurting the industry
๐ CHAPTERS:
00:00 – Concrete’s Biggest Challenges
03:29 – Why Older Concrete Is Crumbling
08:40 – The Science Behind Moisture & Salts
15:13 – Game-Changing Curing Innovations
21:14 – The Real Impact of Environmental Factors
24:20 – What Happens When Concrete Meets Water
25:21 – The Hidden Effect of Salts
27:00 – Cement Composition Secrets
29:48 – Self-Desiccation & Strength
32:15 – The Future of Concrete Hardening
34:44 – Modern Concrete’s Biggest Pitfalls
37:49 – The Truth About Transparency in Cement
๐ง LISTEN NOW – This is a MUST for anyone in the concrete industry!
๐จ๐ฉ๐ฆ Guest: Robert "Concrete Bob" Higgins | RC Consulting
๐ง Email: rcconsulting.higgins@gmail.com
๐ Guest Website: https://www.concretelogicpodcast.com/guests/robert-higgins/
=============================
๐ Recommended Book:
Curing Concrete – https://amzn.to/41UMJ0u
๐ช Take Your Knowledge Further – Join Concrete Logic Academy!
๐ Gain exclusive access to expert video courses, live Q&A, and cutting-edge industry insights. Earn Professional Development Hours (PDHs) and elevate your expertise!
๐ Learn More: https://www.concretelogicacademy.com
๐ธ Support the Podcast – Be Part of the Concrete Revolution!
Donate: https://www.concretelogicpodcast.com/support/
Become a producer & get recognized on our next episode!
=============================
๐ถ Music by: Mike Dunton
๐ Website: https://www.mikeduntonmusic.com
๐ Stay Connected & Watch More!
๐ Host: Seth Tandett
๐ Email: seth@concretelogicpodcast.com
๐ฅ LinkedIn: https://www.linkedin.com/in/seth-tandett/
๐ Podcast Website: https://www.concretelogicpodcast.com
๐ LIKE, SUBSCRIBE & SHARE for more expert concrete insights!
#ConcreteLogic #ConcreteDurability #WhyConcreteFails
#keepitconcrete
Seth Tandett (00:01)Welcome to another episode of the Concrete Logic Podcast. And today I have Bob Higgins back on the show. Folks like to call him Concrete Bob. Isn't that your nickname down in Australia? They called you Concrete Bob when you were down there.Robert Higgins (00:17)Yeah,in Ireland, Germany, Switzerland, Australia, and some places here in the United States. Sometimes it's, some of the people here in the US use concrete bob in a derogatory way, but just because I, Tennessee still has those.Seth Tandett (00:24)Yeah.Well, I think to meif you're if you're associated with concrete and you concrete in your name then you're doing something right, but there's Bob's gonna go over a few things for us today So we're gonna learn about the challenges that we're having with older concrete as far as durability So when we say older concrete, we're talking about 10 years plus Also, we're going to talk about whyRobert Higgins (00:40)Ha ha!Seth Tandett (01:00)with the new concrete that we're dealing with now, how we can't properly cure that concrete, the ways that we know of curing. So we gotta come up with new ways of curing concrete. And then the last thing we're gonna go over if we got time is the differences in today's concrete versus older concrete. Before we get Bob started on that today.just want to remind you all how you can support the podcast. There's, several ways of the first way is if you enjoy the podcast, please share. And, with a colleague or a coworker, I've had people reach out to me on LinkedIn, asking how they can help. And that's the first thing I tell them. Just, just share it and get the word out. the second way is if you go to the website, concrete logic podcast.com.There's a couple of ways that you can get a hold of me. There's a contact link at the top of the webpage. It just says contact. You just click on that. And then at the bottom right hand side of page, there's a little microphone and you click on that and that's, they'll record right over the computer. it's like leaving me a voicemail. So those are the two ways to get a hold of me. And what I'm looking for from you is a guest or topic suggestions, things that you want to hear on the podcast. theNext week can help out is there also on the concrete logic podcast, homepage, www.concrete logic podcast.com. there's a donate button. click on that and you can give any amount and I'm serious. When I say this, any amount is, is totally appreciated. It just tells me you appreciate what you hear on the show and helps pay for the things to keep the podcast going.And then the last way is if you're one of those people are like, Hey Seth, I want to send you money, but I want to get, you know, something back or some kind of service back. with that in mind, what we came up with is, concrete logic Academy. So if you go to concrete logic academy.com, you can go on there, you can join several ways you can take, you can take a one-off courses or you can.join. There's monthly memberships as well, annual memberships, however you join. But it's essentially a community that everybody can go in, join, and we can talk about whatever we want. We can take courses. We got quizzes in there to take. So it just reinforces what we're talking about on the show. Same topics, maybe things that you won't, I know, things that won't just be discussed at the otheryou know, associations or industries in the concrete business. So jump on there. We got a couple dozen people already in there. So feel free to join those guys. And I think that's it for now, Bob. So we can jump right into what you want to talk about today. So you want to roll into the challenges we're having with older concrete.Robert Higgins (04:07)youYeah, I'm going to give an example. At the beginning of 2023, I was given a seminar to an installation, a foreign installation group up in San Leandro. And as I was getting towards the end, one of the installers said,I want to bring up something that confuses us and it continues to confuse us and we don't know why this is happening. said, okay, go ahead. He said, why is it the older concrete? We will do moisture tests and the moisture tests are consistently lower than newer concrete, but we have more flooring failures with older concrete than we do with newer concrete.I said, you know, that's a great question because I had to learn the hard way. I went through about 20 years of that before I finally, you know, got knocked in the head enough times to realize, okay, there's something going on here. So I did some analysis on it. And about 30 years ago, I did a hypothesis that the salt buildup towards the surface of the concrete can be extreme enough to where it can create sweating slab syndrome. although we didn'tcall it that it would just cause a dampening effect. I think Peter Craig actually coined that term sweating slab syndrome later on but when I came out with a hypothesis well I was I was attacked from all sides that's stupid concrete is like a big sponge and everything stable and well that's not true. What was really nice isI got vindicated later on, I'll finish this story. So anyway, I told him, said, it tends to build up towards the surface. Now, if you have a coating or even a hard trowel surface or a carrying compound on there, what will happen is moisture wants to move to the cool side. So the moisture, if the concrete is consistently cooler in the center, which it normally is, compared to ambient conditions, the trend is to move into the concrete. Well,Chemicals such as salts tend to get more active as it gets warmer. So it wants to migrate towards the surface. So we've got these this disparate Activities going on but what will happen after time it just kind of does this levels off it gives reaches a dynamic equilibrium But then when you strip the coating off now, it's exposed to a brand new moisture source, which is the ambient air and They just looked at me and saidHow's that possible? So with the salt, think of a calcium chloride test. You put salt on top, it collects water vapor into the little dish, and then you measure it. Well, just think of that. There's salts in the concrete. They're pulling moisture from the air rather than from the concrete. So that's what's going on. Well, they weren't quite sure they believed it until about three months later. There was this company that went out there to go show them their moisture meters. so we're going to show you how to use them.exact same location which was perfect. It was a 42 year old slab. It's out in the warehouse. They tested over the curing compound and it was 1.9 percent.moisture content. So they ground it off, tested immediately, it was 1.9%. Well they left and came back somewhere between 10 and 15 minutes later. They didn't keep track of it, but they said it was a very short period of time. They put the meter back down, it went all the way up to 4.3.So they called me immediately and how does this happen? I said, well, that's the salt I was telling you about with the older concrete. that it will, you expose it like that, it will attract moisture from the air. And I honestly didn't think it'd be that dramatic and that quick. So where the vindication came in, last year there was a European concrete conference and there were...studies, my god, in the seminars and everything else you kind of had to pick where you were going because there were literally two or three hundred seminars that were going on during this incredible amount of...concrete information being shared, and this is over in Europe. And anyway, this one company based out of the United States, Westin-Nielsener, showed on the September 24th, 2024, that salts tend to accumulate towards the surface of the concrete as it gets older, and that's one of the causes of sweating slab syndrome. So the hypothesis I gave over 30 years ago,This 20-year study confirmed it, and they did not know I was the originator of it. And they had no idea of other data that was coming in. They arrived at this independently, which to me is more important because there's no collaboration. When you arrive at a similar, almost identical conclusion using completely different approaches, that to me is the most compelling thing you can do.Seth Tandett (09:31)Yeah.Robert Higgins (09:31)And then thirdly, I was giving a seminar to this group. They apply epoxy coatings in commercial and industrial settings. One of the epoxy manufacturers now recognizing this with older concrete, they're also seeing this in some of the newer concrete. They test it first, and then with the older concrete, they normally recommend that you shot blasts.Well, they have to shot blast as deep as a quarter inch under some circumstances. And without doing that, they won't give a warranty for their epoxy. But when they do this, they're not having failures. So that's very compelling. Well, they discovered the same thing we did, the collection of salts towards the surface.Seth Tandett (10:22)So they're going down a quarter inch because they're taking all the salt off the surface.Robert Higgins (10:26)Yeah, well, I don'tthink they need to do that that deeply, but unfortunately, concrete is very inconsistent, especially in the surface. And it's been getting less and less consistent as we go, where the newer concrete is now starting to look more like older concrete.which is, it's really confusing the separation. There used to be a fairly clean separation. The concrete's five years old or less. This is pretty much what you could see in 10 years and older. And then there's that gray area that was between five and 10 years that could go one way the other, but now it's getting all mixed up. You can get concrete that's a week old and can start having the same issues as you can see in older concrete. But with older concrete,A lot of the details that we should have been taught are not being taught. All concrete goes through hysteresis. I'm not going to take a dive into these things because that's a rabbit hole we don't want to go into in this podcast or some of the other technical things I'll be telling you about. concrete also tends to be adiabatic, which is another technical term.But I learned that when I looked at the study done in Florida by the Solar Energy Commission. They wanted to find out what was going on, how they could optimize the rate of heating and cooling control in residential buildings. So they took these side-by-side homes in Cocoa Beach. This is fairly recent, 2015, 2016. And they found that the center portion of the concretetends to be adiabatic. Well adiabatic means the temperature doesn't leave or enter. It stays constant. That surprised me. But when I correlated it with another study that was done in 1974 byby the Army Corps of Engineers, they were testing concrete that was going to be used for these nuclear vaults and containment. So they were subjecting the concrete to 150, 160 degree temperatures. And they would do it from both sides. One of the key takeaways I saw in that is they referred to that as adiabatic. The central portion of the concrete, the moisture volume never changed.It didn't move because there's a dynamic that goes on that we're not being taught. Water tends to move to the cool side. Temperature controls water movement more than anything. People say pressure, but the pressure does not exist without a temperature change unless there's a forced outside environment. It has to be a forced outside environment. It has to be pretty significant. Otherwise, that won't happen.So what happens when you're drying out concrete that's going through that zone, we have gradients of the concrete that tend to isolate in the top 3 quarters of an inch to one inch of the concrete. Now, this didn't happen so much in the past because there's stuff that we put in the concrete now and the finer drying that is creating these issues where it's getting worse.We thought that with a finer grind, because if you go back to 1920, they had a very coarse grind of concrete. And if you just fogged it with water, say once or twice a day for three days, you had really good concrete. Well, when they started grinding the concrete finer, they found that, wow, look at the great strengths we get. And so they targeted the 28 days. I'm not quite sure why they picked 28 days. I've never really been able to.convinced myself that okay this is the genesis of that I'm not quite sure but the 28 day thing came up so let's get 3,000 psi at 28 days and that's great well what happens when they were using the finer grind they found hey we can use less cement still hit that target so by 1980There was in Concrete International Magazine, which is an ACI publication, an author by the name of Ed Monroe, who was a concrete technologist out of England, pointing out that with the finer grind cement, if you took...1950s concrete with a Korsha grind and put it side by side with a 1980s concrete and they're both 3000 psi, 1980s concrete would be five times more permeable. And also it generated more heat. So it was requiring longer periods of dampening with water to help cure the concrete because when it heats up, cement tends to accelerate and set.then it becomes retarded. Now, those links have never been established, which time and time again, I read study after study, and it's so frustrating because they're not tackling the chemistry. If they had looked at the alkaline salts, the salts end up collecting towards the surface. That desiccates the concrete. When you desiccate the concrete, cement will not form.Once it drops below 80 % relative humidity, cement formation stops. So why they're not putting two and two together, it's just absolutely mind numbing to me that they're not doing this. So another correlation, that's what we're going to start finding as we start curving into newer concrete.they were doing these studies globally where they had a more sophisticated method of measuring the concrete, where they embedded these relative humidity devices along with thermal couples. Now they found that the concrete in the field, when they're trying to even with the water cure, within two to three weeks after placement,the relative humidity in the first inch or so of the concrete would drop below 80%, even though it had water on it. Then they're showing that there's, basically it becomes, I don't like the way they explained it, but they said it, it,causes something that doesn't allow the water to penetrate, well, it's called dynamic equilibrium. That's the same thing that the floating people are dealing with. So you have that salt collect there. not gonna let what happens, it saturates, but keeps the relative humidity low. Because if you take a saturated solution, say of sodium chloride, just table salt, no matter how much water is in, if it's a saturated salt solution, the relative humidity will stay at 75%.Well, you can't form cement. And the alkaline salts in concrete are even more aggressive than that. They can actually bring the relative humidity down below 70 and 60%. In some cases, I've seen 50%. Well, once that happens, the damage to the surface of the concrete is irreversible. So by following current standards of carrying practices, we cannot give a customera good concrete like we did in the past. It's not as good as it used to be. We have to change our approach to caring.Really, so the only method really that I've seen is if they start making self cure concrete because the studies even the ones where they use like absorptive aggregate, which is ironic because absorptive aggregate used to be considered bad and they were and they were discounted and berated. Don't don't use that stuff because it adds to the water cement ratio. Well, now they're finding out that that doesn't happen. It's actually reserved for moisture that replaces the water that gets consumed during the initialcement hydration and replaces the water that's being used up and keeps the humidity higher so they get more cement formation. But it's too inconsistent because it's captured in the aggregate and it's not well dispersed through the concrete. So they're finding other issues where they're starting to have if it's dispersed poorly what will happen is they can get restraint.areas through the concrete and can actually a half-assed job like that can actually create more problems than it solves. again, this older concreteThe mistake is, it's a big sponge. Water soaks in and then it dries out. Well, with sponge, it doesn't have any chemistry going on in it. Concrete has all this chemistry and the salts are constantly moving, which is why hysteresis occurs. Hysteresis basically is kind of the opposite of diffusion in a way.Because when it happens, diffusion, what concrete will do, especially in a lab setting, it allows moisture in, allows it out, allows it in, allows it out. What happens with hysteresis, it allows it in, but hangs onto it for a while. Then slowly but surely let it go. And the older the concrete gets, and the more dynamic the environment, the farther apart these go. So the diffusion models are constantly used in these studies, no longer are accurate. So we keep...repeating these same tests, these same studies that don't help us. And we keep getting the same results and they don't match up with what we're seeing in the field. So I get so frustrated dealing with this because if you're going to do a study, if you ignore the chemistry in the concrete, why bother? Because the essence of insanity is doing the same thing over and over and expecting a different result. And that's what we've been doing for 70 years.Seth Tandett (20:11)Yeah.Yeah. When, just going all the way back to when the, you were talking about the 40 year old warehouse and they went and grinded off the, the whatever was on the surface, right? What they were grinding it off for what purpose?Robert Higgins (20:47)Yeah.We're not sure if it was, well, to grind it off, because it was a curing agent or it highly polished, they think it was a curing agent, because when they would put water on it, it would just sit there, it wouldn't wet. So it needs some more time here. Yeah. They wanted to see also if the moisture testing would be affected by the presence of the curing compound. I told them, do not make that...Seth Tandett (21:01)Okay, because they were going to go in and put something else else down. Okay.Robert Higgins (21:15)generalized assessment off of that because that's not an accurate way to do it.Seth Tandett (21:20)Okay. So what was your, I guess, solution to that? So they ground off the curing compound or whatever was on there so they could put in on the new material, but the new material required a certain moisture content, The moisture test to be below a certain amount before they put the new product on. So what was the solution to do that?Robert Higgins (21:45)Yeah.There are actually a couple ways of doing it and I tell them it depends on how high the initial rate is. one of things I pointed out, said this shows you the procedures how poorly executed they are. Because I used to be fooled by this as well because I thought you grind it, you let it vent for 24 hours. Then you do your moisture test. Then it'll be accurate. Well, no, that's not true. Look what happened.Seth Tandett (22:11)That was quite an eye roll, Bob.HuhRobert Higgins (22:18)So if they had waited till the next day, I don't know what the moisture level would have been, but they would have assumed it originated from the concrete, not from the air. So it's really important to get your baselines. And people are not establishing an accurate baseline in at least 99 % of the tests I've seen.Not even in the studies. They're not establishing a proper baseline. So what happens with that is if it's not too bad, what I like them to do is test it, grind it, test it again immediately, wait at least an hour and test it again. Now, if it's not climbing rapidly, you're in good shape. There's not much you have to do. But if it's climbing rapidly, you have to start, do the moisture test, grind down some more and test it again. Now, at the rate ofMoisture increase is very slow. You're probably in good shape But if it's if it's still going you're gonna you're gonna have to probably shock blast it and you put an aggressive blast on like that epoxy company does They just say screw it. We just just blast it and we're not gonna deal with it because they didn't want to go piece by piece but with some of these you don't want to blast a lot because it's it's a sense of environment and you want to try to grind it with HEPA filters and all that but another combination I found works really well and I stumbled across that that's not somebrilliant idea I had because I walked into this project and there are blisters on the epoxy and there but there were other areas where there are no blisters. Well wherever there were no blisters they had a trow down.So then I started looking at that. did an analysis and we looked at a few other pores and we decided to do this combination of where they ground it down. The moisture pickup was very slow, if at all. They put down a trowel down, which would allow diffusion, not only of the moisture, but also the salt. So it would allow the epoxy or the adhesive to properly set and cure before the moisture got there. Because once you set and cure and they're not invaded by the salt or moisture,no matter what they said, what's going to come back up again? So what? That's the reason why it stayed down for 40 years. But once we open it up, we expose it to a new moisture source. All we're doing is we're bringing it back to where it was. So yeah, the floor will stay down. The adhesive will stay down. We just need it controlled long enough to allow the adhesive or the coating to set and cure properly because they're really durable once you do that.Seth Tandett (24:49)Sothe two solutions are one, you shot blast it, which takes off the portion of the concrete that has the salts in it. Or the second solution is that you control the environment to a point where the moisture is no longer being drawn to the colder concrete, which is why there's moisture on there. So you control the environment so that stops occurring.Robert Higgins (24:56)The cream,Seth Tandett (25:18)just long enough for you to do the application. Is that right? Okay.Robert Higgins (25:21)Yes, yes, and thenand in this I found another one where They were applying this We're in these are two separate jobs when they were applying this epoxy and the epoxy started bubbling having failures Well, they removed it and put it back down again. They were having failures again So I said welldid you do an environmental analysis? said no. I said, well, do an environmental analysis. So they gave the temperature and relative humidity of the room, temperature of the concrete with an infrared thermometer, and then they tested the moisture, and it was all within acceptable range. And I said, well, what's the temperature of the epoxy?Well, it turns out the epoxy was really cold because they were storing it outside. were bringing it in, mixing it, and putting it down in the concrete. Well, when you put a cold material down, it'll pull water towards it. the epoxy actually attracted the moisture from the underside from the warmer concrete. So they said, are you sure this what's happening? I said, well, yeah, let's go warm it up. So I had them put these blankets on the epoxy buckets. They warmed it up to room temperature, did it again. Nothing happened.So they go, that was it? We thought it was a moisture problem. I said, no, you put a cold product down in a warm environment. I said, it's worse when you put down an adhesive because now you created a bond breaker sandwich. So it'll pull moisture from the underside and from the surface. So then when you put your floor down, you got too much moisture in the adhesive, too much moisture on top of the adhesive, you put the floor down, it's going to fail.I mean, those are fundamentals that we're not dealing with.Seth Tandett (27:06)So that.Yeah, so the temperature of the concrete, adhesive, and then above the adhesive all need to be the same temperature.Robert Higgins (27:19)Yeah, or as close as possible. And what you want to do is, and now they talk about, relative humidity, blah, blah, blah. The only relative humidity that's important at the surface is make sure that you're at least 10 degrees above dew point. If you're at least 10 degrees above dew point, it's not going to fail. You know, they try to make it look so scientific. It's just, no.If it causes dew on a leaf or a surface, yeah, then you got to take care of that.Now, the other thing, and this is what's so important, that's salt on the surface, because I'm going to go all the way back there. A salt on the surface, that is a hygroscopic salt. Everybody keeps talking about dew point, dew point, dew point. There's two types of dew points that we're dealing with when we're dealing with concrete. That's atmospheric dew point, which when it starts approaching 100%, things can get wet. Now you can see things getting wet before 100 % if they're hygroscopic, so glass andand surfaces like that can actually start getting a layer of film of water on them even before atmospheric dew point occurs because of the strong attraction it has.So when people say, is it that strong? I said, well, yeah. I said, one of the good examples I like to give, because the salacious, it's SiO2, it's just silica. Well, so is glass. Glass is silica. So I use that as an example. I'll take two lenses that you use for microscopes and put a drop of water in one, stick them together. And I tell them, OK, pull those apart. They can't do it.They can slide them apart, but they can't pull them apart. The attraction of the water is so strong to the surface, it clings and acts like a glue. So it's hanging in there. So if you have those salts, that attracts even more. And it hangs on to the moisture.Seth Tandett (29:15)Yeah. But the salts are, if we're talking about newer concrete, how long does it take the salts to accumulate on the surface?Robert Higgins (29:26)With the older concrete back, again, prior to 2002, I would say that it would probably take at least five years to be even a minor problem. But 10 years and older seems to be like the area there where you start having problems. So all concrete prior to 2002 is over 10 years old now. So that's a test.Seth Tandett (29:50)Yeah, way over.Robert Higgins (29:52)Yeah, way old. Now what I wanted to talk about with the salt accumulating, that has an ionic dew point. It has a dew point, like I explained earlier with the sodium chloride. Depending on the salts, it will attract water at maybe 60 % relative humidity, 50 % relative humidity. We don't know.So it can accumulate and start getting damp. And we don't think it's damp because we're not even close to atmospheric dew point. People get tricked by that. So that's why you got to take that salt off the surface. Because if it's doing that, even though it looks dry, and if you use a relative humidity probe, that doesn't tell you squat, because this is all at the surface. But you can find it out with a moisture meter.Seth Tandett (30:38)Yeah. I guess the reason I'm asking the question is with newer concrete.If I circle back to your original story about the guys grinding off whatever was on the surface of that concrete and that exposed the salts to draw the moisture to the concrete. If we're talking about newer concrete, the reason why I asked you how long it takes the salts to get to the surface is if you put down new concrete,What we're seeing especially in data centers and warehouses is there's a lot of use of hardners. So they're putting down this hardener. If the one manufacturer that pops my head, I believe they say you have to wait 28 days before you put it down.What I was wondering is how long does it take for the salts to reach to the surface of new concrete if it's longer than 28 days is I guess There in theory is these hardeners Stopping the salts from getting to the surface. I guess is what I was getting atRobert Higgins (32:04)Well, that would have worked with older concrete, at least to some degree. I'm glad to hear that they wait 28 days because some of these NIMNODs put it on the day after or the day of the pour. No, don't ever do that. But the problem is between 2002 and 2018, the EPA kicked in a requirement whereSeth Tandett (32:08)Uh-huh.Yeah.Robert Higgins (32:25)These cement manufacturers had to gradually come to compliance and that's why it took such a long window of time Because they don't want to put them out of business But they had to comply where they were recapturing some of the flue gases to stop stop co2 and all this pollution that the cement Manufacturers were putting into the air and it's called CKD or cement kiln dust cement kiln dust is extremely alkaline now it varies from plant to plant because it your local resources someAggregate is more out than others. That's just regional. That's just the way it is So some will have a more severe problem than others so you can't take okay a nice neat package that this is what we do all the way across the country Now if you go worst-case scenario, it's too expensive, but if you go optimistic you're gonna miss things soWhat's bothering me is the cement producers are not coming clean with this. I would, because I asked them, said, what is your CKD in your cement? They wouldn't tell me. I said, look, well, I didn't sign an NDA, but if we're going to compensate for this, I have to know what the content is. But if you're not sharing this with me, it's a big guess. Because cement kiln dust is so alkaline that...during the curing process, which prior to this near-service alkalized silica reaction was an issue. It's more of an issue now than it ever was because there's now more alkalinity. Now the alkalinity where it's really, really bad is sodium hydroxide, which is the main alkaline component of the cement kiln dust.suppresses the solubility of calcium hydroxide. By suppressing the solubility of calcium hydroxide, what it does, it inhibits the formation of additional cement.So here's where the chemistry is not being addressed in these studies. They're wondering why this self-desiccates so much and they're blaming the cement. Well, no, the cement formation will consume some of it, but not all of it. Because you have technically enough water in there, even with a very low water-cement ratio, to hydrate all the cement. The reason why it can't, and especially if it's warmer...What will happen, the heat will trigger that and you get a spike where you get a rapid formation of cement, then it drops off a cliff. It drops off a cliff a combination of heat and alkalinity. Heat and alkalinity both suppress the formation of cement. They both do. Alkalinity creates an artificially low, I can't say artificially, but it lowers the relative humidity.So that's what's causing the lowering of relative humidity in the top inch of the concrete, is this new alkalinity. So does it affect the concrete? Immensely.I saw a study done by the Texas Transportation Institute, and this was fairly recently, I think it was 2014, where the concrete was 4,000 PSI. They water cured, they did a seven-day water cure, and this is in allow. They did a seven-day water cure and then an air cure.I'm not even going to address the air cure, only the water cure. Seven day water cure, nobody does because you can't spend the resources on it and the water, you know, that's considered a waste of water. But what they did is they went ahead and did the seven day water cure, but they found that this surface was still self-desiccating. Not to the same extent that you see in the field, but it was still dropping and got close to 80%.and then eventually dropped below that, but after a couple of weeks, it got close to 80%. 80 % is the bare minimum to form cement. That's too slow. And you're gonna get an inhibition of the cement formation. So what they did is at 20 days, they did a compressive strength test of the concrete, 3000 PSI. It was fine. However, he sliced off the top edge. It was a full 20 % lower in compressive strength.Why? There's not as much cement. This is not a uniform homogenous material. So if you start correlating what we're seeing with the salts, the self-desiccation, the near surface ASR, all the evidence points to this alkaline salt collecting in the surface, and we're not addressing it. If we address the surface, let's say you put in something like a colloidal silica. A colloidal silica...in my opinion is being presented incorrectly or incompletely I should say. They show how it acts like a pozzolin and reacts with calcium hydroxide. Well yeah does. Now so do other pozzolins but what happens if it self-desiccates and the calcium hydroxide doesn't form the pozzolins don't do squat especially a dry ad. Now colloidal silica is wet. It adds water to it every time it reacts so it's replacing its own water.with this and gives off its water. However, if the alkalinity is high enough, I don't think we'll get a consistent result. So if we know what the CKD level is in the cement, you can compensate by adding more colloidal silica. Now the colloidal silica, what it does is it will react with the sodium hydroxide and convert it to sodium silica.Well, that's OK because the sodium silica is not an admixture. It's already in there. And the volume and the setting of the concrete have already established themselves when this starts to react. So it doesn't thicken the mix. But what it does, by reducing the sodium hydroxide, it stops the self-destruction of the concrete surface. Because I saw a study done by Purdue.Seth Tandett (38:15)Hmm.Robert Higgins (38:27)And the surface, you know, and we have to take this to the grain of salt because they did this in a laboratory, but the surface is actually denser than the remainder of the concrete. I honestly didn't think that was possible. So there are ways, and it's not just colloidal silica, there are ways of creating these admixtures that don't cost a lot of money. fact, you know, it's basically it's just management of moisture.don't cost a lot of money, but they can create a self-curing concrete. We don't have to put water in the concrete anymore. It becomes self-curing. We get rid of that weak and layer. And I will tell you right now that I guarantee that all these problems are having with things like type 1L cement and the carrying issues they're having with elevated temperatures, those are going to go away. We're going to have a really good concrete.It'll probably last at least twice as long as conventional concrete and probably last longer than the concrete they were placing in 1920. So we'll have really durable concrete because that durability goes across the board because if you look at weathering...Seth Tandett (39:30)Mm-hmm.Robert Higgins (39:38)characteristics of concrete and durability it almost always starts from the top down. It doesn't come from the bottom up, it's top down. Bottom up is usually subsidence or frost heave or something else like that. It's not the concrete itself. Most of the weathering durability issues we have goes from top down. ASR starts there, all that.Seth Tandett (40:05)So going back to my original question, I think you might have answered it in there somewhere, but I might have not caught it. I know you gave the answer to our third item that we wanted to cover, which is the differences in today's concrete versus the older concrete and why we can't cure it like we typically do, which is a chemical application you spray it on or...Robert Higgins (40:13)So I didn't want toSeth Tandett (40:34)or yeah, that's normally what we do. Cause like you said, no one does wet cure anymore. Cause it's, it's just the logistics and the cost of it is cumbersome, especially in today's environment of concrete construction where you don't want things to slow, slow things down. So do you want to build these things fast? Get, get, get the other trades behind you. So the wet carrying isRobert Higgins (40:51)Yes.Seth Tandett (41:04)just not feasible. I do see it though on water treatment plants, pump station type jobs. So they do have it still on that, believe it or not. But anyways, so going back to my question is, are we...Maybe we're just masking or covering up the salts that are coming to the surface when we're putting down a hardener at 28 days. Is that?Is that something that could be happening? Because what I'm hearing is these hardners are specified and very common companies that you know that are out there that build big warehouses and they build data centers, the hardners are specified. So.Robert Higgins (41:51)Well, I think it's, yeah.Seth Tandett (42:15)There's gotta be something out there that the engineers are seeing that there's a reason why they're specifying these products. There's gotta be something out there that says, hey, this has given us a durable surface, a durable concrete. That's why we want it in our specifications.Robert Higgins (42:35)Depending on the chemical makeup of the hardener, I don't like the alkaline silicates as a hardener because if you have cement kiln dust in there, it's going to add more sodium.Seth Tandett (42:38)Uh-huh.Robert Higgins (42:50)ion to the mix and you don't want to do that. Lithium silicate is a good hardener for that and certain colloidal silicates. Those I think they're probably the predominant hardener's that being used today and I have no problem with those. So if all you're doing is hardening the concrete that'll work great. You just can't put anything on it.Seth Tandett (43:11)Yeah, I do.Robert Higgins (43:12)you keep puttingit on afterwards. You'd have to go through what you did before and just shot blast it, get that salt out of there, and basically treat it like an older piece of concrete.Seth Tandett (43:23)Yeah, and then your comment about you were glad to hear that there's there's They're waiting for 28 days. I have heard I haven't been part of a project that's done this but I've heard people putting the hardners down Before the 28 days actually after the concrete is placed and they're using it as a cure YeahRobert Higgins (43:43)Yeah, no, no, no, no, no, no, don't doit. Even in lab study, I saw this study done with metakaolin, which is a type of posilin admixture. It was shown that the development of the normal development of calcium hydroxide took anywhere from five to seven days to develop in a lab setting in a.Field setting could be nearly a month before it all forms. At least, you know, we're substantially formed. And you do have to wait for that for the hardeners to do you any good. Now the lithium hardener and the, uh, the colloidal silica probably don't have to wait that long because they will do things independently. I call lithium silicate a forgiving one and, uh, theAnd I call colloidal silicates the patient ones because they'll sit around and wait for the calcium hydroxide to form and then react. Because they're pretty selective about what they react with because they have to react with an alkaline component. Because if you take colloidal silica and mix with sodium hydroxide, it'll make sodium silica. So it changes it to something that's...type of a hardener. So it will set it'll secondary hardening as well. So in that kind of a sodium silicate you're not adding more sodium to the mix. If you're spraying sodium silicate on there, you're just compounding the issue. So I don't like that. But with the lithium or the colloidal silica, you're not compounding the issue. You're restricting it.Seth Tandett (45:22)Okay. All right. Well, I think we hit on the three things we promised that we were going to talk about today. Is there anything else you want to hit on before we go?Robert Higgins (45:38)are also additives in use for cement grinding that are creating complications and it was nice because it was acknowledged on LinkedIn. I brought up the issue about the...issues they have with the grinding aids and it prompted quite a bit of discussion because the grinding aids that they use now that are the most efficient are glycol based and amine based. Well, those don't go away. Those don't exhaust.I'm not sure how much they put in there. But what happens, Sika, and I'm gonna give him credit for this, Sika out of South Africa, this gentleman was doing a study on it, he was looking at this decorative concrete, and the cement grinding aids were reacting with some of the aggregate in the concrete.Creating liberation of the iron so that it was floating to the surface. It looks like a bunch of rust spots on the on the concrete now that sounds slightly for Decorative concrete, but what's that doing underneath the coating you don't want iron under a coating? under any circumstance that's going to change a lot of things and Besides debonding andcreating issues with future coatings that were just not being told this because as I did more research I found that the cement producers are not required by law to divulge what they put in their product. That is ridiculous. The ready mix producers are required by law to divulge what they put in if it's not sand, water, cement, and aggregate.If they put anything else in, they have to divulge it. If they just give you concrete, they don't have to divulge anything. But I think it's unfair that they get saddled with a product they don't know what's in it. And they can have things go wrong, go south on them. The concrete contractors have things go south on them, and they get blamed for it. Well, I saw a...I revisited a problem they had up in the northeastern portion of the United States where all this carpet tile failed. And they blamed it on plasticizer migration. And the manufacturer got nailed. Well, and they were showing the alkaline to the concrete was contributing to it, blah, blah, blah. Well, as I started looking at it in hindsight,They never tested for amines or glycols, even though they were in there when I looked at the mass spectrometry, where they were doing the chemical analysis. Those were in there.They didn't identify where it came from. They just assumed it came from the backing of the carpet or something, the liner, the adhesive it had or whatever. They just blamed it on that. That could have originated from the cement, but nobody bothered to look because they were never told. This information is not being divulged.And we have to all come clean so we know what we're dealing with. Otherwise, people get thrown under the bus that didn't do anything wrong.Seth Tandett (49:06)Yeah, or come up with a, I don't know if there's a test out there that people we talked about on, think a couple of podcasts is how you can, test your cement when it comes in. So before, before, putting it, you know, utilizing it, there's, there's a, you could set up a, essentially a, a quality assurance or quality control,program to test your cement and so that you do know what you're dealing with but on the other hand I think you knowUm, I think your, your, your concern is, uh, beyond, it fair to say beyond a 28 day, 28 day strength? Cause that's what we're all concerned that that's what the concrete, uh, ready mix supplier is, is graded on, right? He's got, uh, sometimes a three day, a seven day and a 28 day, uh, uh, test that he's got to show that, uh, he's met a strength. So.Robert Higgins (49:56)Yeah.Seth Tandett (50:16)I think your concern is beyond that and it's difficult for us to think about what could be down the road for the concrete being blamed for, I guess.Robert Higgins (50:32)Well, yeah, because the workmen get blamed because they're not chemists. They're not scientists. They're skilled craftsmen. They should be allowed to do what they're doing without having to look over their shoulder every time they put something down. And this really irritates me. What you're talking about with your cement quality control, I would love to see some of that in aget feedback because I would have a different perspective on that from a chemical standpoint because like you said all the emphasis on 28 days that is the worstbenchmark for quality concrete, the worst. Because the higher the 28 day is, especially with warmer temperatures, it means your concrete's going to be weaker in the long run. Correlations are always there. One of my favorite whipping boys is to show the surface absorption of precast concrete. Precast concrete that's steam cured, if you sit it side by side with a piece of concrete that you've placed,with your company, if you put them side by side, if you throw water on your concrete, it will dampen the surface and gradually go in. But if you throw the same amount of water on precast, it'll disappear. Throw it on there again, it'll disappear. Throw it on again, it disappears. Why? Because there's no cement on the surface. It's really permeable. But that heat destroys cement formation.So inside the precast, it's really durable. Now, if you could take precast and sacrifice the first inch, you would have one incredible piece of concrete. So if you overdesigned it, say by two inches on either side and considered your, gradient is like an icing around a cake or something, remove that icing, expose the cake. You'd have an incredible piece of concrete, but we don't do that. So it soaks in, carries in things that are not supposed to be in the concrete and starts the damage.in the surface and it works its way down. I mean, again, we're ignoring the chemistry. If we start incorporating the chemistry, and this makes sense, we will know how to compensate for what we're being given.Seth Tandett (52:51)You'reright. Yeah. All right. Well, I think this is a good spot to end the day. We went extra long, but there was a lot of good nuggets in there. So I hope everyone was paying attention. Bob, there a, I usually ask you if there's a, if people want to reach out to you, how do you want to reach out to you? But I'll just, I'll put your information show notes. Is there's, are you given any talks or conferences?coming up or anything you want to plug before we go.Robert Higgins (53:22)Well, notin the next couple of months. just, I'm kind of burned out right now because I had five in a row. And I think I'm down to two brain cells and they're playing hide and seek.Seth Tandett (53:29)Okay.Okay, all right.Well, we'll like I said, we'll put your contact information in the show notes as usual and I appreciate you coming on the show today. All right, folks, until next time, let's keep it concrete.Robert Higgins (53:47)Thank you, Seth.All right.
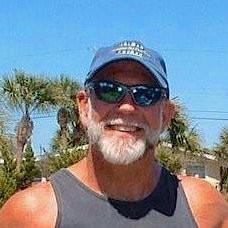
Robert Higgins
Involved with waterproofing and restoration of buildings and specialized in concrete. Have been involved with several committees with professional groups such as ICRI (first chair for moisture testing), CSI, speaking at national and regional conferences, authored the Flooring industry โWhite Paperโ for the WFCA (World Floor Covering Association), moisture test instructor for the Academy of Textiles and Flooring, guest instructor for ICRI. Authored many articles regarding weather and environmental durability of concrete in multiple publications. Currently involved with IICRC Committee S230 and NFCA (National Floor Covering Association) โbest practicesโ for moisture testing concrete prior to installation of Floor Materials.