EP #087: The Importance of Properly Curing Concrete
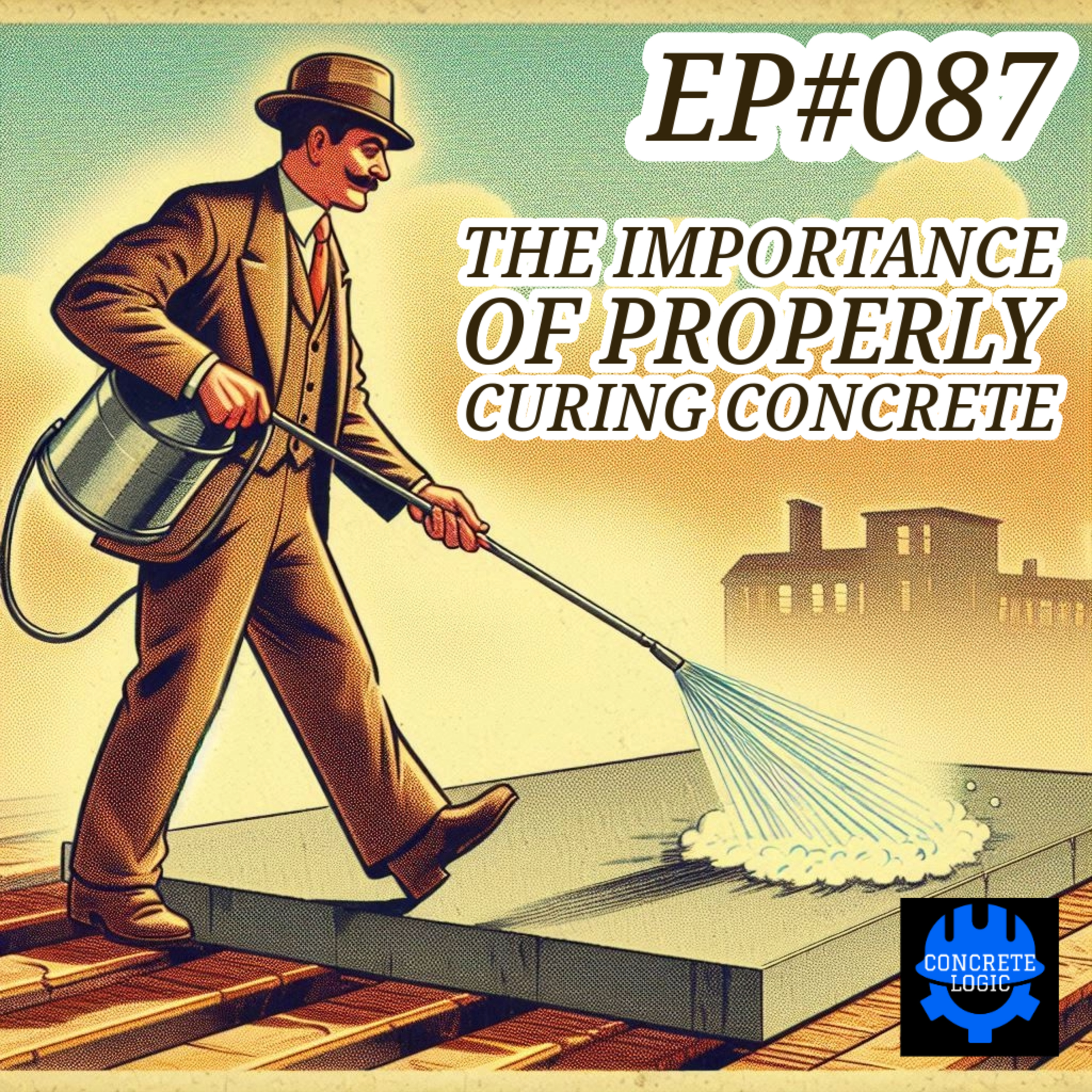
In this Concrete Logic Podcast episode, Seth and Robert Higgins discuss the importance of curing concrete properly and the impact it has on the durability and sustainability of concrete. They highlight the historical practices of curing and how they have not evolved to keep up with changes in concrete composition.
They also discuss the effects of temperature on curing and the role of alkalinity in concrete. The conversation emphasizes the need for improved curing practices to ensure the longevity and performance of concrete structures.
Takeaways
- Proper curing practices are essential for the durability and sustainability of concrete.
- Historical curing practices have not evolved to keep up with changes in concrete composition.
- Temperature plays a significant role in the effectiveness of curing, with higher temperatures leading to faster curing but potentially weaker and more permeable concrete.
- Alkalinity in concrete, caused by changes in cement production and the use of additives, can affect the curing process and lead to weaker and more porous concrete.
- Improved curing practices can significantly increase the durability and sustainability of concrete structures.
Chapters
00:00 Introduction and Podcast Support
02:41 The Effectiveness of Curing on Concrete
08:22 The Impact of Alkalinity on Concrete
10:26 The Effects of Temperature on Concrete Curing
22:36 The Weaker and More Porous Surface of Concrete
28:34 The Importance of Proper Moisture Content in Concrete
32:14 The Potential for More Durable and Sustainable Concrete
37:30 The Need for Improved Curing Practices
41:29 Testing and Understanding Alkalinity in Concrete
45:03 Conclusion and Closing Remarks
***
Did you learn something from this episode? If so, please consider donating to the show to help us continue to provide high-quality content for the concrete industry.
Donate here: https://www.concretelogicpodcast.com/support/
***
Episode References
Guest: Robert Higgins | RC Consulting | rcconsulting.higgins@gmail.com
Guest Website: linkedin.com/in/robert-higgins-b8294411
Producers: Dan McCoy ($257.94)
Donate & Become a Producer: https://www.concretelogicpodcast.com/support/
Music: Mike Dunton | https://www.mikeduntonmusic.com | mikeduntonmusic@gmail.com | Instagram @Mike_Dunton
Host: Seth Tandett, seth@concretelogicpodcast.com
Host LinkedIn: https://www.linkedin.com/in/seth-tandett/
Website: https://www.concretelogicpodcast.com/
LinkedIn: https://www.linkedin.com/company/concrete-logic-podcast
Seth (00:01.054)
Welcome to another episode of the concrete logic podcast. And today I have Robert Higgins. He's back. And let's see, Robert, I was counting episodes here. One, two, three, four. This is number five for Robert or I learned this morning. You're, you're known as concrete Bob. I did not know that. And we've done this five times now. So, this is going to be episode 87.
And we're going to talk about our favorite topic when we have concrete Bob. It's still funny to me. On the, on the show, we're going to talk about concrete moisture and curing. Before we get started, just remind everybody about how this, this podcast works. I ask you to do three things to support the show.
First is to share the podcast. So if you get something out of the podcast today, which I promise you will today, please share it with a colleague, coworker, or somebody else in the industry. The second thing you can do is if you could go to ConcreteLogicPodcast .com and click on either the contact button or there's a little microphone button at the bottom right -hand corner of the homepage and leave me a message.
suggesting a topic or a guest. And then the last one is, there again on that homepage, concrete logic podcast .com upper right hand corner. There's a donate button. If you click on that, you can give any amount. And today I want to thank Dan McCoy. He donated $257 and 94 cents.
Dan, thank you very much. Dan will be listed as a producer of today's show. And of course, Dan's been on the show several times. Again, Dan, thank you. Appreciate your support. And with that, Robert, I'm so used to calling you Robert. I'm not going to call you Concrete Bob, but I saw that post on LinkedIn this morning. I thought that was funny. So today, we wanted to talk about curing.
Seth (02:19.518)
And I'm going to share my screen and we're going to do our best to explain to the folks that are just listening and not watching us on YouTube what we're talking about today. So with that, Robert, you want to kick us off and let's talk about the effectiveness of curing on concrete.
Robert Higgins (02:41.952)
Okay, thank you, Seth. by the way, I did not nickname myself Concrete Bob. Somebody decided that was a good nickname for me and it stuck. So I can't get rid of it. The thing about curing concrete, it started out as a really good idea and basically curing practices have not changed that much since the 1920s.
Seth (02:52.51)
Hehehehe
Robert Higgins (03:07.616)
But back then we were dealing with a far different concrete than we're dealing with today. Because back then they had a very coarse grind of cement and it would react slower and it released heat slower. So there was a less buildup of heat. It was a slower reaction. So they kind of nurtured it along by keeping it wet. And it produced a really good strong concrete. But then they found that if you grind cement finer, it would...
it would produce a much faster set of concrete and would cure faster, but also produce more heat. And that was not ever adjusted for. And at first it didn't matter because the grinding wasn't so fine that it created issues that were noticeable as long as you used a water cure. But where this really starts separating, if you take...
concrete from the 1950s. Ed Monroe in Concrete International magazine in 1984 did a really good article on this. It showed that the concrete in the 1980s versus the concrete in the 1950s, if you evaluated them and you took 3000 PSI concrete at 20 days from 1950 to 1980, the 1980 concrete was 500 % more permeable to water.
than the concrete back in the 1950s, which showed the effect of less cement as well, because they didn't need as much cement to produce a 3000 PSI concrete. So we had this cascade of effects that we've never adjusted for. So...
So they're wondering why concrete isn't as sustainable as it used to be. And a lot of them won't admit that, but if you look at the, but it's kind of hard to find. You have to go back into the archives section of Google and some of the other ones to find it. But way back when in the 1970s, they were designing bridges or supposedly designing bridges to last between 80 to 150 years. Now they've kind of have that.
Robert Higgins (05:24.068)
expectation was 75 -80 years now and in most cases most concrete surfaces need to be repaired to some extent in as little as 12 to 15 years so we're not getting the sustainability and it really all falls back to the curing practices because properly cured concrete can get extremely dense but if you don't cure it properly
especially in the first 30 days, what happens you have permanent porosity increases, a permanent permeability increase. So let's go to the next slide.
Robert Higgins (06:08.448)
Now, this is unfortunately more typical than atypical now. Even in a lab cured specimen, you will start finding this where the top surface of the concrete is obviously more porous, but it's also more permeable. And those are two different situations. And you get them both involved, and that's not a good combination. Because one of the...
contributing factors and a significant one was when the EPA, they started pushing for this back in the 70s actually, and then came up and pushed it hard in 1983, but it was not really, they kept delaying it because of all the challenges of trying to make CO2 less of an issue with the flue gases when cement production.
So in cement production, we said, okay, it's producing too much CO2 and it's releasing toxins into the air and we need to recover it. So in the recovery process, there's this material called cement kiln dust. Now cement kiln dust is kind of a cementing product in and of itself, but it's also extremely alkaline. That has now been re -added into the cement process.
which was gradually done between 2002 and 2018. And it was probably finalized towards the end of 2018 because in 2019, the concrete industry came out and stated that low alkalized cement will no longer be available. Well, you can't make low alkalized cement with CKD in it. Cement killed us. It's too alkaline. You can't do it. So they kind of minimize the impact.
horribly so in my opinion especially now that they're using even a finer grind of cement so that has a really a dramatic effect on the alkalinity and what it's going to do and I'm not going to get into the additives too much because that will kind of sidetrack us a bit but let's go to the next slide
Seth (08:22.43)
Yeah, before we move on, just to folks that are just listening. So we're looking at a cross section of a piece of concrete. And the top of it really looks like a sponge. It reminds me of a sponge. And then the top, what do you say, this half to half inch to an inch, Robert, is.
Robert Higgins (08:44.84)
Yes.
Seth (08:48.702)
looks like a sponge and then down below that the concrete it's solid. It's definitely there's a big difference between that top layer and the rest of the concrete. So that's what we're looking at.
Robert Higgins (09:00.128)
And it shows you the fallacy of what the moisture test will indicate because there's this big reliance on RH probes and the requirement is to sink the RH probes at least two inches into the concrete. We've completely bypassed the problem area. You're not going to get any information with that because when you go deeper into the concrete, that's fairly stable and that moisture content will remain that way for a long time, many years.
Seth (09:29.822)
Yeah, I mean, if you just look at this slide, I mean, you could tell that that top layer there, that's going to be dry, right? And down here, more likely would have moisture. Just looking at the slide, if you were just.
Robert Higgins (09:42.334)
Yeah and the top layer even though it looks dry it probably is as far as RH goes but it tends to be very alkaline so holds a lot of water disproportionately so.
Robert Higgins (09:58.208)
Now this graphic, a lot of this information has been collected since the 1940s through the early 2000s, which I think is really dramatic. This shows the effects only of temperature at time of the curing of concrete. We've been taught and just drummed into us that 28 days, the higher the 28 day strength, the better the concrete.
Well, that's not true. It's very sullen truelish. You've done something to really modify that cement mix. A higher 28 -day strength is generally an indication you're going to have a very low durability concrete. And the greater the strength difference between 28 days and 365 days is dependent upon the temperature. Now, this graphic that we're looking at,
This is the effect of curing at 28 days under these temperature differences. If you notice, 55 degrees, the 28 day is unacceptable. It's 43 % and that will delay construction schedules. So they won't, they don't like that. They'll speed it up and they'll do what they can to make sure that the concrete hardens and sets faster. 73 degrees at this time was ideal.
Then as you get to 90 degrees, wow, look at that. You get 127 % of the targeted value of the compressive strength, but then at 365 days, it drops down to 90 % and it continues to get worse. Now, 120 degrees Fahrenheit, that's actually pretty common for outdoor concrete that's placed in the summer. It can get 120 degrees and higher than that. And...
you may get a really good 28 -day strength, but you're going to get very weak permeable concrete. What this also shows, and just how permanent this damage is in the first 28 days, is they took every one of these samples after the 28 days and put them in an environment where the relative humidity remained at 100 % and its temperature was 73 degrees.
Robert Higgins (12:16.768)
and it still had permanent damage to the overall strength of the concrete after one year.
Seth (12:23.33)
These are average temperatures of curing for 28 days. So average temperature of the concrete, right?
Robert Higgins (12:29.952)
Yes, concrete surface temperature, yes. Yeah, it could be overall, I'm not sure, because they're a little vague on what the modeling was, but I would imagine they probably put these in a temperature controlled environment where it got this temperature all through the concrete. So that would be my guess. But they haven't been real. I don't want to speculate and say that's what they did, but...
Seth (12:33.534)
surface temperature.
Robert Higgins (13:00.32)
That would be my guess.
Seth (13:03.678)
this wouldn't tell you what the temperature is inside, I mean at a depth of the concrete, say the middle of whatever thickness of the concrete it is, this is the surface.
Robert Higgins (13:16.704)
Yeah, and if it's six inch concrete, I'd be really surprised I've ever got that temperature because the moisture content alone would cool it enough to where it, I don't know if it would could even get to that temperature. But they didn't do any probes in the middle of the concrete because back then they didn't have the technology to do so.
Seth (13:21.692)
Yeah.
Seth (13:28.862)
Yeah. Yeah.
Seth (13:37.118)
Yeah, we have that now. I'd be interested to see what that looks like now.
Robert Higgins (13:41.44)
it'd be really interesting, yes.
Seth (13:45.31)
Because we do that when we do the maturity curves. We plot the temperature and the compressive strength of the concrete to predict where it's going to be before we pull post -tensioning cables. And that is the technology we use for that. So I would think.
Robert Higgins (14:07.2)
Yes.
Seth (14:14.942)
If somebody's got this, I don't think someone's done a year's worth of measurement, but it'd be interesting to see.
Robert Higgins (14:26.4)
But that's a good point, Seth, because they keep cutting it off at 28 days. Some of the longer tests I've seen are better at 56 days, and they actually show a downward curve, but they kind of dismiss it, which really irritates me because most of the studies I've read where they'll come to a conclusion, but the conclusion isn't really a conclusion. It's speculation. They'll speculate something, but then they leave it dangling, and it's an open.
Seth (14:31.014)
Yep.
Robert Higgins (14:55.296)
It's an open -ended conclusion that nobody ever gets around to verifying. And that just drives me crazy. And it's consistent. But it's a good way to keep yourself busy.
Seth (15:07.71)
Yeah, but the 20, the 28 day and the 56 day, I assume is a lab cured specimen. So it's in the lab because that's what happens on a job. They take, they take the cylinders. and then they might sit out for their spell only sit out till you're allowed to move them. Then they go back to the lab. And so they'll be in an ideal environment. And then they.
Robert Higgins (15:16.2)
Yes.
Seth (15:36.99)
they break them. I'm saying that we need this data based on something out in the field, something that's built. But you would think if it's a building, if it's a building, then it's then it's going to be conditioned space. So that I would think logically that would help the concrete. So it should perform better.
Robert Higgins (15:46.368)
you're preaching to the choir here. My big...
Seth (16:05.726)
I just understand what the purpose of this is. They're measuring the surface of the concrete. And the higher the temperature, the more detrimental the strength of the concrete is, is what the point of this graph is, with the ideal temperature being 73 degrees.
Robert Higgins (16:22.432)
for reference.
Seth (16:29.406)
But what I'm saying is I would like to see what the temperature is in the middle of that concrete specimen and graphed out the same way. Because there's not concrete that lasts or is at 120 degrees for 28 days is what I'm getting at. All right, next one.
Robert Higgins (16:49.568)
Yeah.
Robert Higgins (16:55.328)
Now, here's where the CKD really rears its ugly head and how it affects the curing of the concrete and why we're seeing that porous permeable surface. They keep showing, the graphic on the right -hand side is fairly typical from what I've seen with these field studies where they put in thermal couples along with an embedded humidity measurement.
and are shown consistently that within the top 1 inch of the concrete, the concrete will self -desiccate within 2 to 3 weeks after placement.
When I first saw that, that shocked me to no end. Because I was under the assumption, as everybody else is, that the moisture content of the concrete is fairly consistent and it remains above 80 % because 80 % will form cement. Once relative humidity drops below 80%, cement formation will not occur. It will just stop. Now that explains the weak porous surface. Now,
But they're not tying that in with the alkalinity, which is really unfortunate. And I don't know why, but they're not. So if you look at these three glasses on the left -hand side, if it's pure water, almost irrespective of how little moisture there is in an area, it will reach a relative humidity of 100%. So that glass, if it only had a teaspoon of water in it, would still be at 100%. Now,
Here's what happens when you have alkalinity. The sodium hydroxide is the most persistent and most voluminous alkaline material in concrete for a variety of reasons that haven't been really explained very well. But as the cement formation occurs, there's less water because the cement production uptakes the water.
Robert Higgins (18:55.604)
As it uptakes the water, there's less water and it begins to concentrate the alkalinity. And when the alkalinity concentrates, it reduces, it has a sharp reduction of relative humidity available in the concrete surface. So as you're seeing here, 20%, wow, that's 78%. Well, that means cement formation will not occur. It's exactly what that means.
And I've had some people tell me, well, it won't concentrate that much. I said, then explain the field studies that show the top inch of the concrete within two to three weeks of placement, the relative humidity in the top inch of the concrete can fall between 50 % and 60%. That actually brings it closer to a more concentrated solution of 30%, which will produce.
a relative humidity of 63%. That's very, very alkaline. Now, it doesn't matter how much water is there, because what alkalinity does and heat does is it renders the cement particle incapable of taking on sufficient amount of water to hydrate it. So that explains the damage that you're seeing in its lifetime, because now that that's...
that's been inhibited, that reduction in cement production causes permanent damage to the surface. So that's why we're seeing the lower strengths. That can be compensated for as long as we understand it and we start dealing with it, but it is not being compensated for because this information's being ignored. Let's go to the next slide.
Robert Higgins (20:45.92)
On the right side is a typical compression strength test. Now the compression strength test is problematic in many ways. It's been accepted in the industry for a long time, but there are a lot of flaws in this. One of the flaws is it does not take into consideration that the concrete surface is weaker and may crush a little bit because this...
This method isn't absolute. It pushes down the concrete and when it breaks, that's when it fails. It doesn't take into consideration that it may actually compress a little bit. It doesn't matter. That doesn't register as a failure. What registers as a failure is when it breaks. And that's a problem with that. Now, the other problem is I've seen other studies where they'll do compression value tests on different thicknesses of concrete and that affects...
the compression strength values. Well, it should not do that. If concrete is consistent and this is truly compressive value, the thickness of the sample should not make any difference. The flexural strength should suffer, but not the compressive strength. So there's these information gaps that are adding to the complex puzzle that we're seeing in the field. Now,
This ties in very well with the graphic on the left hand side here, which is done by Drs. Dan Zollinger on 4000 PSI concrete. Now, when they did the break, it broke at 4000, both of them did. However, when he sliced the surface off, the no curing was considerably weaker. It was 30 % weaker than the remainder of the concrete. Instead of being 4000 PSI, it was 2800. That was the top inch.
which again corroborates what we're seeing in the field with those field studies that are completely unrelated to this one and it's around the globe. Over in Portugal and the Middle East, they're showing this. Now the seven day water cure, this is what's really dramatic. So even with the seven day water cure, when they sliced off the top inch of the concrete, it was a full 20 % weaker and compressive value than the remainder of the concrete. That means the cement formation is being inhibited.
Robert Higgins (23:06.368)
even in a very well controlled environment. So in an uncontrolled environment in the field, we're going to see some pretty dramatic differences. Now, if we want sustainable green concrete, this is our re -clink. If we take care of this, concrete will be very sustainable and considered very green because if we did something, for example, let's take one L cement that's got this big push.
Well, it's a big push for the greening because it can reduce CO2 emissions by up to 8 to 12 percent. But if we took care of this curing issue that we have, we can more than double the durability of concrete, probably triple or even quadruple the durability of concrete. The other methods that they're experimenting with right now don't even come close. We have the technologies staring us right in the face, but we're not dealing with it. So let's go to the next slide.
Robert Higgins (24:08.544)
And these are two other different studies. The first one corroborates what we saw with the compressive value you saw with the Dan Zollinger study. This is Texas A that was done in conjunction with Texas Transportation Institute. And if you look, the RH value as you go towards the surface is very, very low.
Again, if it drops below 80 percent, cement formation will not occur. Look at the concrete surface. I mean, it's terrible.
Because look, it follows the ambient curve, which the center of the concrete doesn't really follow the ambient curve. Now here's the other one where they have what's called a super absorbent polymer, which adds moisture to the concrete as the cement forms. And it compensates for the water loss. And you can see what happens. The relative humidity in the top surface of the concrete remains well above 85%.
so you get full development of cement and look at the difference.
It's dramatic.
Robert Higgins (25:29.376)
And this also follows the same pattern we're seeing in the field, where after 20 days, the relative humidity is down below 60 % in the top surface of the concrete.
Seth (25:41.244)
What's the, so this graph on the right hand side, this, what was the, it says without SAP and spherical SAP. What is that again? Say that again.
Robert Higgins (25:55.176)
Okay, that's a super absorbent polymer that what they've tried to do is add these little resin balls in there that contain water. So as cement forms, these little resin balls have a reservoir of moisture that adds moisture to the concrete as the cement develops. So you're not lowering the moisture content. The moisture content stays fairly constant.
Seth (26:04.028)
-huh.
Seth (26:20.382)
Right. Do you know where the measurement for relative humidity was on the, is it the same as what they did on the left hand graph? Did they go, is this one inch?
Robert Higgins (26:30.944)
Yeah, it's not very well done, but apparently this is the first inch of the concrete. And it's showing the difference where it goes from above 90%, but even after three weeks time, it's still above 85%. And that's what you want to form cement. But without it, look what happens. You get that rapid decline and the concrete self -desiccates.
Seth (26:34.204)
-huh.
Seth (26:48.446)
Right.
Robert Higgins (26:58.816)
And that's the biggest problem we're having is the top one inch of the concrete self -desiccates. And that's what receives all the weathering, the wear and tear. So why aren't we protecting, you know, it's like sending somebody out without armor. If you're going to send somebody out without armor, they're going to get stabbed and they're going to die. If you give them armor, they're not going to. You know, I don't know why we're not doing this. The technology is all over the place.
And we can really, we can more than double the durability of concrete virtually overnight if we just start accepting the carrying practices. Because the two tenets of durable concrete is water -cement ratio and carrying. If you, if they're both done ideally, you get really durable concrete. And we're not doing that. We're still following 100 -year -old technology of concrete that doesn't exist any longer.
Robert Higgins (28:03.104)
Now here's a good example what happens when it self -desiccates but if you get a good finisher everything went fine. We were on this large project and they wanted to do a calcium chloride test so they went ahead and ground the surface as soon as they saw this they stopped. So what they wanted to do is grind some more of the concrete to find out if this was a consistent pattern and this pattern continued through over 700 ,000 square feet of concrete.
Seth (28:34.494)
how far did they grind down?
Robert Higgins (28:37.76)
This was about 90 and a 32nd of an inch.
Seth (28:45.63)
It had these cracks that are in a, you said an 18 inch by 18 inch grid pattern throughout the slab.
Robert Higgins (28:51.424)
Yeah, I believe there's a reflection of the steel reinforcement. But it shows you how dehydrated the concrete is, and it has no resiliency. Hold on for just a moment.
Seth (28:58.462)
Right.
Robert Higgins (29:17.216)
My wife is, our granddaughter is getting married and she's getting excited while they talk about things. So I had to quiet her down.
Seth (29:22.832)
Well, congratulations. That's awesome.
yeah. So that you said just the 32nd that it was, and this appeared.
Robert Higgins (29:32.224)
I mean they barely, they ground it enough to where they could get down to the concrete past the curing compound. You can see where the paint was removed and there was curing compound on there. Since it took the curing compound off, there's what we ended up with.
Seth (29:49.63)
And they were doing this to test what again?
Robert Higgins (29:52.8)
They're doing a moisture test because they're going to put a floor down. So they're going to do a calcium chloride test and this is what they discovered. So then they found out they had some concrete issues that had to be taken care of before they could consider putting down a floor.
Seth (29:56.998)
Okay.
Seth (30:08.094)
Right.
Robert Higgins (30:10.992)
Surprise!
Seth (30:11.838)
So they were doing the moisture testing because the flooring required that before you put it down.
Robert Higgins (30:16.8)
Correct. Correct.
So basically Seth, we have in our possession the ability to deal with a problem that we know is happening but the researchers are not covering it. I want to know why this is not being covered. I keep asking questions and all I get are crickets.
Seth (30:41.438)
Well, if there's no problems then what are we, there's nothing for these people to do. And there's no way for them to make money.
Robert Higgins (30:52.392)
Unfortunately, you're right. In fact, one of the running jokes I have, because I watched that movie called Men in Black. And so I nicknamed them Bugs. Because when Tommy Lee Jones was measuring this, it's, my god, we got a bug. We got a bug. And then Will said, why is that bad? He said, bugs thrive on carnage. So.
Seth (31:20.476)
Yeah.
Robert Higgins (31:21.136)
So these so we have these Cottage industries where they these inspectors come in the attorneys come in moisture These moisture mitigation products come in at least 90 % of the time those aren't needed Because again, they're using bad data to confirm an issue that isn't what they think it is
So even in the flooring industry, they are basically, they're upwards a little over three billion a year now dealing with moisture failures. Well, that should be almost zero. There's no reason to have those. And there's no reason to have concrete that isn't durable. There's no reason we can't put in concrete that we don't have to touch.
with any form of maintenance really for about 50 years. Because I was reading this study the other day, because I was trying to think, where's the origination of this? Because when you look at chloride penetration in the concrete and how detrimental it is, and they were showing how the calcium hydroxide will bond with the chloride and it helps discourage the penetration, I thought, that just doesn't sound right, because why are we having so much damage then?
on seacoast structures when you look at surfside and things like that. Well, unfortunately, I found one of the keys of all things through veterinary science. Because in veterinary science, they were exploring the use of calcium hydroxide as a disinfectant in their facilities. But they found there was a minimal use for it, or it was limited use, I should say, because it wasn't very soluble.
But they found if they added 1 % to 3 % sodium chloride and water solution to the calcium hydroxide, it more than doubled its solubility. I thought, my gosh, they figured it out. So just a slight penetration of sodium chloride into concrete will increase the solubility, and that will actually draw it in.
Robert Higgins (33:33.344)
But as it keeps getting more and more concentrated, it starts to become blocking. But now you've got this trailing, you got this front edge that's going into towards the reinforcing steel that's basically pulling the rest of it with it. And as it keeps diluting, as long as it stays diluted, keeps pulling, it keeps it soluble. So that mechanism has not been recognized because unfortunately, most researchers look at, look at,
chemical reactions as being a linear event. That almost never happens. Sodium hydroxide that we're talking about, the alkalinity, is a perfect example of it. Because if you take sodium hydroxide, when they're producing it and they're shipping it and everything else, they actually have to keep it in heated tanks. Reason being is they keep it at 40 % solution. Now I'm gonna digress a little bit.
If you take sodium hydroxide, and this was in the NIST study, 1999 state -of -the -art report on concrete, it showed, well, it says that sodium hydroxide acts as an annual freeze. Well, that's accurate only within a really narrow range, and again, they're using truncated data. So what happens when you have it at 20 % concentration, it will reduce the freeze point of water down to negative 20 degrees. But if you increase...
which we saw in that, how it reduces the relative humidity. But if it increases, say 40%, the 40 % solution will increase the freeze point of water up to 59 degrees. Now if it gets to 60%, the freeze point of water is now 125 degrees. The water behaves in a completely different fashion and that is not being addressed.
It's being addressed as being a, okay, this is what it does, this is what it does, this is what it does. It does not do that. They are ignoring what the dynamics of the field go into. Now, the reason why they don't deal with that, because in a lab that doesn't happen. Because it's a controlled environment, stays in a controlled situation with a relative humidity and the temperature is the same all the way around. So all these dynamics are taken away.
Robert Higgins (35:54.208)
By taking away those dynamics, you're getting false ratings.
Robert Higgins (36:01.568)
crazy isn't it?
Seth (36:02.75)
It is crazy. So just to sum this up, so the alkalinity that we're seeing is coming from the cement making process with this cement kiln dust that the EPA basically mandated on the industry. And then also from the aggregate, because we're using different aggregate than we had in the past. And this aggregate has.
It contributes to the alkalinity as well. Is that right?
Robert Higgins (36:37.824)
That's correct, and I'm gonna take it one step further. The cement industry is not required to divulge what they use in their cement mix. The ready mix producers have to, but that's another missing information gap right there. They're also using these grinding aids in cement. Now, one of the things that bothers me about that,
If you look at some things such as ethanol, for example, and these amines that they use and these glycols, those also affect the solubility of the components of cement. But they're not dealing with that either. So that's being incorporated into the cement and into the concrete. But we don't know what that's doing. So in the concrete compressive value, it doesn't change anything.
But what it changes is the dynamics of the chemistry in the concrete. And we're not dealing with that. However, if we cure the concrete properly, none of that makes any difference because it can't migrate up or down. Because if you discontinue a capillary pore structure, all that other stuff is irrelevant. Even the alkaline is irrelevant.
Robert Higgins (37:55.744)
That's really all we have to do. Cure the concrete properly. We need to upgrade our specifications for that and we will get really durable concrete and this green and all this other requirements, we're right there. Concrete becomes its own sustainable, its own green. There's really nothing else needs to be done.
Seth (38:16.67)
Can you test the alkalinity of concrete before, like when you bring it in on a ready -mix truck and you just dump it in a wheelbarrow just like we're going to do our cylinder, testing cylinders? Is there a way to test the alkalinity of that concrete in that wheelbarrow?
Robert Higgins (38:43.706)
Not a present, no. You can test the pH but not the alkalinity. And that's the other, that's just another layer of complexity is a lot of people confuse alkalinity with high pH. They're not the same thing. High alkaline, high pH means something totally different.
Seth (38:59.838)
Mm -hmm. Right.
Seth (39:04.67)
Can you quickly discern the two?
Robert Higgins (39:09.152)
Yeah, a high pH is the strength of a solution. Alkalinity is its concentration. So it's kind of like what pool, spa, and agriculture, and people that tend aquariums, they deal with that. But they call it hard water and pH, just to get a differentiation so people don't get confused. The hard water is actually the alkalinity, and the pH is the strength of the solution. So the alkalinity buffers it, keeps it from changing dramatically.
But sodium hydroxide, fortunately and unfortunately, is one of the most well -buffered alkaline salts that exists. So it doesn't want to change.
Seth (39:57.054)
So maybe we need an alkalinity test to reject lobes.
Robert Higgins (40:03.088)
I did one, I call it a relative alkalinity test on a project where they used a sodium silicate admixture and they were having problems with the concrete. And because my issue with sodium silicate admixtures is... Well anyway, I said, huh? yeah, you betcha. So anyway, I said, the floor is, you know, it doesn't...
Seth (40:22.078)
another episode. That'll be another episode.
Robert Higgins (40:32.626)
dispersed very well. In fact, it's kind of like an anti -dispersant. So we're going to have areas where the floor is going to be more damaged than others, and that's what happened. So I had the testing lab take samples of the highly damaged area, moderately damaged, and undamaged area. And I did what I called a relative alkalinity test. I had them take an area where they, on the surface of each area,
they put some plumbers putty down and put in a half milliliter of water and they'd run a pH test. So, and they would mark the pH test. So then I'd have them add another half milliliter of water and run another pH test. Until it dropped to a pH of nine, that means it's an elevated alkalinity because the really stable carbonated concrete has a pH of around nine.
So the more alkaline it is, the more water you have to keep adding to drop the pH. So the areas that were highly damaged, it took between eight to 12 additions of water to finally bring the pH down to nine. So it was pretty effective. So there's probably a range in there. And researchers, pay attention, that we could probably do this and get a relative alkalinity.
indicator of what the concrete what the condition of the concrete is at the site but as far as in a wet mix I don't know I don't know I don't know how to do that
Seth (42:06.462)
Sounds like good project for Dr. Belkowitz. Before we go, Robert, I appreciate you coming on the show. Do you want to plug your upcoming trip to Australia or?
Robert Higgins (42:20.512)
Okay, yeah, we're all be speaking at up in Brisbane. They're gonna have a couple workshops the epoxy manufacturers have a gathering up there and the Restoration International it's gonna have a Restoration industry Association gonna have a couple workshops up there and we're gonna kind of combine them
We're going to be doing two workshops up in Brisbane. And then we're going to go down to Melbourne. And June 4th and 5th, I'll be speaking at the National Convention there. That's an Australian -Asian combination convention. And we'll be discussing a lot of what we're talking about today on your podcast about the challenges of alkalinity and what they have to do to start addressing it. Because it is not being addressed.
And what's funny is the restorer said, yeah, we'll dry it to a certain point in the concrete rebounds. I said, yeah, that's because you overdried the alkalinity. Then once you pull away the dehumidifiers, it bounces back up to where it's supposed to be. So what do you mean where it's supposed to be? I said, unfortunately, there's this, I'm not going to get into it, this is called concrete hysteresis, but concrete, every piece of concrete will have its own dry level.
You've got to treat every piece of concrete like a different species of wood. It'll have its own dry level. So if you can over dry it and see what the bounce back is, now you know what's dry level is. That's what's dry for that piece of concrete. This one may be up here, this one may be up here, another one may be way down there. But that's its dry condition, depending on the stockl and condition.
Yeah, it's pretty crazy. But now that we've been doing that with the restoration contractors, they said a lot of the things they're doing now make sense. So effects have a tendency to do that. And I love hearing that where it said, now it makes sense. Now we're figuring it out. And then when they do the repairs, they said, yeah, the repairs are working. I said, yeah, because that is dry for that concrete.
Robert Higgins (44:34.784)
Just make sure that there's no salt on the surface. That's your biggest concern. Because with concrete, we're always taught about dew point, dew point, dew point. Well, it's fine. But there's two types of dew points in concrete. There's atmospheric dew point, where it gets to 100 % relative humidity and it condenses. There's ionic dew point, where you have these different kinds of salts in concrete, where it can condense water at a much lower relative humidity. So they have to pay attention to these things.
And that's where they hit their bounce point, where they dry it down and it bounces back up because that's the ionic dew point of whatever that salt is. It's pretty crazy.
Seth (45:14.11)
All right, well, I think this is good spot to end the day. Robert, thank you for coming back on the show. I will put all the contact information so you all know how to get a hold of Robert, maybe get him to come and talk to you. So Robert, thanks for coming on the show and everybody until next time, let's keep it concrete.
Robert Higgins (45:18.72)
you
Robert Higgins (45:37.64)
All right.
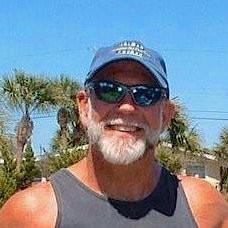
Robert Higgins
Involved with waterproofing and restoration of buildings and specialized in concrete. Have been involved with several committees with professional groups such as ICRI (first chair for moisture testing), CSI, speaking at national and regional conferences, authored the Flooring industry “White Paper” for the WFCA (World Floor Covering Association), moisture test instructor for the Academy of Textiles and Flooring, guest instructor for ICRI. Authored many articles regarding weather and environmental durability of concrete in multiple publications. Currently involved with IICRC Committee S230 and NFCA (National Floor Covering Association) “best practices” for moisture testing concrete prior to installation of Floor Materials.