EP #075: How to Unlearn Everything You Know About Moisture in Concrete
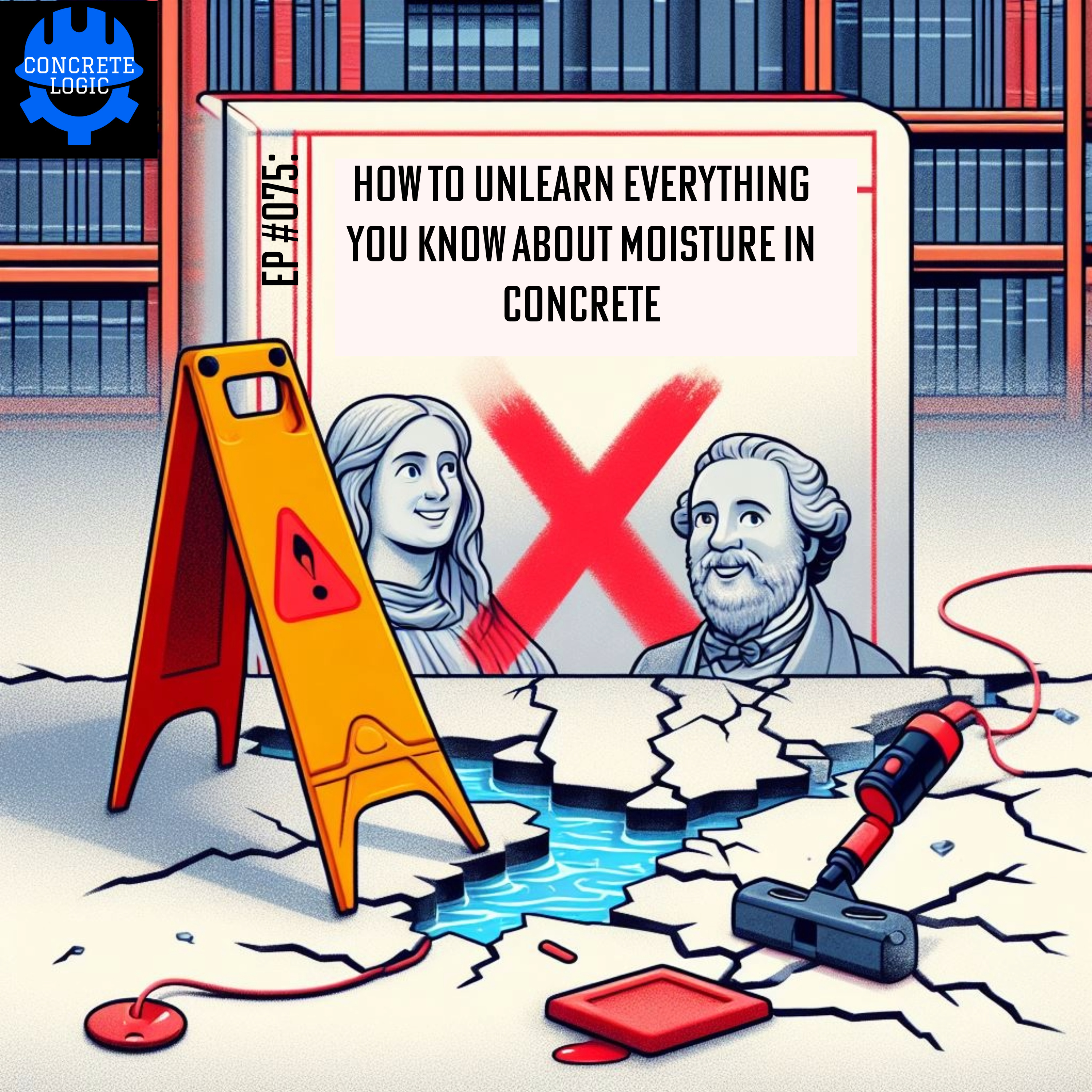
Summary
In this episode, Seth interviews Robert Higgins, a flooring concrete consultant specialist, about the issue of moisture in old concrete. Robert explains that moisture in older concrete is caused by a condition called ionic dew point, where particles migrate to the surface due to diffusion, not moisture migration.
He emphasizes the importance of addressing older concrete differently and recommends grinding off the surface to remove accumulated salts. Robert also discusses the acclimation of adhesive and flooring products to prevent moisture accumulation. He highlights the need for proper testing and understanding of environmental conditions to avoid moisture issues.
Takeaways
- Moisture in older concrete is caused by ionic dew point, where particles migrate to the surface due to diffusion, not moisture migration.
- Grinding off the surface of older concrete can remove accumulated salts and prevent moisture issues.
- Adhesive and flooring products should be acclimated to the same temperature as the concrete to avoid moisture accumulation.
- Proper testing and understanding of environmental conditions are crucial to prevent moisture issues in flooring installations.
Chapters
00:00 Introduction
02:28 Issue with Old Concrete and Moisture
13:59 Moisture Accumulation and Adhesive Acclimation
20:34 Addressing Moisture in Operating Warehouses
26:00 Permanent Solutions and Avoiding Blame
29:33 Cement Grinding Aids and Chemical Migration
32:40 Conclusion
***
Did you learn something from this episode? If so, please consider donating to the show to help us continue to provide high-quality content for the concrete industry.
Donate here: https://www.concretelogicpodcast.com/support/ *** Episode References
Guest: Robert Higgins | RC Consulting | rcconsulting.higgins@gmail.com
Guest Website: linkedin.com/in/robert-higgins-b8294411
Producers: Jodi Tandett, Jace Stocker
Donate & Become a Producer: https://www.concretelogicpodcast.com/support/
Music: Mike Dunton | https://www.mikeduntonmusic.com | mikeduntonmusic@gmail.com | Instagram @Mike_Dunton
Host: Seth Tandett, seth@concretelogicpodcast.com
Host LinkedIn: https://www.linkedin.com/in/seth-tandett/
Website: https://www.concretelogicpodcast.com/
LinkedIn: https://www.linkedin.com/company/concrete-logic-podcast
[00:00:00] Seth: And welcome to another episode of the concrete logic podcast. And today I got one of my favorite guests returning. Robert Higgins is back on the show. He is the flooring concrete consultant specialist. I don't know how else to explain what Robert does. He's like a mad scientist, the mad chemist of concrete.
But anyways so just to remind folks how this works, the podcast if you get some kind of value out of our discussion today with Robert, I ask you to do one of three things, or you could do all three things, Actually, you should do all three things. The first thing you could do is share this podcast with a colleague.
If you get some value, you learn something what Robert's sharing today, and I guarantee today you'll learn something from Robert. You should share the podcast with somebody. The second thing is you go to the concretelogicpodcast.com website. And if you go to the homepage and look at the bottom right hand side of the homepage, there's a little microphone there.
You can hit that microphone and you can leave me a message and you can either give me a topic or a guest suggestion or just give me feedback on what you think about the podcast. That is very helpful. And then the last thing you can do. Is back at the homepage up upper right hand corner of the homepage.
There's a donate button. Click on that donate button and you can give the podcast any amount you want, and any amount is appreciated. So don't worry about what you send in, whatever you think, what the value of what you learned from this podcast is just. Just put it in there and then you get listed as a producer for the next episode that's released.
So your name's attached to the next new episode, which I think is pretty cool. And you can put it on LinkedIn and tell everybody you're a producer of the Concrete Logic podcast and I'll back you up.
Robert, let's talk about old concrete and there seems to be an issue with old concrete and with., We're gonna solve that mystery today.
So you want to get us started?
[00:02:22] Robert Higgins: Okay, you got it. It's really interesting because it's almost a year ago today where I was invited to go speak in front of these this installation group over in San Leandro. And we went through the normal education presentation where I presented and then the concrete side of things.
And then they came in and learned how to do moisture testing. But in the, Question and answer session. That's when things got really interesting because one of the installers, you could really sense the frustration because everybody's head was nodding. Yeah. When he's asking this question, he said, why is it.
We have so many problems with older concrete that we don't seem to have with newer concrete, even though older concrete, with the methods that we use, appears to be drier. And I said, well, unfortunately, that's to be expected. And it's caused by a condition that we're all missing because we're all taught and I was taught and I had to unlearn because you have to unlearn to learn, especially in this.
In this discipline, moisture migrates from the bottom to the top. The underside of concrete is normally cooler than the top side of the concrete, so moisture does not move from cool to warm, it moves from warm to cool. So What we've been taught violates the second law of thermodynamics. So I dug in and I wanted to find out what caused that and what happens when you have the top layer of concrete that's warmer, especially when it gets older, it starts collecting these little Particles in there, these hygroscopic particles that like water, but it's not doing much in the way of anything except that the warmer temperature makes these things more active, so it moves to where it's more active.
This is my, this is a migration of particles that's caused by diffusion. It's not moisture migration. We need to get that out of our vernacular, because if we keep using moisture migration, we lose the whole concept and the mechanism of what's causing this damage. And I said, oh, sorry, I didn't mean to go out, go to get too technical for you.
He said, no, he goes no, go ahead. I said, so what happens when you, especially this happens mostly when you're moving old flooring, doesn't it? And they lit up. They said, Yeah, that's what happens. I said, well, that's because all this stuff's collected. But once you grind off. Or remove that surface, you, all the salts in there are now exposed to a new moisture source, which is the air.
So, in a way, all these salts, because some of the salts in the concrete have a greater traction for moisture than a calcium chloride test. So, envision it as being a calcium chloride test upside down and inside the concrete. It's pulling moisture from the air. So you're collecting moisture that way.
So how do we get rid of it? The best way I've found is just to grind it off. There's other combinations of methods, but it depends on how old the concrete is, how bad the surface of the concrete is. There's some other things you need to look at, but I'm more than happy to work with you on that. Give me some calls and I've given them some advice.
And they were a little skeptical because it was something that was contrary to almost everything they were taught, but not 3 months later the concrete meter company. Went out to go show them how the concrete meters work. So, they were out in their warehouse, and the warehouse was in excess of 40 years old.
It was 40, 42 years old, somewhere in there. So they took an area of the concrete, because they had a curing compound on it. They, before they took the curing compound off, they're shown, when they were able to do a moisture reading, it was 1. 9%. That's very low. So anyway, they ground off the curing compound, and they did another moisture test.
It was 1. 9%. Remained the same. So they left to go to a different area as they were discussing different aspects, and they came back the same area, not 15 inches later, they put the meter back down, it was 4. 3%. Now, what's so startling about that is that moisture meter averages the first three quarters of an inch.
That is a lot of water that's come into that very top surface to average out at a 4. 3 percent over three quarters inch of the concrete. That's a lot of water that concrete's picked up. They were shocked. And I said, wow, so they called me, and they said, this is exactly what happened. I said, I couldn't have designed it better if I had to show you how to do it.
And unfortunately, they didn't take pictures because they were so startled. Nobody was expecting it to be that dramatic. But that's what they're seeing. And what would have happened, the normal course of business is you'll grind it off, you let it vent. And that's what I was taught as well. You let it vent.
No, it doesn't vent. It absorbs moisture. It's the other way around. It starts picking it up. So what would have been the assumption when you tested the next day? Well, look at the moisture that came from the concrete. No, it did not come from the concrete. It came from the ambient conditions. The ambient conditions are the key portion of all the moisture pickup, virtually every flooring failure I've seen.
Very rarely is it from other sources, and if it is it's in an isolated location. You can really tell the difference because once, when there's an aggregate condition that's coming from the Ambient conditions, but when it's just in spots, well, there's something like a broken pipe there or something else is involved, or you got the watering where the concrete's permeable and it's coming in from the side.
But with the concrete itself, almost all the moisture originates from the ambient conditions. And as I've had the installers start doing time of installation testing, where they start looking at this and this added another element to that, test it before you move, remove the. The last bit of adhesive of the curing compound.
Test it then, and test it immediately after, and test it a half an hour later. If you get a moisture pickup, you know you have a dew point condition. Now, they said, well, it's not atmospheric dew point because it's not a hundred percent relative humidity. I said, therein lies the problem. We're not taught this correctly, and I really have an issue with a lot of these certification bodies because they don't even know to test to teach this.
What you look for with these materials, they're collecting the surface, you have what's called ionic dew point. Their dew point is well below 100 percent relative humidity. It can be 50 percent relative humidity, can be 75%, can be 80%, but it will be lower than 100%. So this will actively pick up moisture and pull it into the concrete surface and it gets saturated.
That's your dew point. That's an ionic dew point. That is not being taught and is, it is the main mechanism for these, for damage, especially in older concrete. So when I've had installers doing this and testing for this, the installers I've worked with, they've stopped having moisture claims. Now, why are we conducting these tests where nothing is getting better?
20 years ago, when they're conducting tests, the calcium chloride tests were wrong, so let's go to relative humidity. That'll improve everything. Because if the testing is so Accurate? Why are we still having problems? Well, the problems since then have tripled. It's now a 3 billion a year issue with florists.
It's tripled. Okay, so I'm going to ask the same question. If RH is so accurate why do the moisture issues triple? Well, people are more aware of it. No, They're not more aware of it. The water doesn't care what we think. What we're losing the foundation and the, and basically the basics of what's going on with the concrete.
If we understood this, and every installer started taking this on, and preferably I'd like to see the inspectors doing this, because it should be, there should be no skin in the game on this thing. I don't think anybody with skin in the game should be doing this, but that's my personal opinion. But I think every installer should do a time of installation testing because you will catch things at the beginning, middle, and even towards the end of the installation.
I did this a few years ago when I was consulting for a large adhesive company. They called me and they had a three story building. And three story building, they did moisture tests and they were puzzled because the on grade slab had the lowest average moisture content. The second story slab has slightly higher, and the third slab has slightly higher.
I said, well, the building isn't conditioned, is it? They said, no. How'd you know that? I said, because when you have that kind of a pattern, it's called the stack effect. As a warm air rises, it holds more moisture and it hits a cold concrete and concrete is more moisture to absorb. Oh, this consultant came in and said we had to put this moisture mitigation system on.
It's going to delay the project by three to four months. It's going to cost almost a million dollars. I said, well, you don't need to do that. The only moisture mitigation you're going to need to do is use floor fans. And use a concrete meter. So how are we going to do that? And I said, well, take your infrared thermometer.
And I gave him this instructions. So they put a line of fans up, they blew it and they let it go for about 45 minutes to put the meter back down. It was low enough to start installing the floor. I said, now you follow. The fans. Push the fans ahead of you, so these are always ahead of you. Keep the air circulation going in the room, not blowing directly on the concrete.
Keep circulation going in the room. And he started following that. 300, 000 square feet. It has now been almost 11 years, and there's been no failures. So they didn't lose the three months and they didn't spend a worthless 900, 000 for a moisture mitigation that would have been a success, because they didn't know any better.
They were curing a problem they didn't really have. And that's the problem we're having with this entire moisture issue with fluoride. We're curing problems we don't really have. They're just environmental issues. If we deal with the environmental issues and you learn the fundamentals, and the installer learns how to test, which is really easy, because you get instant reaction, instant results and instant reactions you can catch anything you want to catch.
So that's why the handful of installers I work with, they're not having issues. So this one installer is in Florida, they have six offices. They had monthly issues. They only have one a year now. There's the goal. Yeah. Well, that's why we have to. Older concrete differently because we're dealing with a different animal.
Concrete changes with age because there's even this big thing to do with what's called hysteresis, which I'm not going to go into, but they have determined that concrete as it ages. We'll take on different characteristics, and they said it is not applicable for other areas of concrete in a different environment.
It's the history of that concrete that dictates what is going to happen to it. So we have to basically compartmentalize where we take each condition, each site condition, as it sits as a unique issue. When we do that, we can start picking this up, then we stop making assumptions.
[00:14:03] Seth: Yeah, because that issue with the concrete that you're explaining and how moisture accumulates on the surface based on the environment is not it doesn't apply just to concrete.
Right? So you got to look at also acclimating flooring adhesive and whatever floor you're putting on or whatever product you're putting on. Right?
[00:14:25] Robert Higgins: I'm so glad you did that because most floors are not acclimated correctly. They'll bring them in and say, oh, yeah, we left it in there for 24 hours.
The hard goods, the dry goods may have acclimated, but your wet goods may not have. There's very few things you could do to sabotage your job worse than a warmer concrete with a cold adhesive and warm air. Because now you're attracting moisture from the warm air and from the warm concrete, you're sandwiching this otherwise good adhesive with bond breakers on both sides.
By attracting water to it. So the acclimation is really important and you can actually create your own moisture issue just by having the adhesive that's too cold.
[00:15:06] Seth: What's the proper practice for that? you were explaining how the fellow was moving fans around with the concrete.
We understand what we need to do for the surface of the concrete. Make sure it's in a proper condition before we put on whatever we're putting on adhesive or, polishing or whatever product that we're putting, I guess I would apply to like an epoxy and things like that. We know how to treat the concrete, the old concrete.
What should we be doing with the adhesive and the flooring products as well?
[00:15:37] Robert Higgins: The adhesive and flooring has to be brought in and it needs to be acclimated. You can take something as simple as an infrared thermometer and test the flooring material and test the adhesive. If it's too cold, don't install it.
Now, there are ways to monitor this. So make sure that, where somebody's in a hurry, I'm making a presentation to some of these manufacturers where they actually have these devices that you can put on the adhesive that can show. What the progression was, and the temperature and humidity it was exposed to, when you bring it in, it will actually sound an alarm if they try to install the adhesive before it's ready.
Because a lot of times they're introducing their own issues into the environment, and everybody's saying, where'd this moisture come from? Because it's not an issue now, and well, it must be a defective adhesive. You can't recreate what you did. It's not possible. So, if we do this on the front end and these devices, they actually they're 5G, and they can go Bluetooth and all that, so at the job site and even remotely, they can keep track of this to make sure that they're not installing a product that's out of spec for the conditions.
[00:16:50] Seth: It is simple
[00:16:50] Robert Higgins: technology. We're just not using it.
[00:16:52] Seth: So do you want the, the same temperature as the ambient temperature where you're applying it to avoid the moisture from accumulating?
[00:17:02] Robert Higgins: Yeah. Cause you want it to be at least as warm as a concrete.
Okay. Or slightly warmer because again, remember mantra moisture moves from warm to cool. If you're not creating a cooler surface, you're not going to be attracting water.
[00:17:17] Seth: But if it's warmer than the concrete, would there be water accumulating between the adhesive and the concrete?
Pulling out of the adhesive?
[00:17:28] Robert Higgins: And act because no, actually be pushing it because sometimes when you're going to for sometimes when you're going on a, like a really warm surface or something, you can get gas bubbles and all that, because again, you're putting a colder material onto a hot surface.
What you don't ever want to do is put something cold on a hot surface or warmer surface. What you want to do is you want to have it at least. Within a couple of degrees of each other, not enough to really attract moisture, if anything, you want the same temperature, possibly slightly warmer, even the ambient conditions of the room.
And that's the problem is the larger the adhesive container, the longer it takes to warm it up because water is a very poor conductor of heat. But the upside is once you warm it up, it takes just as long to cool it back down. So what you want to do is you want to get in there as early as possible.
Adhesive should be the first thing to arrive at the job site and keep it warm. Get it to get it acclimated, get it warm, bring in your dry goods. Cause dry goods, a lot of times those will be conditioned very quickly. Generally within the first day, but what you want to do is you want to make sure and take a snapshot, take your infrared thermometer and make sure that you take a temp, a temperature reading of the concrete, take a temperature reading of the room, take a temperature reading of your dry goods and your adhesive, you all, you want all of those to be as close in in temperature as possible and nobody's doing it.
[00:18:58] Seth: The warehouse example that you gave, were they putting down flooring on top of old concrete? And what were they doing?
[00:19:09] Robert Higgins: Oh, they were just, they were actually this reason why they didn't take any pictures, darn it. Cause they were just showing how to use a moisture meter. They weren't planning on putting up down a floor material, but if they had been screwed because they would have done what everybody else did because they would not have tested afterwards.
They would have ground the concrete. Let it sit for 24 hours and then test. You would have had a false baseline. It would have picked up all that moisture and you would have believed, and everybody in that project would have believed, this moisture is originating from the concrete, not originating from the air, because it can't pick up that much moisture from the air.
Yes, it can. Yeah.
[00:19:46] Seth: If they were they were just taking off the curing compound in that example and then moisture was accumulating on it, other than just, I think you explain the solution to this, like in a warehouse, an operating warehouse, you don't want moisture accumulate on the floor.
It's a safety hazard. That's bad for machines and everything else. So you want to address the moisture, even if you're not going to put anything on top of it. So to fix that problem, you were saying you just Keep on polishing or grinding down.
[00:20:24] Robert Higgins: Yeah, because most of the salt will click at the very top surface of the concrete.
Very rarely have I ever seen where you've got warehouse grade concrete is pretty dense, where if you grind down more than 16th of an inch, you get any more benefit. So normally about a sixteenth of an inch is enough to take off all the accumulated salts that would cause that kind of a problem.
[00:20:45] Seth: Okay. Is that, part of a maintenance plan too?
[00:20:49] Robert Higgins: I don't know. I haven't really looked into that very much. Yeah. Cause, cause a polished surface will do that even if you don't have salt accumulation.
[00:20:59] Seth: Moisture will accumulate on the polished surface.
[00:21:02] Robert Higgins: Yeah, it can, but that's called slab sweating syndrome or sweating slab syndrome, whichever way you would put it. That's really well established. Now, if you want to see good examples of that if you look online and some of the NBA games, they've actually had to cancel basketball games because what they'll do is they'll open up a facility and the air is too warm.
And so what happens is the playing surface is too cool, so when these people walk in and they're breathing, they're adding moisture to the environment and all of a sudden, the courts start getting slippery and the basketball players are slipping. And no matter how many times they try to dry it off, they mop it and put air blowers on it.
As soon as they stop, it gets water on it again because that's dew point. Now that actively happens every time you have a colder surface. So whether it's a parquet floor or a concrete, now the concrete will absorb it, so it's harder to get rid of later on. Because one of the other mechanisms people don't look at is when water's coming off the concrete, it's evaporating.
Right at the line of evaporation, that's the coolest portion. Of the equation. It's called evaporative cooling effect. That's why we put fans on it, because when you put fans on it, you can remove that. I call it basically air scrubbing because you keep the cooling down where you actually eliminate by put blowing air on it.
That's why you can that's why if you go out on a construction site and there's puddles after rain, if you, anywhere you look when there's active wind, let's say it's funneling through between buildings. Well, that dries out right away. Whereas the other areas where there's dead air the ponds and puddles can sit there for hours, maybe even days.
Yeah, it's just fundamentals that we're not paying attention to.
[00:22:50] Seth: When you blow the fan across the surface are you equalizing the temperature between the concrete or whatever flooring material it is. That temperature and the air immediately above that surface, you're basically equalizing that temperature, right?
[00:23:08] Robert Higgins: Well, basically you're just keeping it from cooling down. And if it cools down, it doesn't want to let go of the water. So basically, you're, you've got this greedy thing trying to cling on to the water. So what you're doing is you're pulling it, you're pulling the candy out of its hands. And that's basically it just what you want to do is you just want to remove it as quickly as efficiently as possible, and a high volume of air doesn't do it.
There's really no benefit to it. All you need is air movement. I found that just a traditional floor fans were just fine. You don't need a high powered fan. Interesting. I know. So I tell people you want your best moisture mitigation or floor fans.
Don't invest in shot blasting and putting down an epoxy. Invest in floor fans. A lot cheaper. Yeah. Look at the job site. They saved over a million dollars on that job site.
Over and over again.
[00:24:10] Seth: And eventually, whatever they shot blast, and apply to that surface, it's going to fail, right? Because you're not addressing the issue.
[00:24:16] Robert Higgins: Yeah, because it's not, nothing is a permanent fix, whether it's underneath the concrete or on top of the concrete. As long as it's an organic material, it is not permanent. It will wear out. That's just how it is. So basically, we're playing kick the can. Okay, we’ll let it be somebody else's problem later on.
We gotta stop doing that. Take care of the issue, take care of it permanently, and let's go on.
[00:24:45] Seth: Do you know how long it takes for the salts to accumulate and increase the chances of having this moisture issue on the surface of the concrete?
[00:24:53] Robert Higgins: Nobody's ever done a study on it, unfortunately, but I have noticed that it, concrete generally needs to be at least 10 years old before that becomes an issue, but depends on the water cement ratio of the concrete, how it was finished the time of year it was placed.
If it was placed in the summer, it's probably going to be worse. Because as you heat concrete also tends to undermine cement development. I know people love it because for job sites it means the concrete will harden faster so we can get on it faster. The faster you get on concrete in elevated temperatures, the worse it's going to be down the line.
That's a given. There's information from the 1950s all the way through today that show that as you heat concrete, you basically retard its ability to develop cement and that that. Retardation is permanent because they showed that in that study where they were, I have this graphic, and I wish I had it on here.
There was this graphic where they're showing 55 degrees, 73, 90 degrees, 105, 120 and on. And they cured the concrete for 28 days and the warmer it got, the faster and the higher the 28 days. Numbers got so it looked really impressive and it seemed like the dead heat one was 73 degrees where At 28 days it hit 100 percent at 365 days.
It hit 100 percent now the 365 day Designation was really interesting because they took every one of those concrete samples after curing them under those conditions, they put them in the 73 degree environment, 100 percent relative humidity, and the concrete that's cured, the warmer it was, the less strength it developed over time.
So it made it weaker and was consistent all the way through.
And we do that for convenience. So for convenience, we're basically having generations behind us inheriting All of our mistakes.
[00:27:01] Seth: Yeah. Oh,
[00:27:05] Robert Higgins: yeah, I know it's a mind blowing.
[00:27:08] Seth: Well, we're, we always like to blame the materials that we use. So, rather than blame the way we install concrete, pour concrete on why we're having issues.
[00:27:19] Robert Higgins: Let me say something. So the concrete people are getting ambushed as well. And in ways that they're not expecting, there are cement grinding aids that are being used in cement that are, is not being they're not informing the concrete producers. They don't have to. Which is unfair because concrete producers have to inform and list the ingredients they give to a customer.
If it's not sand, rock, water, and cement, they have to reveal what they put in the concrete. Well, the cement producer is not being required to do that. And that's really ticking me off because some of these cement grinding aids are glycol and amine based. These may be contributing to some of the problems we're seeing with floors because I saw a write up done by Sika out of out of Switzerland and how like cement grinding aid, where they were showing these what looked like a rust spots showing up on this decorative concrete that were these cement grinding aids reacted with some of the aggregate in the concrete and migrated towards the surface as a creating unsightly surface.
Well, if it's doing that to aggregate, what do you think it can do to adhesive?
See, and there's, there, see, now that, so that's how moisture migrates. No, it's different because you're looking at a chemical. A chemical will move and gets more active where it's warm. So they will accumulate in a warm environment.
Moisture will not do that. It wants to be driven away from the warm environment. We need to understand these dynamics. So all this crap that we learned about, well, moisture migrates from the underside of the concrete and goes to the surface, and then some people will cite the 1965 Brewer study that's been done by the Portland Cement Association.
Well, everybody reads the headlines. I read that study in detail, and in the conclusions, it does not say that. There's no way in the conclusions it doesn't say that moisture from the underside caused the flooring failure. What it did say is that moisture coming off the surface of the concrete caused the flooring failure.
So it's been established, we're just looking past it. We want it to be nice and confusing, and it keeps the attorneys busy, keeps these consultants busy because Boy, nothing makes money more than conflict.
[00:29:35] Seth: if there's no problems, there's, people wouldn't know what to do.
[00:29:40] Robert Higgins: Yeah, so if we do this with the concrete people, we do this with the installers, we can get rid of these problems.
a lot of unhappy attorneys, but I don't care.
[00:29:50] Seth: No, we don't. First place. That's right. Yeah. All right. Well, I think this is a good spot to end today. Did we cover everything you wanted to talk about today, Robert?
[00:30:01] Robert Higgins: Oh, well, the gist of it, because the details of this, yeah, it's, it really, when you take a deeper dive, it gets more and more interesting and not only more compelling, but it's extremely difficult to argue against.
[00:30:15] Seth: I would recommend any GC's or flooring folks that are listening and you're having issues. Robert's the guy to talk to. I think he could help you out. I will put everything as far as how to get a hold of Robert in the show notes. And because he's been on the podcast before you go to the website, and you can click on guests.
Robert's got a profile on there. If you go to his, you can listen to all the other episodes that he did, but we've covered this several times. All of it's been great stuff. Robert, I appreciate you coming back on here and sharing.
Until next time, folks, let's keep it concrete.
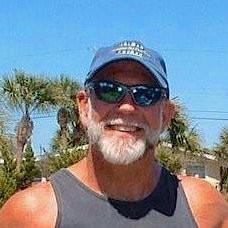
Robert Higgins
Involved with waterproofing and restoration of buildings and specialized in concrete. Have been involved with several committees with professional groups such as ICRI (first chair for moisture testing), CSI, speaking at national and regional conferences, authored the Flooring industry “White Paper” for the WFCA (World Floor Covering Association), moisture test instructor for the Academy of Textiles and Flooring, guest instructor for ICRI. Authored many articles regarding weather and environmental durability of concrete in multiple publications. Currently involved with IICRC Committee S230 and NFCA (National Floor Covering Association) “best practices” for moisture testing concrete prior to installation of Floor Materials.