EP #071: Concrete 3D Printing That Makes $ense

In this Concrete Logic Podcast episode, Seth interviews Darren Baldwin, the president of Pikus 3D, a 3D printing company in the construction industry. They discuss the unique approach of Pikus 3D, which focuses on commercial applications of 3D printing in construction.
Darren explains that their stationary, climate-controlled facility allows for larger, more complex prints, such as architectural facades and themed structures. They also discuss the advantages of 3D printing, including speed, design freedom, and safety.
Darren shares the future direction of Pikus 3D, which includes expanding into site furnishings, theme facades, and structural concrete.
Takeaways
- What are commercial applications of 3D printing in construction.
- How stationary, climate-controlled facility allows for larger and more complex prints.
- Advantages of 3D printing include speed, design freedom, and safety.
- Future directions for commercial 3D concrete printing include site furnishings, theme facades, and structural concrete.
Chapters
00:00 Introduction and Welcome
02:48 Introduction to Pikus 3D
07:30 Different Approach to 3D Printing
13:14 Advantages of 3D Printing in Construction
18:30 Applications of 3D Printing in Construction
22:18 Future Direction of 3D Printing
27:32 Limitations and Constructability
31:08 Reinforcement and Structural Capabilities
33:00 Conclusion and Contact Information
***
Did you learn something from this episode? If so, please consider donating to the show to help us continue to provide high-quality content for the concrete industry.
Donate here: https://www.concretelogicpodcast.com/support/
***
Episode References
Guest: Darren Baldwin | Pikus 3D | darren@pikus3d.com Guest Website: https://pikus3d.com
Producers: Jodi Tandett, Jace Stocker
Donate & Become a Producer: https://www.concretelogicpodcast.com/support/
Music: Mike Dunton | https://www.mikeduntonmusic.com | mikeduntonmusic@gmail.com | Instagram @Mike_Dunton
Host: Seth Tandett, seth@concretelogicpodcast.com
Host LinkedIn: https://www.linkedin.com/in/seth-tandett/
Website: https://www.concretelogicpodcast.com/
LinkedIn: https://www.linkedin.com/company/concrete-logic-podcast
[00:00:00] Seth: And welcome to another episode of the concrete logic podcast. And today I'm excited. I got Darren Baldwin, president of Pikus 3D with me. I've been trying to get a 3D printing company on here and Darren was nice enough to agree to come on the show. So thank you, Darren, first off.
And as I've been doing, I'd say the last handful of podcast episodes is I've been asking you all, if you get if you get some time here and you want to support the show there's several ways you can support the show.
The first way. So you get something out of the episode today with Darren, if you could share it with someone that you think would get some value out of the podcast, that would be great. The second way is if you go to the ConcreteLogicPodcast.com website, in the bottom right hand corner on the homepage, there's a microphone.
You can click on that microphone, and it will leave me a voicemail. And what I'm looking for from you is either topics or guests ideas to have on the show or feedback. You can always leave me feedback. And that's just another way for you to reach out to me. Obviously, you can reach out to me on LinkedIn or shoot me an email, but I just think it's a fun way that you can leave me a voicemail. And then on the same homepage. In the upper right hand corner, this is the third way you can support the show. There's a donate button So if you get something out of this episode or any episode that you listened to previously You can donate any amount you want There's a couple suggestions in there, but it doesn't matter if you get a dollar value two dollar value whatever Any amount is greatly appreciated when I get those donations.
I know I’m going in the right direction. So I appreciate that
Like I said, Darren Baldwin's with us. He's the president of Pikus 3D, and he's joining us from Utah today. Darren, I've tasked you today to change my mind about 3d printing.
I've shared with folks on previous podcasts that I'm not a big fan of what I've seen with 3d printing. But I enjoyed our conversation that we had before, and I was hoping we could expand on that conversation. So if you could first tell us a little bit about Pikus, what you guys are doing and what your angle on 3d printing is, and then we'll go from there.
[00:02:24] Darren Baldwin: Yeah, well, 1st, thank you, Seth for having me on today. I'm a big fan of concrete innovation. Anything that speeds up construction and enables us to enjoy creating right? At the end of the day, we take level ground in a field somewhere and we erect a building and some of us get excited. We're willing to travel to remote places and.
And build big structures and change the world. And so and we point at things and tell stories about it later, so for those of you don't know, I've worked at both Baker concrete and Lithko contracting two of the larger concrete contractors, North America. So, seeing a lot of concrete and understanding the challenges that go into a day in and day out of running a profitable construction business.
So, I appreciate you having me on here, Seth, to talk about 3D and where is it fit and why? I think that's a good question. When you go and search online for 3D concrete printing, you will see a number of images and many of which you look at and you think.
That's pretty ugly. I don't know if I like that. Some of which you might respond. Boy there's a lot of organic shape to it. Whatever your opinion is, I'm excited to talk about some of that. So, so that everyone's aware, Pikus 3D was birthed out of Pikus concrete, a structural concrete contractor here in Utah, the largest in Utah and Lithko bought them in 2020.
That's what happens when you grow a successful business that makes good money. Right? And you treat your people. Well, Rob Pikus was the visionary and leader behind that business. And well, the birth behind Pikus 3D was he just started to observe after the Great Recession. He wasn't seeing as many good carpenters around.
It was harder for him to find the carpenters he needed. And he felt his carpenters were fewer and fewer between that could go and do anything he needed them to do within the commercial space. And Seth felt like this was going to lead to longer lead times, higher prices, neither of which he wanted to go deliver to his GC friends and his developers.
So, he's he set about trying to solve that. He started looking at 3D printing and ended up he was used to going to Europe because he was buying some of his form systems directly. And while he was over there, he thought I'm going to go to her Europe and look at this, robots outside robots inside and which 1's better and what are the best filaments?
And he started going on this research. Face-to-face with those who were doing it around Europe and looked at the various systems and up selecting the system that we have bolted in here behind me in fall of 2019. Perfect timing, right before Covid, right fall of 19, this thing gets bolted in.
And so that was really the beginning, and his vision was always to automate them. Then, you mentioned being around parking garages for 10 years when you and I talked previously, and that's the kind of space that your structural concrete, right? The columns, the crash walls and getting to the decks and getting that turned over as fast as possible.
That's how you're going to get it open faster for the developer and make money as a. As an installer, so that was his vision. That's the birth behind and that's why we exist. And yeah, we're currently in several swim lanes, but I'll just pause there. I don't know if you have any follow up questions on the birth of 3D.
I think what's unique with you all from what I personally see, and I'll be one to admit that I haven't dove into 3D printing too far compared to other things I've studied. But what I've seen is mostly residential printing, and it's usually a machine that is shipped to the job site, set up, and then they print a walls of a house. That's most of what I've personally seen. I think what's unique about you all is your machine is, as I understand it, is stationary. It's in one spot and it's inside a facility similar to how most I say most because I've been to a lot of different places. Well, not a lot, but different precast facilities and most of the time their operation is inside.
[00:06:59] Seth: I've been to a couple that is actually outside too, but that's what it reminds me of. So if you could, I guess share as much as you can about that facility and how you guys are set up, I think that would be good for our audience to understand. Because right now, I think if someone would just start listening to this podcast and they say, hey, they're talking about 3D printing, they're seeing what I've seen before, all over YouTube, a machine is shipped to a job site, and it's printing walls for a house.
[00:07:29] Darren Baldwin: Right. Yeah. I think it's fair to say, Seth, most of the images. Yeah. Yeah. Yeah. People have seen online are of a residential out in the weather robot that is a gantry robot shipped to the site in the, and it's doing one thing it's printing walls and it prints walls, and it tends to print them relatively slow.
Actually, that's a reaction to hear from a lot of folks. Most people are aware probably have seen the 60 minutes special on Ikon who is doing this in Texas. And they're using a mortar that does take some time to set up. So they can only go so high in 1 day. It has to cure to some degree and then proceed from there.
And so, and it looks like it's printing out about thickness of a 2 by 4, right? So it's laying down some thick layers and, you're managing bond strength, right? Layer to layer and I've got I've got material here in my office. I can show you just to just, and for those of you who are listening I'm holding up a piece of our print.
You can see kind of print. Okay. Width, and ideally, you're going for this homogenous look, right? right? And so when you're laying down, everyone knows in commercial concrete. And in residential, when you're laying down concrete, you want it to all operate as one homogenous mix. And so, 3D printing, otherwise known as additive manufacturing, it just, it starts somewhere, and it continues to go around and around depositing layers.
That's just how the resin, if you've got a 3D printer at home. Same method. It's depositing layers layer after layer. And some of these layers in this case, if it's thick as a two by four, you just can't have big overhang angles. And an overhang angle is, how far can you deposit this stuff before it falls over?
Right? It needs to support itself. So there is a, an understanding of overhang angle we're achieving. Actually up on a compressive dome up to 90 degree on a straight line. We were doing as much as 35 degree and up to 45 degrees. So it does give you a lot more design freedom. You can see this wall behind me and we're doing contours.
We just launched rock work 3D printed rig ready. Themed facade in the rock work space, right? If you think of any amusement park zoo when they open these exhibits, you want to have rock work. You got to make it look natural. And so we're part of that place making facade work. So we're not just doing walls.
We're doing facade. We're doing. Leaving place column forms. We're doing sculptures. There's just a lot more design freedom in an additive manufacturing process where you're adding in an accelerant. So we have grout. It's a poly grout. It is a cementitious material and then we have some amount of poly, and an activator just lights up that concrete.
It's throwing off lots of heat but allows it to maintain support. And so we're printing 11 ft columns in 30 minutes. I think about 11 foot column and 30 minutes. I know last time you said 11 foot column, but, I think the rule of thumb in the industry is 3 men can say 8 columns in a day. We can print 12 foot in 30 minutes.
If we print and stack these on pallets, send them out. We're killing that number. Right. And with fewer people. So when you think about Pikus 3D, you think about commercials, most of the photos online, YouTube, you're seeing residential and there's a use case for that, right? But when you think of commercial, most of them are successful.
Products commercially are prefab, right? When it comes to any kind of thing that's going to speed up your construction process measurably, it's going to be pretty fab. And so that's the space we're in. And I love cast in place. I love precast. 3D printing is not going to replace cast in place.
It's not going to replace precast, but there's components. And niches within construction where you say, hey, cast in place is just laborious if I'm going to do a sculpture or if I'm going to do a wild looking column holding up this parking garage. Those things are better done by a 3D printer. If you're going to do anything architectural, if you got some class A space, there are some architectural walls and columns, you're definitely going to want a 3D print instead of making a one off mold or having to construct a bunch of wood to try to hold that space and a lot of advantages, a lot of speed advantages.
We tend to talk about the three S's. It's speedier, it's sleeker. And it's darn safer and don't have rubbing patch when you're done and silica dust in the air when you get done with our calls.
[00:12:28] Seth: no rub and patch. That sounds great.
[00:12:31] Darren Baldwin: No rub and patch at all. No.
[00:12:35] Seth: Yeah. Yeah. That'll eat you up at the end of a job.
Yeah, no, I, my ears lit up because you're saying things, I heard from gosh, it's been three, it might be three years now. So, so, I bought a concrete chess set from a local guy that was 3D printing the chess sets and I met with him at his shop and it was just he was at one of those, like, it's like a coworking space, but for like craft folks or whatever he was working out of one of those shops. So I met him over there and I was paying him for the chess set, picking up the chess set. And I was like, man, this is cool. You 3d printed these chess sets. And he's like, he's like, yeah, he's like 3d printing is good for one off things like.
Those sort of things. But as far as doing a mass production of tons of things, say like a, like precast or something like that, he's like, it's no good. And that always. I guess was in the back of my mind after I heard from someone that actually was, doing what we'd call 3D printing back then.
And so I guess that's that might have slanted my opinion of 3D printing after talking to someone that's done it and then everything else, I was really skeptical of. So I really like what the angle you all are taking. I checked out y'all's website. You're doing like. Very architectural like pieces.
And always thought if 3d printing is going to survive, it's going to be doing things like that. Things that like you were saying, the way you can print it, angles or cantilever out. Angles, that it's very difficult to do with traditional form work.
[00:14:24] Darren Baldwin: Well, that's right. Yeah, I think when you talk about 1 offs, it's clearly a slam dunk to go to 3D printed of concrete. And then, if you do a million of something, right, you want to precast it. If it's a boring straight line let's talk about design. If it's a straight line and not a serpentine curve wall.
Cast in place is still going to beat out in terms of price per linear foot. I think you start angling it out. You start putting any kind of theme on that wall, branding artwork, and you want it to be in concrete. You definitely start pushing into, this is much more economical to be 3d printed. Keep in mind.
Seth, this is we're again in the early stages. If cast in place has been around for a thousand plus years, precast has been a hundred plus years. 3D printing of concrete has been only 20 plus and really the launch of commercial, which is pioneering has been 4 years. So we've had product in park city for 4 years.
Our filament is some of the most tested filament in the world and, the reason why it's taking hold is because the amount of square foot we can generate in a day. And so when you do have a climate control facility, and we have the largest 3D printer, largest climate control 3D printer in the world, let that sink in for a second.
You can go bigger outdoors, but if you want to have a climate control, you're not going to beat him. What that means is you have better overhang angles and more square foot that you can cover in a day. And so being able to create in this case, upwards of 3000 square foot of custom facade of themed rock work that can't be done really any other way.
So it starts to beat out other methods, other technologies once you get to that scale per day. And that's where we are.
[00:16:34] Seth: Gotcha. And is the machine? Is it all 1 of the, is it put out just that 1, the poly grout right now? Or is that it for now? Or
[00:16:47] Darren Baldwin: yeah, so we are printing with poly grout our ability to do secondary process add other.
Secondary structures, textures, colors that can all be done, and we are doing that today, integrating woods, steels that are powder coded, integrating maybe other some cases we're even doing ballistics with polyurethanes and sandwiching other materials in there. And so, different use cases we can achieve different products for.
And some of which will be automated in our next facility, and we are in our plans over the next five years to have numerous facilities around the country
[00:17:28] Seth: and different, I assume different colors since you're doing like you were saying theme park stuff. And because right now, and again, going back to what I've seen on YouTube and these residential guys, it's 1 color.
And sometimes it matches, but sometimes it doesn't.
[00:17:45] Darren Baldwin: Yeah. So you can see a theme wall behind me with some with plants in it. It's we call it Pikus pure. Pikus pure white. It is very light gray effectively, which means it, it takes color very well. It we do use Butterfield integrated color, highly UV resistant.
And if you chip it, it's the same color throughout. Right. Seeker bought them. It's a Seeker product. We also use some other integrated color. And so you can print and use the raw plus an integrated color and 95 percent of the time, at least in site furnishings, planters, benches. Bollards those are being ordered in the raw print, because architects like how it holds light or cast shadows within the print makes it unique.
Yeah, so it's like regular concrete stuff. Anything you coat on regular concrete. Stucco's, you can put tile on it, you can stain it, you can paint it, you can paint it, you treat it just like concrete. If you want to do penetrations, you can drill a cut into it and put fasteners just like concrete.
[00:18:56] Seth: And as far as reinforcement
Is it fiber or is it how you guys doing that?
[00:19:03] Darren Baldwin: Yeah, we have several ways to reinforce. Right? So a lot of things don't need a whole lot of reinforcing. If you think of a baller, it's okay if it's hollow. In fact, it makes it easier to get lighting up through it. Right? If you get into benches, having a hollow bench where we can hide sound equipment.
Is advantageous, but we do need to meet the North American standard, which is a 300 pound drop from 6 inches. We do, in some cases, fill objects with concrete with rebar. Sometimes we use our PSN28. It's a Pikus structural membrane, an alternate to concrete, which is a lightweight. It's a polyurethane made from recycled water bottles and also has a waterproofing and fire resistance to it.
And so depending on the product and depending on the project, we evaluate from a digital design perspective and a digital engineering and come up with what's the best material for the project.
[00:20:05] Seth: Yeah. Well, I think we at least we convinced me, what we can use 3D printing for, so I appreciate that.
What are you thinking? I, so right now you're doing one offs, you're doing furniture and some theme park projects. What are, What's the direction of 3 D printing?
[00:20:29] Darren Baldwin: Yeah, we made 3 major swim lanes. So I'll send you a copy of make a statement magazine is our quarterly magazine or catalog and you can see our site furnishings in there right now.
So that's definitely 1 of the initial emphasis for us was site furnishings, fountains, really cool benches, really cool fire pits. Planters, right? So we're definitely working on those doing custom 1 offs with landscape architects. The other swim lane that we focused on now, with our recent launch of rig ready rock work is the facade.
So, whether that's a parametric, or whether that's just rock work in your zoo, where that's a space we're going after. And next quarter, we will be launching structural concrete, a fill and go form. And so that is a product that supports structural concrete contractors who are doing columns. And today, right, there's a lot of work, we spend a lot of money in order to fur out the columns once those are done.
Most of which is there to either do fire rating and or electrical. But we can integrate all of that within our fill and go form. In this case, it moots and shifts the value upstream. So when the structural concrete contractor is done with that install, it's a class a finish with integrated connectors for electrical and also meets the fire rating.
So you're not having to add those. Those there's trades downstream. It is all covered with a protective wrap, and it just makes speedier, safer, sleeker construction.
[00:22:07] Seth: I saw an article. It's been a while, a few months. There was a project up in New York, I believe, and they used shotcrete to make the angles.
It was a very big it looked like 45 degrees, but I'm sure it wasn't, but a 45 degree angle that kind of jutted out and they used Shotcrete to create that wall that I guess this architect dreamed up and I was like, that, what I see there, that should be 3D printed. That, because to me, yeah, because that would give you, I would think of what I've seen and what you're sharing with me today.
And this is not to kick my shotcrete guys out there, but I think it would give it a better look better product at the end.
[00:22:54] Darren Baldwin: Well, yeah, and 2, yeah, the there's still gonna be use cases for shotcreting but there's a lot of zoos. That maybe have a small amount of square footage where you just can't afford to get someone to come out, set up shop and do a shot, create if you're not doing a ton of square footage.
And so they'll get prices they just can't afford. It's just not achievable. And so we have then a modular. Panelized print. And when you look at the print, it's perfect for receiving a carve code, a finished texture, right? And so that can be sent out, pinned in place. It wouldn't even have to weld it. They didn't want to.
They go ahead and finish it without having to close down the rest of the zoo right from the mess and dust that's going to blow up. And so I think it gives more flexibility for those zoos. As well as the shock readers who want to take care of those smaller projects where maybe where it doesn't make sense to bring in a hose and set up your system.
So yeah, I think it gives more flexibility to installers out there as well.
[00:23:57] Seth: And I'm assuming embeds and, you just brought up welding and penning and all that, so I was thinking I should ask about that. So embeds and all that. That's not a problem to incorporate into your process.
[00:24:12] Darren Baldwin: Yeah, not only is it not a problem, but we do a lot of that here in our climate control facility. So we're not dodging the weather trying to get embeds done. We can do all the penetrations here, have those sealed sent out and then the installer can get that done, quicker where it's done, you're moving essentially a sequential part of your construction process into parallel, right where it's getting done when you're not there and it just shows up ready to go.
[00:24:41] Seth: So really as far as limitations for what y'all can do it's based on what you can put on a flatbed truck.
[00:24:50] Darren Baldwin: That's a good question, Seth. We have a print bed that can do 16 foot by 13 foot by 12 foot. Okay. It's 70 cubic meters for those people who like meters. Big print, largest in the world in a climate control facility.
Often the constraint is not the print bed. It's not even transportation, actually. What we're seeing time and time again, Seth, is the constraint tends to be constructability process. So even though I can print a 12 foot tall column. It probably doesn't make sense to ship it down the road. Although I can lay it down and do that.
Once you get it to site, it's, tipping that sucker up and getting it slid over my rebar is easier done in smaller segments. And so much like, let's go back to construct ability. We had a fountain that was going into backyard of a u-shaped building.
So it had, they could only get to the backside with a crane and because our print was hollow, they could go with a smaller crane. But we did print it to a steel plate, so they could just drop it right onto a level steel plate instead of trying to nail it right to the bolts. We ended up dropping it onto the plate and it was just stitch welded.
So we're usually working with the installer to understand all these details of construct ability. So it makes their life and their world easier. And again, this is. Our goal being my background and in construction focused on making things speedier and safer for the installer. And so we're really installer focused and working with GC's to help them
[00:26:35] Seth: the hollow form that you mentioned, I assume that this is something that you
put in place and you leave it, right? Not like traditional form work where you remove it afterwards.
[00:26:45] Darren Baldwin: Yeah, having to deal with needing space in a lay down yard and oil the forms, wreck, remove your forms, rub and patch and blow silica dust in the air. We wanted to engineer all of that out.
We heard that, a great percentage of safety issues. And so if we could engineer out this part of the process where a lot of those injuries are occurring and also just sequencing at work, having a wreck forms on the deck above. Where you're wanting to get work done, if you can remove that segment of the work out, so you can go ahead and move on to the next deck of work, it just makes the installers world easier and it actually makes them more money, right?
It gets them off the job faster and onto the next job.
[00:27:32] Seth: has anyone studied or looked at since you're leaving this essentially, this precast piece in place and you're filling it up with concrete. Does that, does your piece The 3D printed piece, does that take place of any reinforcement possibly since it's a structural piece. Can it replace, maybe if you were doing a traditional concrete column, you would form it up well, you put all the rebar in there and then you would form up around the rebar, pour the concrete and you would have that and then rip the form off. So you're losing the form. But in this case, you're saying you put it up and you leave it.
Can it take the place of reinforcement that's in that example, that column.
[00:28:17] Darren Baldwin: Yeah. Yeah. I love where you're going Seth, because it's that, additional savings and material, right? So the installer if we get today, our fill and go form is not approved for the structure. Okay, so we're not deleting clear cover.
We're actually adding to the clear cover, but we're not deleting because today we're not saying it's structural. We're just saying, hey this thing's going to hold up on under hydrostatic pressure, let her rip with the pump truck, fill her up to the top, vibrate it, move on to the next. And once we do get it approved for structural.
Meaning it would remove would require less material for the installer and you're talking 70 bucks per column. And it's 1 additional add on for the use and value that we're delivering.
[00:29:15] Seth: Yeah, well, like you said, we're in the infancy of the technology. So, baby steps.
[00:29:21] Darren Baldwin: Baby steps.
That's right.
[00:29:24] Seth: Well that's awesome. I think that's that was a great intro. Like I said, I think you changed my mind. I like the way you all are going at this thing. I just, I don't understand the 3D printing where we're printing straight walls. I was like we can, we already got that solved. We can do that all day and pretty sure we can do it faster and cheaper.
Darren, I appreciate your time today. I got architectural friends that listen to this. I know that. So I can see, I could see them kind of thinking of, well, what can I cook up for Darren and send it his way? Because I can imagine I was looking on your website. It looks like you guys have some kind of sandbox or something for designers to learn how to use your technology. But anyhow, other than the website, which I'll share with everybody, what's the other best way to reach out to you and Pikus?
[00:30:13] Darren Baldwin: Yeah, I would say 2 ways, Seth. The best way to reach me directly is to email me and that's just Darren.
D-A-R-R-E-N at Pikus 3d. com. Email me there or find me in the notes under this this cast also, you can message me directly on LinkedIn. If you go to Baldwin, Darren just search for me, Darren Baldwin. The tag is actually Baldwin. Darren, by the way, I look up Pikus 3d and you can just message me direct there.
[00:30:43] Seth: All right. Sounds good. Thank you again there for coming on the show and folks until next time. Let's keep it concrete
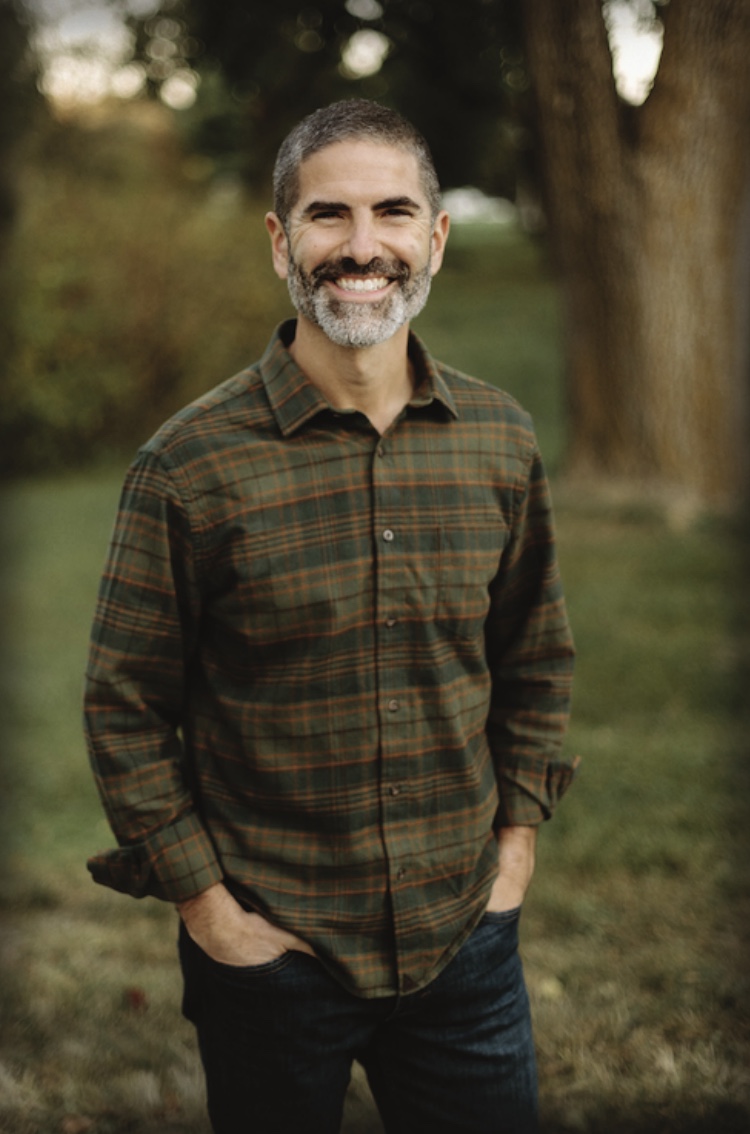
Darren Baldwin
President
Darren Baldwin is President of Pikus, a 3D concrete products company headquartered in Utah. They design and fabricate the speediest, sleekest and safest concrete products for commercial construction. With installations in all US time zones at some of the coolest locations, Pikus has product at Disney Epcot, The Kennedy Center, Park City and NFL player’s houses. Using the largest climate-controlled 3D printer in the world, they can print and ship columns, facades, rockwork and fountains to over 90% of the US within days. After starting his career at Deloitte Consulting, he left to work for two of the largest structural concrete contractors in the US, Lithko & Baker Concrete. He has launched SaaS-based companies and commercialized digital products. In 2022 he returned to concrete, this time with advanced additive manufacturing technology. He resides in Cincinnati Ohio, where he and his wife enjoy time with their 5 children. In his free time, he enjoys mountain biking and motorcycling.