EP #069: Dampening the Risk: Concrete and Moisture Emissions
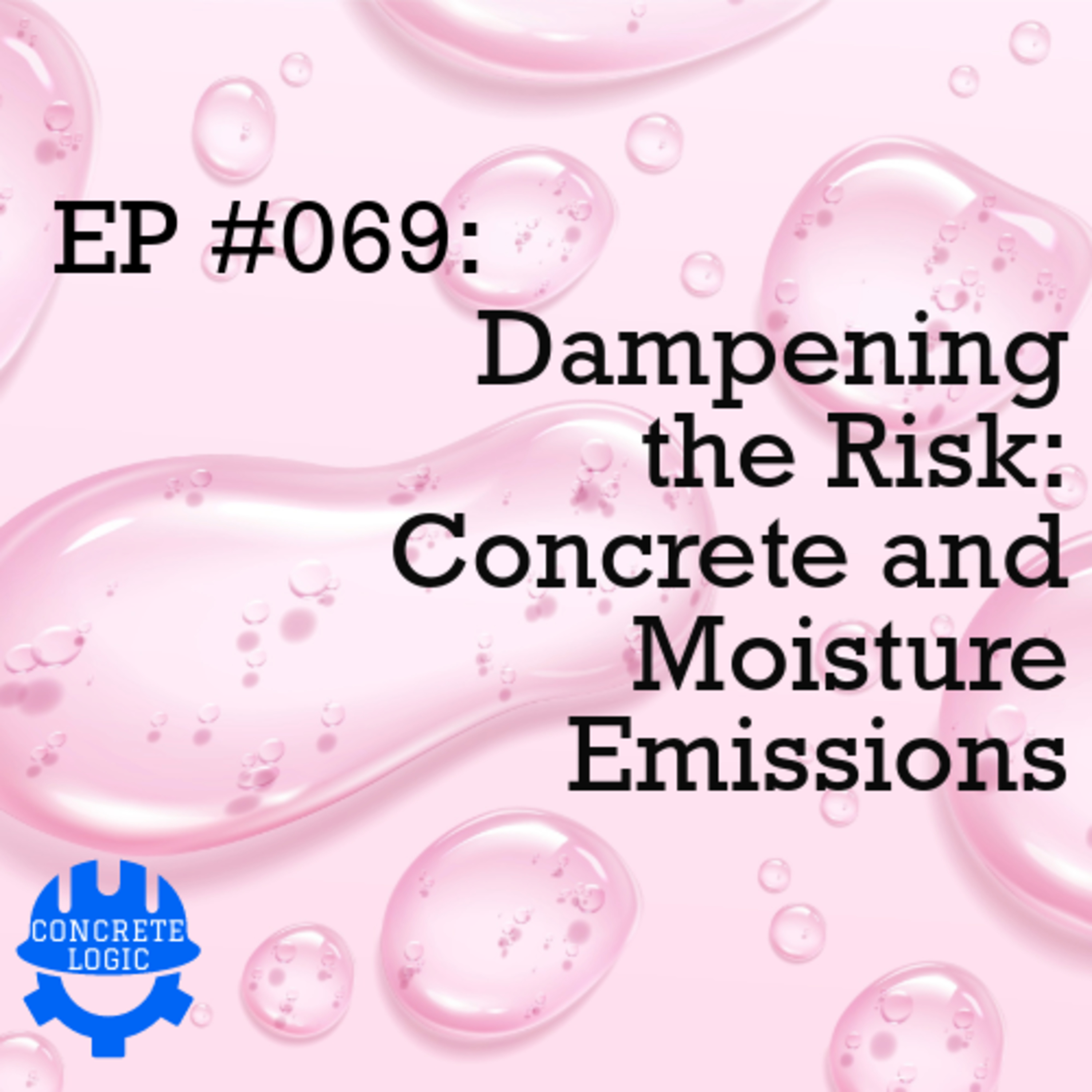
Summary
In this Concrete Logic Podcast episode, Dean Craft discusses the topic of concrete moisture vapor emissions. He explains that moisture vapor emissions occur when residual moisture in concrete is released and can cause adhesive bond failures and other issues. Dean emphasizes the importance of addressing moisture vapor emissions early in the construction process and suggests proactive approaches such as using concrete mixes with admixtures to mitigate moisture. He also highlights the limitations of moisture testing and the need for a shift in the industry's mindset regarding moisture vapor emissions. Overall, the episode emphasizes the importance of proactive planning and communication to prevent issues related to moisture vapor emissions in concrete projects.
Takeaways
- Moisture vapor emissions in concrete can cause adhesive bond failures and other issues.
- Addressing moisture vapor emissions early in the construction process is crucial.
- Proactive approaches, such as using concrete mixes with admixtures, can help mitigate moisture vapor emissions.
- Moisture testing has limitations and may not accurately reflect the moisture conditions in concrete.
Chapters
00:00 Introduction and Podcast Support
02:28 Concrete Moisture Vapor Emissions
04:46 Effects of Moisture Vapor Emissions
09:05 Importance of Proper Timing
11:42 Personal Experience with Concrete Countertops
13:12 Importance of Proper Mixing
16:30 Misconceptions about Moisture Vapor Emissions
19:11 Real Issues and Blame on Moisture Vapor Emissions
22:19 Addressing Moisture Vapor Emissions Proactively
30:28 Proactive Approach and Liability
36:59 Moisture Testing and Relevance
41:59 Conclusion and Proactive Approach
***
Did you learn something from this episode? If so, please consider donating to the show to help us continue to provide high-quality content for the concrete industry.
Donate here: https://www.concretelogicpodcast.com/support/
***
Episode References
Guest: Dean Craft | ISE Logik Industries | decraft@iselogik.com
Guest Website: https://iselogik.com/
Executive Producers: Jason Adams, Shannon Hoover
Producers: Jodi Tandett, Jace Stocker
Donate & Become a Producer: https://www.concretelogicpodcast.com/support/
Music: Mike Dunton | https://www.mikeduntonmusic.com | mikeduntonmusic@gmail.com | Instagram @Mike_Dunton
Host: Seth Tandett, seth@concretelogicpodcast.com
Host LinkedIn: https://www.linkedin.com/in/seth-tandett/
Website: https://www.concretelogicpodcast.com/
LinkedIn: https://www.linkedin.com/company/concrete-logic-podcast
[00:00:00] Seth: And welcome to another episode of the Concrete Logic Podcast. Today I have Dean Kraft with me with ISC Logic Industries. Dean was on episode 36, which was fairly popular. I was sharing with Dean before we hit record. We talked about Glue water you would like, why people are so interested in glue water?
[00:00:23] Well, we're gonna revisit that topic today That's why Dean is here. So you guys will learn about that but before we get started as I've been doing the last few episodes just wanted to remind folks How you can support. so there's a few ways that you can support the podcast. The first way is if today you hear something from Dean and you thought it was insightful or you learned something from it, please share the podcast with somebody that you think would get some value out of it.
[00:00:55] The second thing is if you go to the podcast website. ConcreteLogicPodcast.com on the bottom right hand section of the homepage. There's a little microphone click on that microphone. You can leave me a voicemail. And if you could leave me a voicemail, just tell me what you think about the podcast, or if you have a topic or a guest suggestion, that would be great.
[00:01:18] You can always email me too. but I thought it'd be cool to hear people. The last way is back on the homepage in the upper right-hand corner. There's a donate button. And again, if you feel like you got something out of this episode or any of the episodes and you want to donate to the show, you click on that and you can donate any amount and just think about it like you're donating to another one of these.
[00:01:42] different associations we're all part of, there's ACI NRMCA there's the flooring. I don't even know what the flooring ones are, Dean, but we all pay into those. So it's like paying into that, but you can, you get to choose how much you want to send over to the Concrete Logic podcast.
[00:01:59] Those guys don't let you choose. With that Dean. We'll roll into our topic of today and we wanted to start off and talk about concrete moisture vapor emissions. Okay. What is that?
[00:02:19] Dean Craft: Okay. So we'll start with the concrete world. Obviously when the like any mix, mix design or the basic recipe, when I talk to non-concrete people, the four components, you got your sand, rock, powder, and water.
[00:02:32] And then throughout the process of placement consolidation, you had the bleed process. So a lot of that extra water from the mix. Is lost during the bleed process and obviously about half that water is consumed in hydration, but throughout the cockroach life. Some of that residual moisture either from placement or from getting re wet after placement is going to make its way back out.
[00:02:56] Which is no big deal. Obviously, we all know that concrete loves water concrete's happy with water. But when we try to Stick things to concrete, or once we do stick things to concrete if that moisture continues to come out, if it emits moisture vapor emission depending on what the chemical constituency of the binding agent to whatever it's sticking to the concrete.
[00:03:19] If it does not like moisture that vapor emission can cause that adhesive bond to fail. It could cause, now let's get back to say flooring. It could cause some kinds of flooring to, adhesives literally to re emulsify, go back to a liquid state. It could cause Certain kinds of flooring product, let's say wood, to swell and cup and buckle.
[00:03:42] Let's go to epoxy flooring. It could cause it to literally bubble up, dome up paint, paint to peel. So moisture vapor emission is the residual mixed water coming out in a gaseous vapor form. And then re emulsifying or basically attacking the material that's causing the bond to the concrete results again a failure.
[00:04:07] Seth: Yeah, that, when you started talking about epoxy, I just did concrete countertops in my house, and I did epoxy coating over the top. And one of the instructions for the epoxy, it says you got to wait 14 days before you put the epoxy down. That's to get all the moisture out, right?
[00:04:25] Dean Craft: That's okay. So that's a whole different subject, but a lot of products and in the commercial world. Most of those products say, wait 28 days and here's the crazy thing. You'd be in a concrete guy. 20 days is the day that we want to see the engineers want to see the design strength, that's the 28 day.
[00:04:43] So a lot of products out there that are not in the concrete world will say very clearly, wait 20, it's this full phrase, wait 28 days until the concrete is fully cured. Which I always hate that term cured until you can put your material down and yes, they are relating, they, those manufacturers are relating 28 days to the concrete, no longer going to emit a moisture in sufficient quantities to cause the material that's being applied to fail, but it skips a whole lot of things.
[00:05:20] One 28 days in concrete terms is related to a design strength goal. And not to whether the concrete emitting moisture. So it's like saying I want to take a trip to Texas. And then somebody responding I'm going to wear a blue shirt. Okay it's not related.
[00:05:41] It's not in the same world. The unfortunate thing is it leads a lot of contractors on owners to think that 28 days is some kind of magical time. Think about concrete roof decks. This is especially damaging with roof decks because that concrete is exposed to the elements. So I always laugh when I hear that and I'm like, okay, what if it rains on day 27?
[00:06:02] And then the manufacturers, they have nothing to say. They're like well, I said, do you restart the clock? Because the data shows the concrete is going to be 100 percent humidified again. It's going to have moisture content again that's going to have to release. So what do you do? And unfortunately, these manufacturers don't have an answer for that.
[00:06:22] But yeah, you're right. So the 14 days is that manufacturer trying to gain the vapor emission from the concrete. Did you have to profile at all or did, were you able to just put it down on the concrete? Just curious.
[00:06:40] Seth: yeah, you had to sand it a bit. that's what you meant by profiling, right?
[00:06:44] Dean Craft: Correct. And that's how you create a mechanical bond as opposed to a chemical bond. The second reason why a lot of these products, especially in the industrial world, will say wait 28 days. Is because the mechanical profiling is usually a bead blast shot blast. And so they want the concrete to be a minimum of 3,000, 3,500 P.S.I. before they start shooting ball bearings into it.
[00:07:04] Seth: I learned that the hard way. So I was trying to, man, doing projects at home with the family involved around you and crazy four kids at home, so it's like a circus. That's why I didn't hire someone to do this.
[00:07:17] You had a labor team.
[00:07:19] I Didn't have a labor team. My oldest son helped make some concrete, so that was cool. But having the patience to work around what's going on within the house, and everyone likes to use the kitchen, so you got to work around, kid running to the refrigerator, my wife trying to use the stove all those different things that if you have a contractor come in and do these things, I don't know if he'll price that in.
[00:07:42] Dean Craft: And his proposal for delay a project.
[00:07:45] Seth: Exactly. You get, how many interruptions a day do you get when you work in the Tandett house. well, anyway, so I was trying to Push the schedule, I got in there and tried to sand a little bit earlier than it told me, and yeah, it was it was ugly.
[00:07:59] Dean Craft: Oh, so you're, so the concrete itself wasn't how early did you try to push it?
[00:08:03] Seth: I was like I think it was like next day or something. I was just see literal, oh my gosh... But like I said, it was a, it just a very it, it was a, like a heavy, paper it was, they just asked for a little bit.
[00:08:17] I forgot what it was like 200 grit or something like that, that you had to hit it with, And I was like, ah maybe, but
[00:08:23] Dean Craft: it's all right. Yeah, it's taking up a lot.
[00:08:26] Seth: Yeah. Yeah. And, you're exposing aggregate and all this other stuff and it's like, no, it's
[00:08:30] Dean Craft: gonna be cool. That's what you're looking for.
[00:08:32] But yeah. So there you go. That's a perfect example. Maybe not a perfect example, but. So if we're ever involved we try to bring it back to, the world of reality and say, well, 20 days is really a design strength construction engineer, use, they can start testing it, 24 hours if they want, but there's usually a 3, 7, 14.
[00:08:51] First and foremost, you're looking for design strength for that product, so that 14 days for you may have been more related to design strength, especially because of the interior, but secondly, those products still related back to some moisture vapor loss that they believe that a certain amount of moisture or sufficient moisture will have been vacated from this emitted from the concrete.
[00:09:11] So it's not gonna cause their product to de-bond. But when it comes to epoxy A two part epoxy, a two part urethane I put much more weight on the concrete strength profile because of the mechanical abrading or profiling or beating the crap out of it would be ball bearings before applying the material.
[00:09:33] Yeah. So yeah. As you saw yourself.
[00:09:36] Seth: it's like those things you do at work, you know better at work, but then when you come home you seem to like,
[00:09:41] Dean Craft: yeah, I was, things that you do. That's why I was laughing with you, because I'm thinking given your history and what you do, I'm like, I've thinking with know that.
[00:09:49] Seth: Well, it's like, on a job site, we're all very safety conscious and you got to all your PPE gear on and you're watching out for each other. And then you get home and then you jump on the ladder and,
[00:10:01] Dean Craft: Sit on a bucket and you're reaching. It's.
[00:10:03] Seth: Exactly.
[00:10:04] So I did that. That was stupid.
[00:10:07] Dean Craft: But so did your wife, was your wife then impressed with your professional acumen at that point?
[00:10:12] Seth: Oh, it's the jury's still out. It's an ongoing process. No I, for my first time of doing countertops, I I'm satisfied with it. I know what to do next time.
[00:10:23] Dean Craft: And I definitely won't do it in an active kitchen ever again. Very big fan of concrete countertops but go back to your two part epoxy. One of the things a lot of people separately, but this does lead to issues that get blamed on moisture. They have nothing to do with moisture. I'm guessing or should have that your epoxy two part had fairly detailed or clear mixing instructions.
[00:10:45] In other words use a certain kind of blade, a certain speed. A lot of people. Yeah. DIY. Well, I'm not going to blend this on low for two minutes, I'm going to frappe it and I'm going to put it on high and I'm going to make, I'm going to make a meringue. I'm going to get this done. I'm going to mix this together quick.
[00:11:06] Well, that then sucks in air. So think about your concrete, you induce, you're sucking a lot more air, which compromises what you're trying to do with the concrete in a lot of cases. So when it applies it, when you, when it is applied, it can create a lot of air bubbles. And the next we can screw it up. The converse though, is if it's blended insufficiently.
[00:11:27] And I have seen this on one fire station in the Northeast commercial job where the installer did not mix sufficiently and. After it was placed, the A and B components started separating and there was a light brownish yellow viscous substance that was oozing out of the surface of the concrete.
[00:11:49] Why this is important to your subject, your question initially about moisture vapor emission. The installer came in and blamed the concrete. Specifically, that moisture in the concrete was causing this stuff to come up. We were not involved with the project, but the concrete sub on the project knew what I did, and he reached out to me.
[00:12:12] And so I asked him specifically, tell me exactly the product and I needed the exact names. And so I got part A and part B, and then I went to the SDSs of both products. A whole list of different chemical compounds, but I started going through each one of them. And lo and behold, one of the constituent components was described.
[00:12:30] As a light yellow to light brown, viscous substance, slippery, because the guy told me it actually had the consistency of brand new 10w30 motor weight oil. And I said, well, one, there is nothing in the concrete. That's that color at all. I think ever. Secondly, if it was, it wouldn't be coming out. So I said that the idea that this is coming from the concrete is simply absurd.
[00:12:56] Secondly, I actually researched, I said, there is a commercial warehouse that sells that exact product about an hour from you. I said, this is what I recommend. I said, go there and buy the A and B. I said, then go to a dollar store. Don't use your wife's China. Go to a dollar store and buy like four or five white ceramic porcelain plates.
[00:13:17] Disposable, you don't want to use paper, but on one of them, put a bit of the A and B. And just haphazardly mix it, don't let it, don't mix it as much as you're supposed to. And then on another one, mix it until it's fully incorporated. And then look at it the next day. He calls me back, and he actually replicated the issue.
[00:13:39] And so they had a meeting at the city hall where the fire station was. And this whole situation starts going down, and he does his little show and tell. He brings it out. He goes, this is on porcelain, that's the exact same material, all that's on here. It's part A and point B, and so it went from being the concrete blamed on the moisture vapor emission to being the actual issue where the material was not blended sufficiently, and it started disincorporating after it was applied.
[00:14:12] So moisture vapor emission, whoever's out there in the world that may listen to this concrete moisture vapor emission is, has become and public enemy number one, and is the easiest situation to blame on basically any issue that manifests with something adhered to concrete. Like the example I just gave you, if the general contractor of the owner in this case, the concrete sub, the ready-mix producer, if they don't know, then they're going to be sitting there playing Texas Hold'em with literally no cards in their hand.
[00:14:49] And then the installer. And their material supplier are going to have all the cards. So literally they can say whatever it is they want. And the other side of the table is just going to have to sit there and say, okay, but in this situation, that concrete sub knew me, and we were, and I was able to help him figure out a way to.
[00:15:11] Totally flip the script and it was back on the installation company to come in and tear up this 30, 40,000 square foot. So think about the amount of dollars involved with that, with epoxy, right? You're shaking your head. Cause these issues can become very expensive very quickly. Cause now you've got partially bonded, partially secure.
[00:15:31] You've got a you've got a maintenance space where you're having very heavy fire trucks parked, ambulances, and now all that has to be ripped out. Which is not easy to remove epoxy so it can be relayed correctly because once it starts deboning like that It's gonna start tearing and opening up and it's gonna just the whole floor is gonna fail again all that was going to be blamed on moisture vapor emission only because the those that actually had liability Or perceived liability, owner, GC, concrete sub did not know the product characteristics that was being applied after their job was already done.
[00:16:16] That's the other, that's the other insidious thing. Ready-mix Producer and the concrete sub had done their job, they'd done their job well. And now somebody else has come in and done something, it starts to fail, or an issue manifests, and then that later organization, later material, has been able to readily, easily, immediately turn around and blame the concrete and the culprit is moisture vapor emission.
[00:16:44] Seth: So moisture vapor emission is a real thing. It's just at a certain point, it's not a cause of an issue, right?
[00:16:54] Dean Craft: Correct. And see, the reason why I say when we get involved is because the world that I've worked in for the past 15 years is to put something in the concrete to keep that moisture from coming out.
[00:17:07] So either when I get involved, it's either one of two ways. One, our product was not used, and somebody wants to know what to do to help address the issue. Or secondly, where product, our product or product like ours was used, which was the case that I just told you. In Connecticut, I think it was Connecticut, where the project is being told something by the flooring, roofing side, and they're like this does not make sense.
[00:17:38] And so they're looking for our help to push back or to figure out, let me give you another example of how this can manifest. This was a project we were directly involved with and let's go back to moisture vapor emission. Yes, it is a very real thing, if not addressed. And there's two major ways to address it.
[00:17:56] Or I guess three, one is not to, or I would argue it's not, are not cost effective one is just to acclimatize the space, turn the HVAC on and wait, that's not cost effective in time or money because it could take months. So imagine a GC going to a hospital group that's building a 500,000 square foot complex, a million square foot right now we're involved in like a million square foot project down in Miami.
[00:18:32] Yeah, these. These hospital complexes can be big, and telling that hospital group that they're going to have to wait an extra four or five months after the building is finished, and the HVAC system is running, before they can start testing for moisture, so they can put the floor down, hospitals are money, revenue generating facilities.
[00:18:57] So that's an opportunity cost loss. And so when you think about the value of a hospital space and what it can generate, we went to one symposium for design construction of hospital facilities. And one of the questions I let off with when I sat down with different hospital groups was if you don't mind me asking, what is the value, what is the revenue potential of something like a cardiac O.R. Suite?
[00:19:19] And the best answer I got that just blew me away was this young lady. She's like. She was like, it depends on how many valves are being addressed. And I was like, what? She goes, the heart has four valves. She was about a quarter million a valve. She just like that. And I just, I was just, I was shocked, but they know.
[00:19:43] So at minimum a quarter million a day. So let's say there's 20 OR suites that can handle cardiac surgeries. And you're going to shut those down for six months. So people start thinking about the cost. It is literally nearly incalculable. Waiting is not feasible time or money. Secondly the Cadillac option is to come in and then be blast the surface.
[00:20:07] So let's get back to carbon emission and offset potential. And now you're coming in electricity and be blasting and silica dust. Then you've got a prime two part epoxy self-level. And that can run anywhere on a low end of maybe 5 a square foot to easily 8, 9, 10 a square foot. So let's go back to that same hospital group that's got the million square foot facility and says, okay, we tested right before flooring, got too much moisture.
[00:20:33] Hey, Mr. and Mrs. Hospital owner on your million square foot facility, we need another 5, to put your floor down. That doesn't, that conversation doesn't go very well. Tell that to a school board that's been saving seven years for a bond. Otherwise, they're gonna have to wait another year to open the school.
[00:20:50] Doesn't go well for the community, or you can put something on the concrete. So that's basically the three ways to address it. You either wait, which is time and money. You pay a lot, or you proactively address it some way in, in the early on. And there's ranges of options in between to 100 percent waterproof adhesives, but they still have a cost and application and ranges therein.
[00:21:15] So let me go back to moisture vapor emission being a very real issue. You can easily Google and actually I just gave a presentation last week and somebody asked me for failed floors. And so you asked me. Is it a real issue? If you Google moisture related flooring failures, you’ll see the things I mentioned.
[00:21:32] You'll see VCT buckling. You'll see mold under, under, under carpet which is always a big, scary thing. You'll see mold under VCT or sheet vinyl. You'll see buckling wood. You'll see bubbles in athletic courts. The damage is not only real from real moisture vapor emission.
[00:21:48] The damage also exists from the claim of moisture vapor emission. And then the owner being stuck with something that should never have been occurred. The At all. The one example I gave you where our product was not used, a competitor was used, but they came to me that the project came to me for help.
[00:22:04] There was a real case of had nothing to do with the concrete. Another case, very real case that we were involved with. It was a 50,000 square foot addition to a school in New York. Not a big community. So pretty big spend for that community. And in this community, in this facility, there was yeah.
[00:22:22] 45, 000 square foot of VCT tile and 5, 000 square feet of rubber tile. So most people that are not in flooring have no idea, what the difference is, they're both. tile. They actually look very similar. Aesthetically, they picked two that were very similar. Unless you really paid attention, you or I would be like, it's the same stuff.
[00:22:44] We wouldn't pay attention. Well, VCT lays flatter. It is dimensionally more stable than rubber. Rubber has a tendency to cup up at the edges, even in the box, before you install it. Because rubber has that tendency, the glue you use to hold rubber down normally needs to be stronger, more solids, more expensive, than the same, similar glue that you could use for VCT.
[00:23:13] Now, there are glues that'll do both. But you could have a pure VCT glow, low solids, but if you use it on a rubber and it's not strong enough and it curls up, it looks like a moisture issue. 45,000 square foot of VCT, perfect, nothing moving. Literally the VCT came into the door to the music auditorium, the tiles were touching, the very next tile as you walked to the auditorium was cupping.
[00:23:42] Every tile in the auditorium was cupping. The flooring industry comes in, pulls a tile up, drops a probe, it's moisture, high humidity. That's what's causing this. We asked, well, what about the rest of the project? Why isn't that failing? Well, the failure just started here. Right. So again, and I'm glad you, I'm glad you laughed because even the GC was like, so it just started here, but it's going to spread to the rest of the 45,000 square feet.
[00:24:11] That doesn't make too much sense. We went to the project and very simply we asked clearly what glue was used and right there in front of the GC My business partner called the manufacturer of that glue manufacturer the glue Asked them say I'm on a project where we got some VCT and some rubber. Can I use this product?
[00:24:34] Absolutely It's great for VCT, but no, you cannot use it for rubber It's not strong enough. And in fact, we do not even make an adhesive for rubber My business partner said thank you very much hung up That was a speaker. He looks at the GC. He goes, this is not moisture. This is the wrong glue for that kind of flooring.
[00:24:57] And he said, most likely the installer was on site, was spreading glue. The tiles looked the same, never even realized. And just kept on going, but the failure that manifest that cupping at the edges looks exactly like what would occur if it were moisture vapor emission. Yes, moisture vapor emission from concrete is a very real thing.
[00:25:21] And part of the thrust of what I try to teach people is don't wait till you're ready for flooring or roofing to talk about moisture vapor emission. Talk about it in design. And let's go back to your world and concrete world. One of the things that, that, that. The message has been slow to take off is the ready mix industry is that, value add opportunities really can affect the bottom line for ready mix producer.
[00:25:50] This world of moisture vapor emission is one of them. There are a number of products they can be involved with. That those products carry the warranty against vapor emission that can help the ready-mix producer protect themselves, but also add to their bottom line. The earlier you address any issue in a project, usually the cheaper it is as opposed to waiting to the very end.
[00:26:13] It's just, it doesn't matter what, especially like say a design issue. Oh, I didn't want that wall there. Well, that's going to be expensive as you put it, right? Same thing with moisture. If you address it early in design or construction. It changes overall how the whole project can approach dealing with this issue.
[00:26:32] The GC then knows that it's been handled as opposed to, let's wait and see, which could have catastrophic timing and cost implications. So yes, MVE is an issue if not addressed. And there are several ways that it can be addressed. So regardless, GCs, concrete subs, ready-mix producers, if you're on a project that's going to be enclosed and receive flooring, be part of the discussion early on, bring it up.
[00:27:02] So if an issue does manifest at the back end, you can be on record of bringing it up. And then saying, okay, don't now, don't invite us to those meetings about why the force film. Yeah.
[00:27:15] Seth: So you're saying a possible proactive approach would be to give, say you're pricing a project and say, I have a concrete mix that has an admixture in it that can mitigate the MVER.
[00:27:30] And ahead of time, right? Yep. And say, hey, I got a, here's an option for you. If we use this concrete in the area that's receiving flooring or epoxy or whatever, if we use this concrete mix, you can put flooring down in 14 days versus waiting, whatever the flooring
[00:27:51] Dean Craft: We've done exposed roof deck as early as five days for concrete placement.
[00:27:55] Seth: There you go. Yeah.
[00:27:56] Dean Craft: So actually what you said was absolutely 100 percent correct. So I'm going to repeat it because the one thing that I like to try to remind producers it's this is no different than in hot weather you providing your hot weather mix design with a line item for ice.
[00:28:17] I don't think producers give away the ice.
[00:28:20] Seth: No, it's very expensive. So we tell our, that's why we pour it one and two o'clock in the morning instead.
[00:28:26]
[00:28:26] Dean Craft: Cause a company like yours, especially doesn't want to pay for the ice or nitrogen, or we're going to inject nitrogen into it.
[00:28:32] So that's a perfect example. Or let's go to cold weather. They have a line item on there. I can give you hot water, weather. I can give you hot water. I can give you an accelerator. So this thing with moisture vapor emission, I cannot stress enough, and liability comes up, but I, and I want to touch on this for the producer.
[00:28:53] Like you said, here's the line item. Here's my mix for your interior slabs on ground. Here's my mix for your elevated slabs, whether it's a subtle metal deck, whether it's whether it's structural lightweight, whether it's normal weight, whatever to have a line on there. I tease I kind of joke, it's like saying, do you want to supersize that?
[00:29:13] Or you want fries with that shake. It's like, do you want to be able to install your floor on time? Or, have a line item on there that says very clearly, here's the up charge for A, a warranted flooring roofing mix. And then the producer's like, well, we don't want to take that liability on.
[00:29:33] I said, well, that's not the case. That warranty is covered by that admix that provides that product. But look at it this way. If they be, and they being whoever's buying the concrete from you, whether it's the sub or the GC says no, and then later on down the road. A situation manifests where the moisture is not the moisture readings are really high, and I'll give you an example of this what I'm talking about in a second, then when those meetings occur about why they can't sell their floor in time, you can politely decline to attend it for anybody out there to think this doesn't occur.
[00:30:13] I'll give you an example. I will not mention firms. This was in Ohio, a about a 300,000 square foot commercial office building lightweight and it was already like five months behind for flooring. So we talk about cost. Now, the organization that was moving into this building had office spaces all around the city anyway, so they couldn't move their people.
[00:30:38] And then I asked when I present architects, I'm like, how much furniture is necessary for a 300,000 square foot building? What's the lead time? They couldn't take delivery of that material. It had to be sitting somewhere in a warehouse. So in, in logistics, we call that demerge, paying for. Storage for stuff that you can't take advantage of right now.
[00:30:56] So that's sitting somewhere. Those people thought they were moving and now their life is in flux. So the question was boiling down to where it was a very well-known owner in that city. Actually, if I sang the tune, you would know it leaning heavily on everybody was circling around to ask me, what is taking it so long to dry?
[00:31:27] And I happen to be in town talking to that producer. And I said, well, heck, I said, if he goes, they have a meeting every Tuesday, I'm like, well, if they'll let me, I'll go over there and talk to them. One of the saving graces was that producer had offered, just like you said, Seth, they had put that down. They had said, Hey.
[00:31:48] We have an option for you to address the issue of moisture. It was said no. So then I went through and gave part of the presentation, the owner's rep was there, and he paraphrased when I was done, he's like, basically we were I won't use that word, but basically, we had no hope of passing this test from the beginning.
[00:32:11] And I'm like, he's like, so what you were saying is we had no hope of passing this test from the very beginning. I said, Sir, I'm telling you what ACI literature says. I'm telling you what ACI 302.2 says. I'm saying what literature goes back 20 years says. I'm just the messenger. I said I'll send you the base documents.
[00:32:30] I said the concrete industry is known forever and the flooring industry that most likely won't pass this test. So the idea that providing a product like this is going to accrue liability to a producer, I would offer that it will actually do the reverse. So there's an issue where a failure occurs or an issue where it doesn't pass a test prior to installation, which I still see as a failure because it affects the project being able to be completed.
[00:32:58] This would actually help protect the producer or protect the concrete sub should that manifest.
[00:33:05] Seth: How many of those issues are related to not properly testing for moisture?
[00:33:12] Dean Craft: Oh, wow. It's, that's a very skewed thing right there because We can have a whole discussion just on the moisture test itself.
[00:33:21] And let me tell you the main moisture test is called ASTM F 2170. you’re a smart guy. You deal in square footage, think about a building that you've done. Give me a decent size building that you've been on square footage wise.
[00:33:35] Seth: Million square feet.
[00:33:37] that’s a lot. If you're out there, you can visualize the surface area, right? That's a lot, right? The standard says three for the first 1, 000 square feet, and then 1,000 square feet after that. So in that million square foot, you're looking at 1,002, tests, okay? The size of the test is less than the diameter of a quarter.
[00:34:04] Dean Craft: What percentage of the surface area are 1,002 quarters going to cover of a million square feet? Not much. Like 0.000 something percent. The reason why I go through that is because the standard says very clearly the only area being tested is directly at that location. So one millimeter over is not tested.
[00:34:29] Secondly, the result is only valid for the point in time of the test. So as soon as your brain recognizes or registers that result, it becomes old. It's no longer valid. Third, and this is within ACI 302. 2, the Concrete Society, so I guess Britain's ACI, going back as far as 2004, has established that the relative humidity of concrete is not related to the adhesion of resilient flooring.
[00:35:03] So here we have a test that's point in time, less than a diameter of a quarter per thousand square feet. Not related to adhesion. So it most likely not passable because of what the concrete is exposed to. It doesn't really start drying. This was also an ACI. This is an ACI article. Concrete International, this would have been in January 2012, there was a whole article, they did a longitudinal test on how long it takes concrete to dry, they tested for like 13 months in an exposed working warehouse, not HVAC, doors open in the daytime, closed at night and they also did it shortly thereafter, seven months in a completely enclosed space, and Even with seven months going of the RH probe in the concrete, it never got below the levels required for flooring.
[00:35:48] Then ACI 302.2 says it's the last wetting that starts the drying cycle. Well, in that million square foot slab, when was the last wetting? It wasn't until it was enclosed. And even then, what about dew point? If that space didn't become acclimatized, it still went through some wetting cycles. So now, the clock doesn't start until the HVAC is on and you're controlling the humidity.
[00:36:13] That's when the clock starts. very much. So even if the test is done correctly, what relevance does it actually have to a successful flooring install? So for the past 20 years, not related to adhesion. And again another subject we can discuss is warranties. Every product that requires these adhesion tests, or requires these RH tests, in their warranties, they exclude moisture.
[00:36:43] So then what value then, even if you do the test correctly, does it have to the owner of shifting their liability? So it's a whole process thing. It's not just, and everybody wants to go back to the test. So if the test is done correctly, what if it is? It's point in time, exact location. So unless the failure manifests right above that probe, which is highly unlikely, the simple answer is that area wasn't tested.
[00:37:11] So there you go. This is not like C39. This is not like C39 where people build hundred story skyscrapers based on the results of C39. This is not like that. So a lot of times the concrete world thinks about C39 of being an established, accepted. Test amongst other concrete tests, we have the air and slump and things like that the moisture tests aren't like that.
[00:37:33] It's not the same kind of thing. There’s no shift of liability. There's no requirement to perform from those tests themselves. And there's no warranty that then goes back to those results.
[00:37:45] Seth: I think the best way to do it is be proactive and address it ahead of time which is a common discussion point on a lot of the topics we talk about is getting ahead of it.
[00:37:56] if you're doing a job during cold weather, don't you guys have a cold weather plan?
[00:38:01] You submit all that stuff ahead of time.
[00:38:04] Dean Craft: There you go.
[00:38:05] If you're hot weather, well, curing should always be discussed, but, anybody placing concrete that does not go through some kind of curing discussion almost daily because conditions change, wind speed, evaporation rate that doesn't go through that is probably looking for, bad things to happen moisture is the exact same thing. So the concrete world needs to be having this discussion way up front like that. And really benefit from this issue as opposed to leaving to other industries that then turn around and blame you anyway.
[00:38:35]
[00:38:35] Seth: I think Making sure that folks are addressing this ahead of time and not and not being dependent on a moisture test. if you use the right approach or products or whatever the moisture test is, sounds like it's shouldn't even be in a discussion, right?
[00:38:56] Dean Craft: That's the goal. Yep. Yep. So again, process change, process change, you do a process change or product change. If you address it correctly early enough, you can actually eliminate the entire need for the moisture test. Totally change in the power of the GC to keep in charge. And so one of the things I've started talking about is how it changes project delivery and I've had hospital GCs now tell me, so if we address this correctly, we can actually use this proactive approach of moisture as a competitive advantage to delivering our projects.
[00:39:29] That's how powerful this is. That's why the concrete world needs to be upfront and bring it to attention way early on, just like you guys do everything else.
[00:39:39] Seth: So if you heard that and you're interested in learning about that you need to reach out to Dean and Dean, what's the best way to get ahold of you?
[00:39:48] Dean Craft: Well, I can get my phone number right now. You can call me, or I can give my email or how do you want to do it?
[00:39:53] Seth: Oh, that's fine. Or we, I can just share it in the podcast.
[00:39:57] Dean Craft: Please share my, yeah. In podcast notes Seth's fully please share my direct email. Sell an email address would love to hear from anybody out there.
[00:40:06] And if we can assist, be glad to.
[00:40:07] Seth: Yeah. And yeah, so we'll share that info on the podcast notes. And if you have a hard time getting ahold of Dean, reach out to me. I'll get ahold of Dean for you. But Dean, I appreciate you coming on the podcast again. I think this is something that's got to be discussed, more.
[00:40:24] Dean Craft: I love it. Thank you very much for having me back. I'm, I was I was tickled and very pleased and glad to be here.
[00:40:29] Seth: Yeah, appreciate it. And folks until next time, keep it concrete.
[00:40:35]
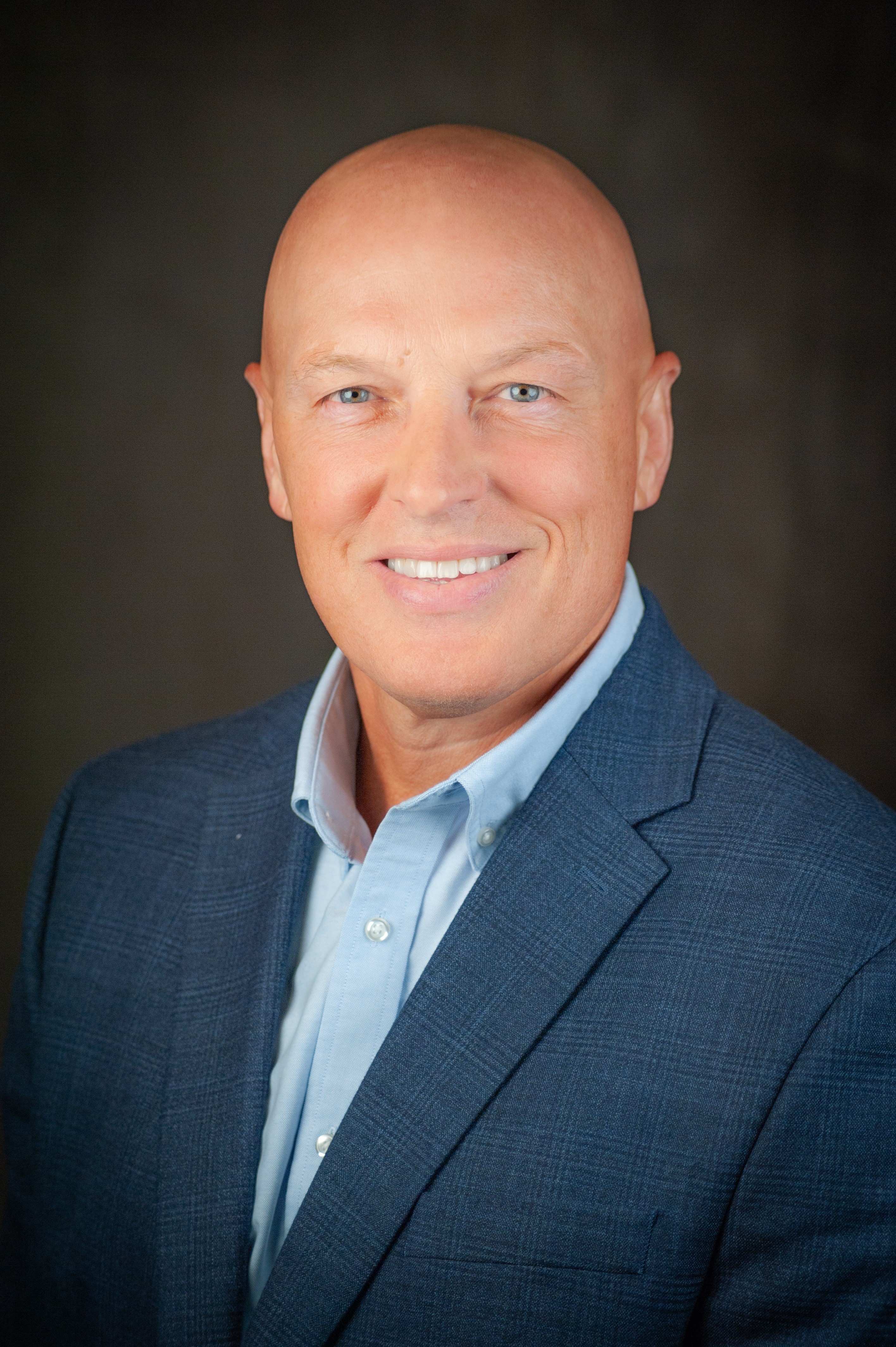
Dean Edward Craft
Principal / Retired Marine
Dean Craft, LtCol USMCR (ret.), DBA, ASTM is a Principal with ISE Logik Industries and a leading specialist in proactively addressing concrete moisture vapor emission issues in new construction concrete and existing slabs that will receive moisture sensitive flooring and roofing. Dr. Craft completed his doctoral work with a dissertation entitled “Fallacy of Current Industry Approach to Assessing Concrete Moisture Before Flooring Installation”. And, as a member of both the ASTM Committee D08 on Roofing and Waterproofing and the ASTM Committee F06 on Resilient Floor Coverings, he is the primary author and technical chair of the following international standards:
• F3191 - Standard Practice for Field Determination of Substrate Water Absorption (Porosity) for Substrates to Receive Resilient Flooring (published 2016)
• F3441 - Standard Guide for the Measurement of pH Below Resilient Flooring Installations (published 2023)
• FXXXX - Standard Practice for Fluid-Applied Membrane-Forming Moisture Mitigation Systems for Use Under Resilient Floor Coverings (currently undergoing balloting)
• DXXXX - Standard Guide for Evaluating the Substrate Surface of Structural Concrete Roof Decks to Receive Adhered Roofing Systems (currently undergoing balloting)