EP #060: Concrete's Lightweight Champion
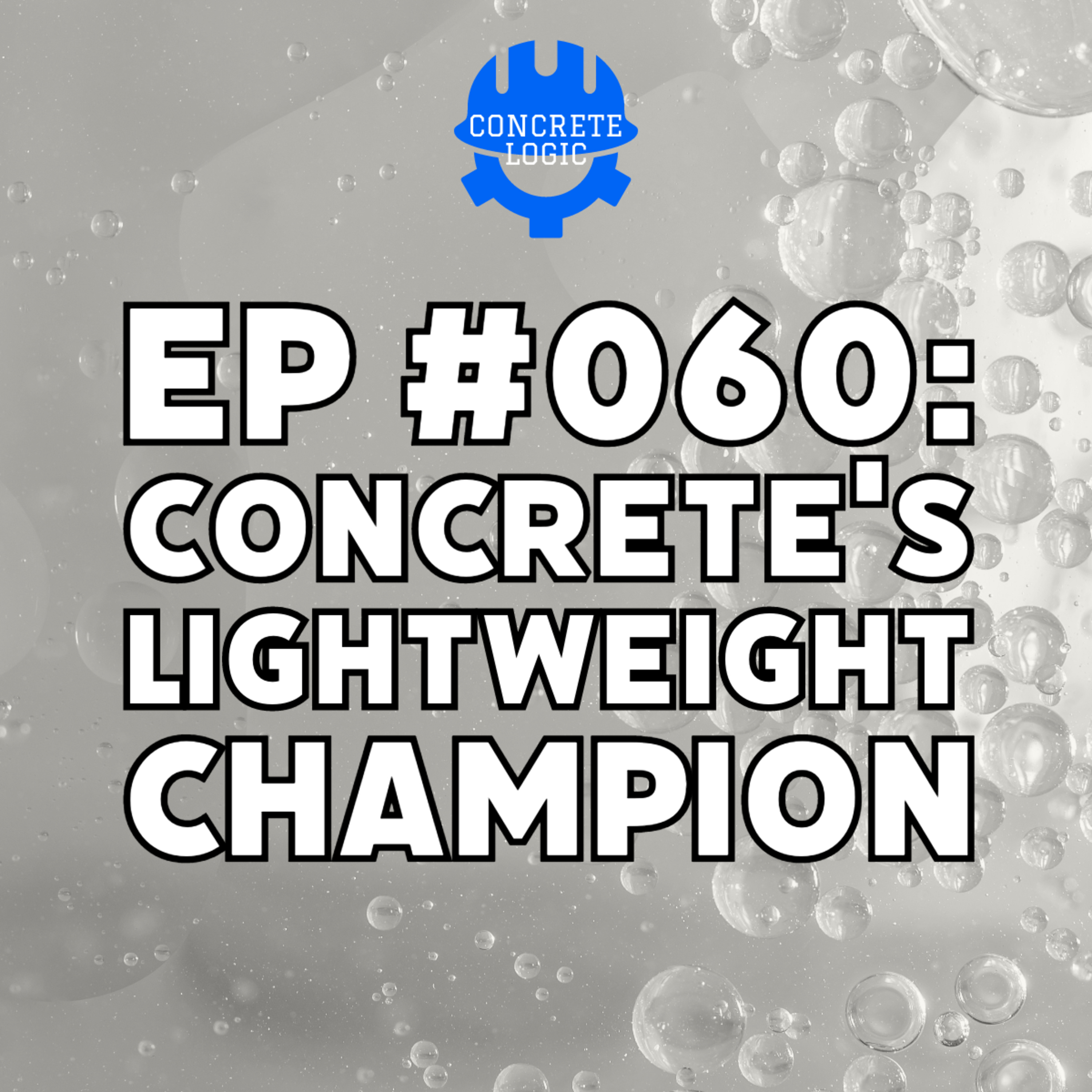
How light can concrete get?
On this episode of the Concrete Logic Podcast, we’re diving into the world of cellular concrete with Kirk Roberts, Vice President of Preconstruction at CJGeo.
In this episode, we’ll explore the fascinating world of cellular concrete. What is it? How does it differ from traditional concrete? And why can’t you just call your local ready-mix guy and ask for a truckload?
Kirk will guide us through the complexities of this specialty concrete, its unique properties, and the innovative techniques used to create it.
We’ll also discuss the guidelines and standards that govern its use, and why a 50 PSI might make a structural engineer balk, but is a game-changer in the world of cellular concrete.
So, if you’ve ever wondered about the future of concrete, or just want to learn about a cool new construction material, this episode is for you.
Tune in to the Concrete Logic Podcast and let’s explore the future of concrete together.
Did you learn something from this episode? If so, please consider donating to the show to help us continue to provide high-quality content for the concrete industry. Donate here: https://www.concretelogicpodcast.com/support/
Episode References
Guest: Kirk Roberts | CJGeo | kirk@cjgeo.com
Guest Website: https://cjgeo.com/cellular-concrete/
Producers: Jodi Tandett, Olivia Stocker, Karl Watson
Donate & Become a Producer: https://www.concretelogicpodcast.com/support/
Music: Mike Dunton | https://www.mikeduntonmusic.com | mikeduntonmusic@gmail.com | Instagram @Mike_Dunton
Host: Seth Tandett, seth@concretelogicpodcast.com
Host website: https://www.concretelogicpodcast.com/
Seth: [00:00:00] And welcome to another episode of the Concrete Logic Podcast. Today, I have Kirk Roberts with CJ Geo. Kirk, thanks for joining the show today. Yeah, certainly. Could you tell us a little bit about yourself and CJ Geo?
Kirk Roberts: Yeah, certainly. So my name is Kirk Roberts, and I am the vice president of pre-construction here.
So I mostly primarily work on special projects and specifically we're a lightweight grouting contractor. So we make. And place grouts that are very lightweight. So as light as 2 pounds per cubic foot up to stuff that I mean, typically isn't the 30 to 50 pound per cubic foot range. And we do it for a lot of.
Primarily lightweight fill, so big, huge embankments of very lightweight material in the vertical and kind of transportation market. [00:01:00] And then we also do. Got a lot of experience working on kind of unusual ground improvement grouting that doesn't really have a lot to do with concrete, but sometimes it can be pretty cool.
So we're like. We'll stop 25, 000, 000 gallon a day leaks in the minds and things like that, but you think of 25, 000, 000 gallons a day is a lot of water. So primarily just pumping high volumes of grout, most of which are really lightweight.
Seth: Yeah, I got a hold of Kirk because we Baker concrete did a project up in Northern Virginia with CJGeo and we used cell cellular concrete and, I was like what is cellular concrete? I didn't know what it was. So I reached out to Kirk and begged him to come on the show too, to [00:02:00] explain what that is. let's start off there. What is cellular concrete? How does it differ from traditional concrete?
Kirk Roberts: Yeah, so cellular concrete is just really lightweight concrete as opposed to a lightweight structural concrete that would be effectively like your typical cement, water, fine aggregate, and then like an expanded shale or lightweight. Coarse aggregate, or maybe lightweight fine aggregate.
If you could imagine if you had a cubic yard of concrete, say at a 0. 6 water cement ratio, and just could magically remove all of the aggregate, and leave bubbles in its place, which is what cellular concrete is like. So by volume, it's going to be as much as 80 percent air.
So it's the cement paste matrix. Surrounding [00:03:00] all of these bubbles and the bubbles are there physically taking the place of the fine aggregate or coarse aggregate, but they're, pretty tiny. They're usually say like millimeter diameter bubbles. So distributed, like fine aggregate would be throughout the uniformly through the material.
Seth: So it's a specialty type of concrete. So you can't call your local ready-mix guy and say, Hey I heard, on the Concrete Logic Podcast about this cellular concrete. Sounds pretty cool. Can you send a truckload over to me?
Kirk Roberts: Yeah, not. Typically not. So there, there are a bunch of different ways to make it.
One of the ways does use the ready-mix supply chain. And on really small volume stuff, say 3 or 4 cubic yards. The way to get the bubbles into the mix is to start with a slurry. So typically 0. 5 to 0. 75 water cement ratio paste. And [00:04:00] then we add the foaming agent, and the foaming agent looks like Barbasol shaving cream or like cool whip consistency.
You mix that in and there are ways where you can just pretty crudely spray the foam into the back of a ready-mix drum. So you may get a load that says, it has 2 and a half yards of slurry sloshing around in the bottom of it, put 7 and a half yards of foam into the back of the truck.
And then just sit there and do a high-speed mix for a couple of minutes and they'll, mix together. But generally your demurrage is increased there. They're not as dimensionally stable because the mixing quality when there's no fine aggregate, it's real hard to get a real good mix between powder and water. So at volume, most of this stuff is made with specialty equipment with like colloidal mixers. And we've got a plant that'll make 200 cubic yards an hour, this stuff on site. [00:05:00] And it's all, but it's all packaged and doesn't look anything like a ready-mix truck.
Seth: I was on ACI this morning and there's actually a guide for cellular concrete which I didn't realize until this morning.
Kirk Roberts: Yeah.
Seth: 523.
Yeah. 523. So it does it, have the same kind of guidelines as a traditional concrete as far as like compressive strength and water cement ratio?
How, do you know you get the good
Kirk Roberts: stuff?
The thing with 523 is it was really written a really long time ago. And a lot of stuff has changed. I don't want to throw too much shade at the committee. Technology is evolving really quickly. So when the guide was written the foaming agents were made with organic protein. So they literally using like cow and pig blood to make these foams. And so if you think if you cut your hand and you go to the sink and wash your hand [00:06:00] underwater, you get some bubbles.
They were, they pull those proteins out of blood and then aerate them and then mix it with paste.
Seth: that's what the Romans did. I'm going back, I'm thinking back to the history on concrete that we did a long time ago. But yeah they, used pig's blood and all kinds of other animal blood.
Kirk Roberts: I guess that gives you your air entrainment really. Yeah, there so though so a lot of the like That was really the only way to make cellular when most of the stuff was written. But as far as there's standards on testing. There's a 1 from there's ASTM.
I think 796 and 869, which talk about like evaluating the foaming agents themselves, [00:07:00] because anybody can make it. You can take Dawn and stir it up with a whisk and some water and have like really nice-looking foam, but can you then take that foam, mix it with, real high alkalinity slurry, pump it have it sit there and be dimensionally stable while the foam set or the paste sets.
ASTM looks at that and effectively has benchmarks to say, okay, this foam meets the requirements of 869 and 796. And then there's another one for C495, which is a lot about sampling on site. QA/QC, that kind of thing and compressive strength testing.
Generally, this stuff is I like to joke when I'm talking when I'm working in the vertical market and working with structural engineers and you say 50 PSI and everyone and the structural engineers are like, oh, that's so weak and everyone's [00:08:00] 50 PSI we would get thrown off site if we made 50 PSI concrete.
But the whole thing is you're not I'm pulling out my trusty T.I. here.
Seth: Is that a T.I.?
Kirk Roberts: It is. Yeah. Yeah. And it's got my wife's Britney Spears sticker on it from high school.
Seth: Oh my gosh. You're showing your age, dude.
Kirk Roberts: I know. No, it's my street cred. And it's got lines on the screen where the pixels havedied, but it still works well.
Seth: I haven't seen one of those for a good 20 years.
Kirk Roberts: Yeah, Old trusty. But yeah, so 50 PSI is really low. But when you look at that from like a PSF, like a bearing capacity perspective, because most of the time this stuff is in place of like soil, or it's between say like a slab and soil. Soil and a wall.
Or just in place where someone may use like foam that only has 10 PSI compressive strength or something like that, then [00:09:00] 72 PS or 7,200 PSF sounds great to a Geotech if you tell a Geotech 7,200 pounds per square foot, they're like, let's build a highway!
You tell 50 PSI to a structural and they're like, where do I start saying no? So the strengths usually are really low in the, like the concrete world. But in the soil world generally significantly stronger than soil that kind of thing.
Where, do you see cellular concrete is, most effective and why?
On the vertical side probably the biggest opportunity really with light with all lightweight materials is there’s the upfront value saying, okay we can make this building lighter. So we've done a lot of work on, and there's a [00:10:00] lot of use of it, say, where you've got the recent project in Norfolk. Norfolk, Virginia, which is the way the whole mouth of the Chesapeake Bay formed is there was a meteor that crashed into it.
Who knows how long ago and flung all of the material out, the swamp was just like before and then a bunch of sand got deposited on top of it. So you've got this layer of just like unbelievably soft material, like there are spots where it may be 50 to 80 feet of peat. That if you were to drop a rock in would just like sink.
So you've got this so all the ground is settling. And so it's okay, the lighter we can make structures, the better. Did a job down there where they were able to do, they did rigid inclusions. It's a ground improvement. And then they said, okay we can only get so much out of this really crappy ground with ground improvement, but we, Thank you. [00:11:00]
The project won't be economical if we do a true deep foundation system. So it's if we can get there with ground improvement, then let's be as light as possible up top so that we can put as much building there as possible. So we brought that site up like six feet with this material. and so the beauty of that is when you're Backfill weighs 25 pounds per cubic foot, instead of, say 125 to 150.
You may be able to bring a site up 6 feet and have a lot more allowable load for a building. So there's opportunity there and then also. When you get away from the coast and start building projects on slopes, one of the cool things about this stuff is when you pour it, it's a liquid, but it's really light as a liquid.
And then once it hardens, which takes six, eight hours, like some, a lot of times you can drive. Like a 25-ton excavator on this stuff the following day. So it's maybe really [00:12:00] lightweight. And in the concrete world, low strength but it's still more than adequate. You build roads on top of it, bridge approaches and things like that.
In the, on those slope site environments, you can say, build a retaining wall and backfill behind the retaining wall with. This material without pushing that wall over or needing to brace it. So like we're getting ready to do a project out in the mountains of Virginia in a couple months where they designed this kind of zigzagging wall through an academic building and said, okay the wall, ultimately the wall is not designed to be a retaining wall in an unbraced condition. Once the floor is poured on top of it, it's braced, but you have to backfill. It's like this chicken and egg thing. It's you got to backfill the wall to pour the floor. It's going to brace the wall that would let you backfill it. So how do you pull that [00:13:00] off? They talked about a couple of things.
They talked about building a mechanically stabilized earth wall with a 1-foot gap. Effectively build like a sacrificial wall. It's expensive and time-consuming.
We also do a lot of work on the remedial side of things, as opposed to the new side of things.
there's a project in the western part of Virginia where there's 1 of those walls that is now moved enough that it's pushing on the basement wall that it was designed to protect. On those kinds of things, they may long term have issues. So here, what we're going to do is they've laid the soil back say, like a 11 vertical to 2 horizontal. So you've got this self-stable slope. And then you just backfill with this material behind it, and you could do a flowable fill too. There's but if you're doing it at 150 pounds for a cubic foot flowable fill mix, or maybe even 90 if you get it real high air entrainment you may only be able [00:14:00] to fill 6 or 8 inches at a time.
So it's you put 8 inches behind your wall, then you let it set. Can you put another 8 inches behind the wall and let it set? Here we're able to fill 4 feet at a time. So we'll be able to fill the backfill, this entire wall with I think 1800 cubic yards worth of material in three days.
So it, it's so light, it just doesn't hardly push on the wall.
Seth: Yeah. That's cool. That's, is that the limitation as, as far as lifts is about four foot at a time. Is that.
Kirk Roberts: standard?
Yeah, so on that one,
At a 4-foot lift, you've got 100 pounds per square foot of liquid head. And so the 1 thing that is. I don't know a lot about how you guys in the structural concrete calculate form pressure, but isn't there the aggregate will do it's not just complete head, right?
There's a d- rating that's based [00:15:00] on some internal friction from aggregate. We don't have anything like that. If you're pouring 25 feet deep, you've got 25 times your density is your lateral pressure. So here, like for this one, we're going to do four feet deep, which will give us a maximum 100 pound per square foot liquid head at the bottom of each pour.
So that I think back to ACI 523, like they talk about two feet thick. Historically the, so the stuff that was made with blood The heat of hydration for this stuff is insane because there's no aggregate, so there's nothing to absorb heat and then you've also got a bunch of bubbles.
So the other 1 of the names for this stuff is lightweight insulating concrete. So you have no heat sink. You've got a bunch of cement that's mixed like really aggressively. You can see [00:16:00] internal temperatures like north of 220 degrees. So it gets real hot.
And with the older foaming agents that are made from blood, that heat of hydration. If the heat of hydration kicks in really before the material will hold it, the cement paste matrix is set to the point of being stable. It'll actually cook those bubbles and they'll pop. And it'd be like if you had a chunk of raw hamburger and you can just do whatever you want with it, but then you go to cook it and you break it in half. There's no pushing it back together.
Sometime lift limits, maybe if you're using an organic foam, you're generally going to have to pour thin just to manage heat. If you're, you may be driven and lift height thickness, just requirements by the capacity to retain it by the adjacent structures. But generally, it's just we'll pour in 1 spot for an hour and a half for 2 hours and then need to move to a different spot because you don't want to move the [00:17:00] material after it started to set.
So we're backfilling a tunnel shaft with it. You may sometimes be able to pour 30 feet deep. Other times, if you're doing 100, 000 square foot pad build-up where you're pouring 2 feet that cover 100, 000 square feet, you're going to pour it 2 foot that 2 foot that can just be bouncing all around.
Seth: Based on the temperature, high temperature concern. Is that right?
Kirk Roberts: No, so they're so most of the hyper outside of the roofing market and flooring, pretty much everything is with synthetic foaming agents now which really are more related to Dawn or like super plasticizers than they are.
There's no organic content. So there you're really just limited by either pouring in one area for one to two hours, or if it's a deep pour, for some reason, if you're up against the wall may only [00:18:00] tolerate. Say, a couple of feet of fill, whereas and to act if you could put 8 feet of material behind a wall in 2 hours, but the wall will tip over with more than 3 feet.
You're only going to pour that kind of thing.
Seth: All right. So there's no temperature control requirements or concerns there with. Okay.
Kirk Roberts: Now, really what it gets into is if you're going to impact anything that's embedded in it. And it real like thin pours. It really isn't a problem. Go But sometimes if you get into, say I had a, an architect calls me a couple years ago now about a project where they had a, somebody filled in a swimming pool out West and then none of the plumbing passed a pressure test after the fact.
If you've got vertical stubs, like coming up to a floor, it's not an issue, but if you've got, say, like a real long horizontal run, the heat of hydration will cause that pipe to get longer. And then anytime you've got a coupling or a change in direction or anything [00:19:00] that's all going to lengthen and then as the Material cures by the time it's hard before the temp comes down. So as the temp comes down and cools that PDC wants to get shorter it's in a restrained joint condition. So then you'll get tension failures at joints. So from a heat management perspective, it's not like a, how's this going to impact the integrity of the material, but just generally what's in this that could be impacted by the heat. Generally, most utilities are, installed after the fact. On this, we're pouring a couple thousand square. It's huge. It's 6500 cubic yards, but only 2 feet thick. So however many square feet that is. On an apartment up in New Jersey right now.
And, and they're there, so we're going to pour the whole thing and then they come in and just try and you can dig through this stuff by hand or with a dingo trench or something like that, just to lay utilities after the fact.
Seth: [00:20:00] Oh, cool. So you could use it as like a mud mat.
Kirk Roberts: Yeah. Yeah.
No, it is real nice because it's also freely draining. So if it gets rained on, the water runs down through it. So yeah, so you can pour it and you've got this real nice surface to work on that you can dig through by hand. You can put rebar benches on top of all kinds of stuff.
Seth: It's like pervious concrete kind of.
Kirk Roberts: So it does have some permeability to it. Yeah. But the permeability for this stuff comes from the fact that, so if you've got material, that's there are two types. There's material that we call closed cell. So the bubbles don't want to touch each other. So they're going to leave like a little film of cement paste between them.
And then there's open cell where the bubbles actually want to come together. And so there won't be a film of cement paste between [00:21:00] many of the bubbles. So they touch each other. And then, so all you've got is that little foam bubble and it's like foam bubble up against foam bubble. And then once the material sets, the bubbles just dry out because they're 98% water.
So it hydrates, it heats up, the bubbles just dry out and then what, so then you've got an air passage from bubble to bubble, and water will flow through those. In the closed cell, when you've got at real low density 25 pounds per cubic foot, you're still going to have about a centimeter per second of permeability.
Water will flow through it, but at the same time enough of the bubbles are closed cells and not touching anything else. They're not touching other bubbles that material will float. It generally has a couple of pounds per cubic foot of uplift capacity. But the closed cell or the open cell material, sorry.
That's going to have 3 centimeters per second and [00:22:00] permeability down at 25 pounds per cubic foot. And you take a piece of material that weighs half the weight of water, throw it in water and just sinks right to the bottom. But
Seth: What's the cost? What's the range that cellular concrete costs?
Kirk Roberts: Yeah, so it is unbelievable. There are huge economies of scale. So it's not you call Vulcan or whatever and say, hey, I need a load of 3,000 PSI concrete or whatever. And it's if you're doing a sidewalk or a driveway or an Amazon warehouse that it's X dollars per yard.
Seth: I don't know if we did a good job or not, but you guys pull up with a truck that actually makes the cellular concrete on site. So do you guys bring in all the raw materials with you? Or does it come in bags? What's that process look like?
And then we can get back to how much it costs. So people [00:23:00] understand that.
Kirk Roberts: Yeah. So generally at scale, it is made onsite with mobile batch plants. So a lot of people think mobile batch plant okay silos, bins, loaders, like all this stuff. If you think back to the ingredients of this stuff, it's really just cement, water and foam.
Also, the foam concentrate comes in chemical totes. So like those kind of 250-gallon pallet milk jugs and one of those will last a day. Usually it's and then the water is just coming from generally a hydrant or if we're working remote, maybe like a frac tank or something like that.
And then you have the cement. So the cement is just brought by tankers. Twenty-five tons here and mid-Atlantic, they're usually 25 tons. Get up to Detroit, you'll get a 50-ton load of cement double tanker load. But yeah, so you bring the cement to the [00:24:00] site and a tanker and the tanker just blows the cement.
The plants are mounted on ready mix chassis. It's literally same footprint as a concrete truck, but just imagine if you had a ready-mix truck that instead of bringing you 8 or 10 cubic yard loads can sit in 1 spot, have 25 tons of cement blown onto it.
And then be making 200 cubic yards an hour worth of finished product out of it. That it's, pretty wild. And then because this stuff weighs so little and there's no fine aggregate, like your pumping pressures are like negligible. So you can pump this stuff at 200 cubic yards an hour, a mile through 12-inch line at like 20 PSI.
Seth: That's crazy.
Kirk Roberts: Yeah, No, it's. It's pretty wild.
Seth: So that's, what it looks like when it's on site. And [00:25:00] what's the cost compared to I get we can talk about what it. Traditional concrete costs, but what I guess what makes sense for cellular concrete as far as a minimum and then maximum, and then give us an idea of the cost.
Kirk Roberts: Yeah, so when you get into big placements, so a couple of years ago pre the run up you used to be able to get cement powder delivered to Manhattan for $95 dollars a ton. Like those days are gone, obviously. Cement is a lot more expensive really for everybody.
So we're still doing stuff that was, like, bid pre COVID. So that the whole everybody getting bit by these like 2019. Pricing 2023 costs and still have two or three years to go on the project. And you're like, oh my God, what's going to, what's 2026 going to look like [00:26:00] some of that stuff, like it was not unusual for this stuff to be installed for like the 50 to 60 a cubic yard range.
Cheap now you get into these like mass pours. You can still be down in the $80-$90 a cubic yard range. But what that's running really light. Because the 1 of the things that we run into a lot is people will say they'll hear 50 PSI compressive strength and they say, oh that's not enough. And I said we need 200 PSI and we run in the tunneling industry. We run into stuff where people would be like, we need a 1,000 PSI route in this tunnel. It's okay you're going to mine this tunnel and it's going to have a one-inch-thick steel, and then you're going to put a ductile iron pipe that's rated for [00:27:00] a direct bury inside that.
do you really need 1000 PSI to fill between these 2 pipes to just keep the 1 from moving? No, but the, and the big driver for that is you get all of that compressive strength and density all comes from the cement and the cement is the most expensive component. So it's we usually advocate for when you're designing this stuff to say, okay, how much strength do I actually need?
What's a reasonable factor of safety and then figure out what density you need. And so a lot of the times what we find out is people would be okay with material that's like not even possible. You can't make this stuff at 15 PSI because it would be like 5 pounds per cubic foot. It would be like, 98 percent air and that just doesn't fly.
As compressive strength requirements increase per yard prices increase, but generally, most stuff is $100 to $150 [00:28:00] dollar a cubic yard in place. If you can get up to a site and place 800 cubic yards a day and just roll with 6 dudes, it's going to be less than that.
we filled a mocked up nuclear reactor 1 time. And it was like 5,000 a cubic yard. But if someone called you if you think about it like from a structural concrete perspective. if someone called you and said I need to do this three cubic yard thing.
It's a three cubic yard pour. It's five hours away from your shop. It's got to be like everything's got to be perfect. And like it's not going to be cheap. It's the same. it's the same thing.
Seth: Gotcha. So there's not necessarily a minimum that makes make sense. It's just because it because your product that you guys provide is so unique and there's so, many unique applications for it that it just [00:29:00] depends.
Kirk Roberts: It does. Yeah. Yeah.
Seth: You're a business development guy like me. That's the thing we say all the time, it depends.
Kirk Roberts: Yeah. And that's another thing we do a lot of work where we're say like working in place of someone using flowable fill. So a lot of, on the utility side.
You may have North Carolina as a great example. So North Carolina D O T says that anytime you take a pipe out of service underneath a state highway, you have to fill it So a say an 8 inch and you have to fill it with flowable fill. You may need to dig it up like every 150 linear feet to get the CLF.
Sometimes guys with the pumpable mixes where you may be able to go like three or 400 feet, but that's really where generally what they end up doing is the sand will segregate out of it and they'll mushroom the road a hundred feet down and they're [00:30:00] running it like a couple hundred PSI.
The beauty of a material that's 80 percent air is you can pump it really, far at these low pressures. The per cubic yard rate. So a lot of times we'll send prices pricing out in dollars per linear foot, because it's like if you tell somebody, oh, it's a, they look at it and they're like a 1000 yards.
I can call Chandler and they'll send me; they'll send me CLSM for $87. It's okay, but so yeah, it's $87 a cubic yard, but you got to spend $5000 a hole every 150 feet.
Seth: And you got to place it, you guys place it.
Kirk Roberts: Whereas like with cellular concrete. You could hook on to your 8-inch pipe here and 28 minutes later have material coming out of the vent 3 quarters of a mile down the road and you never had to dig an intermediate hole.
There's a lot of constructability and like time [00:31:00] in the vertical market, like not having to do bracing thinner walls that kind of thing that tends to balance out a lot, but it usually is significantly less expensive per cubic yard than say expanded polystyrene. So the EPS geofoam blocks and foam glass aggregate. Some of the expanded shale aggregates are less expensive per yard. But if you're going for weight reduction and your material weighs 60 pounds per cubic foot, you may need to have twice the volume of 60 PCF material as you would to with 30 PCF material. So that helps to balance things out as well.
Seth: what do you think about the future cellular concrete use? Where, do you think it's going to be utilized more?
Kirk Roberts: So I think one of the coolest applications in the vertical market and in the civil market as well is Lateral load reduction. [00:32:00] There's a lot of lightweight fill material out there for just settlement prevention.
So it's okay, we're going to we've got underlying compressible soils. So we're going to try to build as light as possible. Where we're seeing a lot of people will get really excited about it in the, particularly in a job at DC a couple of years ago where They did an early procurement package for a parking deck on this big kind of redevelopment brownfield site. So they bought this parking deck and they said, okay, we're going to put the parking deck here and it's going to be the cheapest parking deck ever because it doesn't need to have any lateral load capacity or anything. But they knew that ultimately it needed to have 3rd floor driving access.
so they procure this parking precast parking structure [00:33:00] that could have no earth pressure on it whatsoever. But they knew that they needed earth up to it to be able to drive in and they weren't going to build a bridge. So what they ended up doing is building a 2nd wall, just a sacrificial wall.
They ended up doing is a cast in place, just a pour wall. And then we backfilled that whole thing. And, so they effectively, they saved a ton of money optimizing their parking structure, by designing lateral loads out of it, and I think that's one of the, those are some of the coolest projects that we work on.
It's hey, we've got this wall that we've got a backfill so that we can pour a slab. To brace it, but it's until that slab is there, the wall can't really be backfilled. So it's how do you really gently backfill this building? And traditionally, people have done it with geofoam.
There's a project up in Tyson's Corner that we did a couple of [00:34:00] years ago where we did all the plaza fill with cellular, but they built this thing right up against the slope and it had 10, 000 cubic yards worth of geofoam between the building and the slope. And we tried hard. It was bid back when geofoam was like $80 bucks a yard delivered.
And then before like petroleum prices went up and transportation got sticky. And the site contractor was on the hook to do it. And they just got destroyed. And we tried our hardest to help them out, but the architect was like, Oh, it's too much concrete. It's what's the difference?
It's foam that's made out of cement or it's foam that's made out of plastic. Yeah, so that, that lateral load reduction, I think is, one of the coolest things and then stuff just like mud mats and things where, you know, you may think about flowable fill or Man, it'd be real nice if we could pour our backfill in here. [00:35:00] That kind of stuff.
Seth: I think the application where you're talking about how you can put it down and, you can put equipment on it the next day. it's a neat product. I see a lot of potential.so I'm sure y'all are staying busy like everyone else, at least at the moment.
Kirk Roberts: Yeah. Our biggest challenge now is managing. Our average project size for this stuff is just a couple of days. Sometimes a lot of jobs and you may be there for a month. We drove to San Antonio a couple of weeks ago to grab a tunnel.
It was 3 hours’ worth of grouting and 60 hours’ worth of driving. But it's like one of those things where it's hey we've got to. We could do this with flow fill, but try finding a concrete, a ready-mix plant that's going to tell all their structural customers. Hey, we're not going to do anything today other than make flowable fill for this tunnel. [00:36:00]
And the structural guy is going to be like, go pound sound. We're going to find somebody else. And then, like, how do you get flowable fill to move 750 feet in the tunnel underneath the interstate? Don't. But our, so our big challenge is just stuff getting pushed around. you'll have, it looks like next week's good.
And then somebody who's been confirming. Yeah, we're good. We're good. We're good. We're good. We're good. And they say, we're good on Wednesday and then Friday, they're like, okay, cool. If anything changes over the weekend, let me know. And they write back. They're like, oh yeah, we just had an update meeting, and we don't need you for another two months.
And it's like that's the biggest challenge.
Seth: Yeah. It's a killer.
All right, Kirk. If folks want to reach out to you and learn more about cellular concrete and CJGeo, What's the best way to reach out?
Kirk Roberts: Yeah, so probably the easiest thing is just our website, which is just CJGEO. com
Seth: And we'll share Kirk's email on the show notes as well.
Sweet. Kirk. Thanks for coming on the show. This is great.
Kirk Roberts: Yeah, my pleasure. I really appreciate it, Seth.
Seth: Yeah, that Like I said, I didn't know anything about cellular concrete, so I appreciate your time.
Kirk Roberts: You bet.
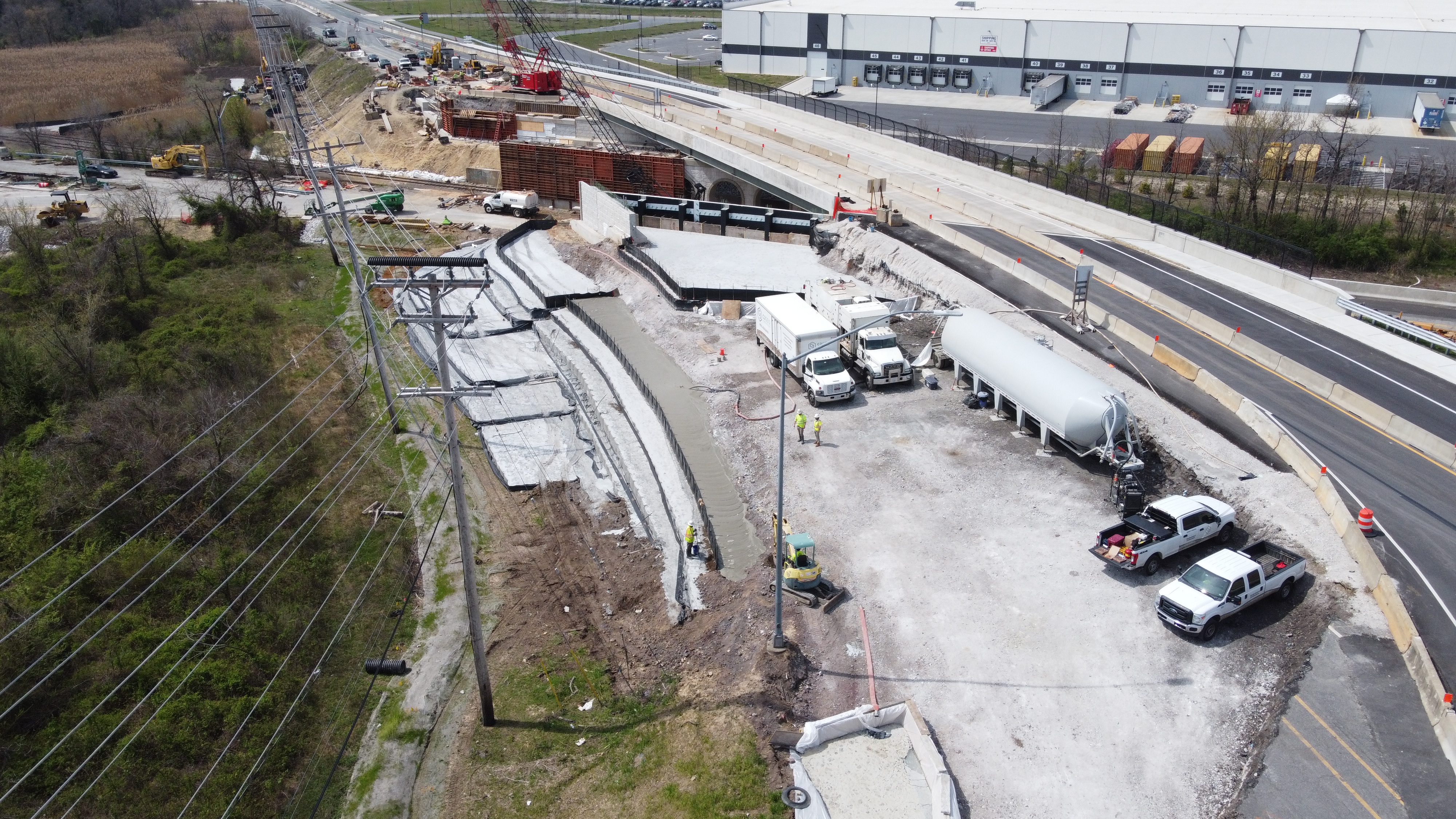
Kirk Roberts
VP, Preconstruction
Kirk is Vice President of CJGeo, a specialty grouting contractor, where he leads the preconstruction group, primarily focusing on special projects. These special projects range from building large embankments of 25lb/cuft cellular concrete to