EP #057: Concrete Chemistry from Cement's Perspective
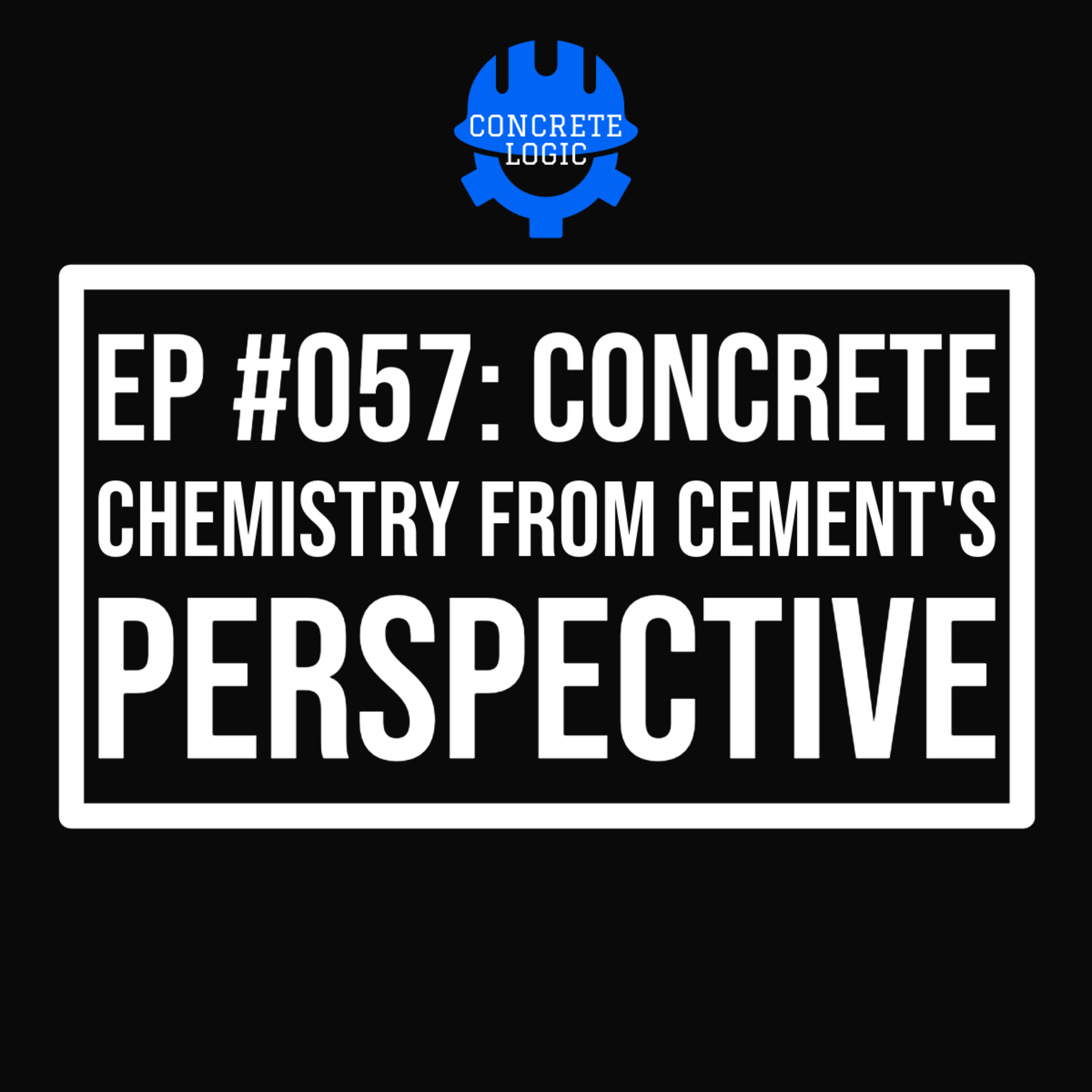
Join us on the latest episode of the Concrete Logic Podcast as we delve into the intricacies of cement production with industry veterans Pete Paone and Robert Higgins.
We’re pulling back the curtain on cement kiln dust, its types, production methods, and alkali content. With over two decades of experience, Pete offers unique insights, while Bob shares perspectives from the ready mix side.
If you’ve ever been curious about the chemistry behind your concrete, this episode is a must-listen. Tune in as we unravel the complexities of cement production and challenge industry norms.
Do you enjoy the Concrete Logic Podcast? If so, please consider donating $5 to support the show: https://buy.stripe.com/9AQ4gP8Mu83Z3045km
Episode References
Guest: Peter Paone | ZAP Engineering | paonep@zapecs.com
Guest Website: https://www.zapecs.com
Guest: Robert (Bob) Higgins | RC Consulting | rcconsulting.higgins@gmail.com
Guest Website: https://www.linkedin.com/in/robert-higgins-b8294411/
Producers: Jodi Tandett, Olivia Stocker
Become a Producer: https://www.concretelogicpodcast.com/support/
Music: Mike Dunton | https://www.mikeduntonmusic.com | mikeduntonmusic@gmail.com | Instagram @Mike_Dunton
Host: Seth Tandett, seth@concretelogicpodcast.com
Host website: https://www.concretelogicpodcast.com/
Seth: [00:00:00] Welcome to another episode of the Concrete Logic Podcast. And today I have Pete Paone. And Robert or Bob Higgins, depending on how good friends you are with Robert Higgins, you can call him Bob. These guys agreed to come on the podcast. They were actually emailing back and forth about the last podcast I did with, with Bob,
We talked about cement, kiln, dust, and alkalinity Peter, reached out 'cause he initially wanted to discuss some points raised in the podcast, and he wanted Bob to clarify some things 'cause I, I only had Bob for a certain amount of time and Bob can only go so far into, his depths of knowledge.
Pete wanted some clarification on the cement kiln dust discussion. It's different types and it's production methods and the, alkali content. within the cement kiln dust, and Pete, just so everyone, I guess I should have said this, but Pete's been on podcast before as well.
[00:01:00] he's got over 2 decades of experience, in cement production. So, what Pete's going to bring to the conversation today is I think he could pull back the curtains a little bit about some of what Bob and I were questioning on the cement side of things.
But at the same time, I think Bob can say, hey, these are the things that we're seeing on the ready mix side of the fence. Pete, we agreed you had pulled the short straw. So, you get to start us off.
Pete Paone: Thanks. And thanks, Bob, for agreeing to this. like I, had said some emails and for the general audience, during Bob's, podcast last week, there was some discussion about CKD and its introduction to cement.
I've been in the cement industry since 2002, and right now I do a lot of training with a lot of different plants who have issues with alkaline materials and need ways to reduce the amount of. I'll say that whether it's alkalized or whether it's chlorine or sulfur, in fact, the last project I worked on two weeks ago [00:02:00] out of the plant was actually dealing with issues related to trying to reduce potassium from the plant.
it's something that I get involved in quite a bit and I think there's a little bit of confusion. and I'll say it's a general confusion industry wide with what CKD is, because, cement plants are built for the long term. The oldest cement plant that I've been to has been running for close to 100 years.
The plants cost a lot of money. They try and. keep them running for as long as possible. it's not like they're up and down and they're out of business very quickly. So, there's a lot of different technologies out there. Some of the oldest technologies out there are these long, dry and long wet kilns.
And, I think Seth, when we had our podcast, we talked about that a little bit. You got a long kiln, might be 4 or 500, 600 feet long. maybe 10, 15 feet in diameter, and, everything comes in one side. Everything goes out the other side, materially wise and all the gas flows. The other way takes a little bit of dust with it.
And that dust [00:03:00] comes back to, to a bag house nowadays. In the old days, it would have been, it's an electrostatic precipitator was what they used to use. basically, they get the dust all charged up. They'd have these, these rods, these electrodes inside the ESP that would get them a little electrostatic y.
And then as they flowed through the ESP, they'd get attracted to different, plates in there, and the dust would stick to them. And they'd knock the dust off and collect it. And with those older kilns with those ESPs, one of the nice things about it is... all the coarse dust gets picked up first, right?
So, the first couple of plates, you pick up all the coarse dust, and then as the gases continue to go through there, you wind up having a, another couple of plates, all your fine dust gets picked up later and later. And there's a chemical difference between those dusts. So, the coarse dusts tend to look a lot like your raw material.
They're not completely alike, but they look a lot like what's coming in. And then further down, the finer dust can tend to be concentrated more, and I'll say some of the nasty stuff you don't want. So, sulfur and sodium and potassium and chlorine and things you don't generally want in your cement.
so, the coarse dust generally gets recycled back in. You can reuse it because it's still chemically similar to what the raw material looks like. If a plant was really trying to drive down their alkaline content, they would waste the fine dust from them, they call them the fields, the later fields in the EP.
So that's how they used to do it. Nowadays, more and more plants have preheaters and pre calciners. So, you have the gases coming from the kiln and out the preheater has a bit of dust to them. The hot gas from that preheater normally gets reused, so they use it for drying off the other materials.
It'll go through their milling system for making the powder that they feed the kiln with, and then you take all that gas over to a baghouse normally to get all the dust out for, environmental [00:05:00] controls. That dust, again, tends to look very similar to the feed, and in a baghouse, you don't have that separation between coarse and fine.
So, it tends to be very chemically similar to what the raw feed is. So that can also be considered CKD. it's the cement kiln dust coming out of the system. There's a third dust that we see in plants. And generally, it's when a plant is either trying to make a low alkali cement or they can't make it otherwise.
Or because they have chlorine and sulfur that kind of recirculate within the system and they'll stick, we call them volatile components. They evaporate in the hottest part of the kiln. And then as they come back through the system, they condense, they stick to the dust. And as the dust comes back into the kiln, they come back in the hottest part, and they boil off again.
So, they form a. A loop within the system and if they build up enough, they'll actually cause the plant to go down. They [00:06:00] choke off all the ducting and they stop the plant from running, to break that loop plants will install a kiln gas bypass. So, they put in kind of an offtake duct. And they pull off a very small portion of that material.
And by pulling off a small portion, they're able to bleed out that material. And they basically make another CKD. We often call it kiln bypass dust as opposed to a CKD, but all 3 of those types of dusts are considered CKD. And they all have very different chemistries. So, for your long kilns, your CKD in the 1st field looks exactly like the kiln feed coming in, gets recycled back to the kiln.
And then the later fields get wasted. they don't normally get returned back into the cement. Normally, those are either landfilled or they get used for some other beneficial use. your dust from a modern bag house on a preheater, pre calciner. That dust tends to be again recirculated back and reused.
The only times that you don't see that dust reused, are [00:07:00] typically if you're trying to bleed out mercury. So that's a more common usage that's become more prevalent in the last, I'd say, 10 years rather than the last 20 years. And generally, since that dust looks a lot like the feed coming in, it's a high limestone, it's got a little bit of inert silica and that sort of stuff.
Generally, plants do try to use that as a cement additive. so, they'll normally, they call that shuttling. they'll shuttle it back over to the cement mill for use. But again, that, that looks a lot like the feed coming in. It doesn't tend to have a very high Alkali content, and then generally your kiln bypass dust.
Everywhere you see that, that material just tends to get wasted. and when I say wasted, it doesn't go back in the process anywhere. You don't take it back in with the feed. You don't take it back. into the cement. There are plants that you have found beneficial uses for CKD. a lot of times, I think, Bob, you mentioned potential use as a soil stabilizer or things like that.
I have seen that, as one of the things that it's used for.[00:08:00] I've also seen it, occasionally used for agricultural purposes. If it’s, it’s got to pass certain testing. You can't just go out and throw it on a farm field. There are regulations in place that say what you can do with it.
So, if it passes testing, sometimes you'll use it for either the potassium or some other content in the material. so, I just wanted to clarify that, that there are different types of CKD. for the most part, the high alkalinity stuff doesn't get turned back into cement. it's going elsewhere.
Seth: And why do they, why would they not use that? do they just know that the high, alkalinity is bad for concrete cement use? And they just police themselves? it's not regulated by the EPA saying you can't use this or by any other regulator. Is that correct statement?
Pete Paone: The big thing, there are regulations for it.
there's a test called a TCLP, T C L P, which is a leachability test. so, you actually have to [00:09:00] test it to see whether or not it, it fails certain criteria for having. I'll say bad stuff leach into groundwater and if it fails a TCLP, it's actually got to be, it goes to specialty locations where it's got to be, treated.
I don't want to say as a hazardous waste. I don't want to misspeak, but you can't just landfill it and put it in the pit and say, we're done with it. So there, there are some regulations concerning it as far as where you can put it for the most part. They don't want to reuse it because they have quality specs to me, right?
You have a limit for how much chlorine you can have in your, cement. You have limits on, there are plants that still do a low alkali where they're trying to hit a sodium equivalent less than, 0. 6%. So, you do have limits. The other big thing is that most cement producers know that those, alkali materials do a lot of stuff to your strengths.
If you increase your alkali content in your cement, your 1 and 3 day strengths will go up, but your 7 and your [00:10:00] 28 day strengths will drop. if you're trying to hit certain targets for 28 day. strength adding a whole bunch of alkali into your cement is not a good thing because it means that now you've got to, increase your C3S.
You got to add a light to it to bring that 28 day strength back up, or you've got to grind finer and both of those are going to cost you money. If you grind finer, you're going to have to use more power to grind it to your cement. Internal cost is going to be higher. if your C3S content needs to go up, you're going to have to burn harder.
It means you need to put more fuel in the kiln, which is also going to increase your cost. you've got not only the, specifications you're trying to hit, you have, you’ve got some things that you want to avoid. You want to avoid those costs of grinding finer or having to burn more fuel.
Seth: I gotcha. How often do they test for that?
Pete Paone: Test the, the, which part? the TCLP on the dust or looking at the chemistry on [00:11:00] the dust?
Seth: How about both?
Pete Paone: You've got to test pretty regularly for the dust that you're wasting. You can't just send it out and be done with it.
So, most plants that I go to, you're testing that dust every two to four hours. Oh, okay. So, you pull it out. Now, there's different methods of doing it. You might have a continuous sampler, or more often than not, you're sending some poor guy out there to, to take a sample in a hot suit, because the meal that you test, the material that you're testing when you do that, it's coming out of that plant at about 1600 degrees F.
So, you're in a hot suit, you've got a long probe and you're pulling out dust that's so hot. It's actually glowing when you pull it out.
Bob, did you hear anything that you want to question?
Robert Higgins: What I was told a few months back, I was on a conference call with the largest cement producer in the world, and the one based out of Canada, they were [00:12:00] boasting how they weren't concerned with the CKD because they're not hamstrung the same way that, that, domestic cement producers are, so they made it a point stating that the,
- S. cement is more, tends to be more alkaline than Canadian cement. And I said, are you shipping that into the country said, he says, this is what we're just doing in Canada because, it wouldn't, they were talking about some other regulations, but I wasn't paying much attention to it. I thought, of course, they don't have to pay attention to the EPA because they're in another country, but.
For them to acknowledge and tell me that the U. S. cement is more alkaline, they added nothing to the mystery or the clarification. And what you brought up about the finer grinding, I've seen that as well. And that's again, the finer grinding has become another issue because some of the grinding aids that they're now using, it’s done specifically to get the blame fineness for the [00:13:00] cement not.
What it does chemically to maybe something later on down the line, because they're adding glycols and amines to the cement grinding aids, and I can't get any information on it. And that's
Pete Paone: getting any information on the grinding aids and use
Robert Higgins: or using, if there's any residue left, I can't get any information on it.
Pete Paone: So, there's a number of different grinding aids that are used and, I'll be careful in how I say this because, I used to work with a couple other chemical engineers and cement and doing design on work and they always referred to it.
Robert Higgins: I'm trying to withhold.
Pete Paone: Yeah, they always referred to it as magic fufu powder.
we're going to add the magic fufu powder to the other powder that we're trying to make and that's going to do some magic and that's going to get glycols and amines have been used as grinding aids for a very long time. Yum. When I started 20 something years ago, as I make myself feel older, we were using DEG and, TEA and all sorts, for your listeners, [00:14:00] those are both, DEG is a glycol, and TEA is an amine.
one of the most basic grinding aids a lot of plants use is actually water. Water by itself acts as a grinding aid. And, for those who aren't really accustomed to hearing grinding aid. When you take the clinker that comes out of the kiln, you get these little nodules that are about an inch in diameter.
You have to grind that down into the cement powder that everyone knows and loves and uses in concrete. That material, as it grinds is very staticky. you start getting the cement powder very, fine. It sticks to everything. it, I could tell stories about seeing people get shocked with how much static comes off as some of the conveying equipment from conveying that powder.
When you're trying to grind the material, the older technology, a lot of people use as ball mills. So, you have a big tube filled with. Ball bearings that are somewhere between an inch and four inches in size. And you split the mill into two chambers, right? The first chamber, you have all the big stuff, all the [00:15:00] grinding media that's between two and four inches in size.
And, it's like that commercial, I pick things up, I put them down. that's what the ball mill does. It picks up the big balls and it literally drops them on the clinker. And it takes that one inch, piece of rock and it breaks it down into something that's probably between, I don't know, like an eighth and a quarter of an inch.
You get some powder in there too, but really that's what you're trying to do. You're trying to get the big stuff broken into big, slightly less big stuff. And then the second chamber, after it's gone through there, you have a screen, that separates out the big stuff and the big balls from the small stuff and the small balls.
That smaller material passes through the screen into the second compartment, and, you have all these one inch balls and smaller that now, instead of getting picked up and dropped, they rub on the material. So as everything's spinning, the balls are spinning, they're rubbing, they're hitting material.
And they, they break it apart, through, abrasion. [00:16:00] So as they, they do that, they're building up a huge amount of static. And what happens is the cement sticks to the balls, and it coats them over like a, a lubricant. So now as the balls are spinning in there and hitting and whatnot.
they're not getting the attrition, they're not getting the grinding because it's slipping past as opposed to breaking off. Makes sense. what you use the grinding aid for primarily is you're trying to, the cement, not to stick to the grinding media. and the way you do that, if you think about it like this, a grinding aid is normally like a soap.
So, it's a long molecule. 1 sides polar, because it's going to want to stick to something else that's got a charge to it. And the other side is non polar, so it's just like how soap helps water, which is a polar molecule attract.
Robert Higgins: Yes, it's price effective in other words. Yeah,
Pete Paone: that's exactly what it's meant to do.
Yeah, the main reason most plants have used grinding aids for the longest time is to help the grinding efficiency use less power. [00:17:00] You don't have stuff stick to it. in newer systems, if you have a vertical mill, so a vertical mill, you have a big spinning table, get a big roller pressing down on the material that's between the roller and the table.
The same thing happens. You get like a buildup of the dust on the grinding elements, on the roller and on the table, which reduces their efficiency. And it's actually a lot worse in a vertical mill than it is in a ball mill. Yeah. Because if it slips. The material starts to plow in front of the roller, and then suddenly it'll just get to a magic height where it all grips together and acts like a big solid, and it causes vibration, the rollers trying to push down, and it's just plowing, and then all of a sudden the roller gets picked up, and it's got all this force that's being pushed down against the table, and it finally, acts like a big cohesive unit, the roller gets pushed up, it's got all this force, it's pushing down, and as soon as that glob of, material goes by, The roller comes down and, bounces pretty hard off the mechanical parts inside the mill and causes a [00:18:00] lot of vibration.
You tend to use grinding aid more frequently on these newer vertical cement mills than you did in some of the older ball mills because you need to. If you don't, you often have issues with vibration in the mill and you wind up not getting the tonnage out of them. Yeah,
Robert Higgins: one of the reasons why I brought that up is because, there's a company's based out of Switzerland, very large company, and they were talking about how on some of the decorative, concrete on the outside, they would get, what appears to be rust bleeding and they, pinpointed it to the grinding age they were using.
So, they were cautioning people that it's still mobile in the concrete, and I thought about that, and I thought. I wonder if that's really an issue with the flowing materials too, because again, I can't get any clarification other than it causes these little rust stains on the top of decorative concrete.
I thought that was very interesting because one of the things about our industry, the ready [00:19:00] mix producers have to divulge what they put in if it's not aggregate water and cement. Anything else they put in, they have to divulge what it is, but I've not seen that from cement producers, if there's anything required as far as how much grinding aid is in there.
do they do an alkalinity test? I haven't seen anything like that.
Pete Paone: Yeah, that I'm not too sure about. I do know that normally you'll, when we talk about how much grinding aid, you're putting in again, the vast majority of the grinding aid that's used in most plants is water. And what I mean by that is normally.
If you look at any of those grinding aids, they remind you normally of like a, almost a syrup. Yeah. So normally when they're dosed into the milling system, you, you dilute them quite a bit. it's normally like an eight to one dilution. Yeah, or 10 to 1, because otherwise it's just so sticky that you can't get it to flow.
yeah, and then beyond that, normally, you're putting a lot [00:20:00] more water in than you are the small amount of grinding aid. it's on the order of you'll have a finished mill. That's got. 100 tons or 150 tons an hour of cement going through it and you're grinding a dosage right is a couple pounds.
So, it's a tiny proportion of what's going in.
Robert Higgins: Okay, a little trivia for everyone and especially anybody's gonna be watching this, they found that, while water is such an efficient lubricant when you're trying to grind things or break anything with silicon dioxide.
They found that when water is added, it takes 17 times less energy to cleave a silicon dioxide bond than without water, than a dry break or dry cleave. I thought that's very interesting. I thought mostly when they were doing saw cutting, it was the lubrication of the water, and it was actually the, efficiency of cleaving the bond of the silicon dioxide that actually helps cause the breakup.
There's some trivia for you. [00:21:00]
So, I love the fact they use water in that because that, to me is a perfect grinding medium, but it'd be really interesting to see how it is for non-silicon dioxide, containing aggregates. I don't know how efficient would be. So, they're the rub.
Pete Paone: The only bad thing is you put too much water in and obviously you're not really grinding anymore.
You're making concrete. So, there's always that fine balance. The other big thing is I'm sure you're aware of is quite often in that grinding process. you generate a lot of heat. And a lot of the reasons that you have water in a cement mill isn't just to, help either stabilize the grinding or act as a grinding aid or anything like that.
You're doing it to keep the heat. and you're trying not to get the temperature to go so high that you, over dehydrate the gypsum. you're adding gypsum into the milling system to act as a retarding agent on your, for your concrete. And, if you put too much water in there, it's not going to help you get the right hemi [00:22:00] hydrate form of the, sulfate.
It's going to cause all sorts of problems with your set times.
Robert Higgins: That makes perfect sense to me.
What the reason why I brought that up and I pinpointed Alkaline CKD, I should probably should have been more specific with that because again, the information I gathered, there was very, it was very nonspecific as far as how much. Each plant will use and how alkaline each one of these are. and you're right, there is a pinpointing of it, alkaline, CKD and there's other types.
But what was bothersome about that and what we've been finding, when you're dealing with concrete, with the, with a premature self des desiccation of the concrete. I believe that the alkalinity has, is probably the major. Conduit in, so to speak, we're causing that self-desiccation towards the surface because, when you add sodium hydroxide [00:23:00] to, to a concrete mix design, for example, as a calcium hydroxide is beginning to form as a, as a
hydration byproduct, then you have your cement, your Portlandite, calcium hydroxide. These sodium hydroxide has an inhibiting effect on the solubility of the Portlandite. And that causes it to not react properly, and in fact, if you get it, if you get a combination of warmer temperatures and higher sodium hydroxide, it won't, you can't.
You can't make it soluble. It will not react. It will actually become partially blocking, for moisture content for the, as yet unhydrated clinker. it's not surprising to me. And then the other thing it does when you have sodium hydroxide and even the calcium hydroxide, as you get a buildup of that alkalinity, you have a reciprocal drop in relative humidity and, they're finding consistently now.
That the top 1 inch of the concrete is [00:24:00] dehydrating down to a point of 50 to 60% relative humidity. And once it drops below 80, cement formation will occur, even if you do have water present, because it will not take it on. So, CKD was contributing to, and I believe it still is, but I don't know how much.
Pete Paone: and that was the interesting thing that I took from your discussion with Seth last week was, quite often. you, you mentioned sodium isn't generally the alkali that I see the most problems with in that, when you see a high sodium coming in with the plant material, a lot of people immediately try and find something else as far as a material source, because sodium is a pain to get rid of, potassium is normally the alkali that people, I don't want to say but they prefer to see in their raw materials because potassium, Is actually a lot easier to get rid of with a bypass.
and a lot of that has some,
there's a much larger molecule. The bigger thing is it's, let me see how I can put this so that I don't completely lose the audience. [00:25:00] you have chlorine naturally coming in with some of your raw materials, right? Chlorine is a key component in salt. So, if you have any type of salt anywhere, you get a little bit of chlorine in there.
Chlorine is one of those compounds that is exceedingly volatile in a cement kiln. you put it into the cement kiln, 99% of it is going to evaporate. And then it's got a low enough, condensation point, or I should say high enough condensation point that 100% of that chlorine just about recondenses in the system.
So, then it comes back up the kiln, it recondenses, it comes back down the kiln, it evaporates, it goes back up the kiln, it condenses, it comes back So it forms this massive loop. So, the rule of thumb, and I'm, going to throw some figures out here. Your kiln can tolerate just by itself, 0. 015% chlorine in the feed, anything higher than [00:26:00] that, and you build up such an incredible loop within the system of this chlorine condensing and coming back.
That it plugs everything off. and that was a revelation when people discovered that back in the 1950s and 1960s, because there were a couple of preheaters. It was a new technology. They started up and then, I'll say the folklore that was shared for me when I first got in the industry from people who were involved in that was, oh yeah, we ran for five days, and we couldn't figure out why the plant kept shutting down.
and it was this massive recirculation of chlorine within the system that chlorine has a natural, affinity for potassium. So, what tends to happen is it grabs onto the potassium in the system, and it treats it the same way. So, if 30 or 40 or 50% of your potassium would have evaporated before.
Now is potassium chloride. It wants to evaporate. It comes back up. So, you see this massive recirculation of potassium chloride. So, when you put in a kiln gas bypass, it's very easy to get rid of the potassium [00:27:00] because any small amount of chlorine you have latches onto it and brings it along for the ride and takes it right back out.
The interesting thing for me, Bob, from your discussion was, you mentioned sodium. I'm curious since we, I don't want to say we like potassium a little bit better because it's easier to get rid of. Does that ratio of the potassium to sodium in that alkali, coming out, does that actually make a difference in terms of what you're seeing?
Robert Higgins: No, actually, potassium and sodium, in hydroxyl form behave very similarly. We're, and it's a strange reaction because, it does a couple of things as it begins to concentrate. I've seen situations where somebody was trying to dry out a concrete floor in the desert, and they couldn't dry it out.
And then when we did an extraction of the concrete surface, there was a combination of sodium and potassium, but it, it was between a 50 to 60 percent, Concentration and we were told it couldn't get to that point. And we, of course, we found out differently [00:28:00] when we did the analysis. I didn't know back then, unfortunately, because we kept trying to input.
We brought in these different companies or drying experts, and they couldn't get a drive. Only in retrospect did I learn that when it concentrates like that, the water begins to behave more like you're cooling it down rather than heating it up. So, what will happen is, the freezing point of water, when it's at a 40% concentration in sodium and or potassium hydroxide, the freezing point of water, goes from 32 degrees up to 59 degrees.
Almost 60 degrees. Now at 50 to 60%, it bobbles around a bit. It can actually jump up close to 100% real, 100% Fahrenheit, or excuse me, 100 degree Fahrenheit, and it'll still freeze. So, it behaves like frozen water. It doesn't, there's nothing acting the way it's supposed to react. So, with the, alkalinity in there, it's reducing the [00:29:00] relative humidity and it's causing the, the, cohesion of the water to increase.
So, it's extremely difficult to get it any drier. And in fact, you can't do it because unless you're drying it down to a relative humidity below 99%, you can't extract any more water. So, we have this. Difficult fight in it, and it basically, it restricts its, its influence in the gradient of the concrete, which is the top 3 quarters of an inch to an inch of the concrete.
I thought, now, under ideal circumstances, what would happen? Dr. Dan Zollinger from Texas, Transportation Institute. Conducted a study under lab conditions, and he took a 4000 PSI concrete and he water cured one for 7 days and left the other one to air cure. Even with the 7 day water cure, when they sliced off the top into the concrete, it had a full, it was a 20% lower in compressive [00:30:00] value than the remainder of the concrete.
Now, I've seen the concrete modified where if they can keep the dehydration from occurring, the strength is actually equal to or can actually be greater. There is a way you can manipulate the concrete and add things to it to get it stronger and get rid of that weakened with. Surface and the big contributor is the alkalinity, because if you look down the road, they talk about when they've done these studies on dam faces and the different angles of the dam concrete, they're talking about concrete hysteresis.
And so, it's unpredictable. it's unpredictable because if you look at all the influences of concrete hysteresis, where the ingress of water. Moisture and ingress of water. Become further and further apart with a diffusion studies and the models don't work anymore. It makes perfect sense if you incorporate these alkaline materials [00:31:00] into the, into this calculation, but nobody's doing that.
I cannot tell you Pete how much I appreciate this information because this closes a lot of information gaps. And there, there's a gentleman by the name of Hugh Howe. I would love for you to give him this information. He's on LinkedIn. He's with West Genie Elstner. This information that you have, I think will really benefit the industry.
Cannot emphasize that enough because he's doing a study when he wants to look at these chemical influences because we've gone back and forth now for about four years. and he's doing a study that's just, I think is going to be a complete game changer. And I would love to see you get involved with this.
Pete Paone: yeah, I can certainly reach out to 'em. To me, again, the things that, that I would find interesting to look at would be, if potassium and sodium, like you said, react very similarly, generally when we look at the alkali, [00:32:00] we look at a sodium equivalent of 0.
6 or less, to make a low alkali product. and honestly, that sodium equivalent means you're only taking the amount of potassium and you're multiplying it by about 0. 658. So if you add your sodium and you add your potassium, you might have above a 0. 6, but because we put everything on a sodium equivalent basis.
Yeah, it knocks it back down. So, I'd be curious to see.
Robert Higgins: Oh, okay. Yeah. Yeah. Because if you look at the critical humidity threshold of potassium and sodium, they're almost identical. And that's how you dictate whether or not we'll cause a dehydration that self-desiccation of the concrete. That's how you can discover that.
Whereas the calcium hydroxide goes in the opposite direction. It gets more soluble as it gets colder. In fact, it's highest solubility point is just immediately above freezing point, but I don't know what it does. [00:33:00] When you concentrate the other alkaline materials, because it makes it, you can't mix it with water anymore.
it won't blend. It just, it's almost like you've, taken it and you've, separated it from the water and it won't, go back into a soluble state until you've reduced the heat and you've removed the alkaline materials. It won't do it.
Pete Paone: the other interesting thing to me would be, and, it sparked my interest when you talked about changes in the industry in the last 20 years.
There's been a big move towards, changing gypsum sources. So, we talked earlier about you have gypsum as a, an agent for sulfate. Yes. Sulfate acts as a retarding agency. Yes. You Seth, you can go out there and you can actually work with the concrete as opposed to just having it set up immediately.
Yes. So, when you make the cement, you're taking the clinker, you're adding gypsum. Now you're adding limestone, as well. You talked about 1L. The gypsum traditionally always came from a gypsum source. It came from a [00:34:00] gypsum mine. The last 20 or so years, there's been, I'll say a big impetus towards using, I'll use the term synthetic gypsum.
So synthetic gypsum is the calcium sulfate that gets formed in wet scrubbers. So as other industries have tried to reduce SO2 emissions, particularly the power industry, they use a wet scrubber and the wet scrubber by nature produces synthetic gypsum. It's making a gypsum in the scrubber and that gypsum rather than landfill it, they try and find a place to put it.
And quite often, cement plants are hungry for materials. And if we can, green up the planet by not using that as a waste, but instead using it as a resource. a lot of cement plants over the last 20 years have started using synthetic gypsum. Now in my line of work, that becomes a nightmare.
Because anyone who's ever handled synthetic gypsum knows that it can be absolutely horrible to handle. Really? Oh, yeah. [00:35:00] Synthetic gypsum can come in with a very high moisture content. We think about SynGyp as coming from like a power plant. But there's other facilities that also make it, if you're trying to reduce an SO2 emission, what you do, and again, for the benefit of your listeners, Seth, you take limestone, you grind it up.
You have a high amount of calcium. It's basically a calcium carbonate. Yes. You slurry it. You. put it with a lot of water. You spray it into a duct that's got a lot of SO2, which causes acid rain. That calcium carbonate latches on to the SO2. It forms the calcium sulfite, so it releases the CO2 but gains the SO2.
It dumps into a big wading pool at the bottom of this scrubber, that's got a lot of water in it, and what you wind up doing is you blow air through it to add oxygen, so you make calcium sulfate. Depending on the way that it's formed, [00:36:00] depending on the pH and the chemistry inside that giant vessel at the bottom, The crystal shape changes.
So, as you're growing this calcium sulfate inside this giant scrubber, you either make these little needle like, crystals, you make the term that some of my former colleagues used to use was potato. They look like clumps. Yeah, there's a huge difference in dewatering because you want to take all that gypsum out.
You want to get the water out. You want to send it on to the cement plant and use it as a, as an additive. You can have a Syngyp come in with 10 or 20% moisture, or you can get a Syngyp in that's 50% moisture. Oh my god. Yeah, so you have a lot of surface moisture. I've seen belt conveyors, right?
It comes on a belt conveyor. It's taking it from point A to point B. The SYNGIP sticks to the belt so hard that as the belt comes around, comes over the idler and comes back, it's still stuck on the belt.
What's the Blaine fineness difference? Because I got a feeling there's probably an issue there as well.
Robert Higgins: It's probably, the finest of this, [00:37:00] synthetic gypsum versus natural gypsum.
Pete Paone: We don't normally look at the, we don't normally look at the Blaine on what's coming in just because it's normally, it's obviously a finer material than a rock hard gypsum. Yeah. but it's almost like a sludge at times.
And what a lot of plants wind up doing is, you get these grand ideas. We're going to replace 100% of our rock gyp with sin gyp, cause it's going to be so much cheaper. And then they run into handling nightmares, and they run into quality problems. Because the gypsum never comes off the belt.
So, you're sitting there saying, we got 5 tons an hour of going in and really, it's 0 because it's just the same 5 tons going around on the belt.
Robert Higgins: Because if you look at the particle size, when you look at the surface area versus mass. the larger surface area versus mass, it's going to be extremely difficult to drive that water out because you're dealing with just a massive amount of moisture compared to the amount of material that you have.
in a slurry like that. I can't even imagine. that's probably an order of magnitude more [00:38:00] water in there and what a
nightmare.
Pete Paone: Yeah, it's a fun challenge. I'll put it that way.
Robert Higgins: Wow.
Pete Paone: We wouldn't call it work if it wasn't hard.
Robert Higgins: I think it's fascinating what you do.
Pete Paone: I try, Bob. I try.
Robert Higgins: I can't wait to keep this dialogue going because, I just love this.
No, I, and I'll, thanks Seth, because I really appreciate being able to see both, I normally see one side of things. I see everything on from the cement plant side until it goes out the door.
And I don't get to normally see how the impact is. once it's out in the field, it's at the ready mix facility, or it's out being, Placed and poured and I've really appreciated the podcast for learning about that side of things.
It's always good to see how the other side lives, right?
Seth: yeah, so I, I don't think we solved our problem today, fellas. I think we just opened the door to more possible issues,
Robert Higgins: but Seth, the information is now available.
So [00:39:00] you can explore it because you can't find information if you don't know where to look. Yeah, no, I did not know where to look.
Seth: Yeah, no, that's awesome. I'm glad. Yeah. I think we in our, in the industry, we all work in our silos and, there's not a lot of this. Talk cement guys have their groups and conferences and they talk and then the ready mix guys have their conferences and their talks and the concrete contractors have their conferences and talk and no one, at least, of what I've seen has built some bridges for us all to coordinate
We're just pointing fingers at each other, trying to say it's your fault. No, it's your fault. We all have our challenges on, what we're dealing with day to day. So, this was great. Pete, for you to share this information, and sounds like we got more work to do Bob, and, maybe look into these others, it sounds like the raw materials that the cement guys could be, part of the issue as well.
And it's [00:40:00] obviously not on purpose. It's just part of their process and them. trying to do better, I don't want to say make more money, but that's basically what it is to make more money to make their processes more efficient is what it sounds like, just like we do in each one of our, sides of the fence.
Pete Paone: So, I think the big focus is, and I think Seth, you would put this in one of your podcasts, the cement industry tends to have a really bad reputation. and maybe that was earned 100 years ago. But you go to a modern cement plant, there's a lot done to try and keep the environmental impact as small as possible.
We do a lot for emissions controls. We do a lot to keep dust down. We do a lot to do all sorts of different things. and I know because I've been involved in, those efforts for 20 years of coming up with novel ideas to, reduce emissions and, make things green. A lot of these approaches are being taken because we want to reduce that environmental impact, right?
Using a Syn Gyp rather than scraping it out of the earth [00:41:00] or seeing the Syn Gyp landfill. that's a, that's something that people push forward to try and reduce our environmental impact. It's not just a dollar sign at the end of it. it's a, there's other driving factors behind it.
Personally, to me, it's interesting to see how that affects others because there's always other levers to push and other things to change and whatnot. Bob, you mentioned that this is not the same cement that it was 20 years ago. It's not the same cement that it was 40 years ago. It's not the same cement it was 80 years ago.
When I was at the, cement industry conference back in May, one of my comments was about, calcined clay. I expect that's going to be the next big thing that people are pushing for here. as much as we're looking at, this is like the next big thing. And the new thing, reading through F.
- Lee's chemistry of cement and concrete, because I've got several copies of it. Unfortunately, because I'm a little bit of a geek, there's references to potter's red cement that was made back in the early 1900s. It was a calcined clay cement with an [00:42:00] OPC blend, which is exactly what we're looking at going back to nowadays.
there was a, I forget who, put it out on LinkedIn a couple of weeks back about, back in the 1940s, pushes to, to reduce pozzolan usage or increase pozzolan usage. it's a cycle, it'll come, it'll go, we'll see new blends come and they'll probably look a little bit like blends that were used.
80 and 100 years ago, just with different goals in mind and different, blames and a little bit more modern way of looking at things,
Robert Higgins: and that my biggest complaint over the past few decades is there's been really a lack of cross-pollination. There's all this great information out there, but nobody's sharing it because everybody wants to point at the other group as being the bad guy.
That's why I'm really glad you brought that up, Seth, because we, this has to be an open communication because we can accomplish so much because.
I'm just going to show you how stupid things are. I was [00:43:00] brought in by a concrete company because they couldn't get the relative humidity of their concrete, which is, had no extra water. There was no excess water in it at all, period. When they replaced the concrete within 30 days, self-contained, there's no bleed water.
There's no, there's nothing. There's no extra water, but they couldn't pass the relative humidity test because. when waters in a case like that has nowhere to go. So, they would do the R. H. probes and be 95% humidity and the architects weren't accepting that and I'm going, That's not a lot of water.
If you look at what it takes to create a hundred percent relative humidity, and one of the, one of the examples I used, if you gave a cubic meter of space, you wanna fill it with water. It takes 264 gallons. If you wanna make it a hundred percent relative humidity, it takes less than two ounces of water.
So, it's not a lot of water to get it up to a hundred percent. So, I said, okay, let's trip this thing then. So I had them add a salt to their mix [00:44:00] design and we were able to engineer it to where it stayed between 80 and 85%, even though they had the same exact amount of water in it. That's how stupid this is.
We brought up the sodium. Yeah, it was a sodium nitrate. Or sodium nitrate, Oh, okay. Because that's what they use in museums. They keep the, these encasements so they don't get spikes in, humidity or drop in humidity. The information is out there. We only have to use it because the concrete that's being produced, it's really easy to make it waterproof and not have these problems.
How much greener can you make concrete if it doesn't break down for hundreds of years? Yep. If we take care of the surface, the concrete will be really durable because there is no pathway for moisture. We eliminate the pathway, we eliminate the damage. It is really that simple.
Seth: makes sense. [00:45:00] yeah, I think, I think this is a good spot to leave today.
And I appreciate all the accolades, you guys, and spending your time here. definitely want this podcast to be a platform so we can do more of this where we have, different. Folks from different industries, and we all share what we're experiencing and figure this thing out. so
To, thank you, Pete. Thank you, Bob, for doing this today. and folks remember that the future concrete's not set in stone. it's our job to shape it. and until next time, Thank you very much.
Robert Higgins: Thank you for having us.
Pete Paone: thanks.
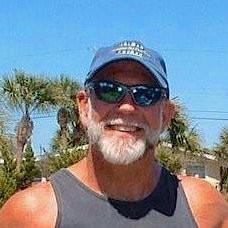
Robert Higgins
Involved with waterproofing and restoration of buildings and specialized in concrete. Have been involved with several committees with professional groups such as ICRI (first chair for moisture testing), CSI, speaking at national and regional conferences, authored the Flooring industry “White Paper” for the WFCA (World Floor Covering Association), moisture test instructor for the Academy of Textiles and Flooring, guest instructor for ICRI. Authored many articles regarding weather and environmental durability of concrete in multiple publications. Currently involved with IICRC Committee S230 and NFCA (National Floor Covering Association) “best practices” for moisture testing concrete prior to installation of Floor Materials.
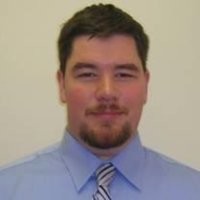
Peter Paone
An accomplished, professionally licensed engineer specializing in pyrotechnology and emissions in the cement and minerals industries with more than 18 years of international experience with Process Equipment, Project Execution & Sales for the Cement/Minerals Industries. An expert in the measurement, prediction, and mitigation of cement and minerals plant emissions. A proven innovator and inventor, with four patents to his name.
Publications include:
High-Efficiency Separator Upgrade: Threading a Separator through the Eye of a Needle, IEEE/PCA Cement Industry Technical Conference, May 2017
Processes for Activation and Manufacturing of Supplementary Cementitious Materials, IEEE/PCA Cement Industry Technical Conference, May 2012
Paone, P., Mercury Control Technologies for the Cement Industry, IEEE/PCA Cement Industry Technical Conference, March 2010
Paone, P., Mercury Reduction Technologies for Cement Production, 7th Colloquia of Managers and Technicians of Cement Plants, Nov. 2009, Malaga, Spain
Paone, P.T., Heavy Metals in the Cement Industry: A Look at Volatile Cycles and Simple Mitigation Techniques, IEEE/PCA Cement Industry Technical Conference, May 2008
Paone, P.T., Blower, M., and Hines, C., The Installation of the New Horizontal, Fixed Grate-Line Cooler at Ash Grove Cement – Montana City, IEEE/PCA Cement Industry Technical Conference, May 2007.
Specialties: Cement process design, emissions abatement, mercury controls