EP #053: Colloidal Silica: Concrete's Next SCM
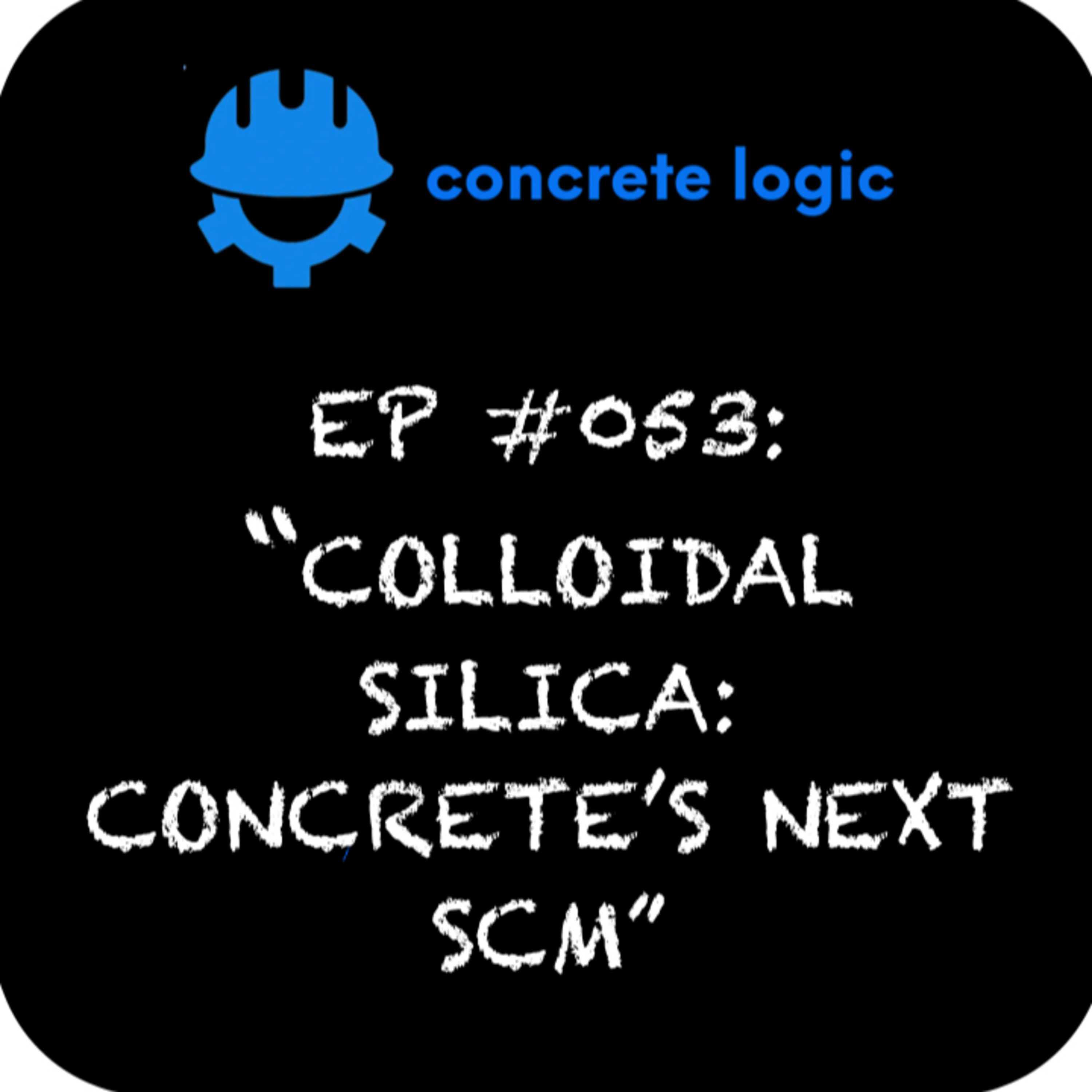
đď¸đ Attention all builders, innovators, and curious minds! Donât miss this episode of the Concrete Logic Podcast where host Seth is joined by the remarkable Dr. Jon Belkowitz, a concrete guru and patent-holder, whoâs here to demystify the world of colloidal silica!
đĄđ§ą Whether youâre a seasoned expert or just eager to learn, buckle up as Dr. Belkowitz, armed with knowledge from his latest Father's Day book haul, unravels the science behind colloidal silica and its game-changing potential in tackling challenges in the concrete construction industry. With Seth asking the âdumb questionsâ for clarity and Dr. Belkowitzâs infectious passion, this episode is a riveting deep-dive that promises to enlighten and entertain. Tune in now! đ§đ
Episode References  Guest: Dr. Jon Belkowitz | Intelligent Concrete | jon@intelligent-concrete.com Guest Website: â â â â â https://www.intelligent-concrete.com/ Producer: Jodi Tandett How to Become a Producer: https://www.concretelogicpodcast.com/support/
Music: Mike Dunton |â â â https://www.mikeduntonmusic.comâ â â Â | â â â mikeduntonmusic@gmail.comâ â â | Instagram â â @Mike_Duntonâ â Host: Seth Tandett, â â â seth@concretelogicpodcast.comâ â Â â
Host Website: â â â concretelogicpodcast.comâ
Seth: [00:00:00] And welcome to another episode of the Concrete Logic Podcast, and today I have another returning guest, Dr. Jon Belkowitz of Intelligent Concrete.
Dr. Jon Belkowitz: Pleased to meet you.
Seth: Yes, sir. Good to have you back. He's a concrete gu guru consultant. He's holder of patents as we've discussed in prior episode.
One of my favorites, by the way, I did ask you, we, I asked the LinkedIn community what was their favorite concrete logic episode, podcast episode. And I modestly picked somebody else's episode, which I appreciate. But I always enjoy talking to you, John, so thank you for coming back to the show today.
Dr. Jon Belkowitz: Heck yeah. It's a great show.
Seth: So today we're gonna talk about silica. I know just enough [00:01:00] to ask some, dumb questions about it. But John has some patents on it and studies it a lot, is my understanding. Is that a correct statement
Dr. Jon Belkowitz: For father's Day, I just got some new books, like Awesome books on Colloidal silica, so Best Father's Day present of the year, and I've already cracked into them.
So I, I do love this stuff and I've been working on it for a very, long time, and it's, solution to a lot of the problems that we have in the concrete construction industry.
Seth: Yeah, I think first place to start, John, is to explain what colloidal silica is. It's a. Co colloid, right? Is that the right way to say it?
So it's
Dr. Jon Belkowitz: so, we could break down the, etymology of the term colloidal or a colloid. It sounds so Russian when you say colloid. [00:02:00] So I, I really do love saying the word but it means a su a suspension of something that normally would be impacted by gravitational forces. Now, there's a range of those particles.
It's normally less than one micrometer. If you don't know what a micrometer is, that's 10 to the minus six, zero 10 to the minus six meters, all the way down to about one or two nanometers, which is 10 to the minus ninth meters. So do, you know what that means? First of all, that scale? No, man. So when I say like, When I say 10 to the minus six uhhuh instead of being one me meter, it's 0.006 zeros, and then the one that's how small it is, right?
When you do a [00:03:00] nanometer, it's a thousand times smaller than that. So instead of six zeros, it's nine zeros, and then it's the one, so when, you look at a hair on a human head, it's around a hundred. Not on your head or my head, but it's, around a hundred thousand to 150,000 nanometers in diameter, right?
When we look at Class F fly ash, class F fly ash, just like in this picture that I'm not showing right now, is around one to a hundred micrometers in diameter. So here's a this is a slide that I often use that when we're trying to compare, what is nano silica in this colloidal suspension versus what is something that we're used to using.
So we're used to using class of fly ash. We know it has a silica content for polan reaction. We know it has a ball bearing effect. It was once used as the poor man's [00:04:00] water reducer all this jazz. And it's very, small. So when we look at under the microscope, this one in particular on the left, this shows Class F fly as, now granted this was from the eighties.
Does it look like this anymore? But this was the ball bearing inducing material that we used in concrete. And to the right of it is this nano silica size particle in a colloidal dispersion. So colloidal suspension, we call it colloidal silica milk is a colloidal suspension of fats and proteins.
So it's gotta be a universal suspension that either happens naturally or we manufacture it that way to keep something in suspension that normally would not stain suspension. Now that can be anything, but for our intent and purposes, it's nano silica sized particles. Does that make sense?
[00:05:00] Yeah, I think so.
Is it could you say it's like oil and water or no?
Can you say it's like oil and water
Seth: just to get an idea of how colloidal silica. We're talking about it's, and suspension and concrete, right?
Dr. Jon Belkowitz: It's really hard if you've never made Italian dressing really freaking hard to keep the oil and the water mixed.
Normally you have to put something in there to break the oil down, like an acid, like a vinegar or a lemon juice. So when you don't do that, the oil pulls to the surface, right? And you have the water below it. What silica will do, if it's not suspended, if it's not a colloidal form, it'll cake up, it'll agglomerate together, it'll cake up, and then it'll fall out of solution and stick to the bottom.
Okay? [00:06:00] So where oil will go to the top, silica will go to the bottom. So colloidal means that you're not gonna have that caking problem on the bottom. It's gonna be beautifully suspended in water and B t w, which is what the kids are saying nowadays. By the way btw save some time. It's a liquid dispersion, right when we're talking Klu silica, it's that liquid dispersion of nano silica sized particles.
It's clear to milky and the larger the particle, the more milky it is. It can have a surface area between 80 and, it's really 2,700 meter square per gram. This is specific surface area, and your particle size can range from really from about 2% solids up to 50. But more often than not, it's 15 to 50%.
Solids. Okay,
Seth: so where does it come from?
Dr. Jon Belkowitz: There's different ways of [00:07:00] making nano silica suspensions. I think the, most the friendliest way I can say it with all the different patents out there is you can either grind sand up really, fine and then suspend that really fine sand in some type of suspension or some type of medium.
Normally it's water or at least a liquid. And then the other way of doing it is growing the particles.
So the other way is getting some type of a monomer that has or, some type of a, basic solution that incorporates a, silica silicate.
Normally we have a potassium Sade, a sodium Sade that we put in solution within acid. We [00:08:00] rip and strip off the, salt. And what happens is the, silica just starts stacking up on each other and growing into these different shapes. The bigger it gets the, shape changes.
So here what we have is this nano silica particle in solution. It grew if you took a string of spaghetti and wrapped it on itself. That's what the nano silica would look like. And that's what this is. It's a spherical ano silica. It's around 20 nanometers in diameter, so it's a nano silica ball, but it's got a bunch of silicone dioxides SiO3, SiO2, sticking outside of it and inside it.
Seth: Gotcha. So it's manufactured.
Dr. Jon Belkowitz: Th there are some natural methods, but they also include a lot of impurities. It's like getting a [00:09:00] a, cabs solve. And, if you like wines, if you get a cabs sauv oftentimes it's not a hundred percent cabs sauv, it's 85%. Then there's a bunch of other stuff in there.
So when you manufacture it, which has a, pretty significant carbon footprint, which is a, necessary evil, especially with how much cement we can reduce from this stuff, and how much durability we can enhance and increase in service life. But when we talk about the naturally occurring ones, they normally come from.
Geothermal juices or other mineral springs where we have a heating process. You have a bunch of minerals, you have a bunch of salts, and they cool and form together. And voila, you have this nano silica, solids and solution. But normally it's with a lot of impurities.
Seth: Huh. And so I, believe listening to [00:10:00] you before talk about the subject and on your YouTube again I'd recommend folks check out John's YouTube channel, Intelligent Concrete. Lots of good stuff there. But I think in prior presentation I saw you mention in the, it, was it the early 2000's when colloidal silica was first used in concrete?
Is that correct?
Dr. Jon Belkowitz: It was late nineties where it was first used. I think the major contribution, and he'll argue with me every fricking time about this, the major contribution was Brian Green's work from the US Army Corps of Engineers, and it was using ultra fine amorphous colloidal silica and a rock matching grout.
So it had nothing to do with concrete, the significant use of nano silica and concrete. I attribute that to Joe Shetterly and specification [00:11:00] products. And to me, he is the real champion to getting this technology out to the masses, getting it out to the ready mix industry. And man, he does it unapologetically.
So yeah the, those are the, forefathers or the, champions or forefather and champion. Of nano silica for the concrete construction industry. And with, Brian, if you read his paper, he wasn't using it to enhance concrete, he was using it as a viscosity modifying agent. Turns out it increased the density to the point that it wasn't just water permeability, it was wave attenuation of nuclear payload or blast loads that were changed to as the title in insinuates, the Rat Rock Matching grout as opposed to the Xantham Gums or dextroses or Celluloses that we had used in the past.
And of course with that, there was a strength [00:12:00] development too, but that's something we can get into here in a little bit. Yeah. And then with Joe Joe Pavements, overlays, bridge work. It's amazing what they're doing at Speck Pro. Absolutely. Freaking amazing.
Seth: Yeah. He was on I forgot which episode number it was, but yeah, we had Joe on here and we we talked about the product a little bit in his background and how he discovered it and he actually used it on his own projects.
Signed his life away to warranty his work and all this other stuff.
Dr. Jon Belkowitz: and he didn't have to he, had a freaking golden parachute. He was good to retire and a very comfortable lifestyle. And he's you know what? Nah. I'm gonna jump into the fire with the frying pan. Yeah.
You did a great job on that interview and talking to him and I think we're gonna [00:13:00] have him on the Colloidal, silica and Concrete Association. But anyway, come on. Let's get into your questions, man.
Seth: Okay, cool. Yeah. So I was sharing with you so I'm, colloidal silicas to my knowledge is not used very much in my area, in the Mid-Atlantic region.
I don't hear people talking about it, and I think it's just because folks don't know what it is or what, how it can benefit them. So we're we're struggling out there with new new, cements, right? LA lack of lack of availability of some SCM's, slag and fly ash and things like that.
And, We are as a industry and we beat this over and over again on the podcast. We're so reluctant to try new things, but this is the one that's one thing colloidal [00:14:00] silica has really caught my attention and I've, ive really would like to see it utilized more and become if it truly is what it is.
And I think it is, cuz I keep studying it and I keep asking folks like you and Joe questions about it. It, just sounds really useful to say the least as a would we would call it an admixture. Is that a correct statement, John?
Dr. Jon Belkowitz: I, think for now that's that's one way of saying it, yeah. There's also a, topical admixture too, or topical additive form of this, so Yeah. But I think Admix mixture in new concrete is fantastic and specifically we use ASTMC Type 4 or ASTMC 494 Type S, [00:15:00] which is chemical admix mixtures for concrete specific standard specification. And that type S is for special performance.
So I think that is put. We are creating a new ASTM for that wk. I, it's either my zip code 80 0 1 0 6, which is either my zip code or it's 89 63. I always get it mixed up with my zip codes, but I'm I'm, on that committee or subcommittee, and we're creating a new ASTM for colloidal silica that matches more like the fly ash standard specification.
More palatable, less barriers to entry and more directed towards the manufacturer and the end user. So the, and that falls under the S scms, so there is a new ASTM coming out for that, for colloidal silica silica for concrete.
Seth: Okay. So it'll be considered an s SCM versus an [00:16:00] admixture and, okay. Gotcha. All right.
I was sharing with you that I came across something recently in a specification about ASR. Which stands for a alkali silica reaction, which is terrible for concrete. I guess the folks describe ASR as the Cancer of Concrete, right?
Dr. Jon Belkowitz: So I've got a, rudimentary drawing here that, that goes over the alkali silica reaction formation, so ASR.
Gel formation. And what we have is many things that we can't get past. Let's just break it down to two things. We have a cementitious matrix, that gray stuff that has alkalies, that has other types of salts in it and moisture and [00:17:00] pores. Ok. Then we have our aggregate, which in certain areas can be a tetrahedron or reactive form with these salts.
Over time, this silica and these alkalies plus moisture combine at the, you see here, this center picture shows the rock in the middle of the paste. The gray stuff. It creates this gel. And this gel, while it's very elastic it, grows at this interfacial zone between the paste and the rock, where there tends to be a lot of pores and it starts expanding and opening in open space and free space, creating these internal pressures.
While these internal pressures overcome the tensile and sheer capacity of not just the cement pace, but oftentimes the rock, and it [00:18:00] ends up cracking the concrete from within because of these internal pressures. Now, once that cracking starts, then you have this influx in this third picture of water and more salts.
And then it's just a vicious effing cycle where mature ring, immature ring of gel and more gel starts cracking. And this scary enough, this can happen within 20 years. It can also happen within 24 hours. I show this picture, which is a, book I wrote a book on ASR.
It's called the ABCs of ASR, and it's a fantastic dictionary on all the things you have to worry about ASR.
. I don't recommend buying the hard cover or the, soft cover get the electronic versions 15 bucks. And the hard cover, which is a small guy like this, is like $135 and [00:19:00] as much of an awesome book it is, I'm not getting the profit.
It's all going to Blurb and Amazon. Get the fricking, the ebook and it'll show you pictures like this where they are. But this is ASR damage on a live structure in the United States. And what you see here is the after effects. Nobody cares about ASR until you start getting issues like this, where you see this gel like stalactites.
Or is that mites Anyway, stuff dripping out of the concrete and that brown stuff is the steel corrosion that you know is caused by the failure, inundated by the ASR. So you have this combination of failures. It's, never it's, rarely ever the ASR gel that causes primary failure. It's normally a, a, something that pushes the snowball down the [00:20:00] hill, right?
It starts the failure mechanism. It's not the straw that breaks the camel's back. It's normally the steel failure. Now that being said, I would call ASR more like the herpes of concrete. Oh, yeah. It's a little bit grosser. It looks like herpes too, or it looks like a cold sore. It's easy, it's gross. It, you normally see it at the surface and. It, shows up in different forms, but when we look at it under the microscope here, this is, it is in Denver, Colorado, right? Where it's been exacerbated by the deicing salts and brines and the wedding and drying cycles. But when ASR damage, when it see it, we, it has a very significant look to it.
And primarily it's these Isle of Man cracks. Cracks that are 120 degrees apart. They look like the flag from the Isle of Man. That's why we call 'em Isle of Man cracks. And they have these salts and gels [00:21:00] coming out of them. But when we put it under the microscope, it really is one of the most beautiful things in the world.
This is an ASR gel roset, and this is under a scanning electron microscope. And I'm gonna zoom into it because as, as nasty as it is, excuse me, the beauty of this. Is where the destructive nature lies. Like it's something from a zombie apocalypse movie looks like a wart. So as we get closer into it, it goes from this bubbly rosette that you can start seeing this fiber wispy like morphology.
And it's those needle-like fibers that create this environment that Ibis or draws more water in, right? These, small pores create a capillary suction that draws in water and salt that creates this vicious cycle of more gel growing, right? And. To stop this ASR [00:22:00] gel mechanism from thriving and surviving.
What we need to do is not only have a a, chemical manipulation, but we also need to have a mechanical and impact on it as well. And that was part of, par part of all my research is how is the impact of nano silica size and surface area mitigating the assr gel polymerization process? And to understand that you have to fall in love with the herpes of concrete.
Seth: But is ASR the, result of. Back of, I guess lack of better words is the, aggregate, the dirty aggregate and the type of cement. It's, a chemical reaction between what we're using now as tho those two materials go. Is, that the. The root [00:23:00] cause of it.
Dr. Jon Belkowitz: So there was, and I'm so surprised I don't have this paper in here, but there was a wonderful, paper written by Katie Barer, Doug Comb Kurt, von Faye from the, Bureau of Reclamation.
And this was back in 2009. And they cited, and I'm, doing this for memory so you'll have to forgive me. They cited three reasons that ASR was gonna become more of a concern in the future. And what's really nice about this paper, like all the conclusions are right up front so you don't have to skip a 30 pages to find them.
God bless them. So the first thing is back in the late nineties we here in the United States had a huge cement production shortage, and we were bringing in a lot of cements from Asia. And these Asian based cements had higher alkaline content. We're finer. We were getting 28 days strengths in 24 hours.[00:24:00]
Now, when we went back to the more Hoover Dam cements that we were used to before this cement shortage of contractors pushed back and said, Hey, we want these Asian based cements or these, higher reactive cements. The problem with those higher rate of reaction, you'll get something for nothing.
You also have a higher alkalinity. So there are cements that we had as high as a 1.76 on sodium equivalent content. And that goes into our ASR engine. That gel polymerization alkalize is what fuels that engine. Now, we were also going through this change of using quality fly ash to Just using fly ash.
There was a huge P2P movement in the early 2000's. I dunno if you remember that, where everybody was using like 40, 50% Class F and class C fly ash thinking they were creating [00:25:00] more durable concrete. As it turns out a lot, what we were thinking is we're diluting the cement and pulling out the alkalies.
And the scary thing is a lot of these ashes, a lot of these supplementary cementitious materials, they had alkalies all their own. And at the percentages that we were bringing, we were kicking ourselves in the ass or, shooting ourselves in the foot. So that was the second thing. We had these higher alkaline cements, finer cements.
And then we're going to these lower quality supplementary cementitious materials that either have cleaning agents on them, they've got higher carbon contents, more impurities or. We just don't have that anymore. Lower ponic materials or lower silica contents. The ashes that we were using years ago, decades ago are a far cry from what we're using today.
I think we can both agree on that, and a lot of our, your listeners will agree on that [00:26:00] too. The last thing is the inevitable reality, and I don't care if you're a Scientologist, if you're Christian, Catholic, Jewish, I, it doesn't matter if you believe the earth is 3 million, 3 billion, 3000 or we're from aliens, we only have so much rock that we can get to on this big blue planet, right?
This big blue marble. We happen to have had some of the best geological engineers or, PGS throughout time helping us build these infrastructure and the structures that we use for our civilizations. You look here in New Jersey, I'm writing a book now called The Concrete on My Block. You know the first chapter is Aging the Concrete based on the type of rock in there.
Cause here in Freehold, New Jersey, we don't sell river rock anymore. For concrete, it's all [00:27:00] crushed rock. But when I run through my, the subdivision that my parents live in, you can still see copious amounts of river rock in the concrete that was made in the twenties and thirties. So there, the reality is, the concrete that was the best to use or the aggregate to use that was the best for concrete, the least reactive.
We've used that crap up and now what we're getting into, especially our sands, is you get what you get and you don't get upset. That's why these technologies like E five nano silica, so gosh darn important because this is the perfect storm. We've got different cements coming in. Our scms are, if you're in New Mexico and Texas, they're gonzo and gonzo California, New Jersey, they're rounding the corner of never coming back.
And ASR is a real thing that's becoming more of an issue faster. [00:28:00] Yeah.
Seth: Yeah. I think yeah, I think that's what I was getting at, was trying to say was the ASR is based on what's available to us now, so we need a, solution to to prevent it. So what I saw in the spec was to offset the amount of cement with an sm to prevent ASR and. What I had was a producer ready mix producer reach out to me and say, Hey based on the availability of, the sems in our area we're, concerned that we're not gonna be able to meet this ASR spec.
Yeah. If, we're not capable of obtaining an SEM to help, that is, is colloidal silica [00:29:00] a a solution that we can use?
Dr. Jon Belkowitz: So we're working in the Western US business unit with a concrete provider that's having that problem where if the D o T would allow him to go to 32% fash, he might be able to get below the 0.1% expansion.
At 14 days might, they won't let him go above 25%. So what we've done is we've used, do you allow me to say product names on this for your listeners? Yeah.
Seth: Yeah. No, I think people can do their own homework. If you hear if, you hear a product on here, do your own homework.
Dr. Jon Belkowitz: And that's the thing, like what works for them in the Western US business unit, you gotta do something different on the east, and that's every freaking concrete additive con concrete's
Seth: a local product.
You gotta do your own testing on what you can get your hands on.
Dr. Jon Belkowitz: And that's one of the things I [00:30:00] wanna comment on, but what we're doing is this stuff is so reactive with asr, it glows in the dark. That's not true. It doesn't clone in the dark, but without ash. Without ash, just straight cement, they're at 0.8% expansion at 14 days.
Seth: Okay. Can you explain if that's good or bad?
Dr. Jon Belkowitz: As TMC 1260 and as TMC 15 67, 1 of the most disputed sets of tests in the concrete industry, it's the accelerated mortar bar test. It's a 14 and 28 day test. It's a one inch by one inch by 11 inch beam set of three beams that are cast with these metal nuggets at the end of them.
And what you're ultimately doing is measuring that bar over the length of 14 or 28 days, [00:31:00] right? This bar is a, bastardized version of your mix. It's not a real concrete mix. It's a mortar mix, right? It's a 440 grams of cement, 990 grams of your granular skeleton based on a, grinding and sitting process.
And a 0.47 water cement ratio. Now, you let that cure for 24 hours. You put in a tap water bath at 175 degrees Fahrenheit. After that 28 days or, excuse me, 28 days, you take a measurement. Then after that 24 hours, take another measurement. It goes into a sodium hydroxide bath for seven a hundred seventy five or at 175 degrees for 14 days.
And over that 14 or 28 days, you measure that change in length. Now remember I said it's in a sodium hydroxide bath at a, I believe it's a 0.4. It's either 0.4 normal or 0.4 molar. I can't [00:32:00] remember. Solution. This is the optimal environment for the alkali silica gel to grow. Now, this is not a real world environment.
It's not realistic because this is called the accelerated mortar bar test, right? So this is pass fail, right? If in that 14 days you're under 0.1% expansion or growth, then you're good to go. If you are working with an airport that same or that same timeframe, or excuse me, that same test is now 28 days, and I think they're using 0.08% expansion.
But ultimately it's an accelerated mor bar test. Okay? Now what you're doing here is you've exposed aggregate surface area, you've created a very porous matrix, and you've given the alkalize or the mortar, the alkalize and the temperatures for [00:33:00] that ASR to thrive and survive quickly. So trying says 8% expansion, that's eight times the legal limit.
Seth: So is that test trying to replicate a period of time? Is that what that's
Dr. Jon Belkowitz: No, It's just really trying to give you a, pass fail. Ultimately what you're supposed to do is, and rarely folks do this, and I'm gonna get a lot of heat for this, is they're supposed to marry that test up to an 18 month test where you're putting the alkalies into the concrete and you're keeping it at a lower temperature at 75 degrees Fahrenheit.
But, You're 18 months instead of 14 days. And who the hell wants to do that test? Yeah. Now there's a 56 day test that's coming out and there's a longer version of that universities run on Treat Island where they're doing [00:34:00] like a three, four year test. So there's different ways of testing, but yeah, the 0.8% expansion without that's very, reactive.
So when we were using 20% Class F ASH with this ReadyMix provider, it was still at 0.3% expansion. So we kept dri or they kept driving it up and at 32% they were 0.11, which, you know, with standard deviation that drops it below 0.1 just by a hair. So what we are going after now, or what we, went after is using the maximum, they're allowed 25% class of fly ash.
With a combination of nano silica from specification products, the E5 Plus, and the Liquid Fly. Now, like I said, the dosages, it will vary based on how much you have to use, how reactive your aggregates are, so and so forth. [00:35:00] So we're using eight ounces per hundred weight of the E5 Plus, and then we're using 24 ounces per hundred weight for LFA.
And that is getting us well below the 0.1% expansion.
Seth: Hundred hundred weight of cement. Is that what you're
Dr. Jon Belkowitz: Yes sir. So you're using this as it was an admixture and the nastier your aggregate, the more of this admixture you have to use cause you're getting those nano silica particles.
Seth: So what are you just doing test and showing that you can meet it by using this colloidal silica with the fly ash. So you're doing the same test? Okay.
Dr. Jon Belkowitz: The accelerated mortar bar test that the Department of Transportation accepts uhhuh, that's the test that we're running with that combination of Class F fly ash and that E5 nano silica.
Seth: And it's a 14 day test. Yes, [00:36:00] sir. Okay.
All right. All right. Yeah. I'm just thinking when we run across this, how long it takes to, cuz usually you're we bid on a job and you get a set of specs and then you're, bidding your pricing based on the specs. Especially a government job. You can't sway off the the specs at the beginning.
So if you get the job and say, Hey depending on what supplier we use, we could possibly use a colloidal silica based on. The products that they can get their hands on. Cuz not every producer uses the same Right. Materials.
Dr. Jon Belkowitz: I, wanna push back on that a little bit, and I guess this is a question or me really a statement and a question for you.
I've been on plenty of, government projects, whether that's building a taxiway [00:37:00] for an active runway or it's normally pavements and then there's pie lasts, and then there's parking aprons when the proverbial, S I H I t hits the fan and they're not getting ash anymore.
The, engineer of record that we worked with on plenty of these job sites wanted a solution. They, would not move forward if there wasn't something in there taking care of a known issue, not just with the ASR. But a lot of these other issues like oxy calcium oxychloride formation, it relies on the same mechanisms that the ASR gel relies on.
Chlorides or chlorides, hydroxides, alkalides permeability and moisture. So if you can fi solve an ASR problem, more than likely you're gonna solve other problems. And, to piggyback on that, let, can I just show a [00:38:00] project that we ran on an airport?
Seth: Yeah.
Dr. Jon Belkowitz: So this was something that was you, the first commercial application of nano engineer concrete in the us.
This is something that we did as part of my PhD work with the Army Corps, with Lafarge North America with Eagle County Airport. It was an awesome job and one of the ready mix providers that I worked with back when I was in the industry, was having a problem that the concrete that we, they were using not only was it not setting up, they were having time set issues, but what they had to do to get it to set up in time was causing durability issues.
And they were ripping and replacing concrete a lot sooner than they had attended. And, this is published in Concrete National, if you wanna go there and see the results. So ultimately they were trying to get 3,500 psi [00:39:00] 24 hours. This taxiway was in front of an air rescue facility, so you know, they had to be able to take off in 24 hours with their, almost looked like emaps.
Just these huge fricking vehicles, these firefighting vehicles. So a lot of powder, low water cementitious ratio. The reference mix is on the left. The nano silica engineered concrete is on the right. And ultimately we had to use at least 20% class F fly ash. So for the nano silica mix, we took it from 20% to 19.5 cuz that's 20% class fash.
And the engineer felt comfortable and then we used 0.5% nano silica. We ultimately could reduce our higher range water reducer, and that's something that we find with nano silica is that they increase the efficiency of everything around it. We not only did hand placement of this pavement, but we also did a slip form paver.
And again, we're trying to re achieve [00:40:00] 3,500 PSI in 24 hours, 5,500 at 28 days. So slump was one of their biggest problems. Every time they got to the job site, it was only a 15 minute drive, but because it was on a runway, We had to do a lot of security sweeps. So it took them about 45 minutes to get through security.
So ultimately it was at 60 minutes when the slump just started dying off. So they ended up having to piss it up to, excuse me. They ended up having to increase water to get it to the point where they could do hand placement. With using the nano silica, we were able to increase our, slump evolution or slump life so they didn't have to include water With that and with the use of nano silica, we saw a significant increase in our cementitious efficiency through strength development.
Before they were using this, they were increasing their cementitious content by more than a sack and a half, and they were using 2% non [00:41:00] chloride accelerators to get the strength in 24 hours. And again, please bear in mind, this is Colorado in the winter. So very unforgiving, the mortar bar at 14 days using the nano silica.
In addition to the mix, just like we did, or excuse me, replacing the class of fly ash, I apologize. We're able to meet and come well below the requirement for the accelerated mortar bar expansion. As you can see, what they were using, even though they were using 20% class of fly ash, fly ash was changing.
It was in 2014. We didn't really know how drastic it was, or the industry didn't understand it at this point, but we had to wait to release this data until they can start increasing their ash content and start meeting the grades. But ultimately what we did is we came back seven years later and, what we did is part of the PhD [00:42:00] was comparing conventional concrete to this nano silica enhanced concrete.
So seven years. We came back to look at concrete that was placed the same day in the same wheel path by the same contractors and how it was impacted by the abrasive environment with the non chloride accelerant or with the, chloride based. The icing salts we used mad chloride as well as the heavy traffic.
And you can see the moderate to extreme surface wear. We got exposed aggregate and they didn't have to pay for it. With the standard concrete and using the nano silica little to no surface abrasive wear. And then when we zoomed in on it, you can see where the aggregate is showing through, and then you can still see the burlap the burlap lines that you get that are being drugged behind the paver.
And again, these were both placed on the same [00:43:00] day. Wow.
Yeah. Yeah.
Seth: That's cool. I'll have to actually post this on our YouTube channel so people can see this. It's good stuff.
Dr. Jon Belkowitz: Oh, heck yeah, man. Heck yeah. Yeah.
Seth: So it sounds out of that example, what I heard was on top of the ASR concern you were able to address, it looks like you reduced the amount of high range water reducer as
well.
Dr. Jon Belkowitz: We did, but if you looked at the mix that was already a rich man's golf course. Okay. They were using 12 fluid ounces per hundred weight. The water cementitious was 0.35. This is when we were still starving mixes. And, this came off the heels of this granola road patch that I had designed.
So 12 fluid ounces per hundred weight. They didn't need that much to begin with. It [00:44:00] was because it was setting off like a bat outta hell that they were putting that much in there and then adding a little bit of water and it was blowing it back up so they didn't have to use that much, but
Seth: okay. So maybe that wasn't a, benefit of it, but what
Dr. Jon Belkowitz: you'll get that there's some wonderful research by Constantine at a University of Wisconsin, and he's the guy who introduced that concept that nano silica does increase cement efficiency or the efficiency of poly carboxyl style high range water reducer.
So that is a fact.
Seth: Because to my understanding it, basically fills in the, voids and concrete. Makes it more pumpable. Is that a good way to explain it to us laymen?
We're not. Can I show We're
not Dr. We're not Dr. Jon.
Dr. Jon Belkowitz: No Can, I, I have a picture that gets into, do you mind if I show that
Seth: picture?
Yeah. Sh show that, show the [00:45:00] picture and I'll try to explain it.
Dr. Jon Belkowitz:
Seth: Cause you, you made that before you get in there, you were making you were trying to explain to it. I thought it was on here. Maybe it was a previous conversation, but it's it's like ball bearings together,
Dr. Jon Belkowitz: yeah, so there's a few things that we get from nano silica, but then it's also a nanoparticle. So what you were talking about is something called particle-to-particle packing. That's a, void filling thing where there are these really, small spaces in between hydrated components of concrete that there's water in and, we can't get ball bearings into if that's what we're gonna steal.
Ball bearings. Yeah. Nano silica itself, or any nanoparticle, if it's really hard and it's some reason it didn't react, if it gets in those [00:46:00] spaces, it's going to pack those spaces and absorb the catastrophic forces that would cause ultimate failure. So, that's what you were talking about.
But when we're targeting nano silica specifically, and I, really wanna be specific to nano silica, if that's okay. There are three things that we care about. And there are, I tell you, you asked me for some papers yesterday. I have an entire folder called "Awesome Silica Papers", and I didn't wanna scare you and send all 200 papers.
And, that's the thing for the audience, when you start looking at new technologies Seth said, all of us have to do our homework. The great thing about nano silica is that there are so many flipping papers, even if you wanted to ignore everything that Jon Belkowitz did, which, hey, I ignore a lot of what Jon Belkowitz did, and proof in the pudding so I can [00:47:00] learn something new.
And I'm reading a paper on nano silica every single fricking day. I have a bunch of them on the floor right here. So there is a copious amount of information out there that really gets past the question of, has this been done before? Has it been done on different ashes, different cements, different in, yeah.
Yeah. Everything that you could possibly ask. It's been done with nano silca. So there's three things that we care about. One is, Since it is a silica, since it's amorphous, it will react in the classical way that we know is called the pozzolanic reaction. But because it's so small and because the force field over it that keeps it in suspension is small, right?
That pozzolanic reaction happens instantaneously. There's a wonderful paper that was written back in 2012 by Land and Stephen that talks about this [00:48:00] instantaneous pozzolanic reaction that they refer to a calcium silicate hydrate seeding effect because it happens so fast that normally wouldn't happen with silica fume, Class F fly ash or anything else that's in the micro realm.
Now the other thing that we get from this nano silica, because reactions start happening so fast the cement, the parent material, wants to dissolve more. It wants to liberate more calcium in the solution to give us calcium hydroxide for this ponic reaction, this instantaneous pozzolanic reaction and this calcium silicate hydrates seeding effect faster and a higher rate of cement dissolution compared to grinding up the cement finer.
And BTW. When we [00:49:00] grind the cement up finer, we have a tendency of keeping the same cement efficiency that we create a, hard candy shell and M&M hard candy shell, where not only we do, we grow our phases around the cement particle and into solution. But we grow a diffusion barrier that M&M hard candy shell into the cement particle, even if we grind it up fine.
By using nano silica, with all these reactions happening faster, our tri calcium di calcium silicate, our A-lite, our B-lite. Our fricking soccer ball of cement dissolves so much faster. There's a wonderful paper written by Bjorn Strom Etal from 2003 2004 that goes into this in detail adnauseum.
The last thing that we get from this, it's a really fancy schmancy term. It's called heterogeneous nucleation, [00:50:00] which means even if we have spent up all the pozzolanic reactions, we have no calcium hydroxide in the localized area of the silica. To convert over to calcium, silica, hydrate. Even if we have exhausted the pozzolanic engine, because the nano silica is nano and because it has this really small force field on it, and I drew a picture of it, it will have something, see here on the left, it shows a micron size particle in solution.
It has this really big force field a nanoparticle, it just can't have that size force field on it because it's so much smaller. It's a higher specific surface area. Because of that smaller specific surface area, because of that smaller force field, it will have something called heterogeneous nucleation, which is a [00:51:00] really fancy schmancy way of saying because something is small, other things will want to grow on the surface so that calcium silicate, hydrate.
It will interact with this nano silica and it will want to grow on the surface. And then we'll have more germination of this thing that I keep referring to, this calcium s silicate hydrate, which is the backbone of concrete strength. I love nano silica, man. Damn, that's good stuff.
Seth: So increases the strength,
Dr. Jon Belkowitz: it increases the production of calcium silicate, hydrate by monopolizing water, calcium hydroxide.
And in doing so, strength is increased. And what we already talked about, durability is increased, but where increasing strength by increasing the cement efficiency. So what they've done in Indiana is they've been [00:52:00] able, and this is what Joe talked about, they've been able to reduce their cementitious concept content by backs.
Yeah. Not by 3%. By a ridiculous percent.
Seth: Yeah. Cause you're, like you said, you're, it's making the cement that you're using more efficient, so you're, able to use, less. How's it I guess it wouldn't matter if we're using Type IL then, cuz Type IL is basically you're cutting, some cement out of there, adding limestone to it.
So d does the nano silica kinda it, doesn't care about the limestone. And,
Dr. Jon Belkowitz: Oh it does. It does. It does. Okay. This is why I go back to product names cause hey man, there, there are a bunch of folks out there that [00:53:00] produce nano silica. In suspension and there are a bunch of folks out there who produce something in a bottle that they claim as nano silica.
And that was one of the things that I wanted to make sure we attacked in the specification that the, b bs products out there that weren't nano silica. We had a way of, shedding light on what was real versus what is fake. But not all nano silica is created equal.
The reason why I work with Spec Pro is that they have made this process of using nano silica a lot more palatable for the industry, a lot easier to start using it and a lot more cost effective too. Did that answer your question? I feel like that answered your question.
Seth: Yeah, no. I think yeah, I think you answered it.
So we're using it on the cements that we have [00:54:00] today. And again we, gotta emphasize that just because Jon used it in Colorado and had great results, we still need to do our own testing in our in our local area with our local
producers.
Dr. Jon Belkowitz: Wait a second, Jon didn't just use it in one plant at one Jon's
Seth: the, example that we went through years, I'll clarify.
We went through an example of the, your first time using it, your first time using it in Colorado. So just to clarify anyhow there's gotta and, you're so you're coming, you're working on a standard. So we all can compare whatever colloidal, silica product that we are electing to use we can put it against the standard and, make sure it's meeting.
The standard. That's one of the [00:55:00] things that that folks are working on to make sure that we're getting quality colloidal silica products would, I guess with anything that we've, we discovered that it seems to be fantastic and, we want to use it. Is there a threshold of, the amount that you can use?
and then you, then it becomes detrimental to the concrete,
Dr. Jon Belkowitz: especially when you are using nano silicas that really you're just folks taking it off the shelf. Part of my, PhD and God bless the US Army Corps for paying the majority of it, it was to understand not only how nano silica can help concrete with ASR durability, but what was the backend of the curve.
When did it start going bad? And when you look at, I think it's either chapter three or chapter four, that was an entire year and a half dedicated to figuring [00:56:00] out what could go wrong and Yeah, man, just fly ash, just like poly's. If you use too much of it, bad things start to happen. There's, a point though where you're like, okay, I'm spending too much money.
This is too expensive. And that's normally what you reach. But shoot, there are DOT's that have used nano silica blindly, and I'm not trying to be a jerk and calling anybody out, but man, I really want to that against the, better consultation with us and the judgment and the, advice that we gave them.
They use an nano silica like silica fume, and holy moly, they're putting 10, 20 gallons per cubic yards to get 6% solids. I don't even know how they got that in the mixer. And of course their results were horrible. The, reason why you work with professionals like the folks at Spec Pro who have [00:57:00] put in the investment on identifying the best type of nano silica, how to use it, all that shtick is you get past all the bs.
It's the same reason why I worked with CHRYSO, with my high range water reducers back in the early 2000's. Lou Cook knew what the hell he was doing when it came to marrying up the right polycarboxylate to the cement chemistry and the, sequencing it was a lot more palatable and easier to get Ws working with that than all the other high range water reducer providers who would say, Hey, this one works with any cement in the world.
You just have to change up the dosage, which was bs right. Yeah, I did wanna show you something else besides that one job site that we did in Colorado. We also did other work with
Seth: you only [00:58:00] used it, the, that, that first time and that
Dr. Jon Belkowitz: one time. That one time. So this is from some of the work that we did with the US Army Corps.
And like I said, there are so many fricking different ways of testing ASR gel. One of the hardest things to do with ASR gel is, look at the gel in an undisturbed state. Any time that we look at the gel using petro analysis, it's normally from an accelerated mortar bar. We cut the bar in half, we put it in epoxy, we polish it, blah, blah, blah, blah, blah.
And then we put it under the microscope. But effectively we are destroying the gel, right? Before we look at, this is a test that we ran with the US Army Corps and it was using a British test that I just flip in love. It's called the B S 79 43, the [00:59:00] ASR gel PAT test. And what you're doing is you're, creating this little pervious puck of mortar that allows water and salts to go through it.
And you're doing that with your reactive aggregate and just enough paste to cover the surface. Okay? You're putting that puck in a, cement porous solution bath at 125 degrees Fahrenheit for 72 hours. And then you do an area fraction analysis of the amount of gel. And if you look at these pictures, the white fuzzy stuff is the ASR gel.
And you do that under two microscopes. So what I love about this test is it allowed us to see you. Remember before I showed you that ASR gel roset under a microscope, it allowed us to see what the nano silica was doing to the ASR gel morphology or the structure of the ASR gel. And before I told you, it [01:00:00] was the needles that create these really tiny pores that draw on the water and salts.
And you can see these on the left here. The ASR gel with using the nano silica. We've changed that up. We've changed up not only the structure of those, that fiber or that wispy like morphology but we've also changed up the pore space. So we increased the, diameter of those needle-like fibrils as they're called, of the ASR gel.
And in doing so, we increased the the, space between those needles. And what we also do is change up the viscoelastic properties the the, elasticity of the gel too. So again, it's not just a chemical approach, but this mechanical approach is, it's not gonna imbibe as much water. When it does try to expand, it's not going to be able to [01:01:00] expand.
And if I have it in here, I don't have it in here. I'm so sorry. What we also did is a chemical analysis of the gel and we found out that the gel on the right had left soluble alkalies in it and more silica and the gel on the left that nasty gel had less silica in it and more of those soluble alkalines.
Seth: Bad stuff. The bad stuff, yeah.
Oh,
cool.
I
Dr. Jon Belkowitz: find this stuff absolutely amazing because understanding the why behind the, nano silica having a positive impact on durability is extremely important. Based off of what we understood and how the nano silica interaction with the hydrated cement matrix [01:02:00] monopolizes and dominates salts led us to our work with Jason Weiss at Oregon State University on how the nano silica has a positive impact on calcium oxychloride formation reduction.
And Jason's own words, it's nano silica is more effective than any other s cm out there in reducing that calcium oxychloride formation. You gotta check out that flipping
Seth: paper. Yeah, I got you. Dr. Jason Weiss is on my list.
Dr. Jon Belkowitz: And it goes back to, and he's another person you gotta have on your podcast.
Jason ir, Jason Weiss are, two. I would say Jason IR is one of the most brilliant minds in alkali, silica reactivity alive today. There's also Maria Younger, Kevin Foyer, and of course [01:03:00] Kimberly Curtis from Georgia Tech. And then there's I, there's the list goes on, but I, would definitely say Jason IR is number one that you should probably talk to about the future of ASR and Concrete.
He's also the guy that writes a lot of these standards up and he flipping hates the accelerated motor bar test. And then Jason Weiss Jason Weiss created the test for calcium oxychloride formation. He literally created the freaking test that we use today. So yeah, he's, both of them are flipping.
Awesome.
Seth: Great. I think dude, we covered a lot today. That number, we haven't covered everything though. We have it and I, think we need to maybe pause to for today and then we'll have to circle back again and, we just, [01:04:00] I think we just barely cracked open your book of colloidal silica, cuz I still have, I don't even think we touched the 15 questions I had on here.
No, but it was all good information. I, so I guess to surmise is this, is, this is a product this is an another SCM solution, right? That could Help us reduce the amount of cement that we're using and also has some other benefits to it, to the concrete as far as durability. Is that a good summary of what we covered today?
Don't go any further cuz we're, I would, we're gonna come back.
Dr. Jon Belkowitz: I would just flip it. I would flip it. Okay. I wouldn't put cement reduction as the number one. Okay. I think this solves, to me, this solves our SCM issue whether or not it's, I have a crappy SCM that I need to get a little more bang out of, [01:05:00] or dude, I don't have any SCM's.
Yeah. So I, think that's the number one thing that it solves that all the other stuff that you said is absolutely right, but right now, when it comes to ready mix providers and what's on their mind there's also carbon footprint, blah, blah, blah. Yeah. I think durability and sems is huge, man.
Huge. Yeah.
Seth: Yeah, that is huge. And now I, understand why Joe calls his product Liquid Fly Ash. It makes more sense to me after our discussion today, so thank you for that, Jon. I will always point everyone to Intelligent Concrete and your coffee talk is 10:30 on Thursdays on LinkedIn, is that right?
Dr. Jon Belkowitz: We have three of them. So one is on Wednesday, then the other's Thursday, Wednesday, it's Edyston. Thursday it's Intelligent, and Friday it's Colloidal Silica and Concrete Association.
Seth: Oh, okay. Cool. I have to check Friday's out. [01:06:00] And then you want folks to visit you on YouTube. Of course you got hundreds of videos on YouTube.
Good stuff there. Any, anything else you wanna share with us today before we leave?
Dr. Jon Belkowitz: I've learned that in our industry there's only two ways of getting people to participate and that's buying them peer beer and pizza or getting them pissed off. So for your listeners out there, this is a call to action.
If this anything in this pissed you off, I am excited and looking forward to working with you. On the opposite end, if you got really excited, I'm also excited to, to try this out with you. This is a new technology. You should be a naysayer cuz that's how we progress in our industry. So call it to action.
Let's get to work y'all.
Seth: Yeah, thank you Jon. I appreciate your time today and we'll do, we'll definitely do it again.
Dr. Jon Belkowitz: Awesome sauce.
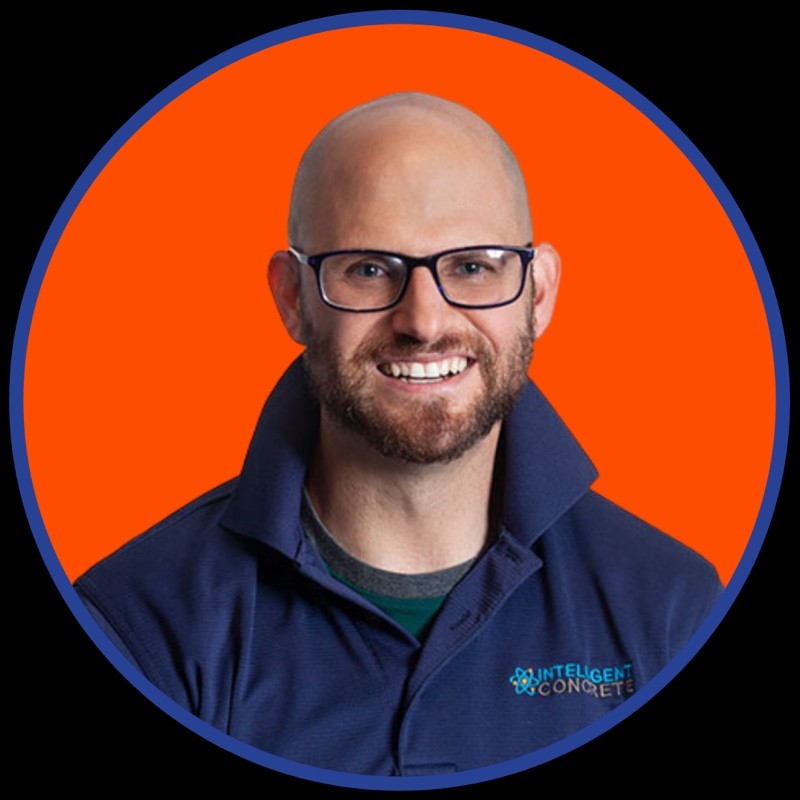
Dr. Jon Belkowitz
Jon Belkowitz is the CEO of EDYSTON, LLC and CTO at Intelligent Concrete, LLC. Before Intelligent Concrete, LLC, he served in the United States Air Force from 1996 to 2006 specializing in Civil Engineering. His tour of duty introduced Dr. Belkowitz to a wide variety of concrete types and uses which were dependent upon the engineering practices of different host nation forces, developing nations, and disaster repair initiatives. Jon has worked in private laboratories on structural engineering and materials development projects to include the application of nanotechnology in concrete. Dr. Belkowitz has worked as a consultant on projects in the United States, India, Turkey, Africa, Italy, New Zealand, Australia, and Germany. Jon has worked as Chief of Materials for a 3D concrete printing firm, an advisor for NASA on 3D printing of concrete holds patent applications on 3D printing with concrete, and is an ACI member on the subject. Jon received his Masters of Mat Science from the University of Denver and his Ph.D. in Mechanical Engineering with a specialty in Nanotechnology in Concrete at Stevens Institute of Technology in New Jersey. Jon is a licensed Professional Engineer in Colorado and Maryland.