EP #045: EPA NOx Out Concrete
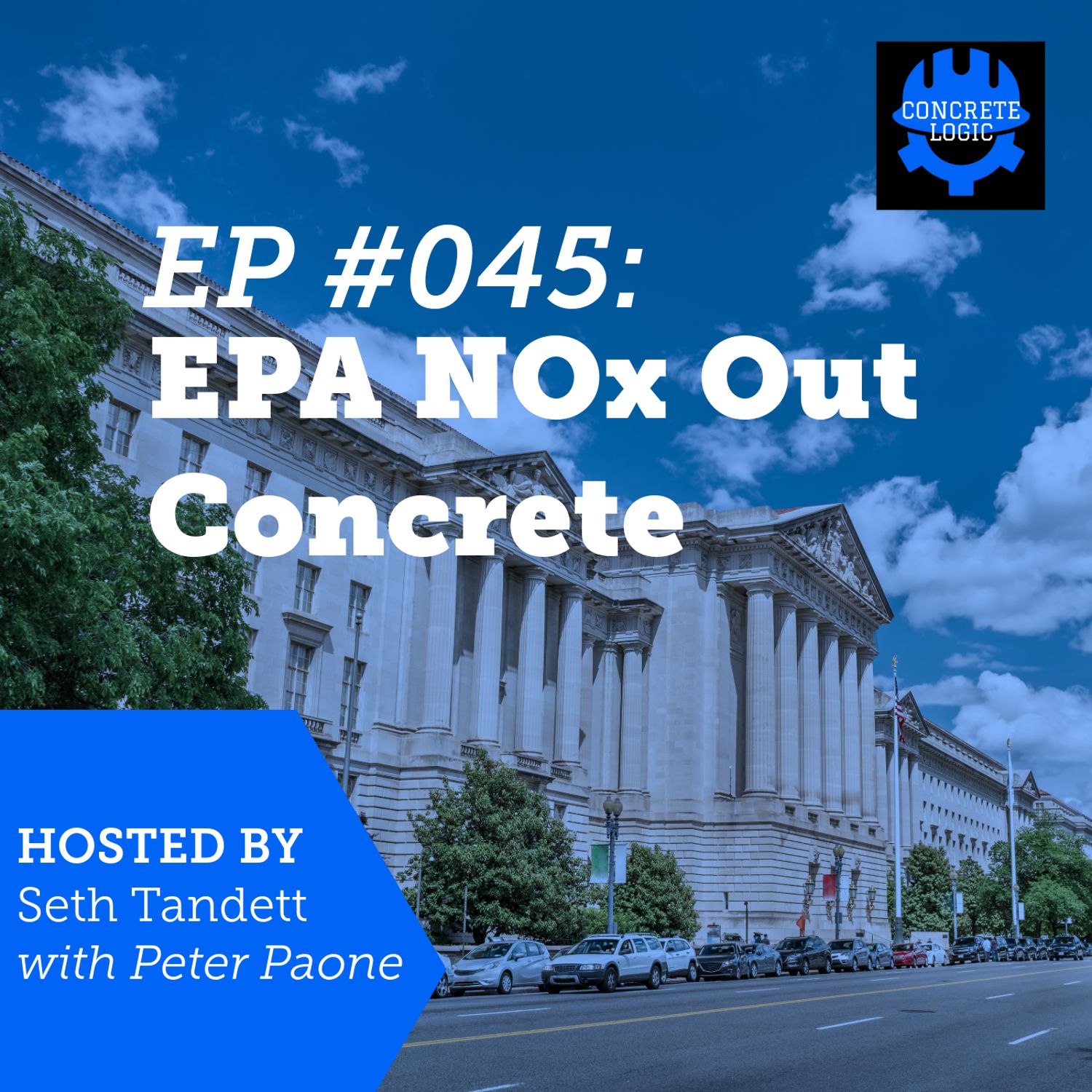
In this episode of the Concrete Logic Podcast, host Seth sits down with Peter Paone, Director of Engineering at ZAP Engineering, to discuss the cement manufacturing process, regulations surrounding NOx emissions, and technological innovations in kiln designs. Peter dives into how the cement industry is addressing both efficiency and environmental concerns, specifically focusing on the "Good Neighbor" rule, which impacts NOx emissions from cement plants. They explore how emission control methods have evolved over time, the complexities of government regulations, and how various technologies help reduce harmful emissions while making cement production more efficient.
Takeaways
- Understanding NOx Emissions: Learn why NOx emissions are a concern in cement manufacturing and how they contribute to ground-level ozone, a key factor in air quality regulations.
- The Good Neighbor Rule: Discover the role of the EPA’s "Good Neighbor" rule in regulating NOx emissions from cement plants and how it affects various states differently.
- Cement vs. Concrete: Get clarity on the difference between cement and concrete, and why cement is the focus when discussing emissions.
- Cement Kiln Types and Emissions: Learn how different types of kilns, such as wet and dry kilns, contribute to NOx emissions and how newer technologies reduce these emissions.
- Fuel Types in Cement Production: Explore the shift from coal and pet coke to natural gas and alternative fuels in cement manufacturing, and the impact on emissions.
- Emission Control Technologies: Understand how technologies like SNCR (Selective Non-Catalytic Reduction) and SCR (Selective Catalytic Reduction) work to reduce NOx emissions in cement plants.
- Innovations in Cement Kilns: Gain insight into how preheaters and pre-calciner designs help improve energy efficiency and reduce emissions in cement manufacturing.
- Recycling Waste Materials: Hear about the use of alternative fuels, such as tires and rice husks, in cement kilns to reduce both waste and emissions.
- The Evolution of Kiln Efficiency: Learn how innovations in kiln design have been driven by cost savings and environmental goals, not just government mandates.
- Industry’s Commitment to Sustainability: Understand the cement industry’s efforts in sustainability and reducing its environmental footprint without relying on regulation alone.
Chapters
00:00 - Introduction
02:29 - Good Neighbor Rule
05:03 - Ground-Level Ozone and NOx
08:51 - State vs. Federal Regulations
12:09 - Cement Manufacturing Process
15:40 - Kiln Types and NOx Emissions
19:26 - Innovations in Kiln Design
25:43 - Emission Control Methods
30:31 - Cost-Driven Efficiency
34:34 - Alternative Fuels in Cement Manufacturing
39:42 - The Role of Sustainability in Cement
43:27 - Closing Remarks
***
Did you learn something from this episode? Would you like to support the concrete industry's favorite podcast?
If so, donate at https://www.concretelogicpodcast.com/support/ .
When YOU donate to the show, you will be listed as a producer of the next episode that is released!
Join the Concrete Logic Academy!
Enhance your learning from our podcast with engaging quizzes that test your knowledge and help you earn Professional Development Hours (PDHs). Support Concrete Logic and take your education to the next level! 🚀
FIND OUT MORE HERE: https://www.concretelogicacademy.com/
***
Episode References
Guest: Peter Paone | ZAP Engineering | paonep@zapecs.com
Guest Website: https://www.zapecs.com/
Producers: Jodi Tandett, Kevin Korchmaros
Donate & Become a Producer: https://www.concretelogicpodcast.com/support/
Music: Mike Dunton | https://www.mikeduntonmusic.com | mikeduntonmusic@gmail.com | Instagram @Mike_Dunton
Host: Seth Tandett, seth@concretelogicpodcast.com
Host LinkedIn: https://www.linkedin.com/in/seth-tandett/
Website: https://www.concretelogicpodcast.com/
LinkedIn: https://www.linkedin.com/company/concrete-logic-podcast
Why join the Concrete Logic Academy?
You get access to:
- Hands-On Video Courses
- Live Q&A Sessions
- Collaborative Projects
- Live Podcast Recordings
- Concrete Library
- Professional Development Hours (PDHs)
Learn more: https://www.concretelogicacademy.com/
Seth (00:05.485)
And welcome to another episode of the Concrete Logic Podcast. And today I have Peter Paon, Director of Engineering from ZAP Engineering. Peter, could you tell us a little bit about yourself?
Peter Paone (00:20.41)
Sure, I've been working in the cement and I'll say related minerals industries for the last 21 years. I graduated from Lehigh University here in Bethlehem a long time ago with a degree in chemical engineering. And I went and I started working for a company called FL Smith, which is a Danish company and they supply equipment primarily to cement plants. So I had experience doing engineering and doing process design work.
kind of fitting all the pieces together in these plants that make cement. And I'm sure all your listeners know cement, not concrete. So all the kiln systems, all the milling systems, I would help design a plant for a certain production and for a certain type of cement. And then I had a unique opportunity because I'd go back and forth between designing those plants and then commissioning them. So I'd go out in the field, discover all the problems with them, and try and get them to actually run.
And then I'd come back and I'd normally switch back and forth between designing new plants and doing research and development on trying to make them better. And a lot of my focus on my last couple of years there was actually on emissions control. So things to reduce NOx and SOx and mercury. You know, a lot of these different emissions that the EPA, you know, tries to cut down on from cement manufacturing. And I left there in 2012 and I've been doing consulting work in all sorts of different
Peter Paone (01:51.071)
quite a bit of work with pozzolins and calcine clays and whatnot, but I'd say most of my focus over the last 20 years has been on cement.
Seth (01:59.605)
Nice. Yeah, so we connected via LinkedIn, of course, because I reached out to our followers, our Concrete Logic followers, after I read this article that was in ENR about, here it is right here. I'll just read the title here.
Seth (02:29.605)
and final good neighbor rule. And, uh, I was like, Oh, what is this? So I started reading about this good neighbor rule. And, uh, apparently this is a something, um, that, uh, has a, has a focus on reducing the, the NOx emissions. Um, and they, um, um, specifically called out, uh, cement, um, manufacturing or cement plants, and that got my attention.
So focused on carbon emissions that I guess I wasn't paying attention that we do things like to reduce our NOx emissions too. So I was like, Hey, we're just, we're just now trying to figure out how to reduce our carbon emissions. What's this new thing? And as I read through it, it's not new. It's something I guess, and Peter, you can correct me here, but it seems like this is something that we kind of, the EPA looks at.
looks like every five years or so. Is that, is that a correct statement?
Peter Paone (03:33.53)
Yeah, the most people have probably heard of the clean air act, which is really the law that tells the EPA that they have to go out and they have to periodically make adjustments to the rules to try and improve air quality. So one of the key things that they are told that they have to go and improve, it's not actually NOx, it's ozone. And probably a lot of people are familiar with the ozone hole. So they're aware of ozone from that.
and the ozone layer in the atmosphere is a couple miles up in the air, you know, up in the upper atmosphere. What the EPA and what most people are more concerned with is ground level ozone. Ground level ozone, if you have asthma, you know, my wife and my daughter both have asthma. Sometimes you see those ozone alert days when you're getting the weather report in the morning. Ground level ozone, you know, can cause some serious health effects for people who are
who have difficulty breathing like the elderly. And it's not normally just found. Normally ozone on the ground level is created by really complex chemical reactions between a bunch of different pollutants. And NOx is one of those key pollutants. So the reason that the EPA gets into regulating NOx from these sources isn't because of the NOx itself, it's because it's a precursor. It's something that creates ground level ozone.
Seth (05:03.567)
I gotcha.
Peter Paone (05:03.89)
So that's why they get into regulating it. And it's really an alphabet soup. And what I mean by that is there's all these different regulations that kind of lead one on top of the other. So when I do training for people, I do training for the Portland Cement Association, when I do training for cement plant operators and environmental engineers and those sorts of people, I talk about the alphabet soup of all these regulations.
Seth (05:06.547)
I gotcha.
Peter Paone (05:33.55)
AQS, five letters, National Ambient Air Quality Standards. And what those standards say is you have to maintain a concentration of ground level ozone below a certain level. So when I was growing up, that figure was up around 100. And over the last, I'll say 20 years, that number has slowly been brought down, down to 90, down to 75. Sometimes you'll hear about things like
and attainment areas. These are areas that are either in compliance and actually meeting those targets or they're not. So most people are probably familiar with what these regulations mean by your inspection stickers, right? One of the things that the states do is if they have non-attainment zones for ozone, they try and get vehicles off the road that emit more NOx,
and things like that, and they do that through the emission stickers on trucks and on passenger cars. So that's one of the results of those standards that you're now seeing that we're talking about as far as applying for for cement and power plants.
Seth (06:49.505)
Right. Yeah. Each state has their own standard, right? So the, and the EPA is kind of the umbrella over it. Is that a-
Peter Paone (06:57.41)
Yeah, it's kind of strange how it works because the EPA doesn't issue permits. So when you have a cement plant, it's not the EPA that issues the permit for the air. And particularly for your car or for your truck, when you're driving down the road, you're not getting a permit sticker from the EPA. The EPA basically empowers all of the state governments. So if you're in Pennsylvania, like I am, or if you're in North Carolina,
submit a plan to the EPA telling the EPA how they're going to achieve compliance, how they're going to meet these standards. And one of those might be saying, look, in these counties where the ozone level is too high, we're going to have inspection stickers, we're going to have emission stickers on cars. And in these other counties where we're not worried about it, we're not going to do those stickers. So that's part of the plan that each state puts together to tell the EPA this is how we're going to achieve compliance with this new limit that you have.
Seth (07:58.385)
But they can, can the EPA tell, I was again, trying to understand these standards within this, uh, can the EPA say that their standards are not, I guess, to the highest or to the level that they want. And then they overrule their, their standard is, is, is that going
Peter Paone (08:22.71)
I don't think we've seen that yet. The states individually will go to the EPA and say, here's my plan to achieve it. And this good neighbor rule that kind of started all this discussion is really one of those ways of, I'm trying to think of the right way to put it, but it's trying to, I'll say assist some of those states with pollution sources that are coming from across their borders. Right? So,
Seth (08:24.707)
Okay.
Peter Paone (08:51.85)
level ozone, a lot of ground level knocks is caused by cars, but some of it's caused by big, we call them stationary sources, cement plants, power plants. And what part of this rule is trying to do is to help downwind states, downwind locations deal with emissions coming from other states that are pushing them potentially over their ozone limits.
Seth (09:15.085)
Gotcha.
Peter Paone (09:16.21)
Hopefully that makes some semblance of sense. I mean, the whole thing is complicated and convoluted and certainly not very easy to follow for someone who hasn't followed it for a long.
Seth (09:28.405)
Yeah, no, like I said, once I read this article from ENR and then you click on the link to the actual.
Seth (09:41.565)
to the actual page where on.
that EPA has on epa.gov. And you open up that page and there are lots and lots of links to click on. But there's a, if you go to, for the folks that are listening, if you go to epa.gov and search good neighbor plan for, I guess this originated in 2015, because it says for 2015 OZO,
Knox, what you mentioned before, Peter, NAAQS. And it's got the map, and it shows the states that fall under this plan. And what's interesting is, like I said before, it's only some states. And only some states have to follow the rule for both their power plants and other industries,
Seth (10:47.345)
kilns would fall under. And then some of the states are just for the power plants. And then looks like just California for some reason is the only state that it's covered for everything but power plants. So it's definitely, if you've got some time to waste,
Peter Paone (11:10.651)
Yeah.
Seth (11:17.085)
to me and that's why I wanted to bring you on here. But can you talk a little bit about, so if we were just to look at the NOx emissions, the different kiln types, can you talk about that and how they're imposing different limits
kiln type that does that does that make sense?
Peter Paone (11:50.71)
It does. And maybe it helps to talk a little bit about how cement's actually made as opposed to concrete. So cement is, I like to tell people, it's not just one compound. Right. There's a lot of different types of cement out there. You know, there's there's in the US, I mean, there's there's at least eight different main types that people talk about.
Seth (12:09.886)
Mm-hmm.
Peter Paone (12:20.65)
you have white cements, you have all these different masonry mixes and you know you
Seth (12:28.045)
A favorite on the podcast is type one L.
Peter Paone (12:30.97)
Type 1L and then you'll probably start seeing a lot more type 1P and type 1T as some of these carbon rules come into effect. So you have a lot of these different types of cement. As a cement manufacturer, as someone who's making cement, it all comes down to the chemistry. So you're trying to make a blend of a certain amount of calcium, silica, iron, and alumina. Those are your four main minerals that kind of go into making whatever type of cement
you're really aiming for. To do that, we take normally it's limestone and a bunch of other materials and we melt them. So we grind up huge amounts of rock. You can see entire mountains disappear over time as you're as you're quarrying out the rock. But you have to heat up that that rock to the point where it physically melts. My kids just get fascinated by me showing them videos of making a lava in a kiln because that's essentially what you're doing. You're making,
lava. And then after it comes out of the kiln, you cool it off and you grind it into the cement powder that everyone's familiar with and normally misidentifies as concrete. It takes a tremendous amount of heat to melt that rock. So the rock coming out of the kiln is going to be somewhere around 1,450 degrees C. So that's upwards of 2,600 degrees Fahrenheit. Certainly, I would not want to be
at that point, because it's probably a little toasterier than I want to experience, but all of that heat does a lot of strange things to the air and to the fuel. At that high of a temperature inside a kiln, the nitrogen and the oxygen in the air, so air is normally just about 80% nitrogen and 20% oxygen. It's 21% oxygen by volume, 79% nitrogen. At those temperatures,
Peter Paone (14:32.13)
react with each other. Like they'll break apart and they will reform as NOx at those temperatures. And certainly the higher the temperature the more the air decides to react with itself. So that's really where you get some of this NOx formation in a kiln system is just by heating the heck out of the air and causing the nitrogen, the oxygen, the air to mix together. So the old
style kilns out there, you see these wet kilns and these long dry kilns, they take up a lot of fuel, they use a tremendous amount of air. They normally have a very high amount of NOx that's just naturally emitted because of the way they were designed. You know, when rotary kilns were first becoming a thing 120 years ago, no one cared about NOx. They were just looking to improve upon some
Peter Paone (15:31.35)
So they tend to be, I hate to call them, but NOx generating machines. They make a lot of NOx just by the nature that they've been made. Over the last 20 or 25 years, we've seen technology change where now you hear about calciner kilns. And I think that's one of the things you have listed in that rule, you have calciner and you have preheater kilns.
Seth (15:40.186)
Mm-hmm.
Seth (15:54.346)
Yep, those are two of them.
Peter Paone (15:56.03)
Right? So starting about, let's see, back in the 1950s and 1960s, cement manufacturers, or I should say the equipment providers to cement manufacturers, started coming out with preheaters. So the old days, you had a 400 or 500 or 600 foot long kiln, and all of your reactions took place in that one piece of machinery. Right? So you had to preheat the material, you had to dry off all the
Seth (16:17.787)
Mm.
Peter Paone (16:26.43)
Then you calcine the material. The limestone you're putting in there, calcination is just a fancy way of saying we're boiling the CO2 out of the limestone. You have a heating section and then you have a section where you're melting the rock. If you look at a kiln as a series of reactors, it's five or six reactors end to end. It's a preheater. It's breaking apart the clays. It's doing some more preheating. It's calcining, doing a little more preheating, melting.
end of the kiln you have a small cooling zone. So just right where the flame is starting is actually colder than at the heart of the flame. So as you get down the kiln length, material actually starts to cool off towards the end and that's where your clinker minerals start to set. That's where all those minerals that we're trying to create start to crystallize and grow and make what we're aiming for in our cement. So these older kilns, all six of those
Seth (17:14.287)
Hmm.
Peter Paone (17:26.35)
in that one single tube. Back in the 1950s and 1960s, a couple of these OEMs figured, you know what? This isn't very efficient. If we can separate out some of these reactions, we can make it a lot more efficient, use a lot less fuel. And really what we're trying to do is squeeze more toothpaste out of the tube. You know, you have a 600 foot long kiln, it's a lot of maintenance on something like that because you have six supports. You're trying to keep them all in a line.
them a little bit, the kiln starts to torque, you start getting these funky shapes on the shell, and no one ever likes that. So they started introducing what people know as preheaters. So they came up with a couple different designs where now this material you bring into the preheater, you start to heat that material separately using the gases that you're producing in the kiln, but you can control the speed a little bit different. So now we can improve how we're heating the material up, and maybe we're not wasting as much of the heat
Right? So we burn less fuel, we get more of that heat into the material. And then around the late 60s and 70s, they started introducing the calciner. So now you've got a preheater that's preheating the material. You've got a calciner that its only function there in life is to just drive CO2 out of rock. So now by splitting all of these different processes, you essentially split the fuel that you're using in a kiln system in half.
Seth (18:55.227)
Oh wow.
Peter Paone (18:56.07)
quite literally, you drop the amount of fuel that you're using in the overall system in half. So between industry and these OEMs, I don't want to say inadvertently, but they've helped improve the emissions from these systems over time just by being able to reduce the fuel consumption. Well, a couple of bright people back in the 90s came up with this concept that
Peter Paone (19:26.15)
using to calcine the material just right, you can actually use that fuel to get rid of the knocks that you're creating in the kiln. We call them reducing conditions. There's two different ways you can run something. It's oxidizing, so you have a lot of oxygen available. You have oxygen combining with things, or reducing, which is normally when you have too little oxygen. We call those reducing conditions.
If you put a little bit of fuel in there without having enough air, you burn, and I'll use a fancy term that no one's going to understand, substoichiometrically. Really fancy way of trying to make me look smart by saying you burn it with not enough air to actually burn everything out. What that does is it makes a lot of hydrocarbons. It starts making all these funky carbon monoxide and hydrocarbons and all
And I'll use a wrestling analogy. All of those little hydrocarbons, they are desperate for oxygen. They don't have enough oxygen to burn. They are looking anywhere they can to steal oxygen from something. And all this kiln gas that's coming into the calciner has all this NOx, which as we talked about earlier, it's got nitrogen, it's got oxygen attached to it. So it sees the nitrogen connected to the oxygen. It says, I want that oxygen a heck of a lot more than that NOx does.
those hydrocarbons basically put the NOx in a chokehold and rip the oxygen off of the NOx and leave behind nitrogen. So with this way of staging the airflow and staging the fuel flow, they've come about this way of making a lower NOx system. They basically use the fuel that they're firing to reduce the NOx that's being made into kiln. So it takes a special way of doing that, like
Seth (21:04.628)
Huh.
Peter Paone (21:26.45)
that you can put the fuel in without having enough air in. And you have to do a whole bunch of things to make sure it mixes well at the end or else you wind up with a whole bunch of other stuff you don't want. But long story short, you're able to use the design of your kiln system, of your calciner, to reduce the NOx by itself. So if you look at that rule, you'll see the long kilns, the wet kilns, the long dry kilns, you have a higher limit. That's because you will just naturally
emission level out of those kilns. You get into preheaters, you might have a little bit lower level, and you get into a calciner design. If you design it just right, you can get a very low NOx coming out of that system to begin with.
Seth (21:58.069)
Mm-hmm.
Seth (22:12.205)
And then are there systems where they combine the preheater and pre-calciner? Yeah.
Peter Paone (22:18.19)
Yeah. So, so normally, normally if you have a pre calciner, you'll have a preheater rate after that's not always the case depending on, on the design of the system, but that's I'd say 95% of them out.
Seth (22:24.365)
Uh huh.
Seth (22:30.685)
Gotcha. All right, so that makes sense why they have, based on kiln type, they have the different limits listed here. Yeah.
Peter Paone (22:41.97)
So that's just with the design of the kiln, right? So that's going out and designing the equipment to try and keep the NOx as low as possible. The problem that a lot of plants have is, I mean, you build a cement plant, you're expecting it to run for a hundred years. You're not putting up a cement plant and then 20 years from now turning off the keys and shutting the doors and saying sayonara. So you've got plants out there for the 1950s
Seth (22:45.036)
Mm.
Seth (23:06.065)
Mm-hmm.
Peter Paone (23:12.33)
that weren't designed in that manner. Right? So now you have to get into all these add-on technologies. And I'd say that's probably another reason why you have those tiers of different emission levels, because most people use, and I'll throw out some more fancy terms, either SNCR or SCR for NOx control. And I'm saying, when I say most people, I mean beyond the cement industry,
technologies that most people talk about. And they're both fancy ways of saying, we're going to spray ammonia or urea into the gas to get rid of NOx. Right. I'd say most people are probably more familiar with SCR without even knowing it. Right. If you have a catalytic converter on your, on your truck, on your car, that catalytic converter is a, is a catalytic reactor. So SCR is selective catalytic reduction.
Seth (23:51.107)
Mm-hmm.
Peter Paone (24:11.85)
If you've got DEF on your truck, if you've got a little DEF tank that you're using, that DEF is basically urea. It's being sprayed onto a catalytic reactor and it's being used to reduce the knocks from your truck. So a lot of people probably are familiar with the technology even if they don't know the fancy terminology for it. So a lot of industries use SCR, a lot of power plants use SCR. And like I said,
saying we're going to use ammonia or use urea to reduce NOx. It requires a lower temperature but it requires a very expensive catalyst, right? So you spray the ammonia or the urea on the catalyst at the right temperature and the urea or the ammonia react with the NOx to get rid of it and form water and nitrogen which everyone's okay with emitting. In a lot of cement plants we don't use SCR.
Peter Paone (25:11.35)
same reaction but without using a catalyst. The reason we don't like the catalyst so much is because number one it's expensive and you need a lot of it because cement plants have a lot of dust in them. You know by the time you get your SCR reactor in a truck that the gas coming to it's normally fairly clean it doesn't have as much soot you've got a lot of dust that can react on the
and basically kill it so it won't work. So most often what we're doing is we're using SNCR where we're injecting this ammonia, very high temperature, again, trying to get it to react with the NOx and get rid of it. So a lot of plants in the US currently use SNCR, so they'll spray in a solution of ammonia to get rid of it, get rid of the NOx. The problem is that it's not nearly as effective
Seth (25:43.707)
Hmm.
Peter Paone (26:12.691)
So you can get rid of maybe 50% of the NOx, maybe a little more with SNCR in a modern kiln. In power plants and some other facilities, you can get upwards a 90% reduction with SCR. So the catalyst can get rid of more, but we have some pretty substantial hurdles to get it to work in a cement kiln.
Seth (26:34.965)
Yeah. So where do they, uh, where do they, you explained it as like a bolt on technology. So where, where do they bolt this on? Is it within the kiln itself or?
Peter Paone (26:48.37)
So with the SNCR, you can spray it inside the system. So for long kilns, for long, long dry, long wet kilns, it's really a fun project when I've had to work on them. You have to figure out a way to get a tube that's stationary into a big rotating kiln, because you have to get it at just the right temperature zone. And that temperature zone in a long kiln is like halfway down it. So you have to figure out a way to get a tube to the end of the kiln,
and then made it up with the rotating section. So you have this special coupling on the end. You take it through the coupling, which comes inside the kiln, pops out the sidewall of the shell, and then runs along the kiln shell down to the right temperature zone, where it comes back in and you have a sprayer. Not nearly as effective in wet kilns because you don't have as much control. You can't really move the nozzles once the kiln's spinning
installed. You're kind of fixed in location. So that's how you do it in a wet kiln or a long dry kiln. In a modern preheater, pre-calciner kiln, you have a little bit more control because you can work around the outside of it because you're up in the section where there's nothing moving. It's just the vessels. In those areas, you're normally having a couple spray nozzles and you're trying
Peter Paone (28:18.79)
So when I do training for people for the PCA, I talk about time temperature and turbulence You certainly need the right amount of retention time. It's got to get in there. It's got to react before it starts to cool off It's got to be just the right temperature range and there's an optimal temperature range of somewhere around 1600 1650 with ammonia maybe 1800 1850 F with urea if you don't find
just the right temperature range, you either burn up the ammonia. So at too high of a temperature, you actually generate more NOx. At too low of a temperature, you get slip. It goes through the system without reacting. And then you have all sorts of problems with the ammonia coming out the tailpipe and basically coming out the stack and causing visible plume issues. So that's how we do SNCR commonly. SCR can be done. That's normally done at the exit
That's a little problematic because there's a lot of dust at that location. So when you're doing SCR on a cement kiln, you need a lot of catalyst. You need a lot of space for it and you have to do a lot of things to try and control how much dust builds up on the catalyst. So it's not nearly as popular here in the US as it is in some other countries that help subsidize it.
Seth (29:42.909)
Huh.
Um, let me ask you something. Uh, you, you mentioned back in the fifties, the, the cement, uh, manufacturers, they came up with a better solution, a more efficient solution. Um, and then again, in the nineties, they did it again. And that wasn't driven by, uh, government policy, right? Those two events.
Peter Paone (30:08.77)
No, it was primarily driven by, I'll say cost, right? So one of the big drivers of, I'll say, adoption of technology has been the cost to operate. One of the biggest drivers was the oil embargo back in the 70s. The cost for oil drove a lot of cement manufacturers to try and reduce how much oil they were using. So taking out older kilns or modifying older kilns
Seth (30:31.665)
Mm-hmm.
Peter Paone (30:39.07)
The fuel usage was driven primarily by trying, you know, to remain in business. They didn't want to be driven out of business by more modern plants that were having lower operating costs.
Seth (30:51.465)
So was the industry before this good neighbor, I'm sure everybody knew that this was common since they've been working on it for eight years, but has the industry been doing anything as far as becoming more efficient that by doing that, it would reduce the NOx emissions anyways? Or, or is, or are they?
how did how those two, and I can't remember those acronyms again, but those two ways of basically spraying ammonia and into the kilns and everything. It sounds it's very problematic it sounds like and it and I'm just wondering if the industry had its own way of becoming more efficient if doing
Peter Paone (31:27.611)
Yeah.
Seth (31:52.246)
working on becoming efficient if the, if maybe not on purpose, but the result of it would reduce the NOx emissions anyways. Are you following what I'm getting at here? I mean...
Peter Paone (32:04.69)
Yeah, yeah. So, so I'd say that's been most of my career for the last 20 years has been going to plants and helping either reduce NOx emissions or make them more efficient or both at the same time. Right. So a lot of plants, I'd say have either experimented with or they've just gone, gone full, full into installing SNCR systems in the last 15 years. So any plant I would have gone to in the
Seth (32:14.186)
Yeah.
Peter Paone (32:34.59)
system in there for reducing NOx, I'd say maybe 80% of the plants out there now have an SNCR system or have, there's a limited number that have SCR out there that are also trying to reduce emissions. So I'd say a lot of that's been brought about not necessarily by this good neighbor rule coming out, but by individual plants and individual states having their limits gradually reduced
reasons. So it's been happening. That's one thing. The other big shift that I'd say we've seen in the last 20 years is a lot more people shifting away from conventional fuels. So away from coal, away from pet coke. Certainly the last, I'd say five to 10 years, there's been a tremendous switch over to natural gas. And how you do natural gas and a kiln can
how you do it, but you see a lot of alternative fuels. So if there's a substance out there that can burn, I can almost guarantee you that a cement kiln somewhere in the world has tried to burn it. Right? You need a tremendous amount of fuel to melt rock. And what a lot of people have done over the last 20 years is move into all of these different alternative fuels that
and a lot of cases can actually help reduce the emissions. So I'll tell you a story. I live in the Lehigh Valley. My office is here in Bethlehem, Pennsylvania. There's five cement kilns, probably within a 20-mile radius of my house. And some good-meaning people from an environmental organization came to my house one day, and they were trying to get me to sign a petition to stop one of the local cement plants from burning tires.
Peter Paone (34:34.69)
want them to burn tires, they're like, oh, they're evil, they pollute. Just think of all the black smoke that comes out. And I'll admit to being a little mean because it was probably 20 degrees out and I had them sit on my front stoop for a good half hour while I argued with them out in the cold. But I told them, look, when you burn a tire in a cement kiln, if you do it right, you reduce the NOx emissions, right? You reduce the amount of NOx that's coming out of the kiln. Everybody
because you've helped reduce the knocks. You don't have this tire that's sitting out there in a swamp somewhere breeding mosquitoes and all that other stuff. It's not gonna catch on fire some other time and create all that black smoke. You're doing it in a controlled environment where it's reducing your environmental footprint and you're able to use the iron and the steel belt that goes into the cement. Now we don't have to mine the iron from somewhere else. So it's a win, win, win. Why do you wanna ban it? Well, cause black smoke.
Seth (35:29.471)
Oh yeah.
Peter Paone (35:34.55)
No, no, it's, you know, 2,800 degrees. There is no black smoke. There's not gonna be anything coming off of it. The only thing left is gonna be the clinker coming out of the kiln. So it's a lot of steps like that that the industry has taken over the last 20 years, which also helps, you know, it helps both ways. It helps reduce the plant costs. It helps the environment and it, to some extent, improves the overall efficiency from the standpoint
Seth (35:45.348)
Uh-huh.
Peter Paone (36:04.57)
mine other stuff to bring it into the plan.
Seth (36:08.465)
Yeah, that's a cool story. Is anyone out there, are they actually burning tires?
Peter Paone (36:17.69)
Oh yeah, there's a lot of plants that burn. I remember one plant, a lot of people are familiar with what a potato gun is, right? There's a couple plants out there that have used essentially a giant potato gun that's big enough to shoot tires into a kiln.
Seth (36:28.326)
Oh yeah. Yeah.
Seth (36:36.905)
Oh, that's cool. Is there videos of that on YouTube?
Peter Paone (36:38.17)
Yeah, it's it's I. So so I I had seen videos from from an R&D test, and it sort of reminds you of any movie where kids are outside playing baseball. Right. Because I watched this video one time of these guys and they have this this tire shooter and basically this big compressed air cannon for shooting tires. And they've got it outside and they're going to try it out because it's the first time they're using it. They want to see if it's actually going to be able to
to arc the tire into the kiln. So you have this shaky video of the guy with the camcorder sitting there recording everything. They're all sent around like, oh, what pressure do we use on it? One guy is like, well, let's just crank it all the way up because we don't want it stuck in there because it's going to be a pain to get it out. OK, well, how far do you think it'll shoot? Oh, I have no idea. Let's just let's just crank it up and see the first time. Right. You have a little shaky video and they're standing back and they're like, OK, fire.
out of this cannon and goes across the road and lands in the neighbor's yard and you hear everyone like, run, run. It's like, oh, it's like the kids with the baseball hitting it through the window. Nobody saw us do it, we gotta hide.
Seth (37:53.245)
Oh man. Yeah. They can't use a conveyor or something. Or what did they end up using?
Peter Paone (38:00.97)
So that's, that's actually what they've used in a couple, uh, long wet kilns out there. So you, uh, you shoot it uphill and then it lands in the jar and it slowly burns coming down. Um, more modern kilns. Uh, there's all sorts of these, these special shoots that allow you to drop a tire in and try and keep the oxygen out. So you'll have like a double, a double flap. So it'll allow the tire in and then you'll have a second valve to let it fall down into the kiln system. Um, there's a couple, uh, OEMs.
again out there that manufacture specialty machines to bring tires into the plant and drop them in and try and burn them well. Lord knows I've seen enough plants where it's gone wrong but normally they try and make them burn pretty well.
Seth (38:45.945)
Yeah. Well, you gotta, you gotta try and figure it out. And then you, I mean, you don't know what's going to go wrong until you actually do it. Um.
Peter Paone (38:55.37)
I got to tell you, there's a lot of other fuels out there. I mean, there have been plants out in the world that burn, you know, leftover rice husk. You know, when they're, when they're making rice and they're getting the grain, they have all the husk. They burn the, the rice husk. There's plants that burn, seed corn that's expired. So all the corn that goes bad because they didn't get it planted in time or it's gotten a little wet, they'll burn that. I've seen sawdust and I've seen demolition debris.
And I've seen all sorts of different fuels used, but I got to say my least favorite is I was at Kilm over in England back probably 16 years ago, back when they were having all the issues with mad cow. And there were some plants in Europe that were burning cow. Like they were, they were. Yeah. Cause you get for, for mad cow, you got to burn all the disease away.
Seth (39:42.453)
Oh, yeah.
Seth (39:48.285)
like the carcass.
Peter Paone (39:54.99)
bury it because it gets in the groundwater and whatnot. So they were basically making these giant hamburger facilities where they're grinding up the cow. And they had this fancy term for it, MBM, meat and bone meal. And they would grind it up and they would inject it in as a fuel in some of these plants because it would burn.
Seth (40:12.886)
Wow.
Peter Paone (40:14.01)
Grossest thing I've ever seen though, because the compressor that they'd fire it with would warm it all up and you get all the Stuff start to melt and would plug the light. It was absolutely disgusting
Seth (40:26.368)
Man, who would have known? So this is, this is to replace like the, the coal that they're burning and all that. That's pretty cool.
Peter Paone (40:36.09)
Yeah, trying to, again, it's one of the, if you look at the PCA's footprint or their plan for reducing carbon emissions using more alternative fuels is one of those steps in the process of trying to replace traditional fossil fuels with essentially anything that'll burn.
Seth (40:59.425)
Yeah, basically stuff that is going to get tossed away. And so once again, I've said this on this podcast before, and this solidifies my opinion, not that I need it, but I still think concrete's the most sustainable building material on earth. And again, it's, we're using waste material to make cement. Um, that's the kind of, uh, uh, folks are smart people we got out there trying to figure out. So.
And again, what I was getting at about the changes from what you mentioned before, the kiln technology changing in the fifties and changing in the nineties is that that is driven by companies want to be more efficient to make more money. It's driven by profit. It's we don't need the government to tell us, hey, you need to be more efficient or you need to, you know, emit less things into the air.
I think we're figuring that out on our own. But anyways, that's my short rant for today, Peter. But I appreciate you coming on the show. I think this is a good spot to end today. I think you're someone we need to go back out to and have on the show again, as we learn more about, I think learning about how cement is manufactured is fascinating.
Peter Paone (42:07.17)
Yeah.
Seth (42:29.825)
a couple hours on YouTube looking at, I think there's a company in Africa that have these videos of their facility and it's really in depth on how cement is made. And I can't remember what the company's name, but it seems like a pretty big outfit, but they show you the steps that you were describing.
on YouTube and look that stuff up so you can kind of follow along what Peter was talking about and it might make more sense for, for people like me that aren't as, uh, in tune with that whole process. But, uh, uh, Peter, if folks want to reach out to you and learn more about what you do, and I'm sure we got some, um, cement, uh, folks listen to the podcast that might need your help, uh, how, what's the best way to get ahold of you?
Peter Paone (43:27.65)
Uh, probably by email or, uh, or reach it out through our website. Uh, so, uh, I'll give everyone my email. It's actually my last name. Uh, so Paone P A O N E P, uh, you know, uh, last name, first initial, uh, and that's at zap, uh, ECS.com Z A P E C S.com. That's zap engineering construction service. That's what it stands.
Seth (43:50.265)
Yeah. And we'll put that in the show notes as always. And folks, if you can go to our website, ConcreteLogicPodcast.com, sign up for the newsletter. You'll get an email when this podcast comes out and we'll have Peter's contact information on there as well. Peter, thanks for coming on the show today. I was happy that you could explain this in layman's terms for the most point.
Peter Paone (44:19.234)
Hopefully, it was mostly layman's terms. It's hard when you start getting into all those acronyms and trying to follow the alphabet soup that's out there.
Seth (44:21.45)
Mostly layman's terms, but it's great stuff.
Seth (44:30.005)
Yeah, I'm going to have to listen to this several times so I can get that done. But.
Peter Paone (44:34.33)
You know, I do also, I have to say, the cement industry. So the Portland cement association runs a conference every year. That conference is normally the end of April or early May. So it's the IEEE-IAS slash PCA cement industry conference. I know again, that's a mouthful, but that's because the Portland
Peter Paone (45:03.21)
EEE, which is the big electrical engineering association. There's a conference every year. I'm actually on the committee that helps put together the conference. And I'm actually in charge of some of the technical content for training. So I do a lot of training there. Certainly if you're in the cement or concrete industries, it's a great resource for learning about the cement industry and for all the processes going on out there. So I can't say enough about all the work they do.
Seth (45:06.607)
Okay.
Peter Paone (45:33.33)
I can't take all the credit for it. I only do a small bit, but if any of your listeners ever want to attend, that's a great conference to go to to learn about the cement industry.
Seth (45:43.305)
Yeah. And so that's coming up soon and where's this year's conference?
Peter Paone (45:49.13)
This year's is actually in in Dallas. So there's a whole bunch of things on LinkedIn about it You can also look at the the cement conference. Just look up cement conference on Google or any of your Different different search engines and I'm sure you can find it
Seth (46:04.465)
Okay. All right. Yeah. And if you're attending that look, uh, look up Peter and sounds like you're going to be doing some, some, uh, talks there as well, huh?
Peter Paone (46:13.292)
I will be, yep.
Seth (46:15.125)
All right. Well, Peter, I appreciate you coming on the show today and we'll have to do it again.
Peter Paone (46:20.411)
Thanks so much, Seth.
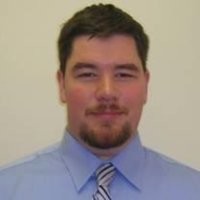
Peter Paone
An accomplished, professionally licensed engineer specializing in pyrotechnology and emissions in the cement and minerals industries with more than 18 years of international experience with Process Equipment, Project Execution & Sales for the Cement/Minerals Industries. An expert in the measurement, prediction, and mitigation of cement and minerals plant emissions. A proven innovator and inventor, with four patents to his name.
Publications include:
High-Efficiency Separator Upgrade: Threading a Separator through the Eye of a Needle, IEEE/PCA Cement Industry Technical Conference, May 2017
Processes for Activation and Manufacturing of Supplementary Cementitious Materials, IEEE/PCA Cement Industry Technical Conference, May 2012
Paone, P., Mercury Control Technologies for the Cement Industry, IEEE/PCA Cement Industry Technical Conference, March 2010
Paone, P., Mercury Reduction Technologies for Cement Production, 7th Colloquia of Managers and Technicians of Cement Plants, Nov. 2009, Malaga, Spain
Paone, P.T., Heavy Metals in the Cement Industry: A Look at Volatile Cycles and Simple Mitigation Techniques, IEEE/PCA Cement Industry Technical Conference, May 2008
Paone, P.T., Blower, M., and Hines, C., The Installation of the New Horizontal, Fixed Grate-Line Cooler at Ash Grove Cement – Montana City, IEEE/PCA Cement Industry Technical Conference, May 2007.
Specialties: Cement process design, emissions abatement, mercury controls