The 28-Day Compressive Strength Test: Is it Really the Best Measure of Concrete’s Durability?
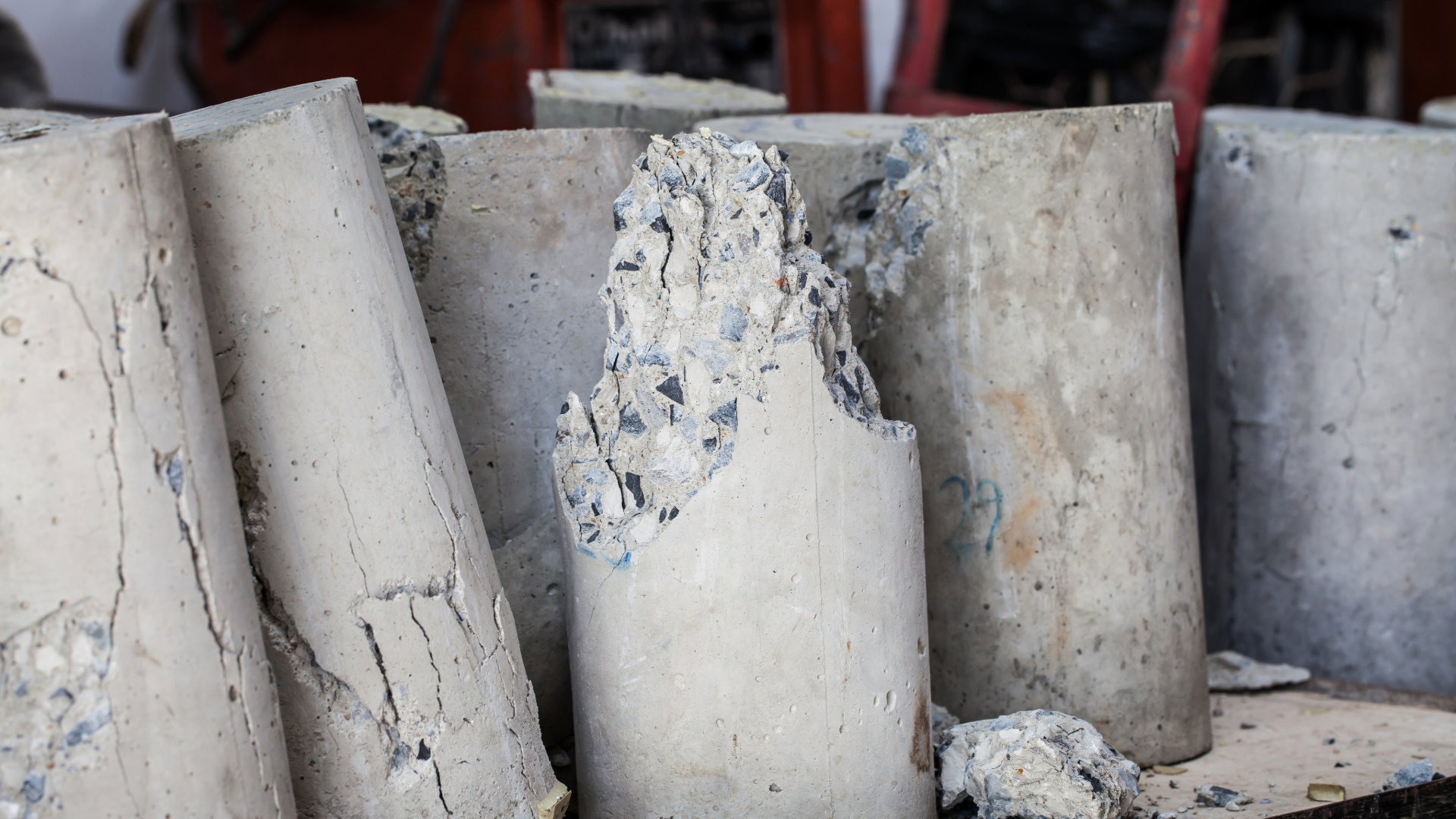
The 28-day compressive strength test has long been considered the gold standard for evaluating concrete performance. It's been the go-to method for everything from design decisions to regulatory compliance. But, as we dug into in our latest episode, EP #116: Why Concrete Fails – The Hidden Truths About Moisture, Salt & Curing, this test might be offering an incomplete—and sometimes misleading—view of concrete’s long-term durability. In this post, we’re going deeper into the limitations of the 28-day test and breaking down the real factors that determine a concrete structure’s longevity.
The Illusion of Strength: What the 28-Day Test Misses
The 28-day strength test is simple enough: concrete cylinders are cast, cured under controlled conditions for 28 days, and then crushed to measure compressive strength. The result is used to assess whether the concrete meets the project’s specs. But here's the problem: this only gives a snapshot of strength at one point in time. Concrete continues to gain strength beyond 28 days, just at a slower rate, and different mixes will gain strength at different speeds.
If you rely solely on the 28-day test, you could seriously underestimate the concrete's ultimate strength. You might also overestimate the safety factors needed in structural design, leading to overly conservative—and expensive—construction practices.
Another flaw? The curing conditions in the test don't come close to mimicking real-world environments. In the lab, you get controlled temperature and humidity. But out in the field, concrete faces temperature fluctuations, exposure to aggressive substances, and moisture variations—all factors that can drastically affect performance.
Moisture’s Destructive Power: How Water Weakens Concrete
Water is one of concrete’s greatest enemies. Sure, it’s essential for hydration, the process that hardens the cement and gives concrete its strength. But when water exposure is excessive or uncontrolled, it opens the door to a whole host of issues.
One major problem is freeze-thaw damage. When water gets into concrete and freezes, it expands. This creates internal pressure that can crack and weaken the material. In colder climates, where freeze-thaw cycles happen regularly, the damage can be severe. The porosity of the concrete, how much water it absorbs, and the number of freeze-thaw cycles all determine how badly the concrete will degrade.
Water exposure also leads to leaching, where calcium hydroxide—a byproduct of cement hydration—is washed away. As this material is removed, the cement paste weakens, which reduces the overall strength and durability of the concrete.
That’s not all. Moisture can also accelerate alkali-aggregate reaction (AAR) and corrosion of reinforcing steel, both of which we’ll dive into later.
The Salt Assault: How Deicing Salts Attack Concrete
Deicing salts—used to keep roads and bridges safe during winter—are another major threat to concrete. These salts not only ramp up freeze-thaw damage but also contribute to the corrosion of reinforcing steel.
Here’s why: salt lowers the freezing point of water, keeping it liquid at temperatures well below freezing. That means the concrete stays wetter longer, making it more susceptible to freeze-thaw damage. Plus, salt solutions can create osmotic pressures inside concrete, amplifying the cracking from freezing water.
The real kicker, though, is chloride. When chloride ions from deicing salts infiltrate the concrete, they break down the protective layer around reinforcing steel. This allows corrosion to take hold, leading to the formation of rust. Rust expands, creating forces that crack and spall the surrounding concrete. This is one of the biggest causes of premature failure in concrete structures in cold regions.
Curing Concrete: Innovations and Best Practices
Proper curing is key to concrete achieving its full strength and durability. Curing involves maintaining the right moisture and temperature conditions to allow cement hydration to happen effectively.
Traditional curing methods—like water curing, wet burlap, or plastic sheets—are the go-to. Water curing is the most effective but can be labor-intensive. For larger projects, curing compounds are an easier alternative. These liquid membranes reduce water evaporation, but their effectiveness depends on quality and application.
New technology is also improving curing methods. Self-curing concrete, for example, includes water-absorbing polymers that gradually release water during hydration, eliminating the need for external curing. There are also sensor technologies that track temperature and humidity within the concrete, allowing for real-time adjustments.
Environmental Factors: How the Environment Affects Concrete’s Performance
Concrete doesn’t exist in a vacuum. The environment it’s exposed to plays a huge role in its long-term durability. Factors like temperature, humidity, sunlight, and aggressive chemicals can all impact how concrete performs.
For instance, high temperatures speed up cement hydration, increasing strength but also raising the risk of cracking due to thermal stresses. On the other hand, low temperatures slow down hydration, reducing the concrete’s ultimate strength.
UV radiation from sunlight can degrade certain admixtures and sealers, reducing their effectiveness. And let’s not forget chemical attacks from acids, sulfates, and other substances, which can damage concrete and reduce its strength.
Concrete exposed to marine environments is especially vulnerable. Saltwater, wave action, and marine organisms can accelerate corrosion of reinforcing steel and cause severe damage to the concrete.
The Chemistry of Concrete: Why Composition Matters
Concrete is a complex composite material. Its composition—cement type, aggregate type and grading, and the use of admixtures—affects its properties and durability. Different types of cement have different chemical compositions, which impact hydration. For example, Type I cement is general-purpose, Type II is resistant to sulfate attack, and Type III is high-early-strength. But there's more to the story. As we discussed in EP #103: Concrete – The Rise of Blended Cements, Type IL and blended cements are becoming increasingly popular due to their sustainability benefits and improved long-term performance. Blended cements, like those with fly ash, slag, or natural pozzolans, enhance concrete’s durability and reduce its environmental footprint by lowering the carbon intensity of cement production. They also improve resistance to sulfate attack, reduce heat generation in massive pours, and enhance the overall workability of concrete. When using blended cements, it’s important to understand how they interact with other materials, as the curing process and hydration rates can differ. With the right mix, these cements offer both environmental and performance advantages, helping to future-proof concrete structures.
Self-Desiccation and Strength: Understanding the Deeper Effects
Self-desiccation happens when water is consumed during hydration, leaving the concrete with less internal moisture. While this is crucial for strength, it can also create tensile stresses that lead to cracking, especially in low-water-to-cement ratio mixes.
Proper curing helps mitigate this effect by providing an external water source. Plus, using supplementary cementitious materials (SCMs) like fly ash and slag can reduce self-desiccation by providing more water for hydration.
Transparency in Cement Production: The Missing Link
A major issue in the concrete industry is the lack of transparency in cement production. Cement composition can vary significantly, impacting concrete’s performance. By promoting transparency—through clear labeling, detailed chemical composition data, and rigorous testing—we can ensure better quality control and stronger, more durable concrete structures.
Conclusion: Moving Beyond the 28-Day Test
While the 28-day strength test remains a valuable tool for quality control, it shouldn't be the only method for assessing concrete’s long-term durability. A broader, more comprehensive approach is needed—one that factors in environmental influences, curing techniques, and concrete composition. As we discussed in EP #116: Why Concrete Fails – The Hidden Truths About Moisture, Salt & Curing, understanding these hidden factors is key to creating concrete structures that stand the test of time. Let’s keep innovating and refining our assessment methods to ensure we’re building for the future.